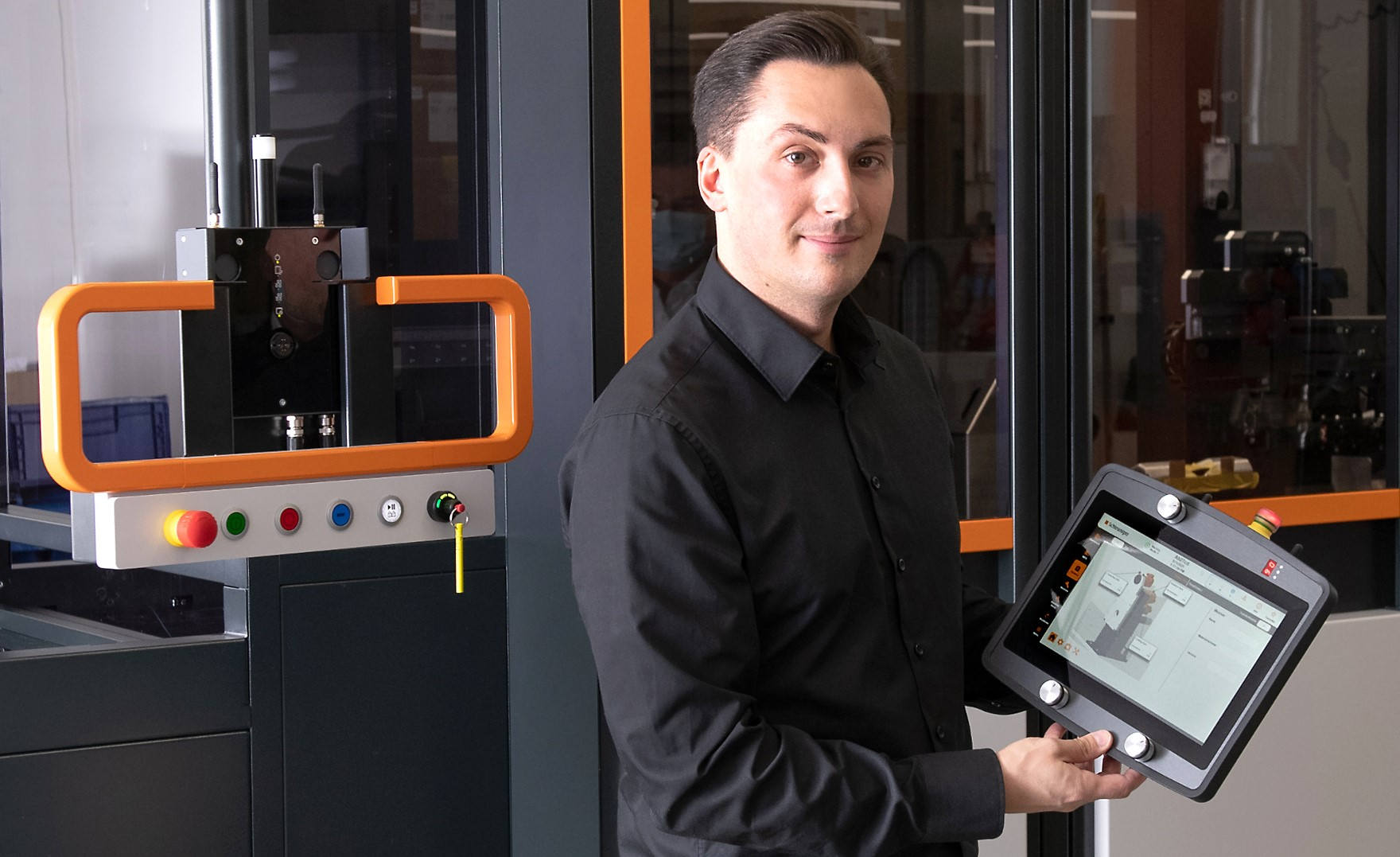
Die Schleuniger AG in Thun ist eines der ersten Schweizer Unternehmen, welches das kabellose Bedienpanel HGW 1033 von Sigmatek in einer sicherheitsrelevanten Anwendung einsetzt. Im Gespräch mit Michael Zbinden, Teamleiter Software-Entwicklung.
Markus Back (Autor) und Susanne Seiler (Fotos)
Die Expertise von Schleuniger ist die innovative und wirtschaftliche Verarbeitung von Kabeln. Ohne die genauen Hintergründe zu kennen, drängt sich die Frage auf, wieso Sie eine Applikation mit einem kabellosen Bedienpanel lösen?
In der Tat mag dies auf den ersten Blick überraschen. Für uns steht aber der Kunde im Zentrum, weshalb wir viel Wert auf die Bedienbarkeit und Ergonomie unserer Anlagen legen. Das mobile WLAN-Panel von Sigmatek bietet dem Bedienenden grössere Flexibilität und mehr Bewegungsfreiheit als ein kabelgebundenes Gerät. In Kombination mit den Encoder-Rädern und den eingebauten Sicherheitsfunktionen ist dies eine optimale Ergänzung für unsere Anlage.
Übrigens nehmen wir uns durch die Verwendung eines Wireless-Panels keine Arbeit, sondern profitieren indirekt sogar durch dessen Verwendung. Dieses ist nämlich über zwei Antennen mit der Basisstation verbunden, in deren Innerem hochwertige, mehrschichtige Coaxial-Kabel eingesetzt werden. Solche Kabel werden vorzugsweise auf Maschinen von Schleuniger verarbeitet. Da auch die Basisstation mit zwei Antennen ausgestattet ist, haben wir hier vier bearbeitete Kabel anstelle eines einfachen Verbindungskabels.
Neuentwickelte, automatisierte Plattform für Verarbeitung von Hochvolt-Kabel
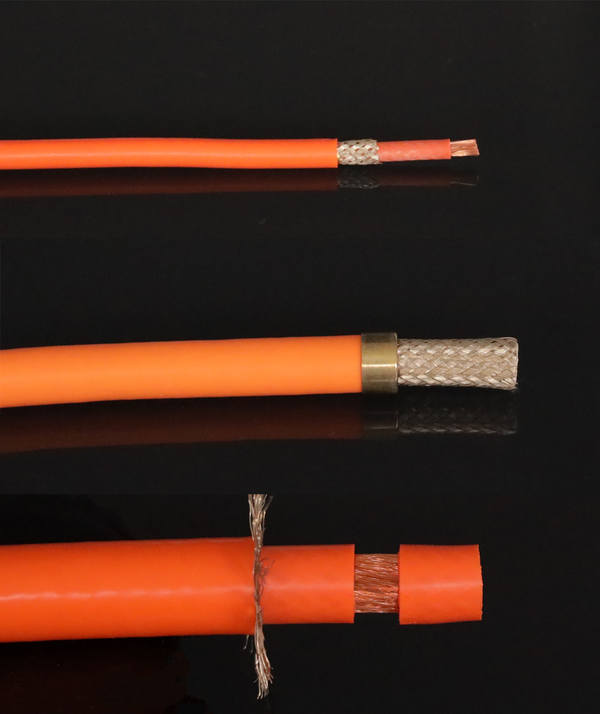
Damit ich verstehe, wieso Sie sich für diesen Lösungsweg entschieden haben, erzählen Sie mir zunächst von der Anwendung?
Die neuentwickelte, automatisierte Plattform von Schleuniger ist die Antwort auf die Frage, wie in Zukunft Hochvolt-Kabel für die Elektromobilität verarbeitet werden sollen. Die orangen Kabel werden der Anlage entweder zugeschnitten oder mit Komponenten bestückt zugeführt. Im Prozess der Maschine bearbeiten wir erst die Aussenisolation und dann die darunterliegenden Schichten. Anschliessend werden die produktspezifischen Steckerteile aufgebracht. Je nach Applikation können noch weitere Arbeitsschritte folgen. Schlussendlich wird das Produkt zur Weiterverarbeitung aus der Anlage geführt.
Der modulare Aufbau der Maschine erlaubt es dem Anwender, die Maschine auf aktuelle Aufgabenstellungen abgestimmt zu bestellen und für kommende Projekte situativ zu erweitern oder nachzurüsten. Um zukünftigen Anforderungen der Branche gerecht zu werden, haben wir während dem Projekt in enger Zusammenarbeit mit den Kunden erarbeitet, wie die Anlage in die bestehenden Arbeitsabläufe integriert werden soll. Dabei zeigte sich schnell, dass zum fest verbauten Hauptbediengerät ein weiteres, mobiles Bediengerät erforderlich ist. Dieses kann der Bedienende jederzeit bei sich haben, um während der Produktion aktuelle Daten einzusehen oder um bei Werkzeugwechseln die notwenigen Eingaben jederzeit am entsprechenden Ort tätigen zu können.
Was ist an dieser Lösung neu beziehungsweise speziell?
Dieses Gerät kombiniert kabellos ein hochaufgelöstes Touch-Display mit diversen Sicherheitsbedienelementen sowie drei Encoder-Rädern und Taster. Meines Wissens nach ist dies heute das einzige Gerät auf dem Markt, welches diese Funktionen sicher in einem industrietauglichen Gehäuse vereint.
Herausforderung bei der Integration
Mit welchen Herausforderungen wurden Sie bei der Integration konfrontiert?
Das Konzept von Sigmatek sieht vor, dass das User-Interface direkt auf dem Panel läuft, also in der Sigmatek-Umgebung programmiert wird. Unseres arbeitet jedoch mit einer Windows-basierten Umgebung, die auf diesem Panel nicht lauffähig ist, da dieses Linux-basiert ist. Für unsere Anwendung haben wir daher den Hauptrechner per VNC-Anbindung mit dem Mobile Panel verbunden und können das User-Interface so nun auf beiden Geräten vollumfänglich bedienen.
Weiter stellte sich die Frage, wie die Encoder und Safety-Bedienelemente auf die Steuerung übertragen werden? Dank des integrierten OPC-UA-Servers haben wir hier eine unkomplizierte, auf einem etablierten Standard aufbauende Lösung gefunden.
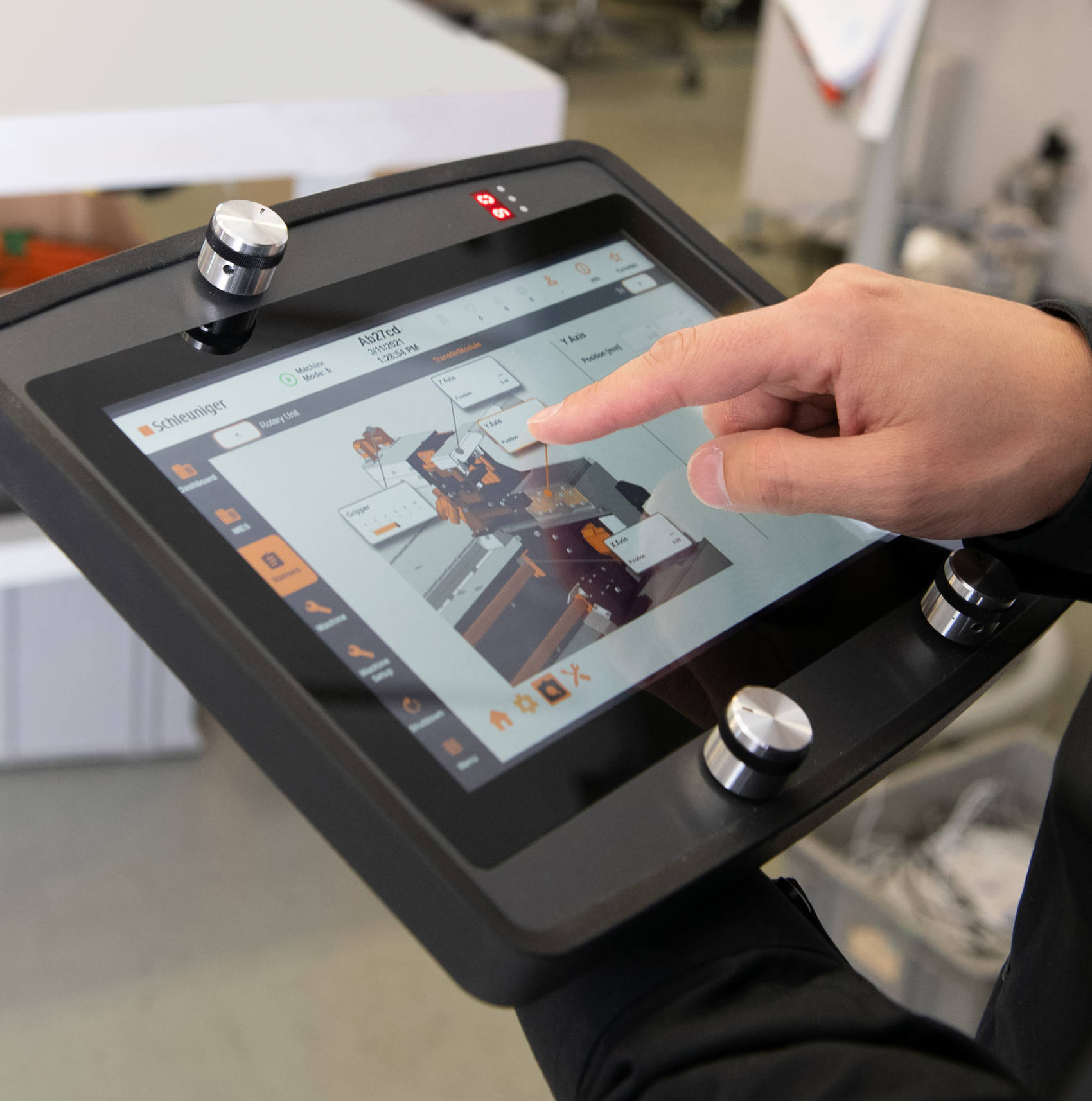
Stolperfalle umgehen mit kabellosem Bedienpanel
Irgendwann wurden Sie im Entwicklungsprozess mit der Frage kabelloses oder kabelgebundenes Panel konfrontiert. Was sprach für die jeweiligen Lösungswege?
Kabelgebundene Lösungen sind bewährt, Sicherheitsbedenken werden kaum geäussert. Zudem haben diese keine Funkverbindung, welche in Frage gestellt werden kann.
Da die Anlage jedoch mehrere Meter lang ist, muss auch das Kabel für das Bedienpanel entsprechend lang sein. Dies kann zur Stolperfalle werden oder hängen bleiben und Schaden nehmen. Alternativ zum langen Kabel hätten wir an der Anlage mehrere Anschlusspunkte anbringen können, an denen das Kabel eingesteckt werden kann. Allerdings sind diese Anschlusspunkte kostspielig, in der Montage aufwendig und sie erlauben es nicht, das Panel während der Produktion umzustecken.
Etliche dieser Herausforderungen werden durch die kabellose Anbindung gelöst. Der Bediener kann sich jederzeit, in einem definierten Radius frei bewegen und die Sicherheitselemente sind jederzeit griffbereit und aktiv. Allerdings muss für diese Freiheit eine zusätzliche Steuerung verbaut werden.
Und was war am Ende das ausschlaggebende Argument, sich für den kabellosen Weg zu entscheiden?
Wir sind ein innovatives Unternehmen in der Kabelindustrie und sehen uns als Technologieführer. Wenn wir den Anwendern durch neue Technologien erweiterte Möglichkeiten, mehr Bedienkomfort oder höhere Produktivität zugänglich machen können, ihnen also ganz allgemein einen Mehrwert generieren, versuchen wir diese Technologie bestmöglich einzusetzen. Das ist auch hier der Fall, weshalb uns die Entscheidung leichtgefallen ist.
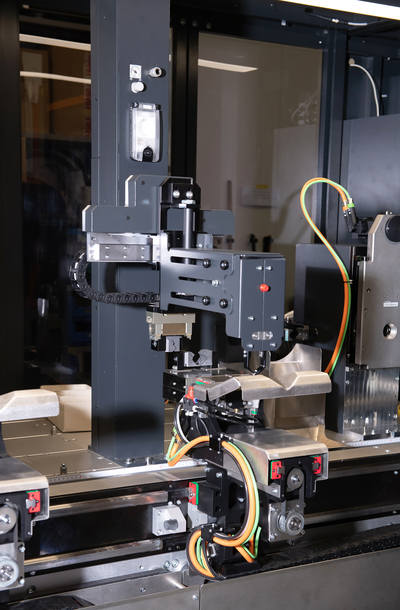
Übertragungssicherheit der Signale
Wie hat man mögliche Bedenken hinsichtlich der Übertragungssicherheit der Signale beseitigt?
Bereits eine herkömmliche Internetverbindung über WLAN weist diverse Mechanismen auf, welche für eine sichere Datenübertragung sorgen. So werden beispielsweise Datenverluste erkannt und automatisch behoben. Da in den meisten Fällen aber keine sicherheitsrelevanten Daten übertragen werden, wird bei einem allfälligen Daten- oder Verbindungsverlust einfach ein erneuter Übertragungsversuch unternommen, was sich teilweise in längeren Ladezeiten niederschlägt.
Dies ist bei sicherheitsrelevanten Komponenten wie hier nicht möglich. Im Falle einer Störung muss das Gerät jederzeit und sofort reagieren und einen sicheren Zustand auslösen und einnehmen. Das HGW 1033-32 stellt daher zunächst eine exklusive Punkt-zu-Punkt-Verbindung zwischen der Basisstation und dem Bediengerät her, wobei die Endgeräte vorgegeben sind. Da dies allein aber nicht für eine sichere Datenübertragung ausreicht, wird die Verbindung mit Hilfe des Black Channel Prinzips sichergestellt und damit Funktionen bis SIL 3 und PL e garantiert.
Strahlenbelastung minimieren mit kleinster Sendeleistung
Wie gehen Sie mit dem Umstand um, dass sich der Bediener im Bereich eines hochfrequenten Funksignals bewegt?
Auch diese Bedenken wurden diskutiert. Im modernen industriellen und privaten Umfeld werden bereits etliche Geräte mit kabellosen Verbindungen eingesetzt, wie beispielsweise Telefone, Laptops, Barcodescanner oder Messgeräte. Keines dieser Geräte wird jedoch so lange und eng am Körper getragen, wie ein Handy. Dies trifft auch auf das Mobile Panel zu, welches hauptsächlich in der Aufnahme eingehängt, und nicht am Körper getragen wird. Zudem wir die Sendeleistung auf die kleinste Stufe eingestellt. Dadurch wird die Strahlenbelastung minimiert und der Wirkradius bewusst eingeschränkt.
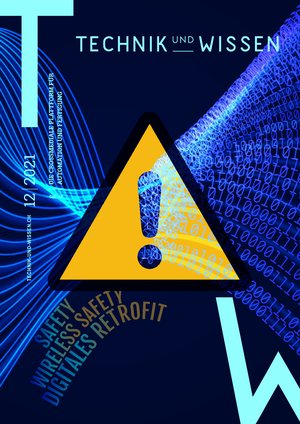
Weiterführender Artikel im Printmagazin
Lesen Sie die Geschichte zum Einsatz des Bedienpanels in der Printausgabe #012 und lernen Sie in weiteren Schwerpunktartikeln weitere Aspekte kennen zum Thema «Safety/Wireless Safety». Dazu gibt es exklusive Fachberichte und Interviews zum Thema Digitales Retrofit.
Noch kein Abo? Kein Problem, hier gibt es eines: Abo Printmagazin
Impressum
Autor: Markus Back, Chefredaktor Print
Fotos: Susanne Seiler
Eine Produktion von Technik und Wissen
Weitere Artikel
Veröffentlicht am: