Unplanbares planen
Agile Optimierung für schnelle Entscheidungen
Autor: Adrian Weiler, CEO der Inform GmbH
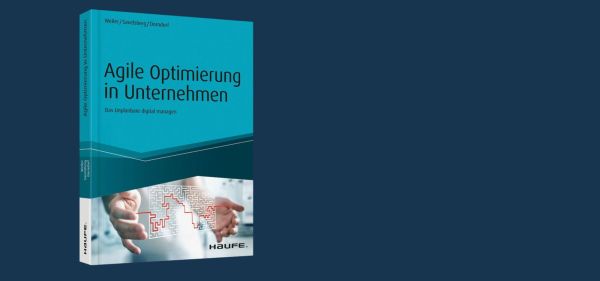
Unplanbares planen
Agile Optimierung für schnelle Entscheidungen
Autor: Adrian Weiler, CEO der Inform GmbH
Als alternative Strategie für das operative Management hält die Strategie der Agilen Optimierung Einzug in die Produktion. Denn um über den Erkenntnisgewinn hinaus auch zu optimierten Entscheidungen zu gelangen, bietet sich der Einsatz entscheidungsintelligenter Algorithmen an.
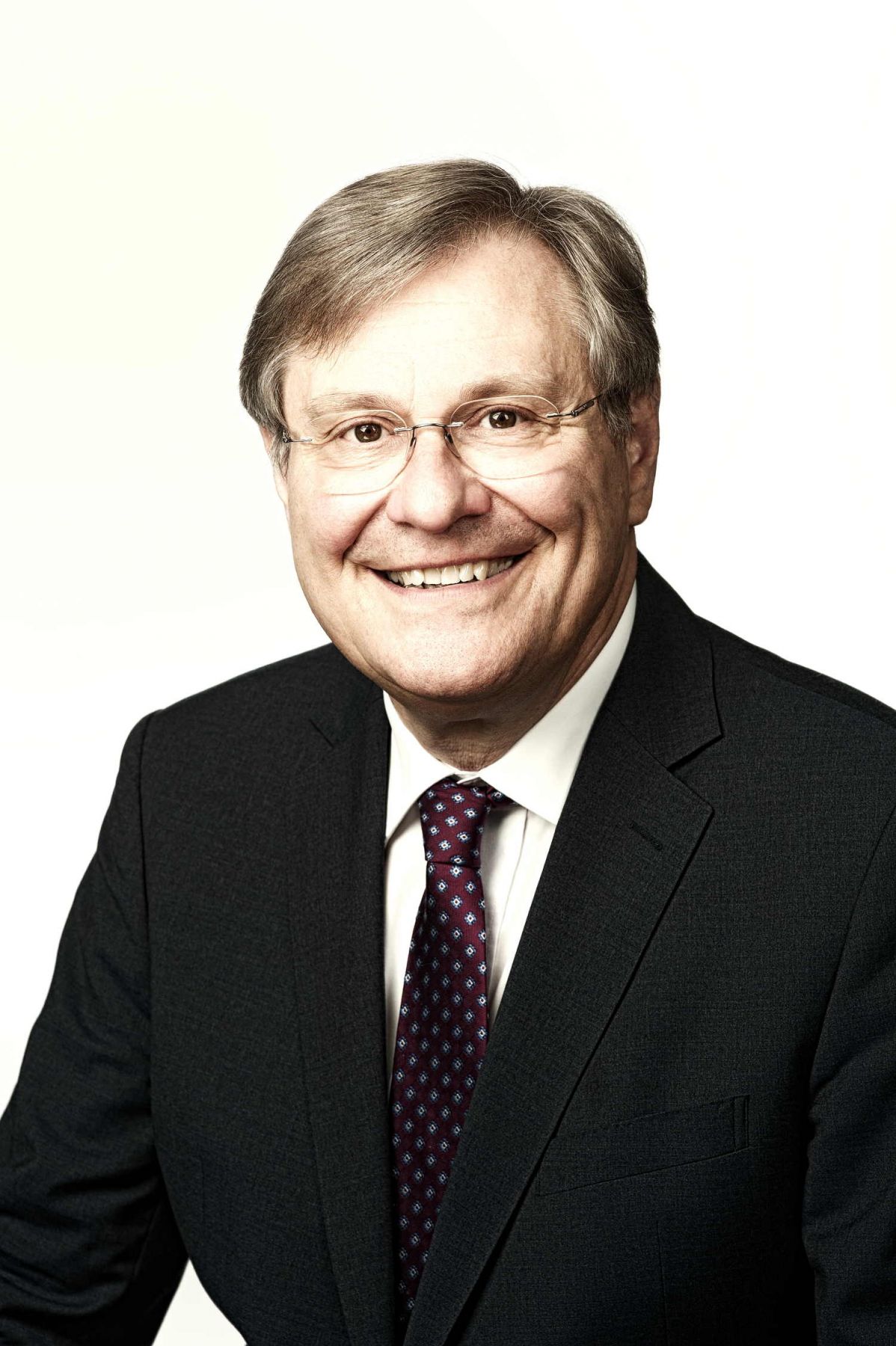
Lieferantenausfälle sorgen im Management für Kopfschmerzen, auch in grossen Industrieunternehmen. Vorab festgesetzte und garantierte Liefertermine gehören dieser Tage zu den wichtigsten Kundenanforderungen.
Doch genau dieser Anspruch stellt eine der grössten und wettbewerbsentscheidenden Herausforderungen der Produktionsplanung dar. So gehört es zum betrieblichen Alltag dazu, kleine, vermeintlich geringfügige Betriebsstörungen wie Materialverspätungen oder Personalausfall zu umschiffen und dennoch Prozesssicherheit – und damit Termintreue – zu garantieren.
ERP-Systeme allein sind dieser Aufgabe nicht mehr gewachsen.
Die Notwendigkeit agiler Optimierung
Klassische ERP- und PPS-Systeme planen gegen unbegrenzte Kapazitäten, etwa die von Maschinen. Sie ermitteln beispielsweise die Durchlaufzeit einzelner Aufträge, berücksichtigen aber nicht, dass mehrere Aufträge dieselben Maschinen besetzen und so einander blockieren können.
Ein vereinfachtes Beispiel veranschaulicht den Ansatz (Abbildung 1): Drei kurzfristig eingehende Aufträge (A, B und C) sollen innerhalb von drei Tagen abgewickelt werden. Dafür sind drei Arbeitstage pro Auftrag notwendig, an denen wiederum an einer Maschine je ein Auftrag bearbeitet wird. Da manche Aufträge dieselben Maschinen benötigen, kommt es zu Rückständen und die Werkstücke stapeln sich in den Gängen, bis sie endlich verarbeitet werden können (Auftrag B an Tag 2).
Der Fertigungsplaner wird seine Aufträge also intuitiv nach Priorität ordnen. Den wichtigsten Auftrag A kann er termintreu nach drei Tagen ausliefern, doch die anderen beiden (B und C) werden das Werk verspätet verlassen. Im schlimmsten Fall stehen hohe Vertragsstrafen und Image-Verlust an.
Kleine Planänderungen wirken sich auf gesamtes Auftragsnetz aus
Warum kann ein ERP-System selbst bei einem solch einfachen Planungsproblem allein keine ausreichende Hilfestellung geben? Ein ERP-System gibt einen Überblick über vorhandene Ressourcen und Geschäftsprozesse. Organisationen sind dadurch in der Lage, Daten abteilungsübergreifend zu managen, zu verteilen und zu integrieren. In der Regel sind in fertigenden Unternehmen aber zehntausende Arbeitsschritte sowie hunderte Materialien und Maschinen engmaschig kausal miteinandervernetzt. Somit wirken sich selbst kleine Planänderungen auf das gesamte Auftragsnetz aus.
Moderne Big-Data-Technologien, Business Intelligence und Business Analytics versuchen hier, aus möglichst vielen Daten möglichst viel Wissen über die Prozesse zu generieren und übersichtlich zu visualisieren. Doch selbst wenn das gelingt, steht der Fertigungsplaner immer noch allein in der Verantwortung, bei Störungen unter Zeitdruck schnell die richtige Entscheidung zu treffen.
Bei den im Maschinenbau üblicherweise kompliziert miteinander vernetzten Arbeitsabläufen stehen den Planern entsprechend viele alternative Planungsoptionen für die Lösungsfindung zur Verfügung. Jede Entscheidung hängt von einer Vielzahl von Faktoren ab: von der Beschaffung von Materialien und Zukaufteilen, die aufeinander aufbauenden Arbeitsschritte der Eigenproduktion und Montage, Maschinenwartungen und -kapazitäten sowie die Schichtplanung unter Berücksichtigung essentieller Qualifikationen.
Gute Entscheidungen lassen sich berechnen
Als alternative Strategie für das operative Management hält die Strategie der Agilen Optimierung Einzug in die Produktion. Denn um über den Erkenntnisgewinn hinaus auch zu optimierten Entscheidungen zu gelangen, bietet sich der Einsatz entscheidungsintelligenter Algorithmen an. Sie leiten aus den vorhandenen Daten der ERP- und PPS-Systeme konkrete Handlungsvorschläge zur schnellen Umsetzung für den Planungsverantwortlichen ab. Es handelt sich um ein durch künstliche Entscheidungsintelligenz gestütztes Verfahren, das nicht nur zur sicheren Termintreue verhilft, sondern auch die übrigen Unternehmensziele wie Kostenreduktion oder eine effiziente Ressourcennutzung im Blick behält.
Mathematische Algorithmen aus Operations Research und Fuzzy Logic berechnen eine Fertigungsreihenfolge, die das bestmögliche Gesamtergebnis für das Unternehmen zum Ziel hat. Im oben genannten Beispiel empfiehlt der Algorithmus am ersten Tag nicht, mit den intuitiv priorisierten Aufträgen A und B zu starten, sondern mit den Aufträgen A und C (Abbildung 2). Die Berechnung hat unter Berücksichtigung der realen Maschinenkapazitäten ergeben, dass sich so immerhin zwei der drei Eilaufträge termingerecht ausliefern lassen. Die Gesamtdurchlaufzeit wird von fünf auf vier Tage reduziert.
Ausserdem ist das Unternehmen in der Lage, transparent Auskunft über sein gesamtes, zentrales Auftragsnetz zu geben und seine Kunden direkt nach der ersten Berechnung über den kommenden Liefertermin zu informieren. Enttäuschungen bleiben aus. Auch für den traditionsreichen Messerhersteller Zwilling lag die Lösung in der Ergänzung ihres ERP-Systems durch ein IT-System zur Agilen Optimierung. Dieses ermöglicht eine sofortige Beurteilung der Machbarkeit von Kundenwunschterminen oder berechnet Projektanfragen und optimierte Produktionsreihenfolgen.
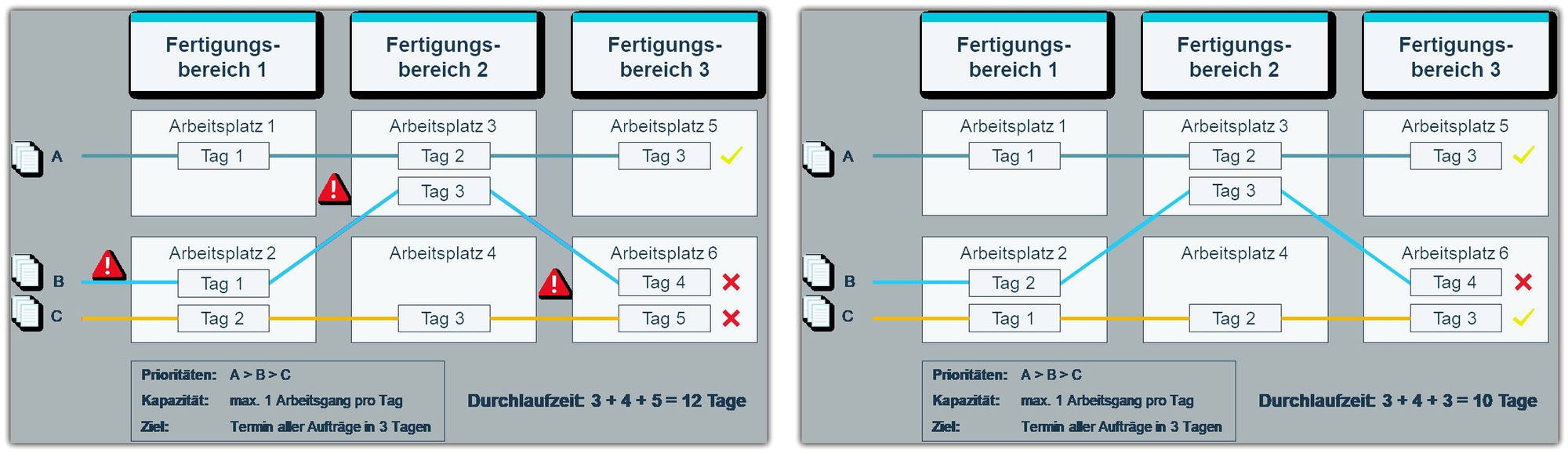
Agile Prozessgestaltung bei Zwilling dank künstlicher Entscheidungsintelligenz
Das über 280 Jahre alte Unternehmen Zwilling stellt seit 1731 hochqualitative Messer her. In einer Kombination aus Handarbeit und Automatisierung produziert Zwilling jährlich über drei Millionen Messer in Serienfertigung mit dementsprechend hohen Losgrössen. Wenn interne oder externe Kunden eine gesonderte Messerlieferung bestellten, die zu einem bestimmten Zeitpunkt sicher ausgeliefert werden musste, war eine verbindliche Terminzusage lange Zeit nicht ohne weiteres möglich.
Dazu fehlten die notwendigen Informationen über die aktuelle Auslastung der Kapazitäten. Denn allein in der Endmontage durchlaufen die zukünftigen Messer bis zu zehn miteinander verknüpfte Arbeitsvorgänge, wodurch sich die Produktionsplanung komplex gestaltet.
Der eingehende Eilauftrag eines Kunden musste in der Vergangenheit unter Verdrängung aller anderen Aufträge in die Produktion eingeschoben und durchgeschleust werden. Damit liess sich der individuelle Kundenwunsch zwar erfüllen, doch die Auswirkungen auf die restliche Fertigung und resultierende Verzögerungen waren kaum abzuschätzen. Inzwischen ist bei Zwilling agile Optimierungssoftware im Einsatz.
Ein APS-System (Advanced Planning and Scheduling) berücksichtigt mit seinen algorithmischen Verfahren alle Veränderungen von Kapazitäten an Personal, Maschinen und Materialverfügbarkeiten und ermöglicht Zwilling so jederzeit eine sofortige Beurteilung der Machbarkeit von Kundenwunschterminen oder Ad-hoc-Projektanfragen.
Trotz Nachfrageschwankungen und steigender Variantenvielfalt kann das Unternehmen so agil agieren: Eine Reduzierung der internen Lieferzeit um 29 Prozent, eine Verdoppelung der Liefertreue sowie eine Senkung der Kapitalbindung um etwa 25 Prozent im ersten Jahr nach Implementierung der Software gehören zu den deutlichsten Erfolgen der Prozessoptimierung bei Zwilling.
Agilität bedeutet Chancen zu nutzen
In der Produktionsplanung sind Add-On-Systeme zur Agilen Optimierung in der Lage, den Fertigungsplan tagesaktuell immer wieder neu an die Gesamtsituation anzupassen. Dabei ist es möglich, dass agile Optimierungssysteme unerkannte Kapazitäten nutzen und in Chancen verwandeln.
So kommt es in der klassischen Auftragsfertigung häufig vor, dass Arbeitsschritte wegen individueller Kundenwünsche, neuer Bestellungen oder anderen Unvorhersehbarkeiten neu geordnet werden müssen. Das Verschieben eines Auftrags mag dabei dazu führen, dass spontan Fertigungskapazitäten frei werden, die eigentlich für den verspäteten Auftrag reserviert waren.
Ein Algorithmus ist in der Lage, auch diese neuen Kapazitäten sofort in die Planung miteinzubeziehen, da er immer den gesamten Betriebszustand im Blick hat. Die frei gewordenen Kapazitäten lassen sich dann beispielsweise dazu nutzen, andere Aufträge vorzuziehen. Im besten Fall können Unternehmen so Verzögerungen wieder ausgleichen.
Agilität ist in diesem Fall keineswegs als Gegenmodell zum an vielen Produktionsstandorten etablierten Lean Management zu verstehen. Sie hilft dort zum Planungserfolg, wo ausschliesslich schlanke Strukturen versagen: in Geschäftsumgebungen, in denen Unvorhersehbarkeit und Komplexität im hohen Masse zusammenkommen (Abbildung 3).
Vier verschiedene Strategien für das operative Management
Je nach Ausprägung der Faktoren Unvorhersehbarkeit und Komplexität eines Betriebsprozesses kommen vier verschiedene Strategien für das operative Management in Frage. Bei gut planbaren Prozessen, die wenig Volatilität aufweisen, empfiehlt sich der Ansatz eines Lean Managements weiterhin. Klassische Serienfertiger mit standardisierten Abläufen gelten hier als prädestinierte Anwender, die schlank und verschwendungsfrei produzieren sollten.
Doch je komplexer die Abläufe, desto wichtiger ist eine gute Planung. Treten nur vereinzelt Störungen auf, reicht Improvisation zur Klärung der Lage oft aus. Fällt hohe Komplexität aber mit vielen Unvorhersehbarkeiten und Zeitdruck zusammen, ist die Ergänzung des ERP-Systems um ein agil optimierendes Add-On der richtige Weg, um die betroffene Betriebsumgebung zu steuern.
Literatur
Titel: Agile Optimierung in Unternehmen
Autoren: Adrian Weiler, Eva Savelsberg, Ulrich Dorndorf
Umfang: 171 Seiten
Verlag: Haufe
Format: E-Book und Print
Impressum
Autor: Adrian Weiler, CEO der Inform GmbH
Bildquelle: Pixabay (Einstiegsgrafik), Inform GmbH (Grafiken im Text)
Aufbereitet durch Technik und Wissen
Informationen
Weitere Artikel
Veröffentlicht am: