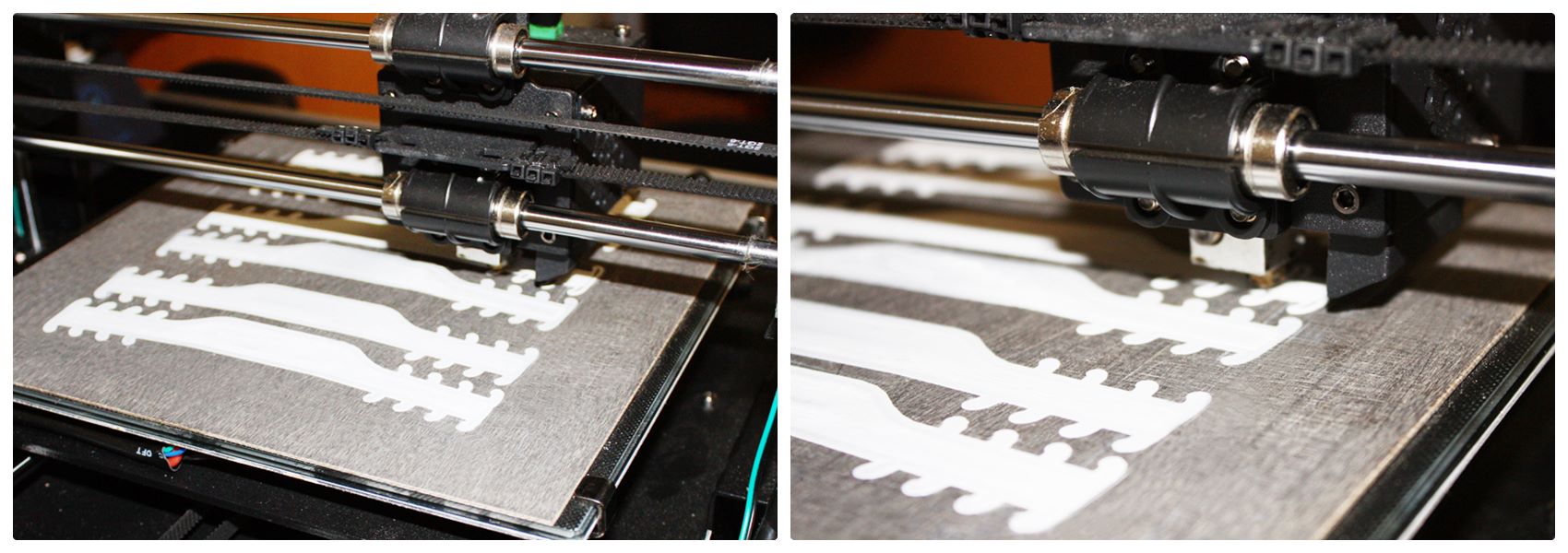
Bei vielen 3D-Druckern ist das Druckbett bzw. dessen Material ein begrenzender Faktor für optimale Druckergebnisse. Vorteile bringt eine einfache Aufrüstung des Druckbetts mit Pertinax.
Viele preiswerte 3D-Druckermodelle sind bei den beweglichen Komponenten für die Düsenführung sehr präzise, haben jedoch bei der wichtigsten Komponente, dem Druckbett, noch deutliche Einschränkungen. Als Druckbett für den 3D-Druck bietet einer der ersten Kunststoffe der Welt, das Pertinax, beste Voraussetzungen. Die Summe der Eigenschaften dieses Werkstoffes verbessert oft die für den Druck essenzielle Haftung des gedruckten Modells auf der Grundplatte – selbst bei hochmodernen 3D-Druckern – und damit die Druckqualität deutlich.
Welche Eigenschaften machen Pertinax nun für den 3D-Druck so interessant?
Welche Eigenschaften machen Pertinax nun für den 3D-Druck so interessant? Der gelbbraune Kunststoff ist bekannt als ein gerne genutzter Werkstoff für die Produktion von Leiterplatten oder robusten Isolierteilen gegen elektrische und thermische Leitung. Er besteht aus papierverstärktem Kunstharz, ist biegefest und zäh, relativ leicht, nimmt praktisch kein Wasser auf und ist in Form dünner Platten recht einfach zu bearbeiten.
Seine geringe Wärmeleitfähigkeit zusammen mit der Temperaturbeständigkeit von bis zu 130 °C prädestinieren ihn für den Einsatz mit den gängigen, heiss gedruckten Kunststoffen wie ABS (Acrylnitril-Butadien-Styrol-Copolymer), Nylon, Polymilchsäuren etc. Die Wärmebeständigkeit und geringe Wärmeleitung erlauben zudem eine gute Verbindung der flüssigen Kunststoffe mit der Oberfläche, etwa so wie man z.B. Keramikplatten im Bad für die bessere Haftung von Schmelzkleber vorwärmt, um die Erstarrung zu verzögern und damit die Oberflächenadhäsion zu verbessern.
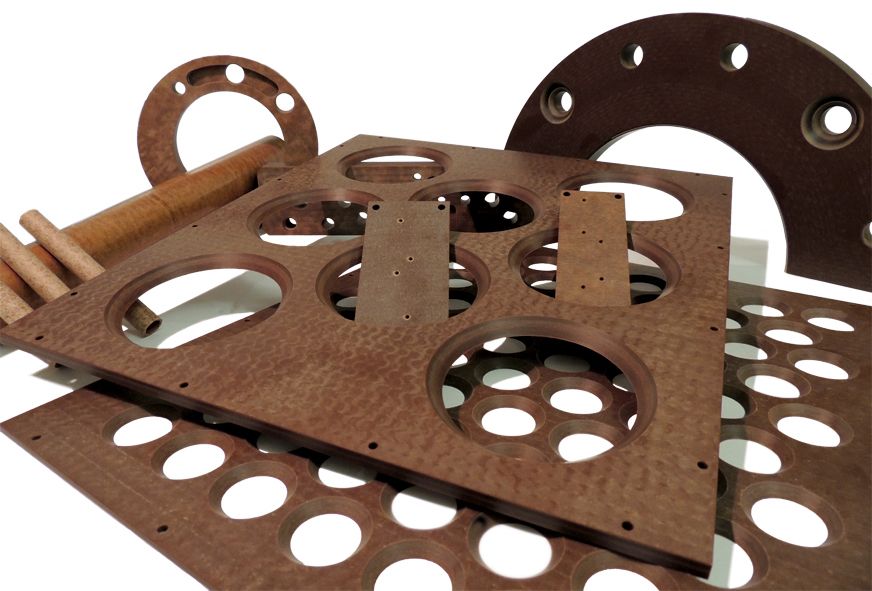
In drei Schritten zum Druckertuning
Um den Drucker aufzurüsten wird als erstes das Druckbett vermessen und eine Pertinaxplatte mit etwas grösseren Abmessungen besorgt. Dabei muss auf eventuelle Nieten oder Befestigungsteile geachtet werden, die über das Druckbett selbst hinausreichen und das eigentliche Plattenmass bestimmen. Als Plattenstärke haben sich 0,5 bis 1 mm, in seltenen Fällen auch bis zu 5 mm bewährt.
Zur Bearbeitung der dünnen Platten reicht ein scharfes Teppich- oder Cuttermesser sowie ein Lineal und Schleifpapier unterschiedlicher Körnung aus. Zunächst muss die alte Druckplatte vom Drucker entfernt und die tragende Oberfläche darunter gereinigt werden. Das Ablösen gelingt am besten mit einer dünnen stabilen Schnur z.B. Angelschnur oder feinstem Stahldraht auch bei komplizierteren Formen. Reste der alten Klebfolie werden mit Isopropanol rückstandsfrei entfernt, je nach Untergrund kann ein Ceranfeld-Schaber dabei helfen.
Pertinaxplatte auf einfachste Weise befestigen
Die neue Platte lässt sich sehr einfach mit einem doppelseitigen Klebeband, z.B. 3M Transferklebeband 467MP, befestigen. Die Pertinaxplatte und die Transferfolie werden passend zugeschnitten und die Folie blasenfrei auf die Rückseite der Platte aufgeklebt. Je nach Druckbettgeometrie oder Zugänglichkeit wird nun die neue Platte direkt auf das Druckbett geklebt und danach die Oberfläche bearbeitet. Alternativ schleift man die Oberfläche zuerst auf die gewünschte Rauigkeit und klebt danach die Platte auf. Letzteres kann erhebliche Zeitvorteile bringen, wenn das Druckbett schlecht zugänglich ist.
Gleichmässige Oberfläche bei jeder Körnung erzielen
Bei beiden Verfahren ist es wichtig, eine möglichst exakt horizontale und bei jeder Körnung gleichmässige Oberfläche zu erzielen. Angefangen mit Körnung 80 arbeitet man sich bis etwa Körnung 400 voran, der Abrieb wird mit einem fusselfreien Tuch oder reinem Zellstoffpapier, eventuell mit Isopropanol (IPA) getränkt, entfernt.
Wichtig ist, hier kein normales Kosmetiktuch zu verwenden, denn viele Tücher sind mit oberflächenaktiven Stoffen ausgerüstet, die die Oberflächenbeschaffenheit minimal verändern und so die spätere Haftung beeinflussen können. Bei eventuellen Haftungsproblemen sollte man daher zuerst versuchen mit anderen Tüchern nachzureinigen.
Bereits aufgeklebte Platten werden mit Schleifpapier und Schleifklotz in kreisenden Bewegungen geglättet. Bei noch unbefestigten Platten dagegen wird das Schleifpapier auf eine grosse ebene Fläche wie eine Glasplatte aufgelegt und die Pertinaxplatte als Ganzes leicht kreisend mit wenig Druck darüber geführt. Für ein gutes Ergebnis muss der Schleifstaub regelmässig entfernt werden. Bei der Endkörnung kann man je nach Geometrie und Material des Objektes durch Ausprobieren die beste Lösung finden.
Objekt muss sich leicht von der Oberfläche lösen
Ist die Platte «poliert» und aufgeklebt wird sie auf dem Druckbett nivelliert und gegebenenfalls mit IPA von letzten Schleifpartikeln sowie Fettresten durch Fingerabdrücke gereinigt. Die Pertinax-Platte bzw. das Druckbett sollten dabei kalt sein. IPA verdampft schon bei Zimmertemperatur recht schnell, ein warmes Druckbett würde daher die Reinigungsleistung vermindern und brennbare Dämpfe erzeugen.
Nun kann der erste Probedruck beginnen. Haftet dabei das Objekt nicht wie gewünscht, muss gegebenenfalls erneut leicht angeschliffen (mit der zuletzt verwendeten Körnung) und nachgereinigt werden. Idealerweise sollte das Druckobjekt sich nach dem Abkühlen leicht von der Oberfläche lösen lassen, bei einer grossen Grundfläche kann es sinnvoll sein, das Druckteil mit einem Tuch zu schützen und mit einer Zange leicht zu drehen, um es loszubrechen.
Keine Nachbearbeitung der Objekt-Grundfläche notwendig
Diese relativ einfache Aufrüstung des Druckbetts kann im Einzelfall zu drastisch verbesserten Druckergebnissen führen. Bei den meisten Anwendungen ergibt sich aber mindestens ein deutlich einfacheres Handling. Das gilt sowohl für Einzelstücke als auch für Kleinserien wie bei den momentan beliebten Grundgerüsten für Filtermasken.
In allen Anwendungen ist bei richtig vorbereiteter Pertinax-Oberfläche keine Nachbearbeitung der Objekt-Grundfläche notwendig. Damit hat sich der altbewährte Werkstoff Pertinax auch in der zukunftsträchtigen 3D-Drucktechnik eine weitere Nische erschlossen und gezeigt, dass auch altbewährtes neue Massstäbe setzen kann.
3D-Druck-Multimediastorys
Das Kleinstgedruckte - Über den Mikro-3D-Druck
Ab in die dritte Dimension - Wie HP den 3D-Druck neu erfand
Impressum
Textquelle: Andreas Zeiff, Redaktionsbüro Stutensee
Bildquelle: Dr. Dietrich Müller GmbH
Publiziert von Technik und Wissen
Weitere Artikel
Veröffentlicht am: