Beschleunigung um Faktor 10 ist beim
3D-Druck keine Illusion
Fraunhofer-Leitprojekt futureAM auf der Formnext
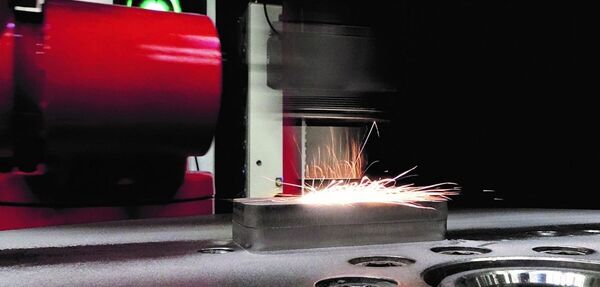
Beschleunigung um Faktor 10 ist beim
3D-Druck keine Illusion
Fraunhofer-Leitprojekt futureAM auf der Formnext
Beim Extremen Hochgeschwindigkeits-Laserauftragschweissen (EHLA) gelang mit einer neuen Anlage der Schritt von der Beschichtung zur echten additiven, dreidimensionalen Fertigung. Bild: Fraunhofer ILT, Aachen
Mutig starteten sechs Fraunhofer-Institute das Fraunhofer-Leitprojekt «futureAM – Next Generation Additive Manufacturing»: Sie wollten 3D-Druck mit Metallpulver um den Faktor 10 beschleunigen und den Prozess ganzheitlich weiterentwickeln. Auf der Formnext zeigt das futureAM-Team, was es bereits erreicht hat.
Bisher bremste die geringe Produktivität des Additive Manufacturings von Metallbauteilen (Metall AM) den Prozess. 2017 startete daher das Fraunhofer-Leitprojekt «futureAM – Next Generation Additive Manufacturing» unter Koordination des Fraunhofer-Instituts für Lasertechnik ILT. Seitdem bündeln sechs Fraunhofer-Institute ihr Know-how und ihre Erfahrung auf dem Gebiet, um die komplette Prozesskette des Metall AM ganzheitlich von der Auftragsabwicklung über Design und Simulation bis hin zur Fertigung in den Maschinen zu optimieren und um den Faktor 10 zu beschleunigen. Christian Tenbrock, wissenschaftlicher Mitarbeiter am Aachener Fraunhofer-Institut für Lasertechnik ILT und futureAM-Projektkoordinator: «Eine wichtige Rolle spielt das ‹Virtual Lab›, das in enger Zusammenarbeit der beteiligten Institute entsteht.»
Weil die beteiligten Institute innerhalb des Projektes vier Handlungsfelder betreuen, in denen sie die teilweise sehr unterschiedlichen Bereiche der gesamten Prozesskette abdecken, verteilen sich die sonst in einer Produktion vereinten Teilprozesse auf sechs Institute. Das Virtual Lab soll künftig über ein Netzwerk und eine Datenbank alle Bereiche und Institute in Sachen AM digital miteinander verknüpfen. Fritz Lange von der der Fraunhofer-Einrichtung für Additive Produktionstechnologien IAPT: «Die Institute werden über das Virtual Lab die verteilte Fertigung abwickeln und nachvollziehen.» Geplant ist dazu die geschlossene digitale Abbildung der Kompetenzen und Ausstattung der beteiligten Institute.
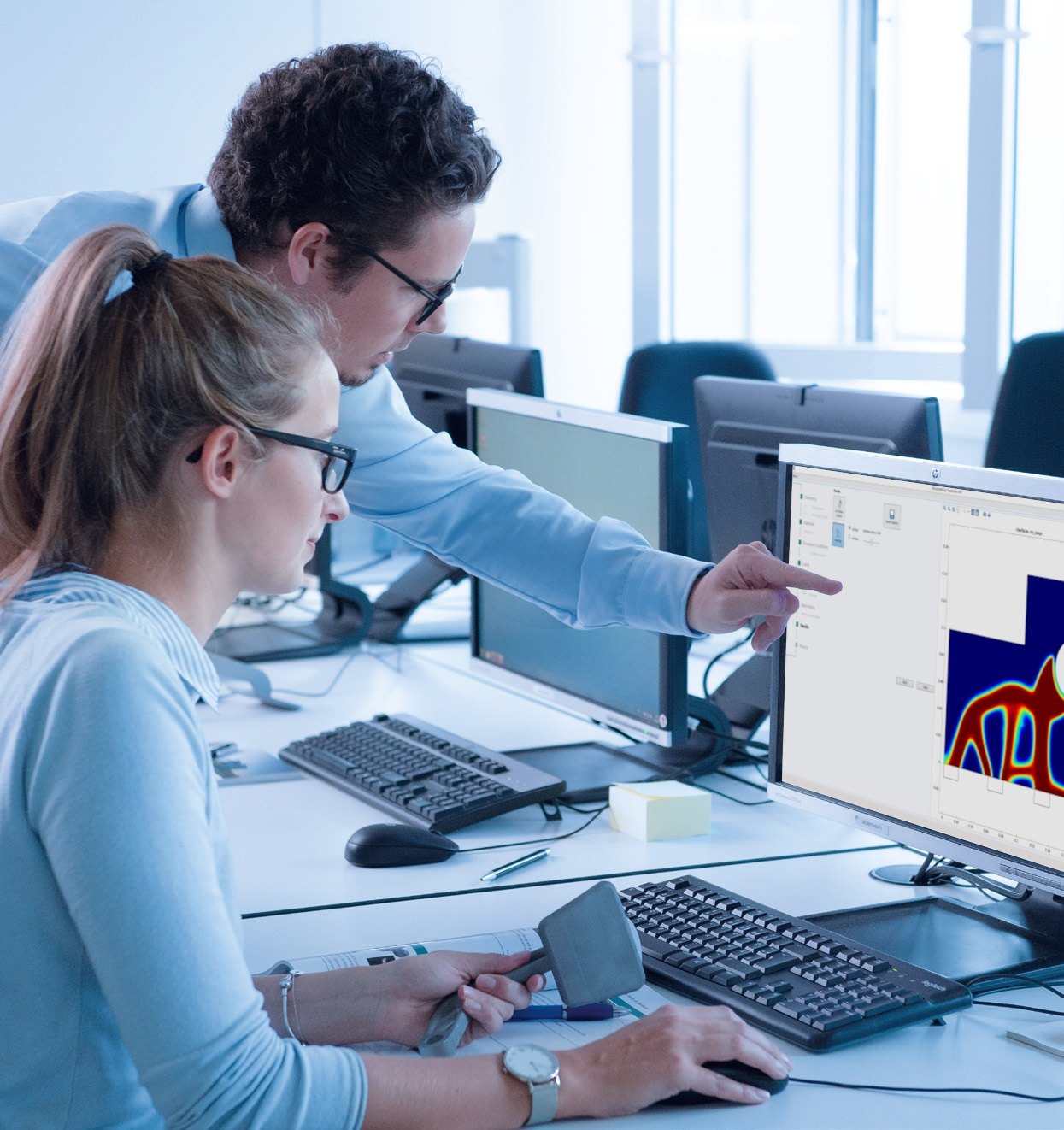
Gesamter AM-Prozess transparent und digital
Das Virtual Lab macht den gesamten AM-Prozess transparent und spiegelt ihn digital: Diese Aufgabe übernehmen digitale Zwillinge als virtueller Teil einer cyberphysischen Maschine oder eines grösseren cyberphysischen Systems. Die Digital Twins ermöglichen den Projektteilnehmern, Prozesse zu modellieren und zu simulieren, um so reale Systeme in allen Bereichen zu optimieren. Auf der Formnext demonstriert das futureAM-Team die Arbeitsweise. «Wir können als für Design zuständiges Institut z. B. einem medizinischen Implantat, einem der Demonstratoren, die Metadaten zuweisen, während ein anderes Institut die Materialkennwerte beisteuert», berichtet Lange.
Anschliessend startet das dritte Institut mit heruntergeladenen CAD-Daten und eigenen Maschinendaten die Bearbeitung und leitet die erweiterten Datensätze zur Nachbearbeitung via Virtual Lab weiter. Damit spiegelt die Zusammenarbeit über das Virtual Lab auch den ganzheitlichen Gedanken, der dem Projekt futureAM zugrunde liegt.
Das Virtual Lab nutzen beispielsweise Experten des Fraunhofer-Instituts für Werkstoff- und Strahltechnik IWS aus Dresden beim Managen von Prozessdaten. Die Dresdner betreuen den Part Werkstoffe im Fraunhofer-Leitprojekt. Zwei Ziele haben sie im Visier: Die Erweiterung des einsetzbaren Spektrums von additiv verarbeitbaren Werkstoffen und ausserdem die Multi-Material-Bauweise. Hier entsteht massgeschneidert mithilfe des Laserauftragschweissens (LMD) ein Bauteil aus verschiedenen Werkstoffen ohne nachgelagerte Fügeprozesse. «Das Verfahren beschleunigt die Materialentwicklungen enorm», sagt IWS-Wissenschaftler Michael Müller. «Wir erforschen im Verbundprojekt, welche Materialien sich miteinander kombinieren lassen und welche Probleme dabei auftreten.» Aktuell untersuchen die Dresdener Wissenschaftler, wie sich beispielsweise aus verschiedenen Superlegierungen ein Multi-Material-Bauteil herstellen lässt.
Die Übergangszone zwischen Materialien im Visier
Wichtig beim Fügen von zwei Werkstoffen ist die Analyse der Übergangszone zwischen den Materialien. Den Materialübergang der Legierung Inconel 718 zu Merl 72 haben die Forscher mittlerweile optimiert, um Herausforderungen wie Rissbildung oder Versprödung zu minimieren. Aktuell untersucht das Fraunhofer IWS, wie sich z. B. aus Titan und Aluminium ein Multi-Material-Bauteil herstellen lässt. Je nach Bauteilanforderungen nehmen sie wahlweise ein drittes oder viertes Element hinzu, um die Eigenschaften exakt anpassen zu können.
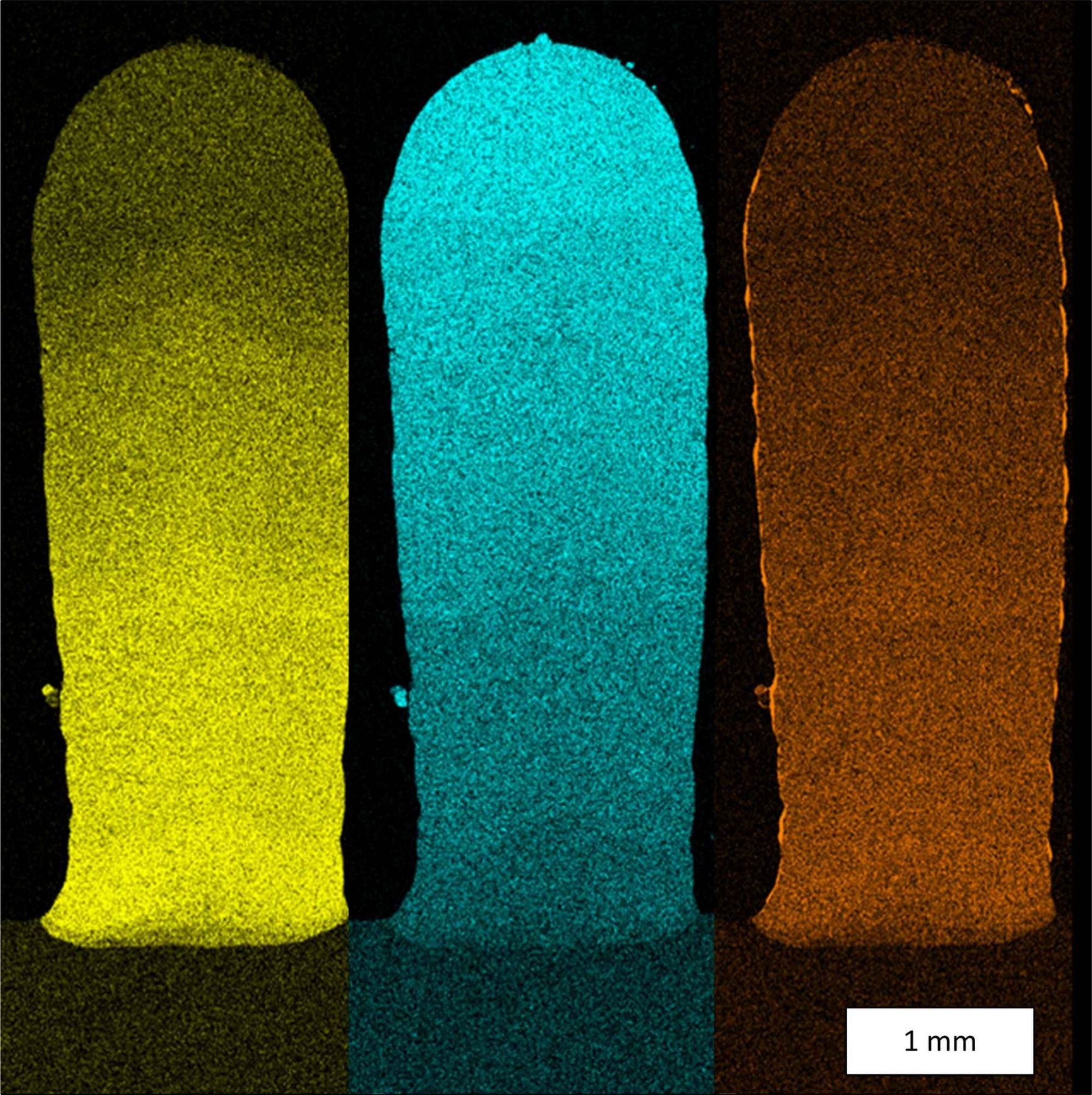
Neue skalierbare Metal AM-Prozesse und -Anlagen sind das Thema des Fraunhofer ILT: Grosse Fortschritte haben die Aachener beim Extremen Hochgeschwindigkeits-Laserauftragschweissen (EHLA) erreicht: Es gelang ihnen der Schritt von der Beschichtung, einem 2D-Druckverfahren, zur echten Additiven Fertigung, dem 3D-Druck. Entstanden ist eine 3D-EHLA-Anlage, bei der die Bauplattform extrem schnell parallelkinematisch von drei Linearantrieben mit stillstehendem Laser-Bearbeitungskopf bewegt wird.
3D-Bauteile im XXL-Massstab
3D-Bauteile im XXL-Massstab hat auch die zweite Innovation im Visier. Für das Laser Powder Bed Fusion (LPBF) wurde ein neues, kompaktes Optiksystem entwickelt. Es kommt zum Einsatz im ersten Prototyp, der dank seines Bauraums (1000 mm x 800 mm x 500 mm) auch grosse Metallbauteile bis zu zehnmal schneller als übliche LPBF-Anlagen additiv herstellen kann.
Ein weiteres Highlight ist ein Software-Modell zum Steuern des Energieeintrags bei der Bearbeitung des Pulverbettes: Die Prozessparameter können dabei für jede einzelne Schmelzspur individuell eingestellt werden, um sowohl die Bauteilqualität als auch die Baugeschwindigkeit zu steigern.
Durch diese gezielte Parameterwahl können z. B. Überhitzungen im Bauteil vermieden werden. «Wir berücksichtigen die lokalen geometrischen Eigenschaften des Bauteils, um eine massgeschneiderte Prozessführung zu realisieren. Auf diese Weise lässt sich beispielsweise die Menge benötigter Stützstrukturen in Überhängen deutlich reduzieren oder sogar ganz eliminieren», sagt Tenbrock. «Zudem können wir die Bearbeitungszeit reduzieren, indem wir in massiven Bauteilbereichen die Scangeschwindigkeit erhöhen.»
Besonders hoch ist beim Metall AM die Nachbearbeitung, die zurzeit bis zu 70 Prozent der gesamten Prozesskosten verursacht. «Es handelt sich dabei grösstenteils um Handarbeit», erläutert Dr. Ines Dani vom Fraunhofer-Institut für Werkzeugmaschinen und Umformtechnik IWU in Chemnitz. «Diese Bearbeitungsschritte wurden bisher nicht automatisiert, unter anderem aufgrund der unterschiedlichen Geometrien. Das soll sich nun ändern.»
Nachbearbeitung aus dem Baukasten
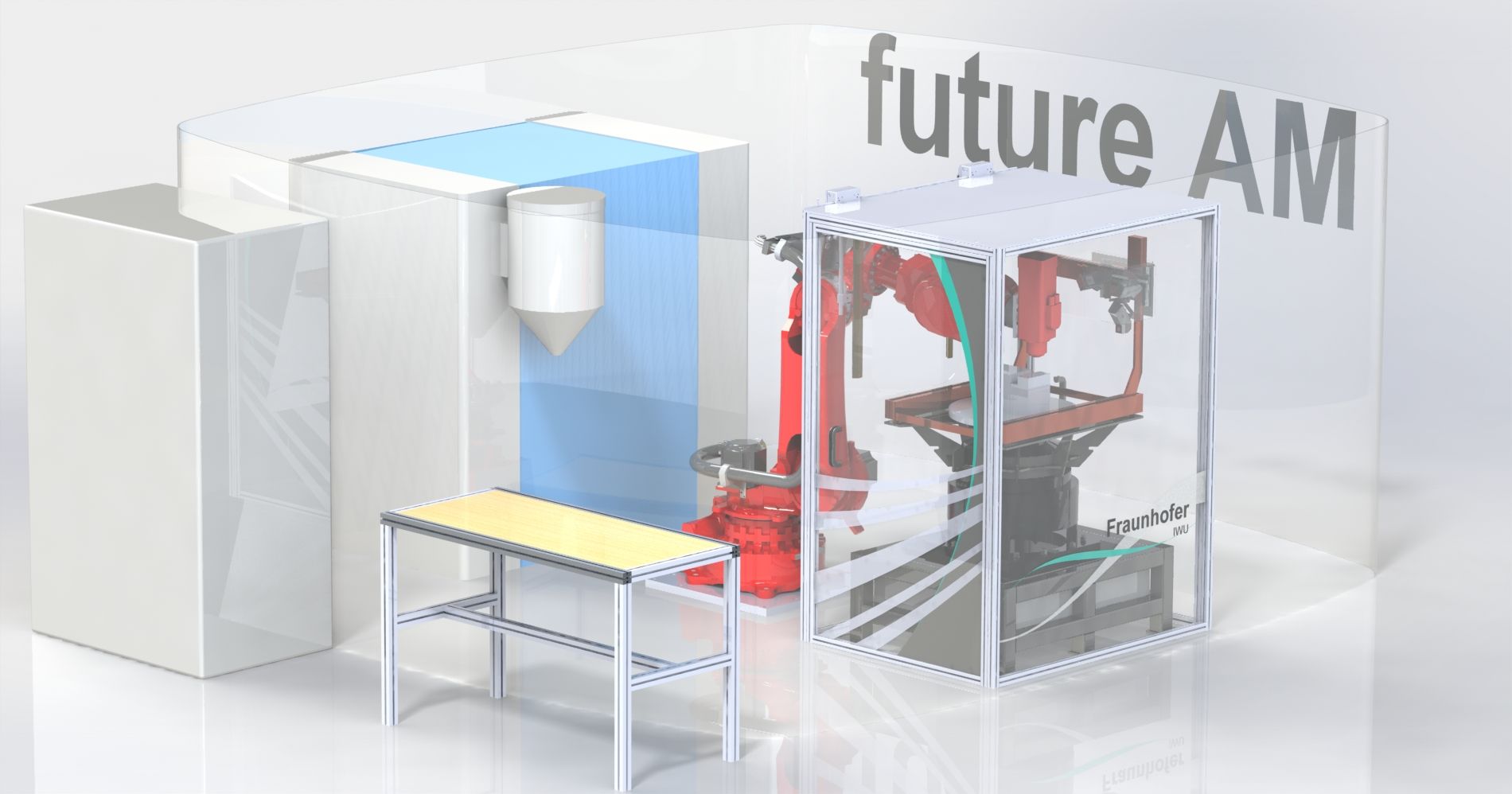
Um das Problem gezielt anzugehen, hat das Fraunhofer IWU die Aufgabenstellung aufgeteilt: Automatisiert werden sollen im Projekt Nachbearbeitungsschritte im und ausserhalb des 3D-Druckprozesses. So wird beispielsweise ein Roboter im Bauraum das Werkstück-Handling übernehmen. Dr. Dani: «Die Greifer haben wir, bei der Steuerung befinden wir uns in der Konzeptphase.»
Für die eigentliche, abschliessende Nachbearbeitung und die einzelnen Prozesse entwickelt Chemnitz verschiedene, autonom arbeitende Technologie-Module. Ein Identifikationsmodul identifiziert das Bauteil und zusätzliche Sensoren helfen bei der Orientierung. Das Modul holt sich die digitalen Informationen über das Bauteil aus der CAD-Datei, um dann anhand der vorgegebenen Stützstrukturen mit Hilfe eines Roboters gezielt den Schneidvorgang zu starten. Zwei Laserlinienscanner vermessen abschliessend jeden Bearbeitungsprozess, damit der Roboter das Bauteil eventuell erneut nachbearbeitet.
Fraunhofer auf der Formnext
Mehr über den aktuellen Stand der Metall AM-Technik erfahren Interessenten auf der Formnext vom 19. bis 22. November 2019 auf dem Fraunhofer-Gemeinschaftsstand D51 in Halle 11.
Impressum
Autor: Nikolaus Fecht im Auftrag des Fraunhofer-Leitprojekts futureAM
Bildquelle: Fraunhofer
Publiziert von Technik und Wissen
Informationen
Weitere Artikel
Veröffentlicht am: