Der Roboter und sein Bearbeitungszentrum
Prozesssichere Lösung für viele Varianten
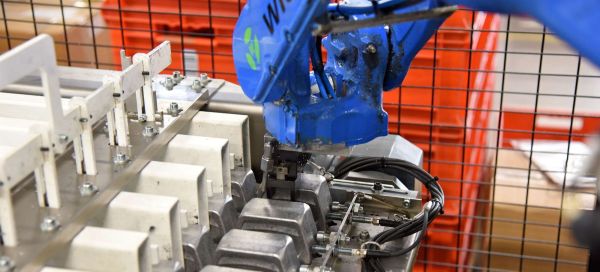
Der Roboter und sein Bearbeitungszentrum
Prozesssichere Lösung für viele Varianten
Die Automation von Werkzeugmaschinen mit Robotern ist heute Standard, kann jedoch bei einem vielfältigen Teilespektrum schnell zur Herausforderung werden. Doch auch für schwierige Fälle gibt es Lösungen.
Die Wieland Electric GmbH ist ein mittelständisches Familienunternehmen mit Stammsitz in Bamberg. Dort entstehen auch die robusten Gehäuse für die Industriesteckerserie revos. Ein Müga S500 Bearbeitungszentrum übernimmt dabei die spangebende Bearbeitung der Gehäuseober- und unterteile, bei der insbesondere Bohrungen einzubringen und Gewinde zu schneiden sind. Von Hand wurde früher noch die Be- und Entladung der Werkzeugmaschine vorgenommen.
Herausforderung: Hohe Anzahl Gehäusevarianten und Schüttgut
Für Frank Hennemann, Fertigungsplaner bei Wieland, war dies seit geraumer Zeit ein Dorn im Auge. Die Arbeiter höherwertige Arbeit verrichten und wahrscheinlich leidet auch die Produktivität darunter. Die Firma EGS Automatisierungstechnik hat bereits hunderte von Automationslösungen für Werkzeugmaschinen realisiert wurde von Wieland Electric hinzugezogen.
Doch auch für die Experten von EGS stellte sich die Aufgabenstellung bei Wieland als echte Herausforderung dar, wie EGS-Vertriebsleiter Heiko Röhrig schnell bemerkte: «Zwei Faktoren waren es, die uns die Konzeption erschwerten: Erstens die hohe Anzahl an Gehäusevarianten und zweitens das Arbeiten von Schüttgut in Schüttgut. Das heisst, die Gehäuse kommen ungeordnet in Metallbehältern an und sollen die Anlage auch wieder als Schüttgut verlassen.»

Hochflexibles Zuführsystem bringt die Lösung
Obgleich eine geordnete Bereitstellung der Teile in Werkstückträgern oder Paletten somit nicht in Betracht kam, fand sich im Standardprogramm von EGS ein passendes Zuführsystem, das mit einigen wenigen Modifikationen die Lösung darstellen konnte: der SUMO Flexiplex. Bei diesem hochflexiblen Beladesystem erfolgt der Transport der Werkstücke über mehrbahnige Staubänder.
Grosser Vorteil für diese Lösung: Alle Varianten der Steckergehäuse verfügen über ein identisches Merkmal: die Breite, die immer zwischen 42,5 und 43,5 Millimeter liegt. Somit muss die Spurbreite des Flexiplex bei einer Umrüstung nicht verstellt werden, weshalb die Zuführung bei Wieland auf diese Verstelloption komplett verzichtet. Mit der unterschiedlichen Teilelänge, die je nach Variante zwischen 60 und 140 Millimeter variiert sowie der Höhe der Gehäuse, die im Bereich von 24 bis 90 Millimeter liegt, kommt die EGS-Zuführlösung ebenso problemlos zurecht wie mit den vielen Sonderformen der Gehäuse, die teilweise über Edelstahlbügel oder Verriegelungsbolzen verfügen. Lediglich ein Teileniederhalter musste zusätzlich montiert werden.
Robuster Sechsachs-Roboter
Im Gegensatz zur Zuführung gestaltete sich die Wahl des richtigen Roboters einfach. Röhrig: «Obgleich wir auf Kundenwunsch Roboter aller Hersteller einsetzen können, haben wir uns aus gutem Grund auf Yaskawa spezialisiert. Die Motoman Sechsachser sind aufgrund ihrer robusten Ausführung perfekt geeignet für den rauen Einsatz an und in Werkzeugmaschinen. Ausserdem überzeugen sie durch hohe Präzision, hervorragende Dynamik und ein gutes Preis-Leistungsverhältnis.»
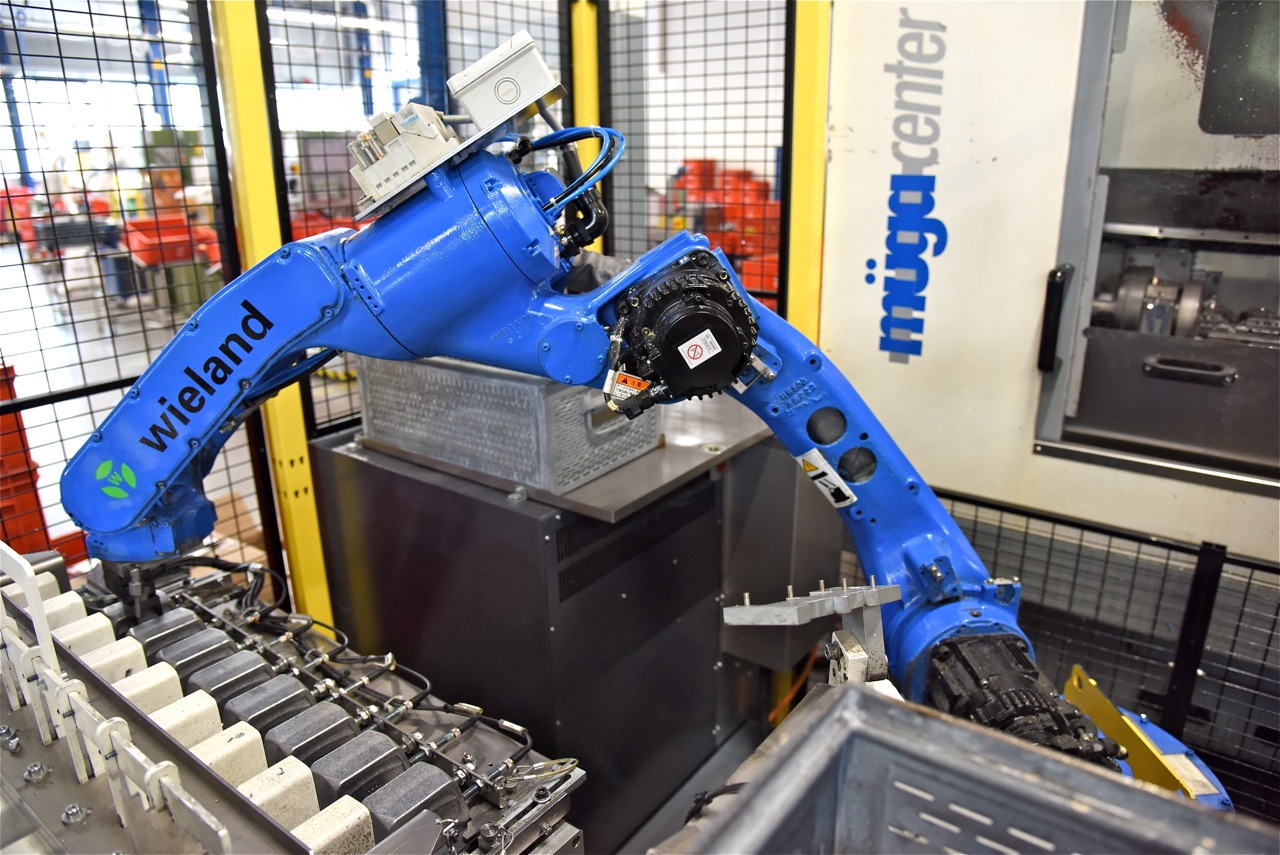
Im Einsatz: Motoman MH12
Im konkreten Fall wählte EGS den Motoman MH12 für sämtliche Handhabungsaufgaben innerhalb der mit einem Schutzzaun gesicherten Zelle. Die lagerichtige Bestückung der insgesamt acht Spuren des Flexiplex mit unbearbeiteten Teilen bleibt ebenso Aufgabe des Anlagenbedieners wie die Bevorratung leerer Metallbehälter für die Aufnahme bearbeiteter Teile. Die Behälter werden über eine angetriebene Rollenbahn in den Arbeitsbereich der Zelle gebracht und in gefülltem Zustand auf eine Pufferstrecke ausgeschleust. Grosser Vorteil: Diese Tätigkeiten können auch hauptzeitparallel erfolgen.
Der Arbeitsablauf
Nach Start des Automatikbetriebes gelangen die Werkstücke auf dem Zuführband in den Arbeitsbereich des Roboters. Der MH12, der das gesamte Teilespektrum aufgrund der identischen Breite mit einem Greifer handhaben kann, greift dazu ein Teil ab und legt es in die Spannvorrichtung der Maschine ein. Sind nacheinander alle Nester der Spannvorrichtung bestückt, löst der Roboter die Spannung der Rohteile aus und gibt das Freigabesignal zur Bearbeitung an die Maschine. Die Maschine dreht daraufhin die beladene Seite ihres Schwenktisches in den Bearbeitungsbereich und gibt die Fertigteile in den Be- und Entladebereich des Roboters. Der Sechsachser holt daraufhin die Fertigteile ab und legt sie in den bereitstehenden Metallbehälter. Danach startet ein neuer Zyklus.
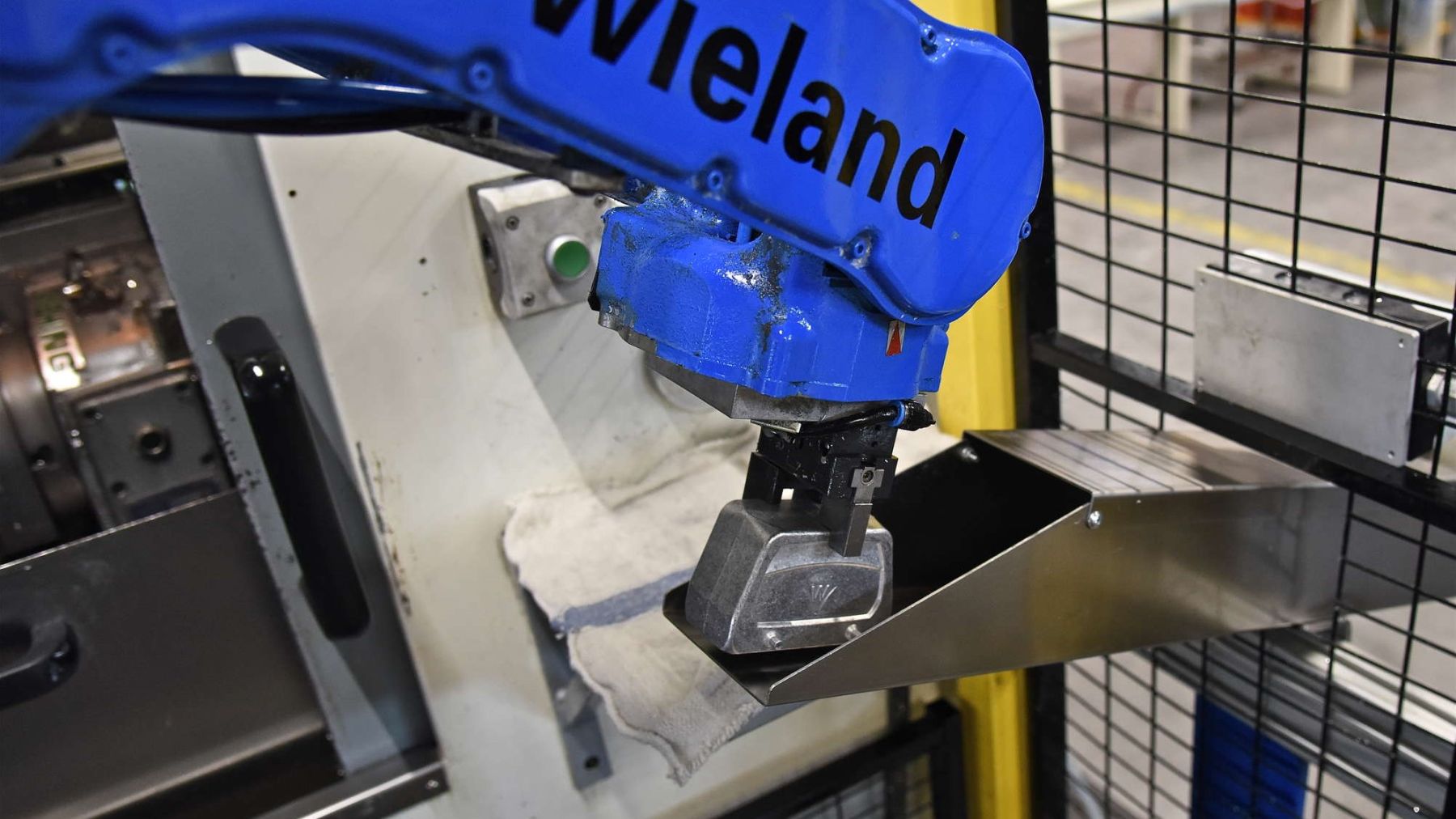
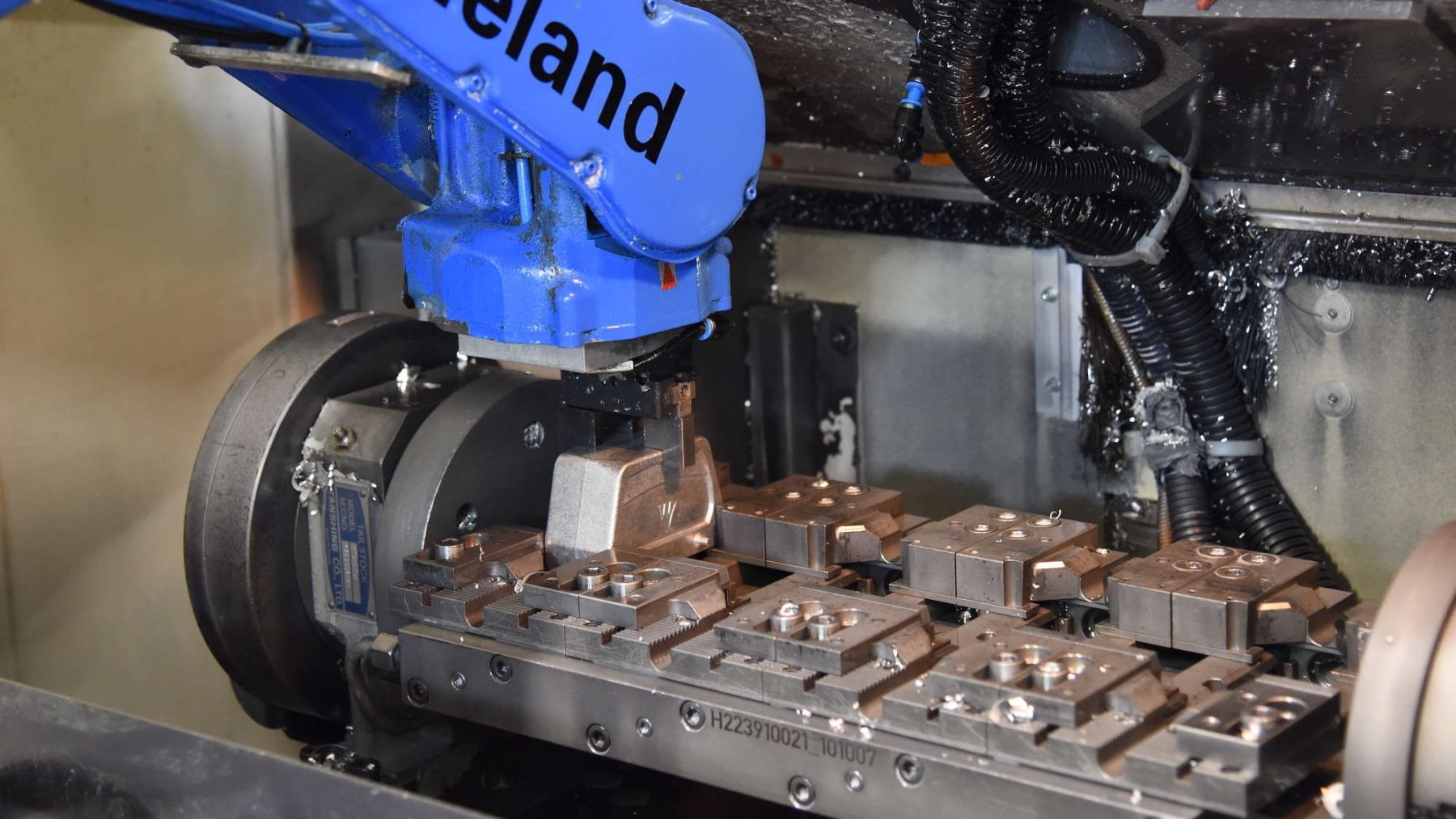
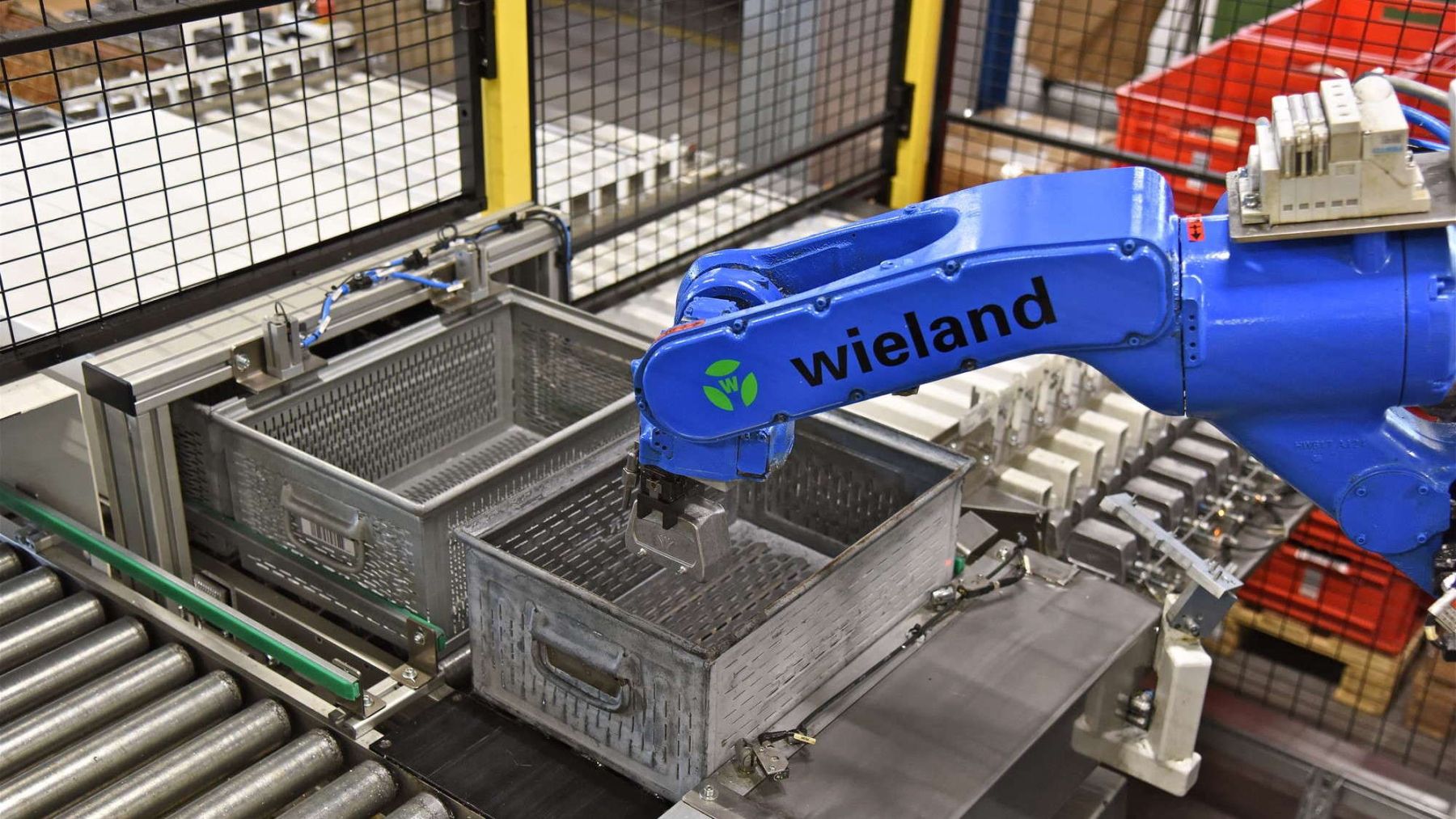
Keine Störungen oder längere Ausfälle
Jürgen Eisinger ist mit dieser Lösung überaus zufrieden: «Was uns besonders am Herzen liegt, ist die Prozesssicherheit von Zuführung und Robotik. Störungen oder gar längere Ausfälle kennen wir an dieser automatisierten Bearbeitungsmaschine nicht. Zudem setzt die Anlage Massstäbe hinsichtlich der Taktzeiten, die bei vier Teilen pro Minute liegt.» Und auch die erreichbare Autonomie, die je nach Teilevariante einige Stunden betragen kann, begeistert die Wieland-Mannschaft. Ausschlaggebend für einen möglichst langen autonomen Betrieb sind die maximal mögliche Bevorratung von Rohteilen durch das Zuführsystem sowie die Bereitstellung der maximalen Anzahl an leeren Metallbehältern im System.
Risiken für Mitarbeiter minimiert
Aber Autonomie und Produktivität allein sind für Jürgen Eisinger, Gruppenleiter Fertigungsplanung, nicht die einzigen Aspekte, die für die Automatisierungslösung sprechen. Für den Fertigungsstrategen stehen vielmehr die Mitarbeiter im Mittelpunkt: «Der permanente Kontakt mit den Steckergehäusen bei der manuellen Handhabung birgt gewisse Risiken. Die Teile sind mit Kühlschmierstoffen behaftet, die auf der Haut zu Reizungen führen können. Deshalb sehen wir es gerne, wenn unsere Mitarbeiter die angenehmen Tätigkeiten verrichten, während die Roboter die monotonen und schmutzigen Arbeiten übernehmen.»
Roboter MH12 mit eigener Ausblasvorrichtung
Dem Yaskawa Sechsachser kann die Beaufschlagung mit Kühlschmierstoffen oder Spänen im Gegensatz zu seinen menschlichen Kollegen nichts anhaben. Dank der Ausführung seiner Handachsen in Schutzart IP 67 zeigt sich der MH12 selbst vom groben Abblasen von Teilen und Spanneinrichtungen in der Maschine unbeeindruckt. Um diese Reinigungsschritte ausführen zu können, hat EGS den Roboter mit einer Ausblasvorrichtung ausgestattet.
Ausreichender Abstand von der Bearbeitungsmaschine
Für die Auswahl des Motoman MH12 gab es einen weiteren triftigen Grund, wie Röhrig betont: «Wir haben die Maschine auch aufgrund ihrer hervorragenden Reichweite ausgewählt. Denn nur dadurch konnten wir den Roboter in ausreichendem Abstand von der Bearbeitungsmaschine positionieren, so dass diese bei Bedarf manuell zu bedienen ist. Diese Option wollte sich Wieland für die händische Bearbeitung etwaiger Kleinstserien offenhalten.»
Impressum
Textquelle: Yaskawa
Autor: Ralf Högel
Bildquelle: Ralf Högel
Publiziert von Technik und Wissen (ea)
Weitere Artikel
Veröffentlicht am: