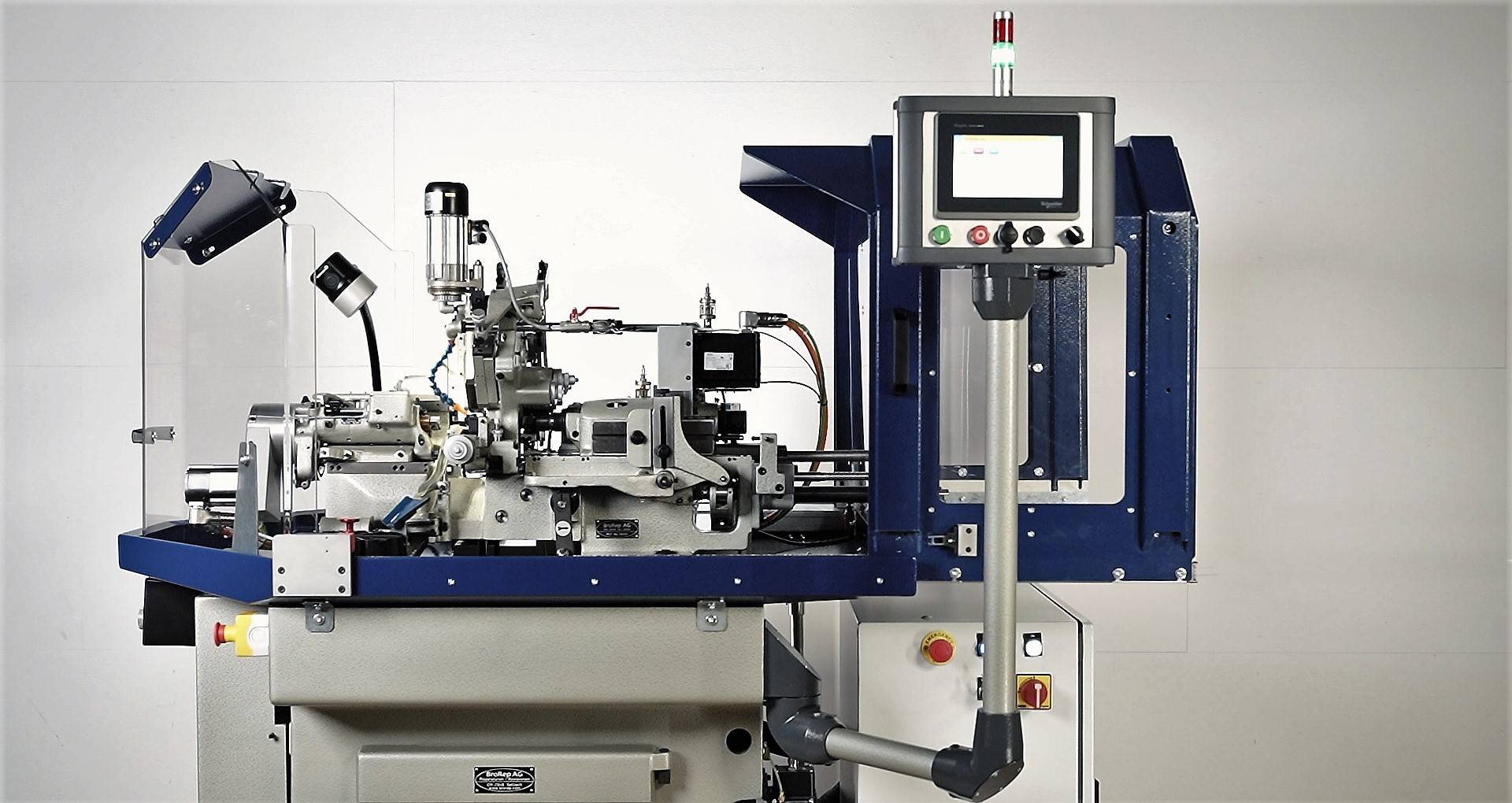
Vier Firmen sagen, was ihre Expertise auf dem Gebiet des digitalen Retrofits ist, über was sie einen Vortrag halten würden, stellen Produkte vor und geben Tipps. Die vier Firmen sind: Alfred Imhof, Brorep, Pilz und Siemens.
Ein Beitrag von Technik und Wissen
Autor: Eugen Albisser
Die Antwortgeber für die einzelnen Firmen sind:
Ihre Firma beschäftigt sich unter anderem mit dem digitalem Retrofit. Was ist Ihre Expertise?
Alfred Imhof: Die SEW als Hersteller von Getriebemotoren und wir als Lieferant dieser Produkte kennen die Anforderungen rund um die Antriebstechnik bestens. In der Schweiz haben wir zudem ein Team, das sich mit diesem Thema auseinandersetzt.
Meist ist es leider ein sich ankündigender Schaden, der durch unsere Experten analysiert wird. Für diese Analyse können wir aus einem Pool von Dienstleistungen schöpfen. Gerade bei diesen Fällen bietet sich ein digitaler Retrofit an, um zukünftig unerwartete Ausfälle zu vermeiden. Wir bieten unter dem Begriff «Drive Radar» verschiedenste Möglichkeiten an.
Brorep: Mit über 30 Jahren Erfahrung sind wir der internationale Spezialist für Reparaturen, Umbauten sowie dem Retrofit von Maschinen wie Kurvenmaschinen, Mehrspindel-Drehautomaten, CNC-gesteuerte Maschinen, Werkzeugmaschinen und vielem mehr. Zusätzlich bieten wir unseren Kunden Sicherheitsoptimierungen an.
Pilz: Wir haben mit unserer Abteilung «System Integration» Experten, die unter anderem Retrofit von Anlagen als Dienstleistung anbieten. Unser Fokus ist es, mit fundierten Kenntnissen der Maschinensicherheit die Systemanforderung mit minimalen Kosten und Ausfallzeiten umzusetzen. Dieses Angebot wird durch «Industrie 4.0»-Produkte abgerundet. So können Kunden zum Beispiel nach getaner Arbeit mit einer Sicherheitssteuerung PSS4000, einem RevPi Core 3 und einer SecurityBridge von überall sicher auf die Anlage zugreifen.
Siemens: Unsere Expertise liegt in der Kombination der langjährigen Erfahrung bei klassischen Retrofits, den Möglichkeiten der Digitalisierung und dem Zusammenspiel mit unseren Softwarelösungen.
Welches Ihrer Produkte oder Dienstleistungen aus dem Bereich «digitaler Retrofit» würden Sie an einem Vortrag vorstellen?
Alfred Imhof: Ich würde als Beispiel den digitalen Retrofit eines Grossgetriebes nehmen. Im Rahmen einer geplanten Revision des Getriebes können wir den Antrieb so weit ausstatten, dass zukünftig die Anforderungen an Predictive Maintenance erfüllt werden.
Der Antrieb würde mit einer entsprechenden Sensorik erweitert werden. Dies kann ein Schwingungssensor, ein Öl-Sensor, eine Temperaturerfassung, eine einfache Ölstandsüberwachung oder die Kombination dieser Sensoren sein. Die Daten werden in einer Edge Processing Unit erfasst und gesammelt. Natürlich können aus einem Berg von Daten teilweise nur sehr rudimentäre Aussagen gemacht werden. Erst das Zusammenspiel der einzelnen Daten und die daraus erfolgte Analyse führen zum gewünschten Ergebnis einer genauen Zustandsbetrachtung und Vorhersage. Hier verbirgt sich unser gesammeltes Know-how über Getriebemotoren. Die Ergebnisse können dann in einer Visualisierung DriveRadar IoT Suite entsprechend dargestellt werden.
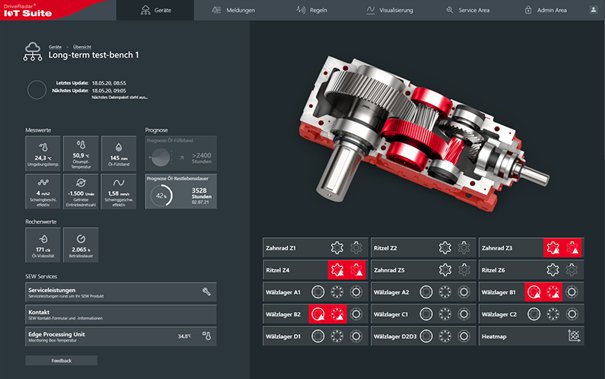
Brorep: Ich würde über unsere Steuerung 2.0 «MODCTRL Cam, MODCTRL Speed, MODCTRL Stop» reden, die wir zu einem Retrofitting empfehlen. Was nämlich bisher unter den Namen VarioCam, VarioSpeed und VarioStop bekannt war, hat einen neuen Anstrich erhalten. Mit «MODCTRL» erreichen wir eine Produktionsoptimierung und können modular erweitern, und zwar bis zu 5 Achsen. Ein weiteres Plus ist der gesteckte Elektroschrank, der optionale Erweiterungen und mögliche Wartungen vereinfacht.
Pilz: Wir haben das RevolutionPi RevPi Core 3 von der Firma Kunbus in unserem Sortiment, das deutlich heraussticht. Ausgerüstet mit dem Raspbian Betriebssystem haben sie einen Mini-Computer in der Anlage, der ein breites Spektrum von Möglichkeiten anbietet. So können Anwender zum Beispiel dank des vorinstallierten Node-RED Konfigurators spielend leicht die gesammelten Daten verarbeiten und dort hinleiten, wo sie gebraucht werden.
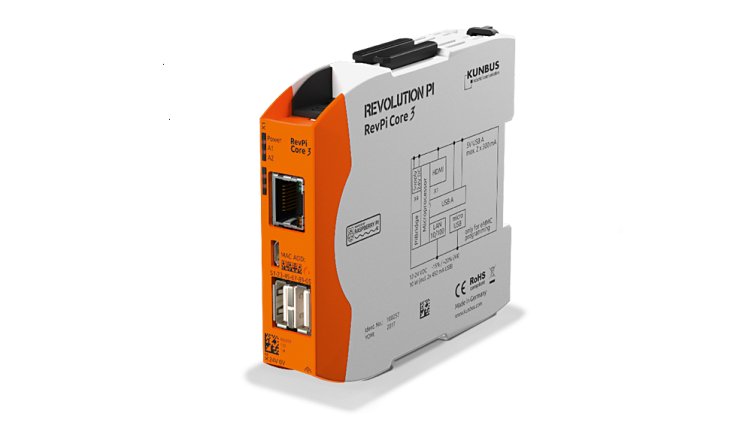
Siemens: Ich würde über den digitalen Zwilling, also ein Abbild der Produktionsanlage oder sogar der ganzen Fabrik, referieren. Durch unsere digitalen Zwillinge können wir mittels Simulation unter anderem Inbetriebnahmezeiten verkürzen, die Produktivität einer Anlage steigern sowie die Qualität erhöhen.
Können Sie noch etwas mehr zur vorgestellten Lösung sagen?
Alfred Imhof: Die automatisierte Transformation von Daten in Erkenntnis, also das digitale Beobachten und das daraus abgeleitete Wissen, sind der gewünschte Lerneffekt, welcher das Prinzip von Condition Monitoring begründet. Mit der DriveRadar IoT Suite erhält der Nutzer eine umfassende Systemlösung, welche die permanente Erfassung des Getriebezustands durch Messung, Analyse und Bewertung ausgewählter physikalischer Grössen ermöglicht. Hierbei spielen natürlich unsere Erfahrungswerte eine tragende Rolle.
Die im System hinterlegten Grenzwerte für die Ampelschaltung werden automatisch aus der Getriebekonfiguration übernommen oder generieren sich durch das selbstlernende System innerhalb der ersten Messungen im Betrieb selbst. Bei der Überschreitung eines Grenzwerts wird der Kunde vom System per App informiert und erhält direkte Handlungsempfehlungen zur jeweiligen Problemlösung.
Bei über mehrere Standorte ausgedehnten Verwendung der DriveRadar IoT Suite kann sich der Nutzer zentral einen schnellen Überblick über den Istzustand verschaffen. Ist etwas mehr Detailinformation gefragt, kann zum Beispiel durch einfaches Navigieren der Ölstand eines einzelnen Getriebes inklusive Ölrestlebensdauer und Prognosen von kritischen Zuständen abgefragt werden. Natürlich können Analyseergebnisse auch als Kurve mit beliebig einstellbarem Zeitintervall angezeigt werden.
Haben Sie einen Tipp für das digitale Retrofit?
Alfred Imhof: Planen, planen, planen! Wir empfehlen generell vor Durchführung eines digitalen Retrofits in einer Anlage, sich ein genaues Bild der installierten Antriebe zu erstellen. Nicht jede Anlage oder Produktionsstätte ist gleich zu betrachten. Bei der Betrachtung der Anlage spielen eine Vielzahl von Faktoren eine Rolle: geplante Verfügbarkeit, Laufzeit der Antriebe, Schichtmodell, Umgebungsbedingungen, Prozesse, Knowhow und nicht zuletzt auch die Kosten. Die besten Ergebnisse eines digitalen Retrofits werden erzielt, wenn bereits in der Planungsphase alle relevanten Parteien involviert sind. Wie bieten hier mit unserer Expertise auch gerne unsere Hilfe an.
Pilz: Oftmals stösst man gerade bei älteren Anlagen an ein Verständigungsproblem der verschiedenen Steuerungen und Informationslieferanten. Dabei hilft es ungemein, wenn man ein universelles Übersetzungssystem hat, welches verschiedene Busprotokolle modular miteinander verbindet. Die Lösung dazu heisst «Modulare Gateaways» von Kunbus. Die Kunbus Gateways bestehen aus zwei Modulen. Ein Modul dient als Slave für das eine Netzwerk, das andere Modul ist ein Slave im anderen Netzwerk.
Siemens: Es ist wichtig, eine langfristige Strategie zu haben. Diese erarbeiten wir gemeinsam mit dem Kunden, um zu sehen, wo welcher Digitalisierungsgrad sinnvoll ist und welcher Mehrwert aus den Daten eines digitalen Retrofits gezogen werden kann. Üblicherweise beginnen wir mit einem «Maturity Assessment» für die digitale Reifegradbeurteilung.
Ganz wichtig dabei: Keine Digitalisierung ohne Security! Unternehmen sollten immer nach bestmöglichem Schutz für ihre Anlagen und Systeme streben, und zwar Anlagensicherheit, Netzwerksicherheit und Systemintegrität in einem mehrstufigen Sicherheitskonzept.
Ganz wichtig beim Digitalen Retrofit: Keine Digitalisierung ohne Security!
Was sind generell die Vorteile eines digitalen Retrofits?
Alfred Imhof: Eine bestehende Anlage kann durch ein digitales Retrofit transparenter gemacht werden. Wo früher viel Bauchgefühl und Erfahrung nötig waren, um eine Anlage verfügbar zu halten, übernimmt diese Aufgabe nun die Technik. Wartungstermine können zielgerichtet geplant werden und die Kosten werden bei gestiegener Verfügbarkeit gesenkt.
Brorep: Mit dem digitalen Retrofitting erreicht der Kunde längere Produktionszyklen und senkt seine Energiekosten um einen wesentlichen Teil.
Pilz: Kurz gesagt, ist es die schnelle Informationsbeschaffung, was die Fehlersuche bei Störungen deutlich verkürzt, oder aber durch genaue Produktionszahlen die zukünftige Planung vereinfacht.
Siemens: Zu den Vorteilen gehören die Erhöhung der Transparenz in der Produktion, die Reduktion von Stillstandzeiten und Ausfällen sowie die Steigerung der Qualität und OEE (Overall Equipment Efficiency). Als Beispiel nehme ich die Umsetzung des digitalen Zwillings bei Ruggli AG: Mit dem digitalen Zwilling konnte die Ruggli AG den Rundtakttisch einer neuen Anlage virtuell konstruieren und optimieren. Die Eins-zu-eins-Darstellung der Mechanik hat den Vorteil, dass die Funktionalitäten visuell überprüft werden können und die Gefahr von Kollisionen lässt sich durch die virtuellen Tests bannen: Werden zum Beispiel bei der Programmierung versehentlich die X- und die Y-Achsen einer Bewegung vertauscht, fällt das im digitalen Abbild sofort auf. An der realen Anlage hätte ein solcher Fehler verheerende Auswirkungen.
[Video] Brorep-Retrofitting und Weltneuheit MODCTRL
Wann lohnt sich ein digitales Retrofit?
Alfred Imhof: Es lohnt sich immer dann, wenn Kosten gesenkt und Verfügbarkeiten gesteigert werden müssen. Natürlich darf die Investition für ein digitales Retrofit nicht die Einsparungen der nächsten 10 Betriebsjahre «auffressen». Hier ist meist eine individuelle Vorgehensweise angebracht.
Brorep: Sobald eine Steigerung der Produktion gewünscht wird, sich die Sicherheitsanforderungen ändern und eine einfache Optimierung der Schutzmöglichkeiten gewünscht ist.
Siemens: Ein digitales Retrofit lohnt sich bei sämtlichen prozessrelevanten Maschinen. Prüfenswert ist auch, ob sich neben dem digitalen Retrofit direkt eine Erneuerung der Hardware anbietet, um so den Lebenszyklus der Maschine zu verlängern.
Welche Herausforderungen gibt es aber immer wieder?
Alfred Imhof: Eigentlich die grösste Herausforderung ist die Einbindung der digitalen Daten in eine bestehende IT-Struktur. Alles auf Maschinenebene – inklusive der Automatisierung – ist relativ einfach lösbar. Sobald aber Daten mit übergeordneten Systemen kommunizieren müssen, kann dies eine echte Herausforderung darstellen.
Brorep: In jedem Betrieb sind die Sicherheitsanforderungen anders. Unser geschultes Team hat mit seiner langjährigen Erfahrung die passende Lösung zu jeder Anforderung und bietet auch Spezialkonstruktionen an, sollten standardisierte Produkte nicht zureichend dienen.
Siemens: Eine grosse Herausforderung für eine erfolgreiche Umsetzung ist die Kombination der verschiedenen notwendigen Kompetenzen Software, Hardware und Digitalisierung. Ein wesentlicher Erfolgsfaktor ist hier auf jeden Fall der richtige Partner für eine langfristige Zusammenarbeit und eine klare Zielsetzung.
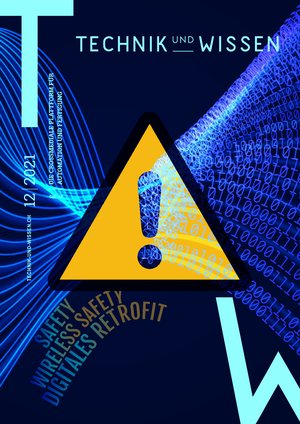
Printmagazin Technik und Wissen
Schwerpunkthema «Digitales Retrofit»
In der Printausgabe 012 von «Technik und Wissen» ist eines der beiden Schwerpunktthemen das «Digitale Retrofit». Das zweite Schwerpunktthema ist Safety und Wireless Safety.
Sie haben noch kein Abonnement? Hier gelangen Sie zum Abo des innovativsten und modernsten Schweizer Industriemagazins.
Die rechtlichen Aspekte
Wie sieht es mit den rechtlichen Aspekten aus, wenn man eine Maschine umbaut: Was muss man da beachten?
Alfred Imhof: Grundsätzlich muss bei einem Retrofit die rechtliche Seite gut betrachtet werden. In gewissen Fällen gilt ein Bestandschutz. Sollte aber zum Beispiel die Leistung der Anlage erhöht werden, muss diese nach den aktuellen Normen und Richtlinien betrachtet werden. Wer sich hier nicht sicher ist, sollte sich entsprechend beraten lassen. Sonst kann ein kleines Retrofit sehr schnell sehr teuer werden.
Siemens: Da muss man grundsätzlich die Aspekte eines klassischen Retrofits beachten, zusätzlich müssen hier die Gesichtspunkte Datenhaltung und Industrial Security (IEC 62443 and ISO 27001) angeschaut und Schutzmassnahmen integriert werden.
Können Sie ein Beispiel geben für ein digitales Retrofit?
Brorep: Ein langjähriger Kunde kam mit dem Anliegen zu uns, dass er mit der Leistung seiner neuen CNC-Maschine nicht die gewünschte Produktion erreichen konnte. Mit den zwei totalrevidierten Maschinen, die der Kunde auf derselben Produktionsfläche wie die CNC-Maschine stellen konnte, erreichte er eine Verdopplung der Produktivität und senkte zudem seine Energiekosten. Als er zudem auch noch eine Schutzhaube bestellt hat, wurde nicht nur die Sicherheit maximiert, sondern auch die Lärmemission reduziert. Und mit dem Teileseparateur-System ist der Kunde ebenfalls sehr zufrieden, da es ihm die Qualitätskontrolle vereinfacht und Zeit spart.
Siemens: Gerne nehme ich hier wieder Bezug auf unser Referenzprojekt von Ruggli: Der Einsatz des digitalen Zwillings verkürzte die Dauer der Programmierung um rund 20 Prozent. Somit ist das digitale Abbild auch interessant für künftige Aufträge, da die Funktionalitäten beliebig weiterentwickelt oder angepasst werden können. Bei der Inbetriebnahme der Anlage blieben dank des digitalen Zwillings unliebsame Überraschungen aus und sollte später im Betrieb beim Endkunden ein Problem auftauchen, gewährleistet Siemens via Fernwartung den Support.
Danke, dass Sie «Technik und Wissen» lesen!
Abonnieren Sie uns! Newsletter / Printmagazin
Und folgen Sie uns: Linkedin
Impressum
Autor: Eugen Albisser, Online-Chefredaktor
Bildquellen: Diverse
Eine Publikation von Technik und Wissen
Informationen
Alfred Imhof – imhof-sew.ch
BroRep AG – brorep.ch
Pilz – pilz.com
Siemens – siemens.ch
Weitere Artikel
Veröffentlicht am: