Swiss Smart Factory: Mit herstellerunabhängiger Automatisierung zur smarten Fabrik
In der Swiss Smart Factory werden die Versprechen von Industrie 4.0 Realität. Ein wichtiges Thema: ein softwarezentrierter Automatisierungsansatz nach der Norm IEC 61499.
In der Swiss Smart Factory werden die Versprechen von Industrie 4.0 Realität. Ein wichtiges Thema: ein softwarezentrierter Automatisierungsansatz nach der Norm IEC 61499.
Mit Innovationskraft und Präzision kennt man sich im Zentrum der Schweizer Uhrenindustrie in Biel/Bienne bestens aus. Das wird auch im dort beheimateten Switzerland Innovation Park (SIPBB) unter Beweis gestellt wird. Denn dort ist eine wichtige Test- und Demonstrationsplattform für Themen rund um Industrie 4.0 zuhause: die Swiss Smart Factory. Hochmoderne Technologien werden an diesem Ort auf ihre Praxistauglichkeit hin erprobt. Eines der Highlights: eine neuartige Automatisierungsphilosophie. Statt mit proprietären Systemen wird in der Swiss Smart Factory heute schon herstellerunabhängig automatisiert.
«Wir helfen, die 4. Industrielle Revolution zu ermöglichen»
In der Swiss Smart Factory steht eine aus verschiedenen Anlagenmodulen zusammengesetzte Produktionslinie, die mit ihrer durchgängigen Vernetzung eindrücklich demonstriert, wie Industrie 4.0 über den gesamten Anlagenlebenszyklus hinweg funktionieren kann.
Ein wichtiges Anliegen, denn die mit Industrie 4.0 in Verbindung gebrachten und vielfach propagierten Vorteile stellen sich in der Realität bis heute häufig nicht ein. Flexible Produktionen, wandelbare Fabriken, kundenzentrierte Lösungen oder die umfassende, mehrwertbringende Nutzung von Daten – von diesen Vorteilen profitieren in der Praxis nur die wenigsten Industrieunternehmen.
Eine von der Universität St. Gallen durchgeführte Umfrage ergab, dass zwar 72 Prozent der befragten Unternehmen mindestens eine Industrie 4.0-Technologie implementiert haben, dies jedoch mehrheitlich auf ERP-Systeme und Cloud Computing beschränkt ist. Dagegen finden Technologien wie Augmented Reality oder 5G kaum Anwendung.
Artikel lesen: Herstellerunabhängiges und softwarezentriertes Automatisieren: Was es bringt und wie es gelingt
Auch deshalb ist man in der Swiss Smart Factory an der Umsetzung einer smarten Produktion, also der durchgängigen Vernetzung von Anlagen, Maschinen und Prozessschritten im Sinne des Internet-of-Things (IoT) interessiert. Ein zentraler Vorgang ist dabei Automatisierung.
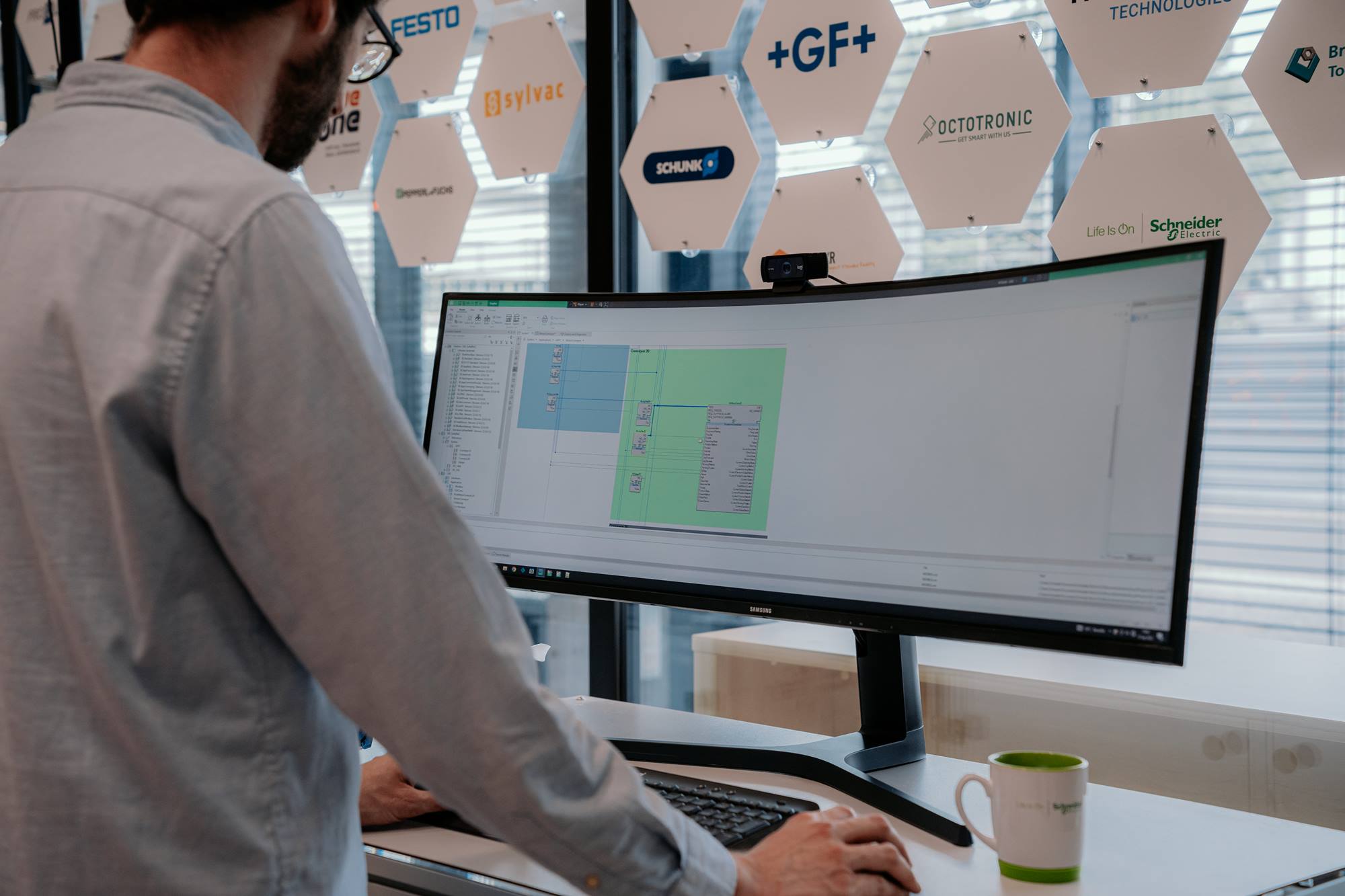
Dem beschriebenen Anspruch an Industrie 4.0 steht die gängige Herangehensweise an Automatisierung jedoch diametral gegenüber. Denn von Durchgängigkeit oder Interoperabilität kann angesichts von proprietären Steuerungssystemen keine Rede sein. Insbesondere wenn es um Themen wie Integration oder Migration geht, ist die proprietäre Logik in der Praxis oft ein Hemmschuh.
Doch es geht auch anders.
Wie in der Swiss Smart Factory zu sehen, ist es längst möglich, Automatisierung auch herstellerunabhängig zu denken und zu praktizieren. Gerade wenn es um mehr Modularität oder Flexibilität, und damit einen bedarfsgerechten Einsatz von Ressourcen geht, zahlt sich dieser Ansatz gewinnbringend aus. Ausserdem harmoniert er ideal mit der alles vernetzenden Grundidee des IIoT. Für Industrie 4.0 ist das eine elementare Voraussetzung.
Probleme proprietärer Systeme
Für die durch die SPS-Steuerung geprägte Automatisierungswelt der vergangenen Jahrzehnte sind proprietäre Steuerungssysteme ein kennzeichnendes Element. Hardware und Software sind im Fall einer typischen Steuerung herstellerspezifisch aneinander gekoppelt. Heisst: Für jede SPS-Steuerung jedes Herstellers und jeder Generation existiert eine jeweils spezifische Entwicklungsumgebung.
Muss also eine SPS-Steuerung gegen ein neueres Modell ausgetauscht werden, lässt sich der existierende Code nicht in die neue Steuerung übertragen, sondern muss in einer neuen Entwicklungsumgebung erneut programmiert werden. In grösseren Anlagen, in denen unterschiedliche Steuerungen verschiedener Hersteller zusammenarbeiten müssen, ist es zudem notwendig, die Querkommunikation zwischen diesen Steuerungen aufwendig zu konfigurieren. Von Interoperabilität keine Spur. Im Fall von Anlagenerweiterungen führt dies oftmals dazu, dass Betreiber auch weiterhin bei dem System bleiben müssen, für das sie sich vor Jahren oder Jahrzehnten entschieden haben.
Eine wirklich freie, herstellerunabhängige Auswahl von Komponenten, rein an der Funktionalität oder der Liefersituation orientiert, ist meistens nicht möglich. Logisch also, dass das Potenzial der Automatisierungstechnik in vielen Bereichen – insbesondere was die Flexibilität oder Resilienz von Anlagen angeht – häufig gehemmt bleibt. Innerhalb der Lösungswelt eines Herstellers ist zwar meist vieles möglich, im Fall von herstellerheterogenen Maschinenlandschaften – und das ist die Realität in den meisten Fabrikhallen – ist die Umsetzung von echten Industrie-4.0-Lösungen aufgrund der Beschränkungen durch proprietäre Systeme jedoch meist nur mit hohen Kosten realisierbar.
Probleme proprietärer Systeme
Für die durch die SPS-Steuerung geprägte Automatisierungswelt der vergangenen Jahrzehnte sind proprietäre Steuerungssysteme ein kennzeichnendes Element. Hardware und Software sind im Fall einer typischen Steuerung herstellerspezifisch aneinander gekoppelt. Heisst: Für jede SPS-Steuerung jedes Herstellers und jeder Generation existiert eine jeweils spezifische Entwicklungsumgebung.
Muss also eine SPS-Steuerung gegen ein neueres Modell ausgetauscht werden, lässt sich der existierende Code nicht in die neue Steuerung übertragen, sondern muss in einer neuen Entwicklungsumgebung erneut programmiert werden. In grösseren Anlagen, in denen unterschiedliche Steuerungen verschiedener Hersteller zusammenarbeiten müssen, ist es zudem notwendig, die Querkommunikation zwischen diesen Steuerungen aufwendig zu konfigurieren. Von Interoperabilität keine Spur. Im Fall von Anlagenerweiterungen führt dies oftmals dazu, dass Betreiber auch weiterhin bei dem System bleiben müssen, für das sie sich vor Jahren oder Jahrzehnten entschieden haben.
Eine wirklich freie, herstellerunabhängige Auswahl von Komponenten, rein an der Funktionalität oder der Liefersituation orientiert, ist meistens nicht möglich. Logisch also, dass das Potenzial der Automatisierungstechnik in vielen Bereichen – insbesondere was die Flexibilität oder Resilienz von Anlagen angeht – häufig gehemmt bleibt. Innerhalb der Lösungswelt eines Herstellers ist zwar meist vieles möglich, im Fall von herstellerheterogenen Maschinenlandschaften – und das ist die Realität in den meisten Fabrikhallen – ist die Umsetzung von echten Industrie-4.0-Lösungen aufgrund der Beschränkungen durch proprietäre Systeme jedoch meist nur mit hohen Kosten realisierbar.
Gesucht: der gemeinsame Nenner
Dass ein Zusammenspiel von Hardware und Software auch ohne proprietäre Systemstrukturen möglich ist, macht der Blick in die IT-Welt deutlich. Denn hier ist es seit Jahrzehnten gang und gäbe, dass Softwareapplikationen nicht nur für die Hardware eines bestimmten Herstellers programmiert werden, sondern dass Software in der Regel unabhängig vom Anbieter einer Hardware ausführbar ist.
Grund dafür ist die Existenz von Betriebssystemen, die sozusagen einen gemeinsamen Nenner zwischen Laptops oder Smartphones verschiedener Hersteller bilden. Ein Prinzip, dass auch auf die Automatisierung anwendbar ist und damit gerade für eine jüngere Generationen an Automatisierern eine grosse Attraktivität besitzt.
Die unabhängige Non-Profit-Organisation UniversalAutomation.Org stellt etwa bereits seit Ende 2021 eine sogenannte Runtime Execution Engine zur Verfügung, mit der eine an IT-Logiken orientierte Herangehensweise an die Automatisierung möglich wird. Bei dieser Runtime Execution Engine handelt es sich zwar nicht um ein Betriebssystem, aber um eine Art Schnittstelle, die zwischen einer aus dem Engineering-Tool kompilierten Control Runtime und dem Betriebssystem eines Device übersetzt.
Egal welches Device, egal welche Buildtime, die Runtime der Org übersetzt. Dadurch werden Hardware (Device) und Software (Buildtime) grundlegend voneinander entkoppelt. Im Anlagenteil der Swiss Smart Factory, der vom französischen Tech-Konzern Schneider Electric – einem Gründungsmitglied der UniversalAutomation.Org – automatisiert wurde, wird die Praxistauglichkeit dieses Ansatzes schon heute unter Beweis gestellt.
Lebenszyklen von Hardware und Software entkoppeln
Im Anlagenteil von Schneider Electric kommen unter anderem Förderbänder und Delta-Roboter zum Einsatz. Automatisiert wurde hier mithilfe des auf herstellerunabhängige und softwarezentrierte Automatisierung ausgelegten Engineering-Tools EcoStruxure Automation Expert.
Orientiert an der Logik einer nicht mehr von proprietären Systemen beschränkten Automatisierung, ist es damit möglich, Anwendung zunächst rein softwareseitig zu modellieren. Die Funktionsbausteine – also Softwareobjekte, in denen etwa die Funktionalität eines Motors oder einer ganzen Anwendung gekapselt ist – werden unabhängig von jeglicher Hardware erstellt.
Entsprechend dieser Herangehensweise entstehen tatsächlich unabhängige und damit immer wiederverwendbare Softwareobjekte. Die Auswahl der Hardware erfolgt später und ist nicht mehr von Herstellervorgaben abhängig. Und das hat Folgen.
Die Lebenszyklen von Hardware und Software sind damit voneinander entkoppelt. Wird auf eine neue Generation an Hardware migriert, muss nur die Hardware ausgetauscht werden – die bestehende Software wird einfach auf die neuen Hardwarekomponenten aufgespielt.
Ein enormer Pluspunkt, der sich natürlich auch beim Austausch von fehlerhaften Komponenten bezahlt macht. Denn sollte etwa unvermutet eine Komponente, wie zum Beispiel eine SPS-Steuerung, ausfallen, kann der Code auch auf jedes andere Bauteil mit CPU aufgespielt und von diesem berechnet werden.
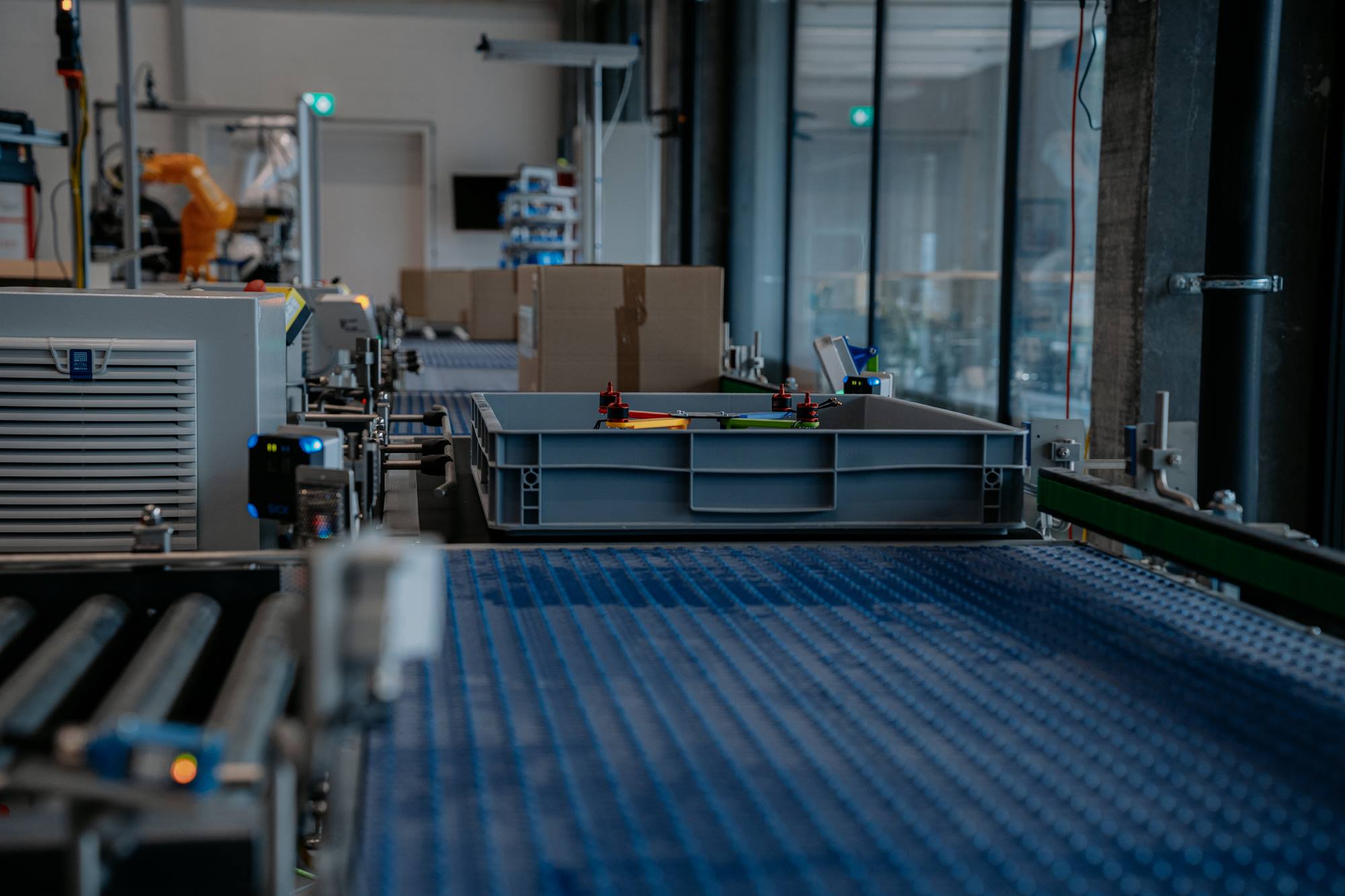
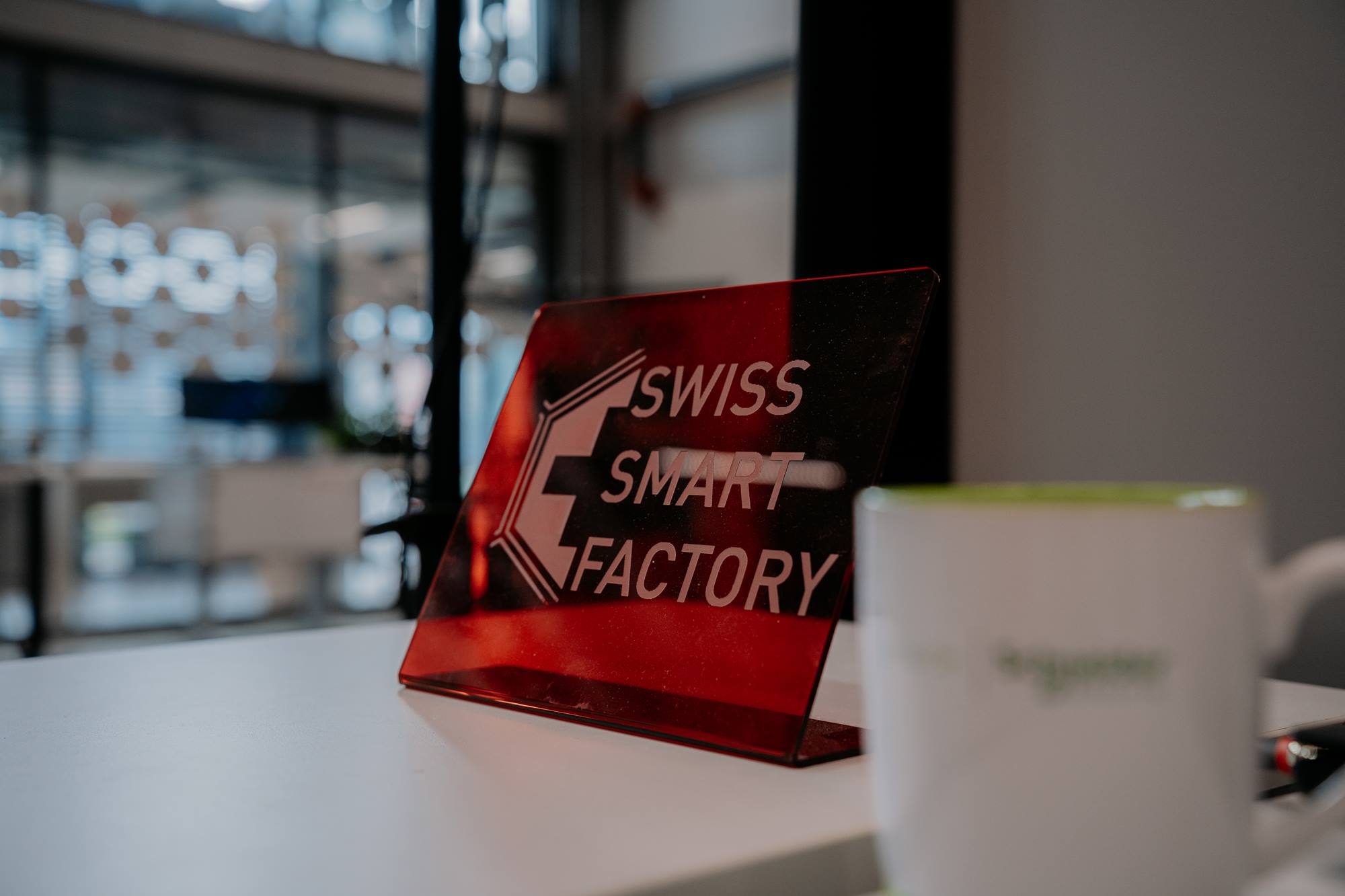
Damit steht diese Herangehensweise an die Automatisierung, mit ihrer herstellerneutralen Runtime Execution Engine, ganz im Einklang mit den in der IEC Norm 61499 beschriebenen Grundlagen für eine dezentrale Automatisierungsweise. Gerade für flexiblere oder sogar modulare Anlagen im Sinne der Industrie 4.0 ist diese Herangehensweise sehr wertvoll.
Denn statt einer starren Automatisierungspyramide folgt der Systembau nach IEC 61499 dem Prinzip der Schwarmintelligenz – das gesamte System ist damit nicht mehr hierarchisch und abhängig von einer SPS-Steuerung. Das ermöglicht einen viel flexibleren und effizienteren Einsatz von Ressourcen. Etwa, dass für die Auswahl der passenden Hardwarekomponenten nicht mehr der Hersteller, sondern allein die Aspekte Funktionalität und Lieferbarkeit entscheidend sind. Gerade für den Maschinen- und Anlagenbau werden damit auch viele mühsame Parallelentwicklungen obsolet.
Weltweit konnte die Praxistauglichkeit bereits in einigen Use Cases im industriellen Umfeld unter Beweis gestellt werden. Auch in der Swiss Smart Factory hat man eine Plattform geschaffen, um Funktionsweise und Vorteile einer herstellerunabhängigen Automatisierung zu präsentieren. Und dass insbesondere im Hinblick auf das Potenzial, das dieser Automatisierungsansatz im Bezug auf die Umsetzung von Industrie 4.0 entfaltet.
Mehr zur herstellerunabhängigen Automatisierung mit EcoStruxure Automation Expert erfahren Sie im EAE eBook von Schneider Electric.
Weitere Artikel, die Sie interessieren könnten
Impressum
Textquelle: Schneider Electric
Bildquelle: Schneider Electric
Redaktionelle Bearbeitung: Technik und Wissen
Informationen
Schneider Electric
www.se.com
Weitere Artikel
Veröffentlicht am: