Digitales Produktionswerk mit Modellcharakter
Warum DMG Mori mehr als 60 Mio. Euro investierte
Das grosse Interview
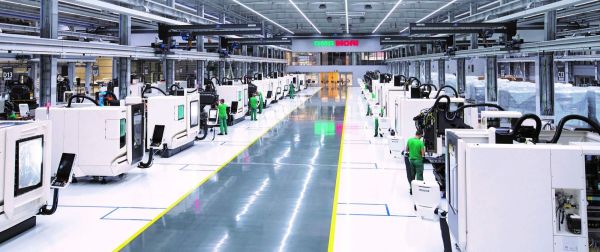
Digitales Produktionswerk mit Modellcharakter
Warum DMG Mori mehr als 60 Mio. Euro investierte
Das grosse Interview
Mit umfassenden Investitionen und weitreichenden Digitalisierungsmassnahmen hat DMG Mori das traditionsreiche Produktionswerk von Famot im polnischen Pleszew zu einer der grössten und modernsten Fertigungsstätten innerhalb der Werkzeugmaschinenbranche ausgebaut.
1877 gegründet, ist die Famot Pleszew Sp. z o. o. mit ihren rund 700 Mitarbeitern einer der traditionsreichsten Standorte von DMG Mori. Mit Investitionen von insgesamt mehr als 60 Millionen Euro hat DMG Mori das Werk – eins der grössten im Konzern – auf eine Gesamtflache von 50.000 m² erweitert, davon 21.000 m² Produktions- und Montagefläche, sowie die Fertigungstechnologien kontinuierlich modernisiert und digitalisiert.
Das erste Werk von DMG Mori agiert über alle Wertschöpfungsebenen hinweg durchgängig digital. Mit modularen Produkten und Services von Istos, DMG Mori Software Solutions und WerkbliQ hat dieses Zukunftsprojekt Modellcharakter. Zbigniew Nadstawski, CTO Famot / Ulyanovsk MT, Dr. Michael Budt, CSO Famot und Marek Osinski, Managing Director DMG Mori Polska berichten, welche Neuerungen in Famot dem Fachpublikum beim Grand Opening am 8. Oktober 2018 vorgestellt wurden.
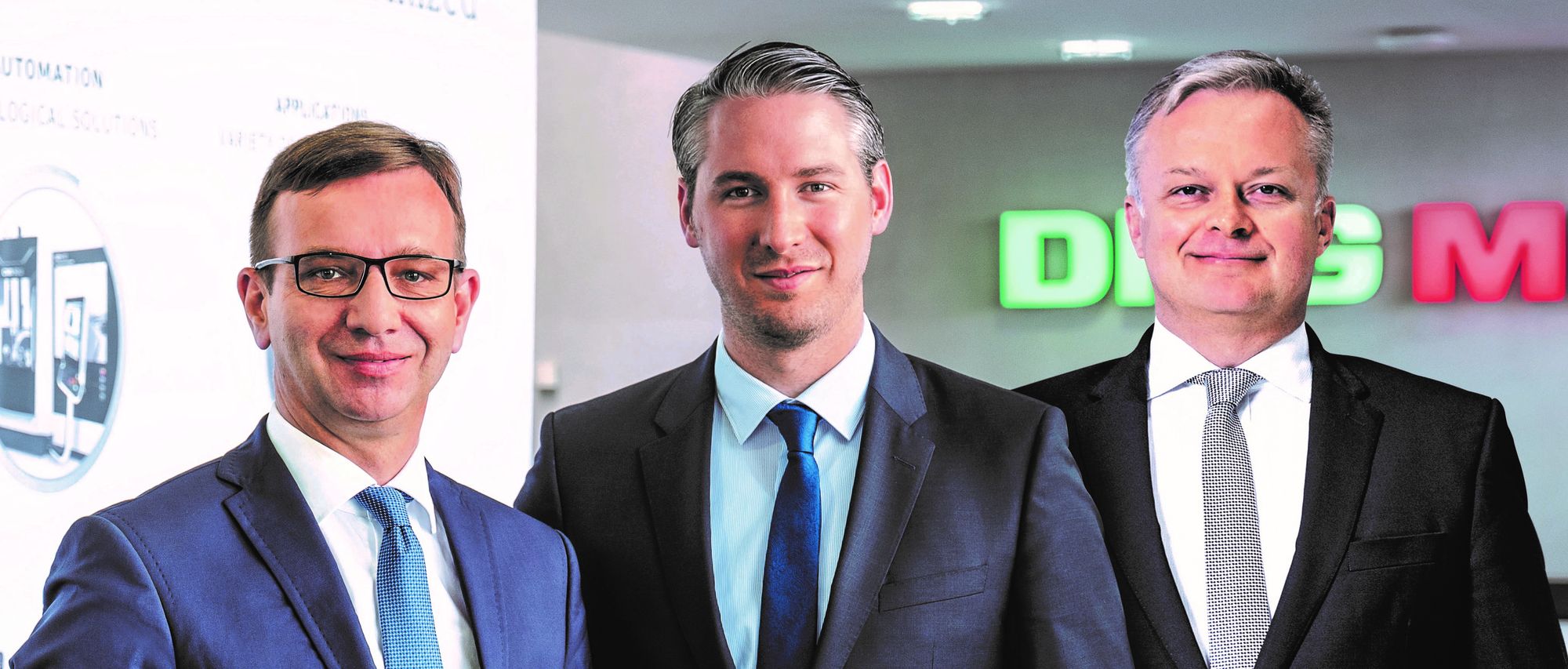
Herr Nadstawski, Herr Osinski, die Digitalisierung im Werkzeug-maschinenbau ist ein Prozess, den DMG Mori seit einigen Jahren konsequent unterstützt. Welche Rolle spielt Famot dabei?
Nadstawski: Mit der grössten eigenen mechanischen Fertigung im Konzern ist Famot bestens geeignet, um DMG Mori Kunden die Vorteile der Digitalisierung zu verdeutlichen. DMG Mori unterstützt seine Kunden ganzheitlich auf dem Weg zur Industrie 4.0 oder zum IIoT und ist Vorreiter in diesem Thema. Um zielführende End-to-End-Lösungen anbieten zu können, müssen natürlich auch wir unsere Digitalisierung vorantreiben. Famot ist das derzeit beste Beispiel. Wir beweisen in der Praxis, wie alle Produktionsprozesse integriert und vereinfacht werden. Hiermit steigern wir unsere zukünftige Wettbewerbsfähigkeit.
Wir erleben ausserdem hautnah, wie sich die digitale Transformation konkret umsetzen lässt, weil wir aktuell durchgängige digitale Lösungen für unsere Produktion umsetzen. Insgesamt markiert das erneuerte Famot Werk jetzt einen Meilenstein sowohl für DMG Mori als auch – mit einem beispielhaften Charakter – für unsere Lieferanten und Kunden. Der Nutzen steht immer an erster Stelle für unsere Kunden, die von DMG Mori in diesem Bereich ganzheitliche und durchgängige Lösungen erwarten.
Hier werden künftig Industrie 4.0 Automaten hergestellt. Zusammen mit dem Ausbau der Logistik
— KonsulatNiemiecWroc (@Kons_Niem_Wro) 8. Oktober 2018
und weiteren Modernisierungen umfasst die Investition 60 Mio €. Famot ist ein
Hauptproduktionsstandort des Deutsch- Japanischen Werkzeugmaschinenherstellers DMG Mori. (2/2) pic.twitter.com/xnvZsBzJmo
Das klingt nach einer digitalen Zeitenwende. Wie sieht diese digitale Transformation bei Famot aus?
Dr. Budt: Wir fügen digital zusammen, was zusammengehört. Insbesondere die Anbindung an die IT-Infrastruktur von DMG Mori bzgl. Auftragsmanagement, Supply Chain und Customer Relationship war entscheidend. Parallel mussten alle Wertschöpfungsebenen inklusive der innerbetrieblichen Abläufe, Systeme und gesteuerten wie manuellen Prozessschritte durchgängig vernetzt werden. Das reichte vom Auftragseingang im Vertrieb bis zum Instandhaltungsmanagement und von der ganzheitlichen Produktionsplanung bis zur hauseigenen MDE/BDE-Software bestehend aus den modularen Applikationen der «Istos Planning Solutions», also «Production Feedback», «production planning» und «production cockpit» für Planung und Überwachung der gesamten Wertschöpfungskette.
Nadstawski: Auch das Personal mussten wir digital fit machen. Für uns sind die Menschen die Basis, um solch eine Mammutaufgabe überhaupt zum Erfolg führen zu können. Ohne die Mitarbeiterinnen und Mitarbeiter würde Innovation nie funktionieren.
Grand Opening FAMOT: Unser Produktionswerk FAMOT ist das erste Werk im Konzern, dass über alle Wertschöpfungsebenen hinweg durchgängig digital agiert. https://t.co/srBID7CITH#newsroom #grandopeningfamot pic.twitter.com/akveQKXefj
— DMG MORI Germany (@dmgmorigermany) 9. Oktober 2018
Was heisst «Mammutaufgabe» konkret?
Dr. Budt: Kernelement der digitalen Fabrik bei Famot ist der sogenannte «Manufacturing Service Bus». Das offene Bus-System ermöglicht die Integration und Integration verschiedener, werkspezifischer Applikationen. Dazu zählen übergreifende Anwendungen wie ERP, HR oder Tool-Management. Hinzu kommen die produktionsorientierten Istos-Applikation unter anderem für Produktionsplanung, MDE/BDE, zentrale Statusvisualisierung sowie für das Stammdaten-Management und die variable Personaleinsatzplanung. Zu weiteren Anwendungen, die über den «Manufacturing Service Bus» kommunizieren zählt die web-basierte Serviceplattform WERKBLIQ der gleichnamigen DMG Mori Tochtergesellschaft. Die Bedeutung des «Manufacturing Service Bus» zeigen allein schon die mehr als 2.000 Mappings, die erstellt worden sind. Das sind (teilweise bidirektionale) Verknüpfungen von Feldern der unterschiedlichen Anwendungen.
Nadstawski: Neben der End-to-End-Performance des Istos-Lösungsansatzes hat uns die kurze Einführungszeit beeindruckt. Immerhin galt es 140 direkte Produktionsarbeitsplätze und knapp 50 Maschinen zu vernetzen. Das ist ein Bereich mit insgesamt 400 Produktionsmitarbeitern, die in Summe 600 Routings bzw. Arbeitsvorgänge und über aktive 3.000 Fertigungsaufträge abzuarbeiten haben.
Projekte in der Grössenordnung haben oft eine Laufzeit von ein bis zwei Jahren. Wir haben das System in rund sechs Monaten auf den Weg gebracht. Zum einen ist das dem exzellenten Projektmanagement seitens Istos zu danken, die durchschnittlich mit drei Mitarbeitern vor Ort waren. Zum anderen hätte das Projekt ohne die hohe Motivation und Kompetenz unseres interdisziplinären Projektteams mit Verantwortlichen aus Produktion, Montage, Mechanische Fertigung und IT niemals so schnell realisiert werden können. Istos und Famot haben ein gemeinsames Ziel und pflegen eine sehr gute Zusammenarbeit.
Welche Ziele haben Sie mit der digitalen Erneuerung?
Dr. Budt: Es geht um effiziente, schnelle und sichere Produktionsprozesse sowie insgesamt eine nachhaltige Steigerung von Produktivität, Qualität, Transparenz und Reaktionsvermögen. Im Pflichtenheft stand ebenso die Forderung, bestehende Insellösungen und neue Softwaresysteme zu einem durchgängig agilen Produktionsnetzwerk zu verbinden.
Woher kam die dafür nötige Kompetenz?
Nadstawski: Wir haben selbstverständlich unsere digitalen Konzerngeschwister einbezogen. Dazu gehört die Istos GmbH. Die 2017 gegründete DMG Mori Tochter Istos unterstützt mit den Produkten der Planning Solutions Fertigungsunternehmen dabei, mehr Effizienz und Agilität in der Produktion entlang der gesamten Wertschöpfung zu erreichen. Wir haben schon immer eine Lösung gesucht, die alle unsere Systeme integriert sowie die automatische Produktionsplanung und Steuerung ermöglicht. Gemeinsam mit Istos verbinden wir unsere Produktions-Excellence mit den neuen digitalen Kompetenzen und schaffen aus dieser Symbiose die beste Basis für die zukünftige Wettbewerbsfähigkeit.
Dazu gehören aber auch die DMG Mori Software Solutions mit Celos und WerkbliQ mit ihrer webbasierten Instandhaltungs- und Service-Plattform. Auf deren Basis agieren alle Einheiten des Systems – zum Beispiel Auftragsverwaltung, Betriebsdatenerfassung oder Stammdatenmanagement – einerseits autonom, andererseits sind sie über den sogenannten Service Bus verbunden. Dieser übernimmt die Funktion eines Vermittlers, über den alle angeschlossenen Anwendungen basierend auf einem einheitlichen Datensatz bidirektional kommunizieren.
Unterwegs in Polen:
— Julia Dusold (@JuliaDusold) 8. Oktober 2018
Dr. Mori and Christian Thönes von #DMGMori eröffnen feierlich FAMOT in Pleszew, eine der größten Werkzeugmaschinenfabriken in Zentraleuropa.
Hier werden Maschinen und Komponenten für die DMG Mori Gruppe gefertigt. pic.twitter.com/93Ms7A6R7b
Die digitale Transformation ist bei Famot ein Teil umfassender Investitionen, die DMG Mori am Standort seit einiger Zeit tätigt. Wie hat sich das Traditionswerk in den vergangenen Jahren weiterentwickelt?
Dr. Budt: Famot verzeichnet seit Jahren ein stetig wachsendes Auftrags- und Produktionsvolumen – sowohl im Bereich der Rumpfmaschinen und DMG Mori Components für den DMG Mori Konzern als auch ganz besonders in unserem Universalmaschinensegment der CLX und CMX Baureihen. Deshalb müssen wir unsere Kapazitäten kontinuierlich ausbauen. Die Investitionen von insgesamt 60 Millionen Euro waren und sind absolut notwendig, um die geschäftliche Entwicklung aufrecht zu erhalten, die steigende Marktnachfrage zu bedienen und unser eigenes Sortiment kontinuierlich weiter zu optimieren. Darüber hinaus sind weitere 30 Millionen Euro für die Erweiterung der mechanischen Bearbeitung und die neue XXL Halle freigegeben, in der DMG Mori Components bearbeitet werden – unter anderem auf der DMU 600 P, der grössten Maschine im DMG Mori Produktportfolio.
Die Investitionen von insgesamt 60 Millionen Euro waren und sind absolut notwendig, um die geschäftliche Entwicklung aufrecht zu erhalten, die steigende Marktnachfrage zu bedienen und unser eigenes Sortiment kontinuierlich weiter zu optimieren.
Osinski: Das zeigt sich auch besonders in unserem Heimatmarkt Polen. Polnische Kunden fragen sowohl nach Maschinen als auch nach lokalem Service und starken Partnern möglichst nah an der Fertigung. Mit unserem Produktionswerk Famot sowie der Vertriebs- und Servicegesellschaft DMG Mori Polen können wir unsere Kunden in ganz Polen optimal unterstützen – vor allem mit unseren attraktiven Lieferzeiten von durchschnittlich vier bis acht Wochen.
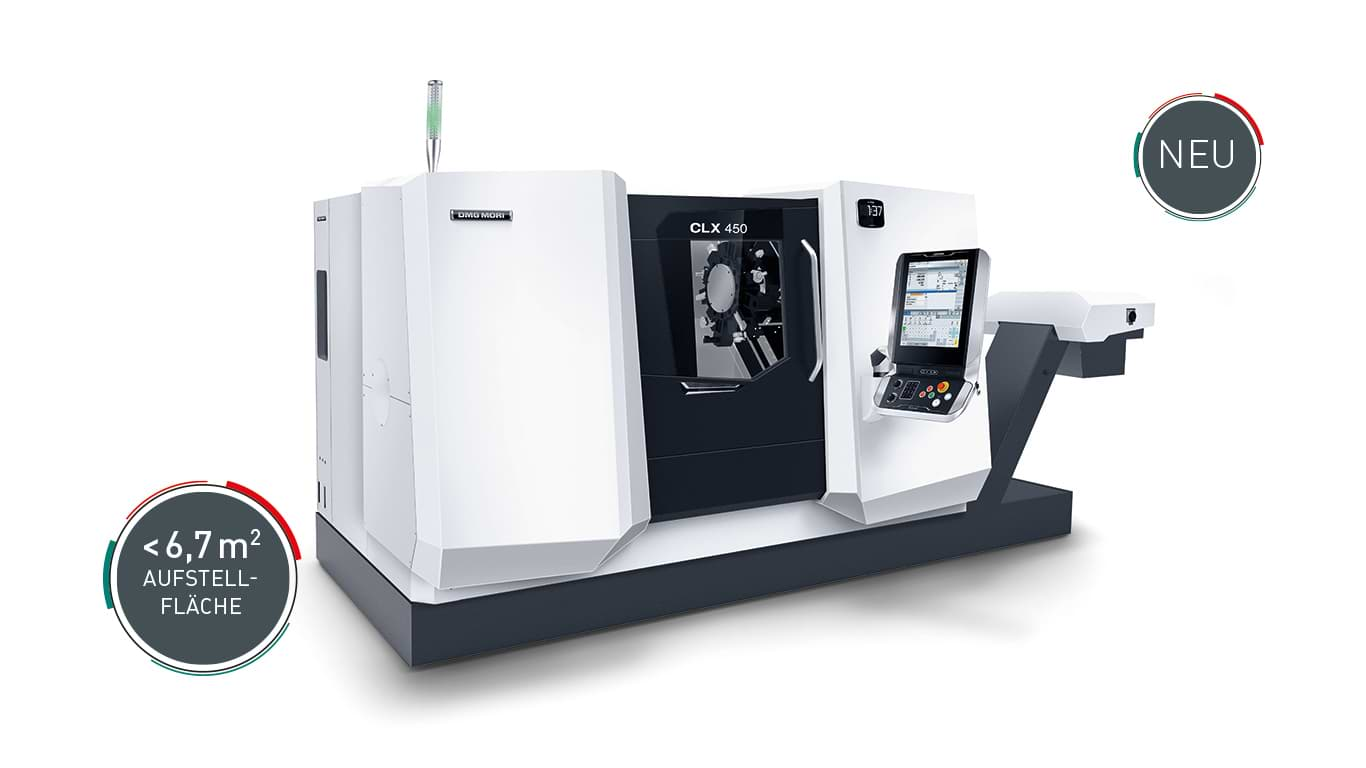
Worin zeigt sich die höhere Kapazität von Famot?
Nadstawski: Bis 2020 wollen wir mehr als 2.000 eigene Werkzeugmaschinen sowie zusätzlich 2.000 Rumpfmaschinen und weitere Komponenten und Teilesätze für insgesamt weitere 3.000 Werkzeugmaschinen fertigen. Ausserdem möchten wir zukünftig einen Umsatz von 300 Millionen Euro erzielen – und das ist «nur» unser Tagesgeschäft. Die Investitionen betreffen sowohl unsere Strukturen als auch unsere Fertigungstechnologie. Die Produktionsfläche beträgt heute insgesamt 21.000 m², ein Drittel davon gehört der Montage.
Hinzu kommen ein neues grosses Rohgusslager und ein neues Logistikcenter. Über ein KARDEX-Kleinteilelager werden pro Tag 140.000 Teile an die vielzähligen Stationen in Produktion und Montage verteilt. Eine Induktivhärteanlage – zur Bearbeitung von Komponenten der aktuellen CTX Baureihe – komplettiert die enorme Fertigungstiefe von Famot.
Dr. Budt: Herzstück von Famot ist die mechanische Fertigung – die grösste im Konzern. Über 50 Produktionsmaschinen überwiegend aus dem DMG Mori Sortiment laufen derzeit vernetzt rund um die Uhr, um den enormen Bedarf sicherzustellen. Pro Jahr verlassen mehr als 1.600 vorproduzierte Rumpfmaschinen sowie hunderte Baugruppen und Komponenten das Werk in Richtung der Schwestergesellschaften Deckel Maho Pfronten, Deckel Maho Seebach, Gildemeister Drehmaschinen in Bielefeld und anderer Konzernstandorte.
Die Bearbeitung der Rumpfmaschinen und Komponenten erfolgt auf einer DMC 340 U und einer DMC 270 U aus der Grossmaschinenbaureihe von DMG Mori. Im Juli 2019 werden wir zusätzlich eine neue hochmoderne, energieeffiziente XXL Machining Halle mit zwei DMU 600 P mit Doppeltisch und drei DMU 210 P mit linearem Palettenpool (LPP) haben, um unsere Kapazitäten in der XXL-Bearbeitung auszubauen. Eine Schleiferei mit fünf Maschinen, unter anderem einer Taiyo Koki Schleifmaschine von DMG Mori, ein hochmoderner Messraum und eine eigene Spindelproduktion runden das Leistungsspektrum in der Fertigung ab.
Wichtigstes Standbein im Tagesgeschäft sind die selbst entwickelten und in Famot produzierten CLX, CMX V und CMX U Baureihen. Welche Neuerungen sind hier zu nennen?
Dr. Budt: Unser jüngster Maschinenzugang ist die CLX 450 mit höherer Drehlänge für Werkstücke bis ø 315 x 800 mm in der Version mit Y-Achse und Gegenspindel. Diese verfährt um 120 mm. Durch ihre Gegenspindel ermöglicht sie die 6-Seiten-Komplettbearbeitung von anspruchsvollen Bauteilen. Die Hauptspindel überzeugt mit einem hohen Drehmoment von bis zu 426 Nm. Für eine hohe Genauigkeit sorgen direkte Wegmesssysteme von Magnescale in der X- und Y-Achse, optional auch in der Z-Achse. Steuerungsseitig haben wir sowohl SIEMENS als auch FANUC im Angebot. Dieses starke Gesamtpaket benötigt gerade einmal 6,7 m² Aufstellfläche. Somit sind alle CLX Universal-drehmaschinen von DMG Mori in allen technologischen Ausbaustufen sowie mit zahlreichen Technologiezyklen und Hard- und Softwareoptionen verfügbar – individuell konfigurierbar nach den anwendungsspezifischen Anforderungen unserer Kunden.
Automationslösungen sind für DMG Mori eins der wichtigsten Kernthemen, so dass auch Famot in diesem Bereich sein Angebot ausgebaut hat.
Automationslösungen sind für DMG Mori eins der wichtigsten Kernthemen, so dass auch Famot in diesem Bereich sein Angebot ausgebaut hat. Kunden bekommen hier ab Werk produktive Standardautomationen im Bereich Paletten- und Werkstückhandling. Alle CLX Drehmaschinen lassen sich zum Beispiel mit Hilfe des neuen Robo2Go 2nd Generation automatisieren. Der Roboter ist wahlweise mit 10 kg, 20 kg oder 35 kg Traglast erhältlich und bewegt Werkstücke bis ø 170 mm. Seine dialoggeführte Steuerung ist auch ohne vorherige Roboter¬programmierkenntnisse leicht zu bedienen. Darüber hinaus lassen sich alle CLX Maschinen mit unseren GX Gantry Loader oder individuell ausgearbeiteten Lösungen automatisieren.
Eine Roboterlösung für die Fräsmaschinen der CMX V und CMX U Serien ist die WH CELL. Das modulare Automationssystem kann für verschiedenste Werkstücke ausgelegt werden und ist mit Einfach- oder Doppelgreifer verfügbar – inklusive kundenspezifischer Greiferbacken. Die CMX V und CMX U Baureihe ist darüber hinaus mit Hilfe des Paletten-Handlings PH 150 automatisierbar. Die Traglast liegt bei 150 kg oder optional 250 kg, während zwei Palettengrössen möglich sind: zehn Paletten mit jeweils 320 × 320 mm oder sechs Paletten mit je 400 × 400 mm. Wir können unseren Kunden somit ein breites Portfolio an Automationslösungen sowohl im Drehen als auch im Fräsen anbieten – und das alles aus einer Hand ab Werk.
Haben die höheren Produktions- und Verkaufszahlen Auswirkungen auf Ihren Personalbedarf?
Nadstawski: Auf jeden Fall. Gleichzeitig aber ist das Wachstum im Personal nicht unser Hauptziel. Wir sind sicher, dass Digitalisierung und Automatisierung in mehr Effizienz resultieren. Sowohl in der Fertigung als auch im Service sind wir auf erfahrene Mitarbeiter und kompetenten Nachwuchs angewiesen. Famot ist in der Region einer der grössten Arbeitgeber und weil wir immer an guten Fachkräften interessiert sind, kooperieren wir mit über 15 technischen Schulen und Universitäten aus der Region.
Osinski: Investitionen in das Werk, die unsere Kapazität erhöhen, motivieren unser Verkaufsteam, mehr lokal produzierte Maschinen im heimischen Markt zu platzieren. Unsere Entscheidungsträger erwarten von uns, die Verkaufszahlen auch mit einem Fokus auf die lokale Produktion zu steigern. Unsere Pläne sind ambitioniert. Deshalb erwarten wir von unserem Verkaufsteam, sich zu engagieren und zu motivieren, diese Maschinen im polnischen Markt zu verkaufen.
Wir sind stolz, die Zahl unserer Servicetechniker in den vergangenen fünf Jahren auf 50 verdoppelt zu haben. Und das ist nicht unser letztes Wort.
Die Latte ist sehr hoch gelegt. Mit der harten Arbeit aller Teammitglieder erreichen wir die erforderlichen Zahlen. Dabei geht es nicht um die einzelnen Vertriebsmitarbeiter, denn wir investieren auch in anderen Bereichen unserer Organisation. Beispielsweise gelten dieselben Massstäbe auch für die Weiterentwicklung unseres Aftermarkets und der Serviceabteilung.
DMG Mori Polen investiert kontinuierlich in die bestehende Teamkompetenz und parallel dazu rekrutieren wir neue Servicetechniker. Wir sind stolz, die Zahl unserer Servicetechniker in den vergangenen fünf Jahren auf 50 verdoppelt zu haben. Und das ist nicht unser letztes Wort. Wenn wir über Servicequalität und den Aftermarket allgemein sprechen, machen wir keine Kompromisse. Darüber hinaus investieren wir in den Ausbau unserer Anwendungstechnik, im Werk Famot als auch bei DMG Mori Polska. Dies ist absolut notwendig, um unsere vielen Kunden vor allem in der Aerospace-Branche bestmöglich zu unterstützen – denn von allen Branchen ist Aerospace für DMG Mori in Polen die Branche Nummer 1.
Impressum
Textquelle: DMG Mori
Bildquelle: DMG Mori
Publiziert von Technik und Wissen (ea)
Informationen
Weitere Artikel
Veröffentlicht am: