Guillaume Hopfner, Leiter Entwicklung und Konstruktion bei Braunform, bringt mehr als 20 Jahre Erfahrung im Formenbau mit. Dabei liegt sein Fokus primär auf der Technologie, Konstruktion, Inbetriebnahme sowie Standardisierung von Hochleistungsspritzgiesswerkzeugen. In den letzten zehn Jahren sind die Anforderungen an Mehrkomponenten-Werkzeuge hinsichtlich der Werkzeuggrösse in Bezug zur Kavitätendichte gestiegen. Die Braunform GmbH hat sich deshalb auf die Standardisierung der Werkzeugausführung ausgerichtet und die Fertigungsqualität stets nach der Werkzeugfunktion bestimmt. Die Spritzgiessformen der Braunform GmbH erreichen angesichts der effizienten Produktion mit bestmöglichem Output sowie der sicheren Wartung der Spritzgiesswerkzeuge eine klare Marktpositionierung. Das Unternehmen geht in Bezug auf Ausführung und Wahl der passenden Normalien nur wenige Kompromisse ein. Guillaume Hopfner ist es wichtig, Werkzeugkonzepte laufend weiterzuentwickeln und stets für neue Lösungen offen zu sein.
Agatalk – eine Multimediastory über Normalien
Die Podcastfolgen von Agathon als Story zum Lesen
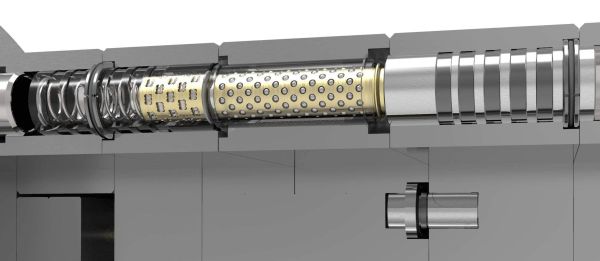
Agatalk – eine Multimediastory über Normalien
Die Podcastfolgen von Agathon als Story zum Lesen
Von Auswerferführungen über Mini Feinzentrierung bis Systemführungen: Mit Agatalk hat Agathon einen Podcast lanciert, in dem Fachleute vieles über Normalien erfahren. Das ist die Multimediastory zu diesem Podcast.
Inhaltsverzeichnis
«Führen, zentrieren schnell wechseln» – das Motto der Agathon Normalien steht für sich. Denn eine hohe Oberflächengüte, engste Toleranzen und eine lange Lebensdauer zeichnen die Normalien von Agathon aus. Zum Einsatz kommen sie im Maschinenbau, im Formenbau und als Stanzwerkzeuge. Unter anderem setzt die Braunform GmbH, ein renommierter Spritzgiesswerkzeugbauer aus Deutschland, auf die Normalien der Agathon «Made in Switzerland».
«Sehr genau, sehr präzise und eine hohe Qualität: Wir sind überzeugt von Agathon», sagt denn auch Guillaume Hopfner. Er ist Leiter der Entwicklung und Produktion bei der Braunform GmbH. Doch wie setzt die Braunform GmbH die Normalien der Agathon ein und warum setzt Braunform auf die Produkte der Agathon? Guillaume Hopfner spricht mit Stefan Nobs von der Agathon über diese Fragen.
♦ Folge 1 ♦
Mini Feinzentrierung – dynamisch
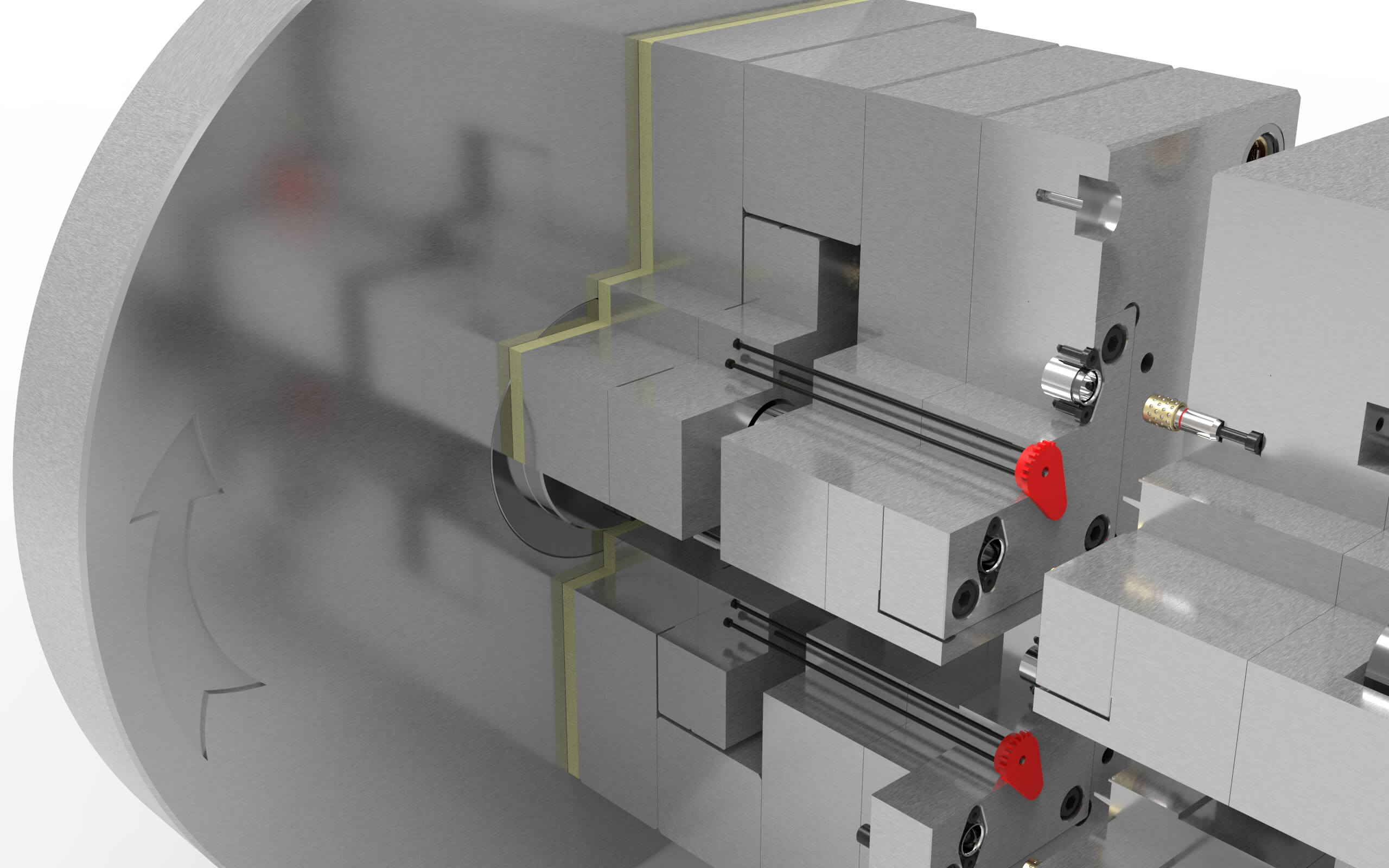
Was ist der ideale Zentrierweg? Wie erreicht der Kunde Braunform die Laufleistung von mehreren Millionen Zyklen? Und wie schätzt er die Mini Feinzentrierung im Vergleich zu herkömmlichen Zentrier- oder anderen Kavitätenzentrierungssystemen ein?
Mini Feinzentrierung dynamisch? Der Name allein sagt schon vieles: Es geht in erster Linie um kleinere Abmessungen, wobei die Mini Feinzentrierung hier in einem dynamischen Anwendungsfall eingesetzt wird. Wobei dynamisch auch heisst, eine spielfreie Formzentrierung bei jeder Werkzeugschliessung zu haben. Bei dieser Normreihe gibt es zwei verschiedene Abmessungen. Das heisst, zwei verschiedene Durchmesser und noch zwei Varianten, wie man sie einsetzen kann: mit Buchse – und daher als ganze Einheit – oder als neues Feature ohne Buchse.
Warum aber ohne Buchse? Hier spielen die Platzverhältnisse eine Rolle. Denn vielfach hat man im Formenbau wenig Platz zur Verfügung, um eine Zentrierung zu platzieren. In diesem Fall kann die Buchse weggelassen werden. Der Kunde kann dann die Gegenwälzfläche, auf der der Wälzkörper abwälzt, selbst herstellen. Das braucht einige Voraussetzungen, um dies präzise herzustellen. Gerade im dynamischen Bereich sprechen wir von circa vier Mikrometer Toleranz im Durchmesser. Aber mit den heutigen Maschinen ist die Einhaltung dieser Toleranz im Normalfall kein Problem.
Kugelzentrierung muss nicht gepaart sein
Die Wälzkörper sind vorgespannt und spielfrei. Spezifisch bei der Kugelzentrierung ist, dass sie nicht gepaart sein müssen. Agathon empfiehlt zwar, dass die Kugelzentrierung zusammenbleibt. Aber es gibt Anwendungen, bei der das nicht möglich ist, und dadurch hat man mit dieser Kugel-Feinzentrierung gewisse Vorteile.
Und genau das spielt in der Anwendung eine wesentliche Rolle, welche Guillaume Hopfner von der Firma Braunform GmbH im folgenden Gespräch mit Agathon Produktmanager Stefan Nobs beschreibt. Denn es handelt sich um ein Drehwerkzeug, bei der die Feinzentrierung immer wieder in einer anderen Buchse eingreift.
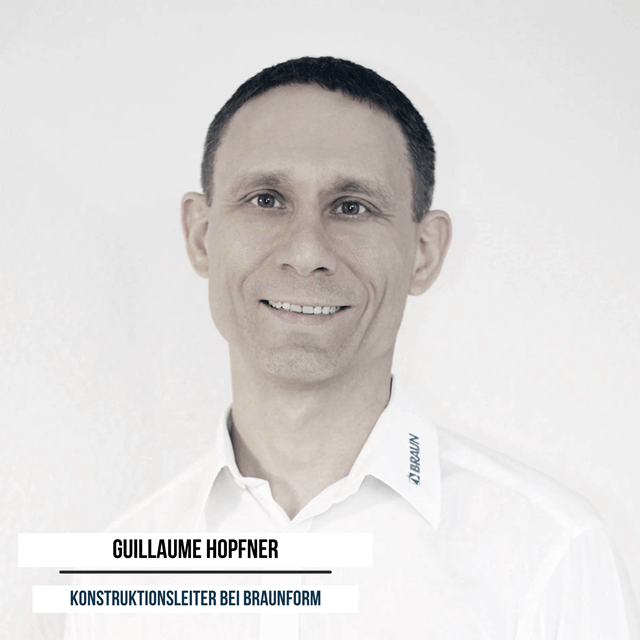

Guillaume Hopfner: Ja, wir sprechen hier vom Herz des Werkzeugs: dem Formbereich. Da die Spritzgiesswerkzeuge immer grösser werden, wird man irgendwann mit dem Problem konfrontiert, dass die Wärmeausdehnung zwischen der festen Seite und der beweglichen Seite des Werkzeugs einen Einfluss auf beide Hälften nimmt. Dafür teilt man die Kavitäten in eigenständige Inseln, die zueinander zentriert werden. Die Düse ist dabei fixiert und auf der Auswerfer-Seite lassen wir die Kavitäten-Inseln schwimmen, das nennt man in der Formenbau-Welt eine schwimmende Lagerung.
Bei jeder Werkzeugschliessung kann sich die Auswerfer-Seite an der Position der Düsenseite anpassen, das ist besonders interessant bei Zwei-Komponenten-Werkzeugen insbesondere mit Drehteller, weil die auswerferseitige Kavität bei jedem Zyklus die Position wechselt: einmal in die erste Station und nach der Drehung in die zweite Station. Der Vorteil der Mini-Feinzentrierung ist, dass sie so klein ist, dass man diese in der Trennebene der Kavität platzieren kann und je nach Platzverhältnis zwischen den Kühlbohrungen platzieren kann.
Dieses System kann sogar ohne Buchse eingebaut werden. Das heisst, auf der Gegenseite ist nur eine Laufbohrung einzubringen; das ist sehr vorteilhaft, wenn es um jeden Millimeter geht. Ein anderer Vorteil im Vergleich zu herkömmlichen Flachzentrierungen ist, dass man nur zwei Stück braucht und nicht vier. Aber für mich der wichtigste Vorteil ist jener, dass die Mini Feinzentrierung zylindrisch ist und spielfrei, sodass die Trennungen gut geschützt werden.
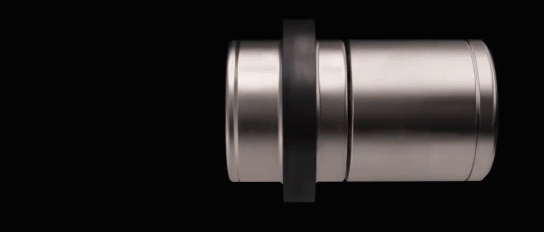
Anwendung ohne Schieber
Stefan Nobs: In Ihrer Anwendung ist mir aufgefallen, dass sie keine Schieber einsetzen. Das heisst mit anderen Worten, dass man gar keinen vorzentrierten Weg benötigt. Braucht man hier gar keinen geführten Weg?
Guillaume Hopfner: Wann die Zentrierung eingreift, ist eher zweitrangig. Weil viele Komponenten, die aufeinandertreffen im Werkzeug, normalerweise immer konisch hergestellt werden. Dadurch kommen sie erst im letzten Moment in Kontakt.
Stefan Nobs: Hinzu kommt bei einer Mini-Flachzentrierung, dass man vier Stück einsetzen müsste. Bei den Mini-Feinzentrierung von Agathon reichen bereits zwei Stück, um alle Freiheitsgrade einzuschränken. Das ist sicher auch ein grosser Vorteil, weil heutzutage die Kunden möglichst viele Kavitäten auf möglichst wenig Arbeitsfläche platzieren wollen. Ist das richtig?
Guillaume Hopfner: Das stimmt absolut. Wir versuchen, die Aufspannfläche der Maschine so effektiv wie möglich zu nutzen. Daher wollen wir in unseren Werkzeugen natürlich so viele Kavitäten wie möglich platzieren. Und wenn man dann weniger Platz benötigt für Funktionen wie Zentrierung, kann man vielleicht noch eine Reihe Kavitäten hinzufügen.
Vorzentrierung bei einem Drehwerkzeug
Stefan Nobs: Für mich stellt sich noch die Frage, da es sich ja hier um ein Drehwerkzeug handelt, wie präzise Sie vorzentrieren können. Man muss sich ja vorstellen, dass die Kavität rotiert. Wie genau kommt sie zu stehen und wie viel Zentrieraufgabe muss dann noch mit der Feinzentrierung übernommen werden?
Guillaume Hopfner: Die Grob-Vorzentrierung wird über das Hauptführungssystem vom Werkzeug übernommen. Natürlich, wenn die bewegliche Seite zur fixen Seite leicht versetzt ist, wird es durch die Drehung verdoppelt, das heisst, es kann dann schon zu einem Versatz von drei- bis vier Hundertstel Millimeter kommen. Das wird aber aufgenommen vom Hauptführungssystem des Werkzeugs, was die Vorzentrierung auf ein bis Zweihundertstel reduziert. Die Feinzentrierung muss nachher nur noch die verbleibenden zwei Hundertstel bewerkstelligen.
Mehrere Millionen Zyklen
Stefan Nobs: Und das ist generell ein idealer Zentrierweg, um zu korrigieren, sodass man eine Laufleistung von mehreren Millionen Zyklen erreichen kann.
Ich möchte noch kurz ein paar weitere Vorteile ansprechen. Eine betrifft die Bearbeitung. Man kann die Aufnahmebohrung für die Feinzentrierung zusammen mit der Form in einer Aufspannung von vorne machen. War das hier auch ein relevantes Feature, dass Sie ganz bewusst eingesetzt haben? Haben Sie da auch grosse Ansprüche an die Zentriergenauigkeit?
Guillaume Hopfner: Wenn man das jetzt vergleicht mit dem Einsatz von vier Flachzentrierungen, ist es auf jeden Fall genauer. Die zwei Bohrungen, die man einbringt für die Mini Feinzentrierung, kann man in einem einzigen Bearbeitungsvorgang in der Trennebene einbringen.
Wenn man vier Bahnen benötigt, um vier separaten Flachzentrierungen einzubringen, braucht man auch vier separate Aufspannungen auf jeder Seite des Einsatzes. Deshalb sind wir in dem Fall auf jeden Fall genauer.
Stefan Nobs: Wir haben es in dieser Episode bereits gehörte: Die Mini-Feinzentrierung muss man nur zwei Stück einsetzen im Minimum; wogegen in Flachzentrierungen vier eingesetzt werden. Wie sieht es preislich aus: Haben sie das schon verglichen?
Guillaume Hopfner: Ja, das haben wir. Der Einsatz der Agathon-Produkte ist ungefähr um den Faktor 1,5 günstiger, wenn man zwei Agathon Mini-Zentrierung einsetzt im Vergleich zu Flachzentrierung von Marktbegleitern.
♦ Folge 2 ♦
Kurzhub
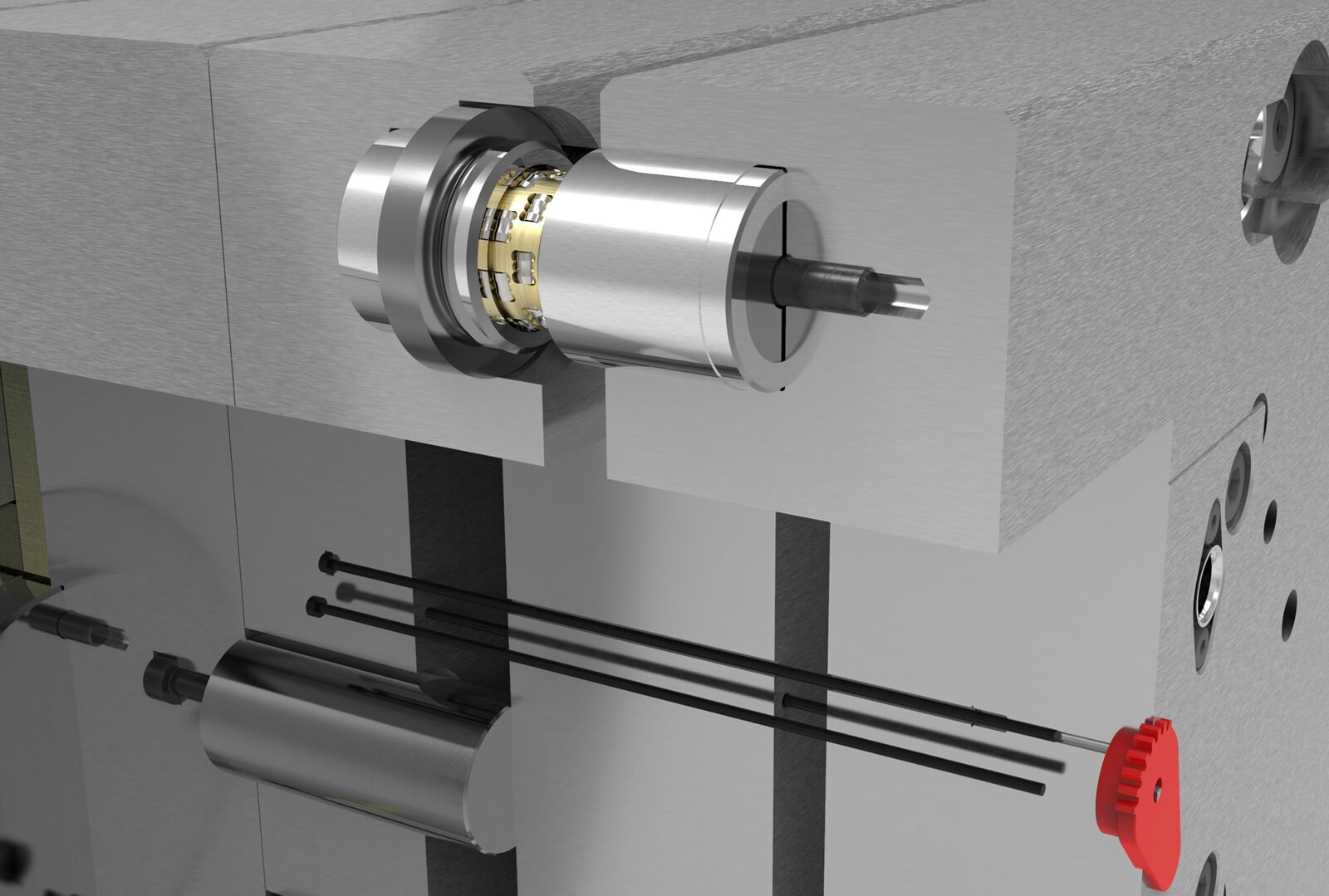
Beim Kurzhub wird mit einer Feinzentrierung eine kurze Distanz gefahren. Doch welche Anwendungen verbindet man damit? Offenbar mehr als sich der Normalienhersteller Agathon sich zuerst selbst vorstellen konnte.
In dieser Episode geht es um das Thema «Kurzhub». Der Name verrät auch diesmal wieder viel: Beim Kurzhub wird eine kurze Distanz gefahren mit einer Feinzentrierung. Typischerweise fährt man gar nicht aus der Vorspannung heraus, sondern verbleibt die ganze Zeit vorgespannt. Die Feinzentrierungen sind mit Wälzkörpern bestückt. Das heisst, die Führung wälzt sehr weich ab. womit ein Ruckgleiten verhindert wird. Ausserdem setzt Agathon Rollenwälzkörper ein, die einen Linienkontakt haben. Das hat den Vorteil, dass sehr grosse Radialkräfte auf die Führung wirken können. Und weil es ein Kurzhub ist, drehen die Wälzkörper kaum eine ganze Umdrehung. Eingesetzt werden Wälzkörper vielfach mit Durchmesser von drei oder vier Millimeter. Rechnet man Durchmesser mal Pi, so ergibt dies circa zwölf Millimeter als Abwälzlänge am Umfang. Diese erreichen Anwendungen in der Regel nicht, demzufolge machen die Wälzkörper nur eine Wippbewegung.
Feinzentrierung: Intitialschmierung und los geht’s!
Die Feinzentrierung ist sehr kompakt, nicht nur im Durchmesser, sondern auch in der Länge. Das wiederum gibt weitere gestalterische Möglichkeiten. Agathon hat hierzu eine spezielle Normreihe entwickelt. Es ist eine Weiterentwicklung der Ur-Normreihe, wo klassisch zentriert wird. Die Entwickler mussten hier einfach noch einen Stopp einbringen, damit der Käfig bei diesen kurzen Hüben jederzeit in der Position bleibt. Mit den Mini-Feinzentrierungen kann man ebenfalls solche Kurzhübe machen –, dann natürlich in einem kleineren gestalterischen Bereich. Die Agathon Feinzentrierung sind einbaufertig. Eine kleine Initialschmierung und schon kann die Produktion starten. Damit sind ein paar Details zu dieser Art der Führungen und Zentrierungen erwähnt. Wie aber kann man sie anwenden – und vor allem: Wie wird sie beim Agathon-Kunden Braunform angewendet?
Das erfahren wir in der Folge 2 des Agatalks mit Guillaume Hopfner, von der Firma Braunform GmbH, im Gespräch mit Agathon-Produktmanager Stefan Nobs.
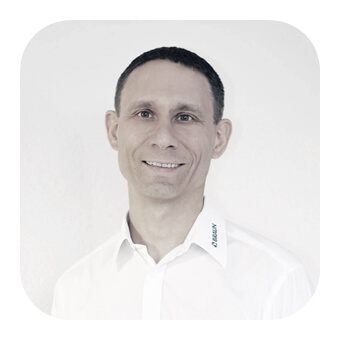
Guillaume Hopfner: Bei Braunform bauen wir die Feinzentrierung Plus oft in Werkzeuge mit zweistufiger Abhebung ein. Ich habe als Beispiel ein Werkzeug, bei dem sehr dünne Kernstifte in einer ersten Stufe über die Abhebung gezogen werden sollen und danach kommt das Kunststoffteil komplett entformt über die Auswerfer. Die Toleranz des Artikels liegt im Bereich von ±0,02, was natürlich keine grosse Freiheit in der Werkzeug-Genauigkeit zulässt. Das Werkzeug ist 16-fach ausgelegt und das verarbeitete Material ist POM (Polyoxymethylen), d. h. das Werkzeug wird warm gefahren mit circa 90 Grad Celsius.
Das Werkzeug fährt auf und die Schieber fahren mit dieser Öffnungsbewegung auf. Danach fahren die Auswerfer und die abhebende Platte parallel vor. Diese erste Stufe beträgt nur vier Millimeter. In diesem Moment hängt die ganze Formplatte, auf der die Schieber liegen, nur noch auf den kleinen Agathon-Feinzentrierungen. Erst dann fahren die Auswerfer vor und entformen die Teile komplett aus der Kavität heraus. Die Feinzentrierungen haben zwei Aufgaben: Erstens tragen sie das Gewicht von ca. 50 Kilo der abhebenden Platte bei diesem vier Millimeter Hub. Und zweitens schützen sie durch höchste Präzision die 1,6 mm-Stifte von einem Versatz während der Bewegung. In unserem Fall muss die Zentrierung auch noch Querkräfte aufnehmen, weil die Schieber auf die abhebende Platte zeitversetzt fahren. Durch die hohe Tragfähigkeit der Agathon-Zentrierteile haben wir sogar auf weitere Führungselemente der Platte verzichtet.
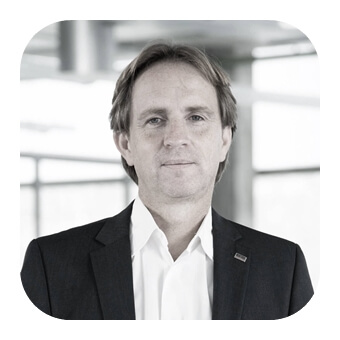
Stefan Nobs: Wenn ich mich recht erinnere, haben Sie diese Werkzeug-Konstruktion schon vor ein paar Jahren entwickelt. Wie hat sich dieses Werkzeug im täglichen Einsatz bewährt?
Guillaume Hopfner: Wir haben sogar schon zwei Werkzeuge mit dieser Lösung gebaut. Sie laufen seit 2017 und 2019 rund um die Uhr in der Produktion und bisher wurde noch keine Feinzentrierungsteile ersetzt. Die Hauptvorteile der Anwendung mit Fein-Zentrierung Plus sehen wir vorrangig in der Langlebigkeit und im spielfreien Schutz der Formstifte während der Bewegung.
«Sobald ein sehr kurzer Hub gefahren wird, ist die Fein-Zentrierung Plus sehr interessant»
Stefan Nobs: Bezüglich solcher Kurzhub-Anwendungen haben wir aus Sicht von Agathon immer wieder weitere mögliche Anwendungen wahrgenommen. Eine dieser potenziellen Anwendungen ist gewissermassen ein Entlüftungshub, der gefahren wird im Formenbau, d. h., die Platte hebt ein wenig ab. Eine andere ist das Spritzprägen. Da wird wahrscheinlich auch ein sehr kurzer Hub gefahren. Soweit ich weiss, wird dort der Kunststoff nachgedrückt in der Abkühlphase. Wie sehen Sie das mit diesen zwei Anwendungen?
Guillaume Hopfner: Ja, natürlich, sobald ein sehr kurzer Hub gefahren wird, ist diese Fein-Zentrierung Plus sehr interessant. Beim Spitzprägen fährt man gewöhnlich nur ein paar zehntel Millimeter, beim Entlüftung reichen natürlich auch locker ein oder zwei zehntel Millimeter Bewegung, d. h., da kann man auf jeden Fall diese Fein-Zentrierung Plus einsetzen.
Bild: Feinzentrierung Plus für Führungsanwendungen, bei welchen nicht aus der Buchse gefahren wird.
Stefan Nobs: Und ich glaube, dieser Entlüftungshub gleicht dem Beispiel, das Sie uns erklärt haben.
Guillaume Hopfner: Ja, und es kann auch auf beiden Seiten des Werkzeugs eingesetzt werden: entweder auf der Düsenseite oder Auswerferseite. Es braucht natürlich nicht viel Hub. Ich persönlich würde vielleicht ein wenig grosszügiger fahren als nur ein paar zehntel Millimeter, um die Entlüftungslagen respektive -flächen zu reinigen, sodass auch der Expansionsraum über die Entlüftungsfläche fahren. Der Vorteil liegt darin, dass dann ein paar Partikel wieder nach hinten mitgenommen würden und die Kavität sauber für den nächsten Zyklus wäre.
Stefan Nobs: Das ist ein sehr interessanter Hinweis. Und aufgrund solcher Rückmeldungen haben wir den Kurzhub auch weiter ausgebaut. Wir mussten auch die Broschüren weiterentwickeln, denn am Anfang haben wir nicht an solche Kurzhub-Anwendungen gedacht. Wir haben unter anderem den geführten Weg bei diesen Zentrierungen weiterentwickelt – das sieht man bei der Rubrik L5 [L5 ist der geführte Weg, bis das Werkzeug geschlossen ist]. Damit wir da noch etwas Sicherheit haben für den Kurzhub, haben wir in der Broschüre jetzt «L5 minus 1,5 Millimeter» hinterlegt. Also man kann da die ganze Länge ohne diese startenden 1,5 mm verwenden.
Was mir hier noch einfällt zu diesem Kurzhub, sind die Auswerferpakete. Es gab also auch schon Kunden, die offenbar die Fein-Zentrierung für diese Kurzhub-Anwendung eingesetzt haben.
Guillaume Hopfner: Da haben Sie recht, man kann es für ganz flache Teilen zum Beispiel einsetzen, die wenig Entformungshub benötigen. Ich denke, es gibt viele Teile, die mit vier oder 5 mm aus der Kavität schon entformt werden können und dann kann man diese Teile relativ gut da einsetzen.
Agathon Normalien
Hohe Oberflächengüte, bestens verarbeitete Werkstoffe, engste Toleranzen, präzise, spielfrei, lange Lebensdauer: die Agathon Normalien stehen im Maschinenbau, im Formenbau und als Stanzwerkzeuge im Einsatz. Agathon ist seit Jahrzehnten der weltweite Innovationsführer, wenn es um die Entwicklung von hochpräzisen Maschinenelementen, hochpräzisen Normalien geht. Dies speziell im Bereich von spielfreien Führungs- und Zentriersystemen.
♦ Folge 3 ♦
Auswerferführung
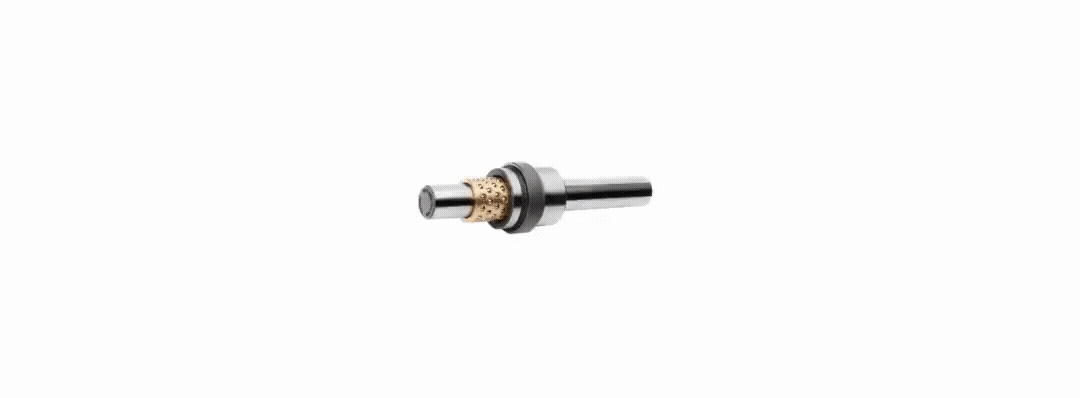
Wenn man den Stand der Technik anschaut, dann sieht man, dass in der Branche nach wie vor mehrheitlich Gleitbuchsen eingesetzt werden. Dabei gäbe es höherwertige Alternativen.
Eine Gleitbuchse gleitet auf der Säule und hat dadurch ein Spiel. Das ist ein grosser Nachteil. Die Firma Agathon hat als Alternative die höherwertige Kugelführung entwickelt. Diese werden hauptsächlich für Dauerläufer eingesetzt und dort, wo man eine Momentbelastung erwartet und das Auswerferpaket abkippen könnte.
Der Grund dafür ist, dass die Wälzkörper in den Endzonen, also vorne und hinten, zu hoch belastet waren. Der Wälzkörper wälzt trotzdem ab, die Gleitführung hat aber dann ein Problem wegen der zu hohen Flächenpressung. Sollte diese Momentbelastung zu hoch werden, kann man alternativ eine Rollenführung einsetzen. Die Rollenführung hat den grossen Vorteil, dass sie dank des Linienkontakts sechs bis acht Mal mehr Tragfähigkeit hat als die Kugelreihe – das allein macht schon deren Mehrwert aus. Auch die Kugelumlaufbuchse wird gelegentlich eingesetzt für diese Art der Anwendung.
Die Kugelumlaufbuchse wiederum hat den Vorteil, dass mit ihr ein unendlich langer Hub gefahren werden kann, was allerdings bei den Auswerferführungen nicht relevant ist. Die Kugelumlaufbuchsen haben aber einen entscheidenden Nachteil: Die Kugeln zirkulieren und kehren immer wieder an den Anfang zurück bei einem Hub. Sie benötigen daher mehr Platz. Diese Buchsenart hat auch eine grössere Wandstärke, damit die Kugeln zirkulieren können. Das bedeutet auch, dass die Kugeln viel kleiner sind und somit weniger Tragkraft erreichen im Vergleich zum Agathon-System. Grundsätzlich werden aus den erwähnten Platzgründen auch weniger Wälzkörper eingesetzt. Mit anderen Worten: Agathon hat hier gegenüber solchen Kugelumlaufbuchsen viel mehr Tragkraft zur Verfügung.
In der Folge 3 des Agatalks sprechen wiederum Guillaume Hopfner, von der Firma Braunform GmbH, und Agathon-Produktmanager Stefan Nobs über Anwendungen, deren Vorteile, Herausforderungen und auch über die Investkosten.
Stefan Nobs: Herr Hopfner, Sie haben zum Thema «Auswerferführungen» eine interessante Anwendung. Bitte schildern Sie diese.
Guillaume Hopfner: Zuerst möchte ich erwähnen, wie überraschend es ist, dass wir über Auswerferpaketführung reden. Aber die Qualitätsanforderungen an die Kunststoffteile sind heutzutage so hoch, dass man sogar über solche Standardtechnik reden muss. Gewöhnlich legt man nicht viel Wert auf solche Funktionen. Es werden oft einfach Gleitführungen eingesetzt. Wir haben aber Fälle, bei denen wir von den vielen Vorteilen der Auswerferführungen von Agathon profitieren können. Zum Beispiel bei kleinen Durchmessern um Durchmesser zwölf. Im Vergleich zu den Produkten der Marktbegleiter muss ich auch sagen, dass bei Agathon die Anzahl der Kugeln im Kugelkäfig höher ist und ich schätze dadurch auch kleiner im Durchmesser. Wir haben diese Einheit erfolgreich eingesetzt und einige Probleme dadurch korrigiert.
Aber zur Anwendung selbst: Wir haben sie eingesetzt in einem Zwei-Komponenten-Indexwerkzeug, bei dem wir an beide Stationen Auswerferpakete brauchen. Die Krafteinleitung des Ausstossbolzens sitzt nicht mittig, da beide Kavitäten versetzt im Werkzeug liegen; die Gegenkraft, die von den Auswerfern kommt, sitzt am Rand der Auswerferplatte. Durch diese ungünstige Konstellation neigt das Auswerferpaket zu kippen, sodass Auswerfer in das Kunststoffteil eindrücken können, was sichtbare Spuren hinterlässt. Nach dem Einbau der Auswerferführungen von Agathon mit Durchmesser zwölf wurde der Kippeffekt stark reduziert und dadurch ist die Markierung am Teil verschwunden. Das kann ich also eindeutig sagen: Die Teilequalität wurde durch die Auswerferführung verbessert.
Stefan Nobs: Für mich stellt sich die Frage, wie es aussieht, wenn man wieder zurück auf die Gleitführung geht. Wenn eine Gleitführung ausfällt, welche Konsequenzen hätte das? So eine Gleitführung kann, wenn sie hoch belastet ist, zu einer Kaltverschweissung führen. Das heisst, die Gleitführung blockiert und das Werkzeug wird trotzdem weitergefahren. Wie sieht es dann aus: Wird das Werkzeug zerrissen oder wie muss man sich das vorstellen?
Guillaume Hopfner: Eine Auswerferführung mit Gleitbuchsen läuft ja über eine reine Kontaktpassung. Natürlich in diesem erwähnten Fall, wenn es eine Überlastung gibt, neigt es dann zum «Fressen». Wenn das Auswerferpaket abkippt, verkanten die Buchsen auf den Säulen und die Flächenpressung überschreitet punktuell die maximale Druckfestigkeit. Die Führung setzt sich fest und das Auswerferpaket kann nicht mehr bewegt werden. Dadurch muss das Werkzeug aus der Produktion zur Reparatur gezogen werden. Mit Kugelführung ist es meiner Meinung nach sicherer. Ein Notbetrieb ist möglich, womit ein Stillstand vermieden werden kann bis zur nächsten Wartung.
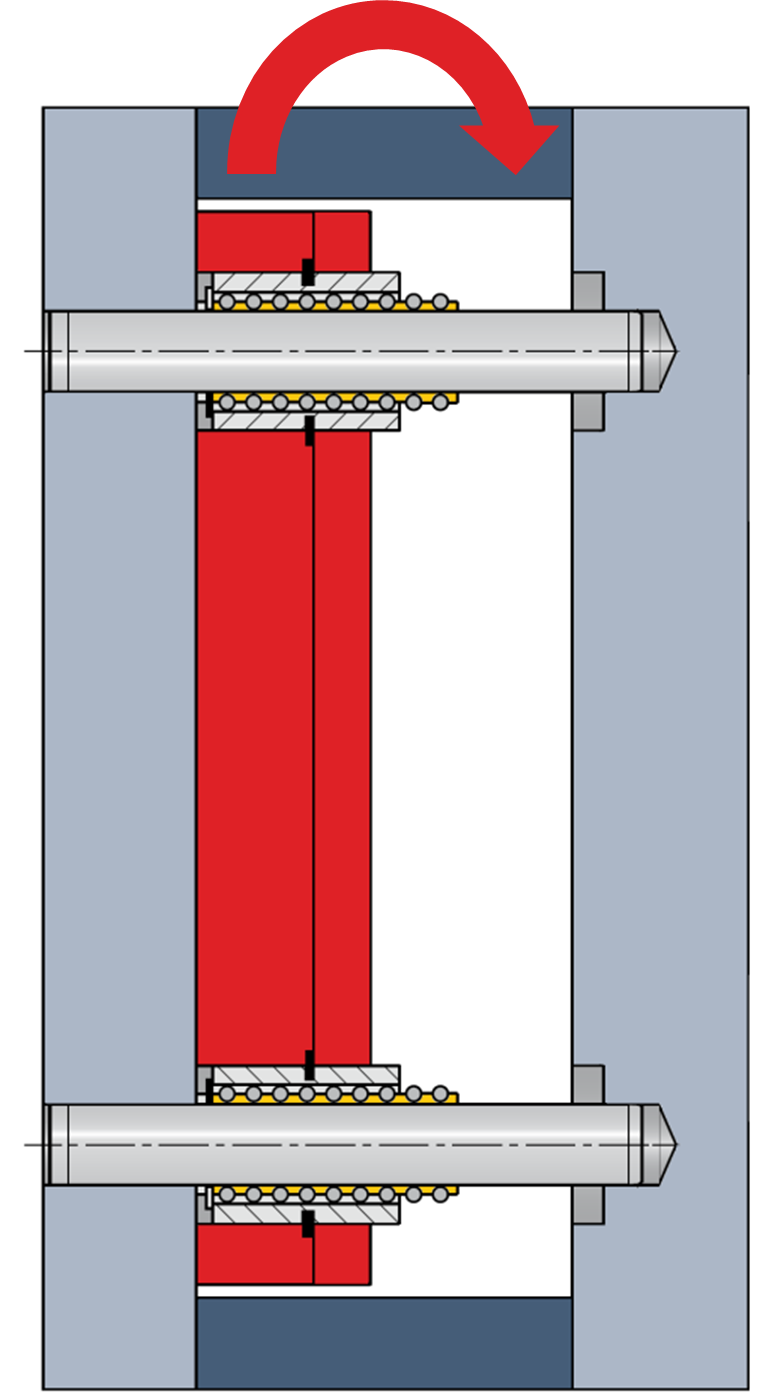
- Ausführung je nach Grösse und Belastung als Kugel- oder Rollenführung möglich
- Ruckfreie Bewegung
- Auswerferstifte sowie alle beteiligten Passungen und Bohrungen in den Formeinsätzen
- Hohe Steifigkeit beugt dem Kippen der Platten vor
- Temperaturbeständig bis 140 °C (Aluminium-Käfig) respektive 170 °C (Messing-Käfig)
Stefan Nobs: Wenn so eine Führung anfrisst, dann eher nicht alle vier gleichzeitig, sondern vielleicht nur eine von vier.
Guillaume Hopfner: Ja, das ist exakt, was dann passiert: Ein Auswerferpaket wird gewöhnlich mit vier Führungssystemen geführt. Wenn es an einer Stelle frisst, dann geschieht die Kraftübertragung nur noch an den drei freien Führungssystemen – und einer hängt.
Stefan Nobs: Dadurch kippt dann das Auswerferpaket wahrscheinlich im Zehntelbereich ab.
Guillaume Hopfner: Das kann sogar bis zu einem Millimeter sein.
Stefan Nobs: Die Auswerfer werden dann nach vorne geschoben und das Kunststoffteil erhält diesen geschilderten Abdruck, den man vermeiden will.
Guillaume Hopfner: Wenn aber eine Gleitführung «frisst», dann kann das Auswerferpaket nicht mehr bewegt werden. Das heisst, es bleibt dann komplett stehen und die Maschinensicherung stoppt die Bewegung.
Stefan Nobs: Was wiederum heisst, man muss die ganze Produktion stoppen, das Werkzeug runternehmen, in die Wartung geben und vielleicht alternativ einen anderen Job starten.
Wir haben auch schon über den Notbetrieb gesprochen. Das ist vielleicht auch der grosse Vorteil bei den Wälzkörpern: Sie können einen gewissen Schaden nehmen. Es kann eine bleibende Deformation geben, einen Abdruck auf der Säule oder auf der Buchse oder der Wälzkörper kann leicht deformiert werden. Aber grundsätzlich bleiben die Kugelauswerferführungen einsetzbar und man kann wahrscheinlich noch weiter damit produzieren. Haben Sie das auch schon so erlebt?
Guillaume Hopfner: Ja, es kann sein, dass nach einer Beschädigung der Führung sichtbare Markierungen am Kunststoffteil entstehen. Dann muss man entscheiden, ob man dann weiter produziert oder ob man aufhört. Aber man kann auf jeden Fall weiter produzieren. Wenn nur eine Seite des Auswerferpakets ein Problem hat mit einem Führungssystem, sind manchmal auch nur die Hälfte der Kavitäten von der Markierung betroffen. Die andere Hälfte ist wahrscheinlich noch verwendbar. Es liegt dann an der eigenen Entscheidung, ob man noch einen Tag weiter produzieren will, indem man nur die Hälfte der Produktion verwendet und erst danach das Werkzeug abbaut.
Bei Braunform bauen wir in den letzten Jahren grundsätzlich Kugelführungen ein. Der Grund dafür ist einfach: Wir übernehmen die Anforderungen der Medizinbranche und daher sind die Kugelführungen das perfekte Produkt dafür. Guillaume Hopfner
Stefan Nobs: Die Auswerferführung ist sicher eine vielleicht etwas unterschätzte, aber ganz wichtige Anwendung. Haben sie dafür auch eine Konstruktionsrichtlinie, die vorgibt, bei welchen Ansprüchen zwingend eine Kugelführung eingebaut werden muss und bei welchen eine günstigere Gleitführung reicht?
Guillaume Hopfner: Eine solche gab tatsächlich vor ein paar Jahren. Aber bei Braunform bauen wir in den letzten Jahren grundsätzlich Kugelführungen ein. Der Grund dafür ist einfach: Wir übernehmen die Anforderungen der Medizinbranche und daher sind die Kugelführungen das perfekte Produkt dafür.
Stefan Nobs: Der Investaufwand steht ja im Verhältnis zu einem gesamten Werkzeug – und damit minimal. Haben Sie da Zahlen, die das unterstrichen können?
Guillaume Hopfner: Ein Werkzeug kostet oft mehrere hunderttausend Euro. Man braucht da tatsächlich nicht Rücksicht zu nehmen auf die 400 Euro, welche man für die Kugelführung des Auswerferpakets investiert, zumal die Sicherheit und die Partikelfreiheit in dem Fall wichtiger ist.
Diese paar hundert Euro, die man vielleicht mehr investiert, lohnen sich also auf jeden Fall. Denn mit ihnen schützt man das ganze Werkzeug, das mehrere hunderttausend Franken kosten kann.
♦ Folge 4 ♦
Feinzentrierung Plus dynamisch
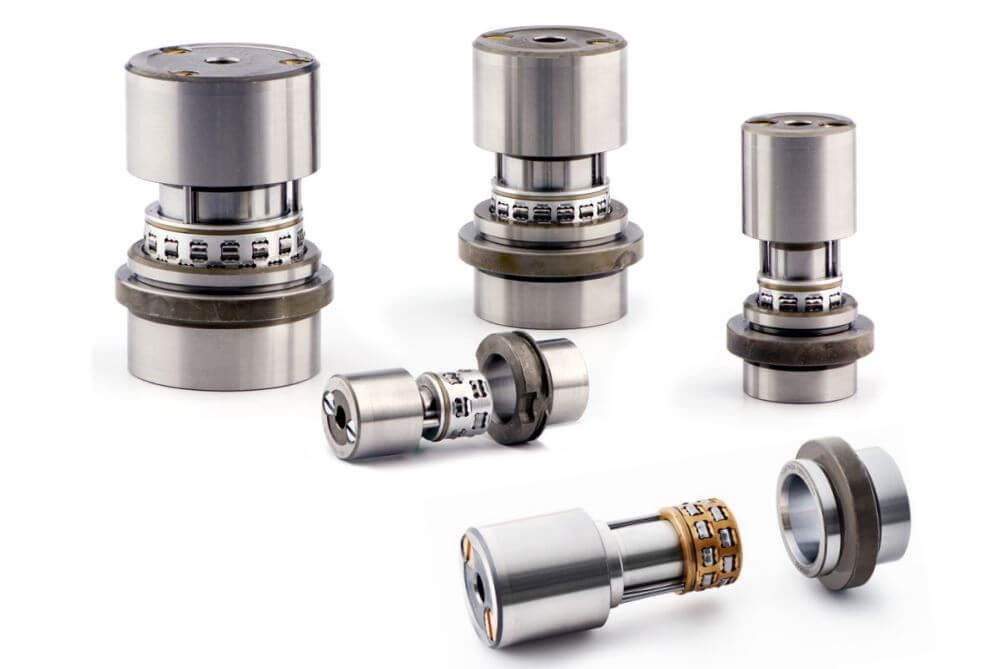
Flachzentrierungen waren lange das Mass aller Dinge. Sie haben aber einige Nachteile, dazu gehört auch der Abrieb. Agathon bietet mit der Feinzentrierung eine höherwertige Alternative. In diesem Teil geht es um diese Feinzentrierung in der Ausführung Plus dynamisch.
Vor rund zwölf Jahren – also im 2010 – hatte Agathon die ersten Feinzentrierungen entwickelt. Das Ziel war, den Kunden eine höherwertige Alternative zur weitverbreiteten Flachzentrierung anbieten zu können. Und da Agathon spezialisiert ist auf die runde Fertigung, ist die Feinzentrierung Plus gewissermassen auch rund geworden. Doch nicht einfach nur deshalb. Denn «rund» bietet auch sehr viele Vorteile. Eine Bohrung ist in der Regel bereits viel präziser hergestellt aufgrund der Herstellverfahren und dadurch auch kostengünstiger als eine Aufnahmetasche für eine Flachzentrierung.
Funktionsprinzip Feinzentrierung versus Flachzentrierung
Aber noch kurz zu den Funktionsprinzipen beider Varianten. Die Flachzentrierung ist gleitend. Damit sie gleiten kann, hat sie bereits im Neuzustand ein Spiel. Je nach Abmessung ist dieses Spiel bereits bis ein Hundertstel gross. Durch den Abrieb wird dieses Spiel im Laufe der Zeit immer grösser, da ja die Oberflächen aufeinander gleiten und es zu Festkörperreibung kommt. Die Agathon Feinzentrierung dagegen ist spielfrei oder anders gesagt: Die Wälzkörper sind vorgespannt. Es werden Rollen-Wälzkörper eingesetzt mit Linienwälzkontakt, der Linienkontakt schmiegt sich an die Säule und Buchse an. Das alles ergibt eine sehr hohe Tragkraft, sodass selbst schwere Werkzeuge zueinander auszentriert werden können.
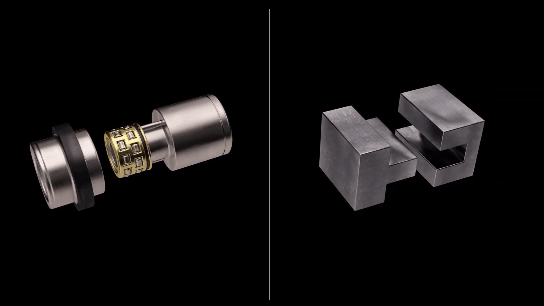
Portfolio der Feinzentrierungen wächst
Mittlerweile ist das Produktprogramm gewachsen. Die kleinste Feinzentrierung Plus hat einen Aufnahmedurchmesser von 20 Millimeter und kürzlich hat Agathon das Portfolio nach oben erweitert, damit man bei Werkzeugen eingesetzt werden kann, die rund 800 × 1000 Millimeter Abmessung haben.
Zudem gibt es inzwischen auch eine Feinzentrierung Plus für den Premium-Bereich. Diese verfügt über einen längeren Zentrierweg, womit auch höher bauende Kunststoffteile sauber entformt werden können. Die Premium-Variante bietet daneben auch noch weitere Vorteile. Unter anderem wird ein Messingkäfig eingesetzt. Messing hat den Vorteil, dass die Feinzentrierung Plus auch ein Ultraschallbad unbeschadet übersteht. Sie muss also nicht separiert werden.
Willkürlich auf der Formplatten-Oberfläche platzieren
Doch wie wird die Feinzentrierung Plus eingesetzt? Was sind deren Vorteile und wie sieht es mit der Wartung aus? Die Firma Braunform hat einige Anwendungen, über die in der Folge 4 gesprochen werden soll.
Guillaume Hopfner: Die Feinzentrierung Plus setzen wir ihn herkömmlichen Werkzeugen seit über 10 Jahren ein – und zwar bei allen Arten von Werkzeugen. Ob Ein- oder Zweikomponente, mit komplexer Entformung oder mit Schieber: Das System ist in der Werkzeug-Trennebene überall einsetzbar.
Klassisch werden vier grosse Flachzentrierungen in die Formplatten eingebaut und die Einsätze direkt über den Aufbau zueinander zentriert. Wir ersetzen diese durch zwei dieser Agathon Feinzentrierungen. Je nach Werkzeuggewicht auch mehr, so wie es im Katalog definiert ist. Der grosse Vorteil ist: Man kann die Feinzentrierungen willkürlich auf der Formplatten-Oberfläche platzieren – sogar mit kurzem Abstand – und trotzdem erreichen wir eine hohe Präzision. Durch die robuste Bauweise ist die Standfestigkeit sehr hoch.
Stefan Nobs: Sie sprechen die hohe gestalterische Freiheit an, was bedeutet, dass man die Feinzentrierung dort platzieren kann, wo man Platz hat. Wenn ich die Konstruktion betrachte, über die wir sprechen, sehe ich, dass die beiden Feinzentrierungen links und rechts angeordnet ist. Wie kam es dazu? Was für Überlegungen haben Sie hier gemacht?
Guillaume Hopfner: Dafür gibt es zwei Gründe. Im Formenbau mögen wir es nicht, wenn Elemente im Fallschacht überstehen, und zwar wegen der Verschmutzungsgefahr der Kunststoffteile. Und zweitens sind wir bei manchen Kunden oder in manchen Ländern auch nicht sicher, wie die Kühlleistung erbracht wird. Dadurch entsteht die Gefahr, dass beide Formplatten sich unterschiedlich ausdehnen. Deshalb wollen wir den Abstand zwischen den Feinzentrierungselementen geringer halten, da das Werkzeug sehr lang ist. Und mit «sehr lange» meine ich eine Länge von über einem Meter.
Limitierter Wärmesprung zwischen den Werkzeughälften
Stefan Nobs: Sie sprechen das Thema an mit der unterschiedlichen Ausdehnung der beiden Werkzeughälften. Wir wissen, dass diese Befürchtung im Formenbau sehr tief verwurzelt ist und dass da die Flachzentrierung gewisse Vorteile bieten kann. Wir haben dies deshalb auch genau untersucht, ob es wirklich einen Wärmesprung gibt von einer Werkzeughälfte zur anderen. Das Resultat hat unsere eigenen Annahmen und Theorien bestätigt.
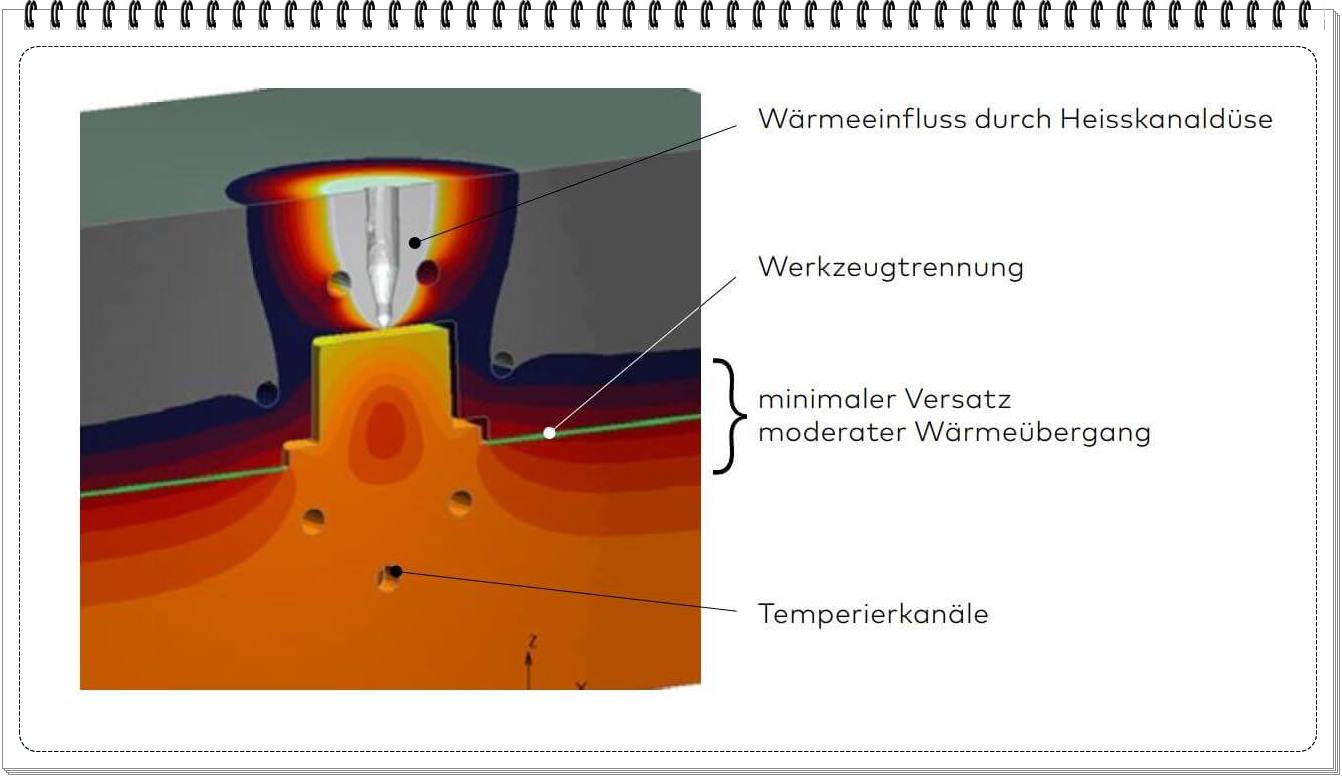
Es zeigte sich nämlich, dass die beiden Werkzeughälften, wenn es geschlossen ist während des Einspritzprozess, sich temperaturmässig komplett zueinander abgleichen. Somit ist dieser Wärmesprung sehr limitiert. Die unterschiedliche Wärmeausdehnung und die Feinzentrierung können auch nicht gross zueinander verspannen. Was man dazu noch sagen kann: Die Feinzentrierung ist nicht unendlich steif, also sie kann gewisse Unterschiede auch zueinander ausgleichen.
Für mich noch eine weitere Frage, die ich gerne aufbringen würde: Sie haben da auch von exakt zentrieren gesprochen. Was heisst für sie «exakt» im Formenbau?
Guillaume Hopfner: Exakt zentrieren heisst bei uns auf jeden Fall unter einem Hundertstel zu sein, damit die Trennungen geschützt werden. Es gibt immer auch Positionsfehler durch die Bearbeitung der Aufnahmetaschen und den Einsätzen. Aber hier haben wir einen weiteren Vorteil mit den Feinzentrierungen plus, und zwar, weil die Kavitätentasche im selben Bearbeitungsvorgang mit der Zentrieraufnahme gefertigt wird. Die Zentrierungselemente sind letztlich dann nur ein Glied in der ganzen Zentrierkette – die weiteren Elemente im Werkzeug sind genauso wichtig.
Wiederholgenauigkeit im Sub-Mikrometerbereich
Stefan Nobs: Ja, das stellten wir auch fest: Das Verständnis mit dieser Zentrierkette – wir nutzen hier auch den Begriff «Anschlusskonstruktion» – ist wichtig zu betrachten. Wir haben zudem untersucht, wie präzis so eine Feinzentrierung ist. Wir konnten feststellen, dass die Wiederholgenauigkeit im Sub-Mikrometerbereich ist. Es waren um die 0,3 Mikrometer, was sehr genau ist. Das heisst mit anderen Worten: Im Formenbau muss man diese ganze Kette, diese Anschlusskonstruktion, genau anschauen. So erhält man dann als Resultat die Exaktheit, die Sie erwähnten.
Für mich stellt sich dann auch noch eine weitere Frage: Es geht auch um Zentrierkonzepte. Wenn möglich, möchte man schwimmende Kavitäten aus Kostengründen vermeiden. Aber wo ist dann die Grenze? Wenn man eine Schliessgenauigkeit von einem hundertstel Millimeter hat, muss man dann eine schwimmende Kavität anstreben? Oder wo sehen sie die Trennung, bei der man «schwimmend» gehen muss?
Guillaume Hopfner: Ja, ab einer gewissen Grösse gehen wir ohnehin auf schwimmende Lagerung über. Das ist die der sicherste Weg, um das Werkzeug zu bauen und die Genauigkeit zwischen den Kavitäten hinzubekommen.
Feinzentrierungen benötigt sehr wenig Schmierung
Stefan Nobs: Ich möchte noch die Wartung und Tribologie erwähnen, denn auch hier gibt es sehr grosse Unterschiede: Gleitende Flächen muss man dauernd schmieren und trotzdem kommt der Schmierstoff gar nicht an die Schmierstelle. Das ist eigentlich bei der Flachzentrierung der Fall, denn die Werkzeuge fahren aufeinander zu, dann wird plötzlich zentriert. Man hat keine Überlappung der Flachzentrierung: Wenn die Flachzentrierhälften aufeinandertreffen, wirkt dies durch den Versatz fast wie eine Kollision. Es besteht am Zentrierstart nur ein Linienkontakt und dort ist die Flächenpressung gewissermassen unendlich hoch und damit wird bereits die Oberfläche der Flachzentrierung zerstört. Nachdem die Flachzentrierung vielleicht ein Drittel Überlappung hat, kann man davon ausgehen, dass doch ein wenig Schmierstoff die Schmierstelle erreicht und das ganze System anfangen würde zu funktionieren. Aber eben auf dem ersten Drittel wird viel Abrieb erzeugt und dieser Abrieb wird eingewalzt in die Flächen und auch vermengt mit dem Schmierstoff. Das alles ergibt einen ziemlichen Abrieb, der insbesondere im Reinraum nicht erwünscht ist.
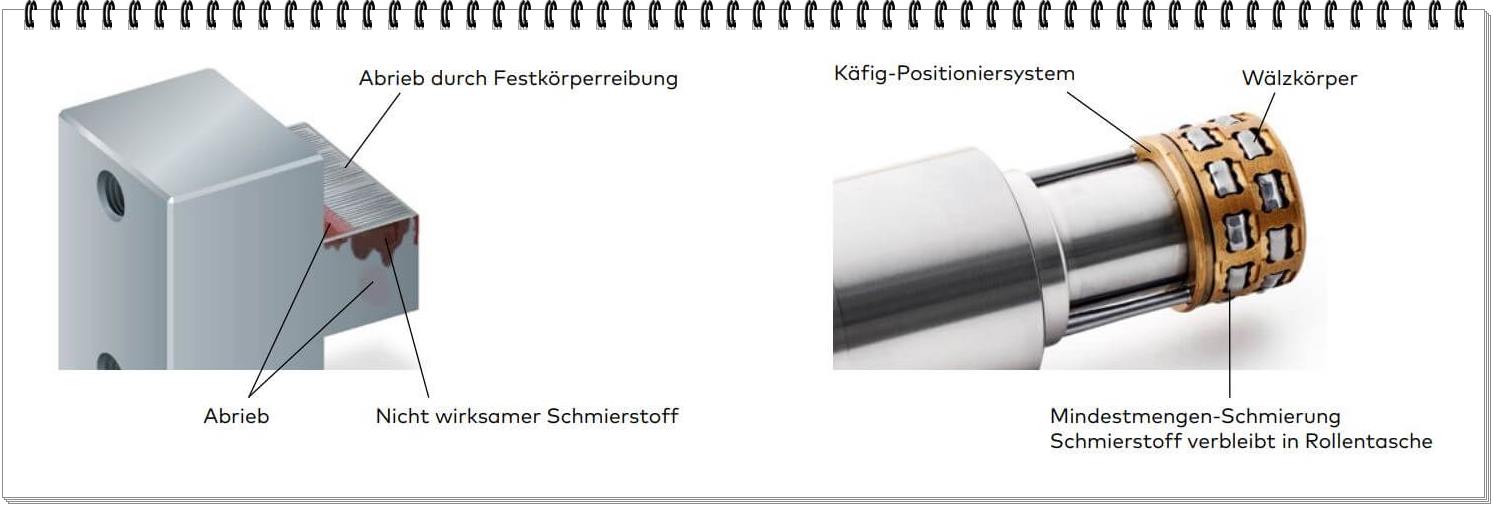
Hier setzt die Agathon-Lösung ein, und zwar mit der abwälzenden Feinzentrierung. Diese benötigt sehr wenig Schmierstoff, eine sogenannte Mindestmengenschmierung ist ausreichend – je nach Viskosität des Schmierstoffs, den man einsetzt. Schlussendlich muss sich der Kunde zwar selbst ein Know-how aufbauen, wie oft die Feinzentrierung geschmiert werden muss. Ich denke aber, das ist nicht mehr als wöchentlich, vielleicht sogar nur zweimal im Monat.
Für mich ist das ein wichtiger Vorteil. Gerade heute beim Fachkräftemangel müssen solche Werkzeuge auch autonom laufen können. Wie sehen Sie das?
Guillaume Hopfner: Genauso. Die Monteure in den Wartungsabteilungen sind erst einmal verwundert, wenn wir ihnen erklären, wie wenig Schmierung eine Feinzentrierung Plus von Agathon benötigt. Sie sind es gewohnt, täglich zu fetten. Hier liefert Agathon übrigens klare Anweisungen auch bezüglich Wartung, Reinigung und Schmierung – und seit wir diese Anweisungen der Werkzeug-Dokumentation beiliegen, haben wir noch weniger Ausfälle bei Agathon Zentrierungen als ohnehin schon.
Die Monteure in den Wartungsabteilungen sind erst einmal verwundert, wenn wir ihnen erklären, wie wenig Schmierung eine Feinzentrierung Plus von Agathon benötigt.
Stefan Nobs: Apropos weniger Ausfälle und hohe Lebensdauer – da muss ich noch etwas erwähnen. Am Anfang, wenn das Werkzeug zentriert werden soll, ist ja eine Hälfte hängend. Diesen Umstand haben wir konstruktiv entgegengewirkt, indem wir bei der Feinzentrierung Plus einen fast zweifachen Rolleneintritt bewerkstelligt haben. Also einen Mechanismus entwickelt für eine hohe Anfangstragkraft, sodass praktisch zwei Rollenreihen sofort in den Eingriff kommen.
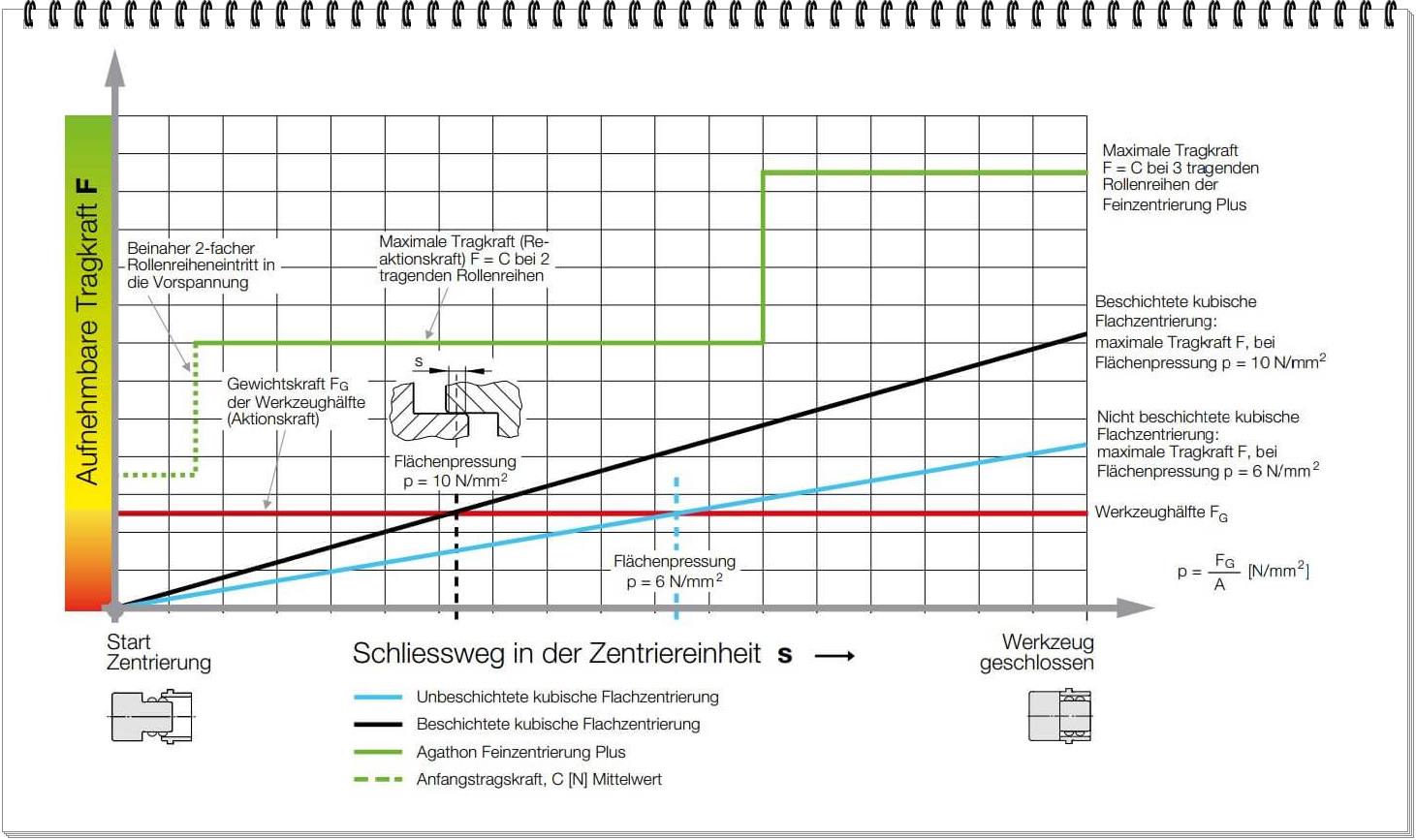
Damit man sich das auch bildlich vorstellen kann: Unsere Rollen haben eine hohe Tragkraft wegen des Linienkontakts. Eine Rollenreihe ersetzt gewissermassen acht Kugelreihen. Wenn wir dann gleich zwei Rollenreihen miteinander zum Tragen bringen, dann haben wir entsprechend sechzehn Kugelreihen, die helfen, das Werkzeug gleich am Anfang anzuheben. Und ich denke, das ist auch das Geheimnis, warum wir so hohe Lebensdauer ermöglichen. Und ich denke, für Sie könnte das auch wichtig sein mit Ihren Kunden in der Medizintechnik und Pharmaindustrie.
Guillaume Hopfner: Ja, das ist sogar essenziell. Es hilft, Partikel zu vermeiden, insbesondere im Reinraum. Bei eingelaufenen Flachzentrierungen kann man zudem immer erkennen, dass diese von vorne her verschleissen. Da gebe ich Ihnen absolut recht. Zudem ist es schwierig für uns, einen genauen Zeitpunkt zu definieren, ab wann die Flachzentrierung als verschliessen gelten, denn sie haben ja von Anfang an Spiel.
♦ Folge 5 ♦
Systemführung Plus
Diese Episode thematisiert die Systemführung Plus im dynamischen Einsatz. Doch da stellt sich gleich einmal die Frage: Was ist eine Systemführung Plus?
Die Systemführung Plus wurde erst kürzlich entwickelt. Neben den verschiedenen Feinzentrierungen ist nun diese Systemführung dazugekommen und hat das Formenbau-Portfolio von Agathon komplettiert.
Gemäss dem Agathon-Claim «Führen-Zentrieren-Schnellwechseln» erfüllt die Systemführung Plus gleich zwei Anwendungsfälle. Sie führt einerseits das Werkzeug und zentriert es anderseits auch. Je nach Anforderung kann man demzufolge darauf verzichten, zusätzlich eine Feinzentrierung im Werkzeug einzubringen.
Noch sind Gleitführungen, welche in den Ecken von einem Formaufbau montiert werden, der Stand der Technik. Diese Gleitführungen haben allerdings nur die Aufgabe, vorzuzentrieren – also das Werkzeug grob auszuzentrieren. Normalerweise werden die Werkzeughälften auf circa fünf Hundertstel genau vorzentriert. Im Gegensatz zur Systemführung Plus muss man mit dieser gleitenden Führung zwingend im Werkzeug eine Feinzentrierung vorsehen.
Vorteile der Systemführung Plus an mehreren Stellen kombinieren
Doch wie werden solche Systemführungen von Agathon sonst noch angewendet? Das erklärt auch hier wieder Guillaume Hopfner im Gespräch mit Stefan Nobs.
Guillaume Hopfner: Die Systemführung Plus haben wir bei Braunform im Jahr 2021 zum ersten Mal eingesetzt, und zwar bei einem Multikavitäten-Werkzeug (48-fach) für einen medizinischen Artikel. Die Formplatte DS hebt bei der Werkzeugöffnung ab, um die Entformung von einem langen Kern zu unterstützen. Dann geht das Werkzeug komplett auf – und der Artikel wird über Auswerfer entformt.
Bei diesem Führungssystem kombinieren wir die Vorteile an mehreren Stellen. Jede Bewegung erfolgt über eine spielfreie Rollenführung oder Kugelführung. Die erste bei der Abhebung von acht Millimetern; die zweite, wenn das Werkzeug schliesst. Hier kommt auf der Auswerferseite die Kugelführungseinheit zum Einsatz.
Bei solchen Werkzeugen setzen wir normalerweise lange, schwertförmige Führungen ein. Diese stellen wir selbst her und sie benötigen zusätzlichen Platz. Diesen können wir mit der Systemführung Plus einsparen, weil sie an den vier Ecken des Aufbaus platziert sind – so wie ganz normale Hauptführungssysteme.
Platz sparen mit der Systemführung
Stefan Nobs: Wenn ich das Werkzeugkonzept vergleiche mit jener aus der Episode über die Kurzhubanwendung, dann fällt mir auf, dass man wahrscheinlich dort die Kurzhubanwendung hier übernommen hat und diese zweite Führung zugleich auf diese Hauptführung genommen hatte. Habe ich das richtig interpretiert?
Guillaume Hopfner: Ja, wir sparen Platz, da kein separates Führungssystem benötigen wird. Agathon hat hier Systemintegration betrieben, die uns zugutekommt. Ohne die Baureihe Systemführung Plus hätten wir für jede Bewegung ein separates Führungssystem einsetzen müssen.
Ja, wir sparen Platz, da kein separates Führungssystem benötigen wird. Agathon hat hier Systemintegration betrieben, die uns zugutekommt.
Vorteile der Systemführung Plus an mehreren Stellen kombinieren
Doch wie werden solche Systemführungen von Agathon sonst noch angewendet? Das erklärt auch hier wieder Guillaume Hopfner im Gespräch mit Stefan Nobs.
Guillaume Hopfner: Die Systemführung Plus haben wir bei Braunform im Jahr 2021 zum ersten Mal eingesetzt, und zwar bei einem Multikavitäten-Werkzeug (48-fach) für einen medizinischen Artikel. Die Formplatte DS hebt bei der Werkzeugöffnung ab, um die Entformung von einem langen Kern zu unterstützen. Dann geht das Werkzeug komplett auf – und der Artikel wird über Auswerfer entformt.
Bei diesem Führungssystem kombinieren wir die Vorteile an mehreren Stellen. Jede Bewegung erfolgt über eine spielfreie Rollenführung oder Kugelführung. Die erste bei der Abhebung von acht Millimetern; die zweite, wenn das Werkzeug schliesst. Hier kommt auf der Auswerferseite die Kugelführungseinheit zum Einsatz.
Bei solchen Werkzeugen setzen wir normalerweise lange, schwertförmige Führungen ein. Diese stellen wir selbst her und sie benötigen zusätzlichen Platz. Diesen können wir mit der Systemführung Plus einsparen, weil sie an den vier Ecken des Aufbaus platziert sind – so wie ganz normale Hauptführungssysteme.
Platz sparen mit der Systemführung
Stefan Nobs: Wenn ich das Werkzeugkonzept vergleiche mit jener aus der Episode über die Kurzhubanwendung, dann fällt mir auf, dass man wahrscheinlich dort die Kurzhubanwendung hier übernommen hat und diese zweite Führung zugleich auf diese Hauptführung genommen hatte. Habe ich das richtig interpretiert?
Guillaume Hopfner: Ja, wir sparen Platz, da kein separates Führungssystem benötigen wird. Agathon hat hier Systemintegration betrieben, die uns zugutekommt. Ohne die Baureihe Systemführung Plus hätten wir für jede Bewegung ein separates Führungssystem einsetzen müssen.
Ja, wir sparen Platz, da kein separates Führungssystem benötigen wird. Agathon hat hier Systemintegration betrieben, die uns zugutekommt.
Stefan Nobs: Wie sind Sie mit der Passung umgegangen? Wir liefern die Säulen und die Buchsen mit einer sehr präzisen H4-Toleranz. Oft setzt man als Aufnahmebohrungen H7 ein. Wir empfehlen aber H5, damit man ziemlich beinahe spielfrei einbauen kann.
Guillaume Hopfner: Wir sind dieser Empfehlung gefolgt. Wenn spielfreie Systeme eingesetzt werden, muss auf jeden Fall die Aufnahme sehr genau bearbeitet werden.
Eine Toleranz von H5 ist auf jeden Fall zu empfehlen. Was uns aber aufgefallen ist, ist die perfekte Zylindrizität der Säule. Trotz der sehr engen Passung kann die Säule in der Bohrung sehr leicht gedreht werden: ohne zu wackeln, ohne Spiel.
Stefan Nobs: Ja, da kann ich Ihnen nur zustimmen. Je präziser die Aufnahmebohrung ausgeführt ist, desto höher ist der Nutzen, den man dann von der eingebauten, spielfreien Agathon-Führung hat.
Guillaume Hopfner | Leiter Entwicklung und Konstruktion bei der Braunform GmbH
Stefan Nobs | Head of Product Management & Business Development
Stefan Nobs, Head of Product Management & Business Development bei Agathon AG, sammelte als Konstrukteur von Feinschneidwerkzeugen in den 90er-Jahren bereits erste Erfahrungen im Werkzeugbau. Sein grosses Steckenpferd ist die spanabhebende Präzisionsfertigung, denn in verschiedenen Positionen hat er hierzu verschiedene Produktionsmethoden und Werkstoffe sowie die Programmierung und Prüfung kennengelernt – unter anderem während eines Auslandsarbeitsaufenthaltes in den USA. Stefan Nobs ist seit November 2001 bei Agathon im Bereich Normalien tätig. In den Nullerjahren erkannte die Agathon Normalien den Trend in Bezug auf mehr Präzision und Laufleistung im Formenbau und erschuf deshalb die Feinzentrierung Plus. In den 10er-Jahren entwickelte das Unternehmen ihre Normreihen stetig weiter, um ein abgerundetes Produktportfolio und eine fokussierte Geschäftsfeldentwicklung im Formenbau/Spritzgiessen zu gewährleisten. Als Verfechter und Förderer für spielfreie und abwälzende Führungs- und Zentriersysteme für den Formenbau ist Stefan Nobs aktuell auch im Aachen Center of Optics Production (ACOP) an Projekten zu Hochleistungsspritzgiesswerkzeugen aktiv.
♦ Folge 6 ♦
Feinzentrierung Plus statisch
Setzen Sie noch Stiftverbindungen ein? Dann räumen Sie den Hammer weg, denn diese Folge von Agatalk sollten Sie sich nicht entgehen lassen! Sie behandelt die Feinzentrierung Plus im statischen Anwendungsfall.
Setzen Sie noch Stiftverbindungen ein? Dann räumen Sie den Hammer weg, denn diese Folge von Agatalk sollten Sie sich nicht entgehen lassen! Sie behandelt die Feinzentrierung Plus im statischen Anwendungsfall. Die Feinzentrierung Plus kann man nämlich ähnlich einsetzen wie eine Stiftverbindung. Als Verbindungselement dient dann die Feinzentrierung Plus und die Platten werden fix miteinander verbaut, was nach Agathon Terminologie eine «statische Anwendung» ist.
Diese statischen Anwendungen haben meist mehrere Hundert Zyklen; je nachdem, wie oft man die Platte demontiert und wieder montiert. Der Vorteil ist folgender: Beim Montieren hat man einen geführten Weg – und zwar ein paar Millimeter, auf denen die Wälzkörper abwälzen. Die Platte ist dann bereits absolut spielfrei auszentriert. Das also ist der grosse Vorteil gegenüber einer simplen Stiftverbindung, bei der die Platte oft verkantet und die Platte nicht nach hinten rutschen will. Es kann dann sogar sein, dass man den Hammer zur Hand nehmen muss.
Natürlich ist eine Bohrung für die Stiftverbindung sehr günstig herzustellen. Doch vergessen geht, dass die Platte im Innern wichtige Funktionen hat. Sie ist dort auch teuer veredelt und diese teure Veredelung kann man eben mit der Feinzentrierung Plus wie auch mit der Mini-Feinzentrierung ausgesprochen gut schützen.
Das sind auch die für diesen Anwendungsfall einsetzbaren Normreihen: die Feinzentrierung Plus und die Mini-Feinzentrierung. Wenn man sehr wenig Platz hat, kann man bei der Mini-Feinzentrierung sogar die Buchse weglassen – so hat man eine noch platzsparendere Lösung.
Im folgenden Gespräch geht es um eine interessante Anwendung, bei der die Feinzentrierung Plus eingesetzt wird und auch die Mini-Feinzentrierung. Wiederum diskutieren Guillaume Hopfner und Stefan Nobs.
Guillaume Hopfner: Wir haben eine Anwendung, bei der es keine zyklusabhängigen Bewegungen gibt – deshalb statisch. Auf der Düsenseite des Werkzeugs haben wir oft eine heisse Seite, in dem das Heisskanalsystem eingebaut ist und die Düsen überstehen. Je nach Fachzahl des Werkzeugs – achtundvierzig oder sechsundneunzig – stehen dann auch viele Düsen über. Alles in allem also eine kostspielige Anwendung. Um schnelleren Zugang zu den Düsen zu schaffen, zieht man die Kavitätenplatte von dieser heissen Seite ab und setzt sie nach der Bearbeitung wieder auf.
Bei diesem Montage- und Demontagevorgang müssen beide Teile sehr genau aufeinandertreffen. Im Düsensitz hat man gewöhnlich unter einem 1/100stel-Millimeter Spiel. Durch diese Passung wird der Heisskanal abgedichtet. Die Kavitätenplatte wird über eine normale Führungssäule zuerst grob zentriert. Wenn wir dann die Platte montieren, greifen dann auf den letzten acht Millimetern die spielfreien Feinzentrierungen, um die Vorkammerpassung der Düsen zu schützen.
Stefan Nobs: Das ist eine interessante Anwendung, die Sie geschildert haben. Denn ich denke, oft wird hier eine Stiftverbindung eingesetzt, weil eine Feinzentrierung Plus natürlich kostenintensiver ist. Oder vielleicht scheint es auch, dass eine Lösung mit einer Feinzentrierung «overengineered» ist. Wie beurteilen Sie das in diesem spezifischen Anwendungsfall?
Guillaume Hopfner: Ich glaube nicht. Aber, ob etwas «overengineered» ist, lässt sich nur in der Praxis prüfen. Man muss sich aber eines vorstellen: Wenn eine solche Platte montiert wird, die um die hundert Kilogramm wiegt, dann muss sie mit einem Kran montiert werden. Wegen der Ungenauigkeit der Bearbeitung oder des Passungsspiels der Stifte kann es aber bei der Verwendung von Zylinderstiften leicht zu Widerstand kommen, wenn die Stifte eingreifen müssen.
Mit der Feinzentrierung erfolgt eine spielfreie Passung ohne Widerstand durch die abwälzenden Rollenwälzkörper. Das heisst, man kann ganz leicht über der Vorkammerpassung montieren. Diese Anforderung übrigens, die Platte zu demontieren, steht oft im Pflichtenheft unserer Kunden. Da kommt ein Hinweis, dass der Kunde zum Beispiel einen Farbwechsel benötigt während der Produktion. Es kann sogar mehrmals in der Woche vorkommen, dass man dann die Platte herunterziehen muss.
Stefan Nobs: Und dann bleibt das Werkzeug auf der Presse?
Guillaume Hopfner: Es gibt beide Möglichkeiten: Entweder demontiert man die Formplatte und zieht diese über die Auswerferseite – mit der Maschine auf der anderen Seite, sodass man dann Zugang zu den Düsen bekommt. Oder man zieht dann das Werkzeug von der Maschine runter und zieht dann die Platte hoch.
Im folgenden Gespräch geht es um eine interessante Anwendung, bei der die Feinzentrierung Plus eingesetzt wird und auch die Mini-Feinzentrierung. Wiederum diskutieren Guillaume Hopfner und Stefan Nobs.
Guillaume Hopfner: Wir haben eine Anwendung, bei der es keine zyklusabhängigen Bewegungen gibt – deshalb statisch. Auf der Düsenseite des Werkzeugs haben wir oft eine heisse Seite, in dem das Heisskanalsystem eingebaut ist und die Düsen überstehen. Je nach Fachzahl des Werkzeugs – achtundvierzig oder sechsundneunzig – stehen dann auch viele Düsen über. Alles in allem also eine kostspielige Anwendung. Um schnelleren Zugang zu den Düsen zu schaffen, zieht man die Kavitätenplatte von dieser heissen Seite ab und setzt sie nach der Bearbeitung wieder auf.
Bei diesem Montage- und Demontagevorgang müssen beide Teile sehr genau aufeinandertreffen. Im Düsensitz hat man gewöhnlich unter einem 1/100stel-Millimeter Spiel. Durch diese Passung wird der Heisskanal abgedichtet. Die Kavitätenplatte wird über eine normale Führungssäule zuerst grob zentriert. Wenn wir dann die Platte montieren, greifen dann auf den letzten acht Millimetern die spielfreien Feinzentrierungen, um die Vorkammerpassung der Düsen zu schützen.
Stefan Nobs: Das ist eine interessante Anwendung, die Sie geschildert haben. Denn ich denke, oft wird hier eine Stiftverbindung eingesetzt, weil eine Feinzentrierung Plus natürlich kostenintensiver ist. Oder vielleicht scheint es auch, dass eine Lösung mit einer Feinzentrierung «overengineered» ist. Wie beurteilen Sie das in diesem spezifischen Anwendungsfall?
Guillaume Hopfner: Ich glaube nicht. Aber, ob etwas «overengineered» ist, lässt sich nur in der Praxis prüfen. Man muss sich aber eines vorstellen: Wenn eine solche Platte montiert wird, die um die hundert Kilogramm wiegt, dann muss sie mit einem Kran montiert werden. Wegen der Ungenauigkeit der Bearbeitung oder des Passungsspiels der Stifte kann es aber bei der Verwendung von Zylinderstiften leicht zu Widerstand kommen, wenn die Stifte eingreifen müssen.
Mit der Feinzentrierung erfolgt eine spielfreie Passung ohne Widerstand durch die abwälzenden Rollenwälzkörper. Das heisst, man kann ganz leicht über der Vorkammerpassung montieren. Diese Anforderung übrigens, die Platte zu demontieren, steht oft im Pflichtenheft unserer Kunden. Da kommt ein Hinweis, dass der Kunde zum Beispiel einen Farbwechsel benötigt während der Produktion. Es kann sogar mehrmals in der Woche vorkommen, dass man dann die Platte herunterziehen muss.
Stefan Nobs: Und dann bleibt das Werkzeug auf der Presse?
Guillaume Hopfner: Es gibt beide Möglichkeiten: Entweder demontiert man die Formplatte und zieht diese über die Auswerferseite – mit der Maschine auf der anderen Seite, sodass man dann Zugang zu den Düsen bekommt. Oder man zieht dann das Werkzeug von der Maschine runter und zieht dann die Platte hoch.
Rollt ab und verkantet nicht
Stefan Nobs: Kostensparender ist es natürlich, wenn das Werkzeug auf der Presse bleibt und man die Platte dann eben mit Wälzkörpern abwälzend demontieren und wieder montieren kann.
Guillaume Hopfner: Ja. Und im Moment, wenn die Platte auf der Auswerferseite hängt, hängt sie nur noch in den Hauptführungssäulen. Diese haben auch Spiel; in der Buchsenpassung zwischen der Säule und der Buchse und dann in der Säulenpassung. Und damit kann sie auch leicht abgesetzt hängen zur Düsenplatte. Und wenn das Werkzeug wieder zusammenfährt, wird dieser Versatz von der Feinzentrierung aufgenommen.
Stefan Nobs: Für mich ist das beeindruckend, wenn man sich diese träge Masse vorstellt. Eine hundert Kilogramm schwere Platte hängt am Kran und jemand versucht, diese Platte sehr präzise auf eine Stiftverbindung zu montieren! Das ist definitiv eine Herausforderung, diese Masse punktgenau auf den Stift zu manövrieren. Dann ist es schon ein grosser Vorteil, wenn man einen Wälzkörper dazwischen hat, der sofort abrollt und nicht verkantet. Da kann ich nachvollziehen, dass Sie in dieser Anwendung einen grossen Kundennutzen sehen.
Auf die Idee mit einer Feinzentrierung kommen Sie also unter anderem, wenn Sie sehen, dass ein Farbwechsel benötigt wird. Dann ist dies ein Hinweis, um eine solche Lösung anzustreben.
Aber wir reden von ein paar Mikrometern und dann haben wir den Vorteil, wenn die Zentrierung schon in dieser Genauigkeit daherkommt.
Guillaume Hopfner: Das ist so. Wir bekommen aber auch aus der eigenen Produktion oft Feedback – teilweise bereits bei der Werkzeugbemusterung. Vor allem dann natürlich, wenn die Genauigkeit oder die Montage damit erleichtert würden mit einer eingesetzten Feinzentrierung.
Stefan Nobs: Bei der Anforderung zu dieser Anwendung habe ich gesehen, dass die Düsenspitzen eine Übergangspassung haben: null minus und die Bohrung hat null plus. Im Extremfall kann das quasi null auf null sein. Ich denke, das ist auch der Grund, warum sie in diesem Fall diese spielfreien Zentrierungen eingesetzt haben, oder?
Guillaume Hopfner: Richtig, da ist die Passungsgenauigkeit unter einem Hundertstel. Auf null bleibt es gewöhnlich nicht lang. Aber wir reden von ein paar Mikrometern und dann haben wir den Vorteil, wenn die Zentrierung schon in dieser Genauigkeit daherkommt.
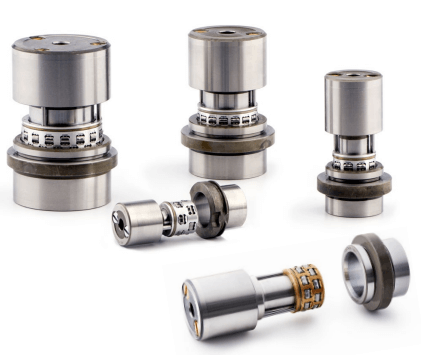
Stefan Nobs: Ich denke, Sie haben sehr hohe Kosten, um diese Platten herzustellen und dann noch einmal, wenn sie die Düsennadeln einkaufen und auf dem Werkzeug montieren. Wir sprechen da wahrscheinlich auch von mehreren Tausend Franken. Diese stehen dann den Kosten einer Feinzentrierung gegenüber. Dann erscheint diese Investition klein, um das alles zu schützen.
Guillaume Hopfner: Ja, denn jede Düse kostet mehrere tausend Euro und wenn man mehrere im Werkzeug verbaut, ist der Preis einer Zentrierung nebensächlich.
Stefan Nobs: Wie sieht es auf der konstruktiven Seite aus? Wir haben einen Zentrierweg von 14 Millimeter aufwärts. Korrespondiert das mit den Anforderungen, die sie haben?
Guillaume Hopfner: Davor habe ich von 8 Millimetern gesprochen – und das ist bereits ausreichend. Eine Vorkammerpassung ist gewöhnlich maximal 2 Millimeter lang. Das heisst, man braucht gar nicht so lang zu führen. Aber wenn es schon vorzentriert ist, bevor es eingreift, ist es sicherer.
Stefan Nobs: Noch ein paar Worte zum Einbauraum: Wie sieht es da aus? Bei der Durchsicht dieser Konstruktion habe ich gesehen, dass sie die 15er-Zentrierung eingesetzt haben. Und die hat einen Aufnahmedurchmesser von achtundzwanzig Millimeter. Es scheint, als hätten Sie da viel Platz, um eine Zentrierung zu montieren. Haben Sie auch noch Bedürfnisse, eine Mini-Feinzentrierung einzubauen? Oder ist das weniger ein Anwendungsfall für eine Mini-Feinzentrierung?
Guillaume Hopfner: Doch, das haben wir auch schon gemacht. Es gibt nicht immer komplette Formplatten, die auf Düsenplatten montiert werden. Manchmal werden einzelne Kavitäten-Einheiten demontiert. Und da kann man diese dann genauso wie die grosse Platte direkt auf der Maschine herunternehmen.
Stefan Nobs: Die kann man also einhändig abziehen und wieder montieren.
Guillaume Hopfner: Ja. Und dann muss man diese aber wieder über die Düse positionieren. Und da es von Hand montiert wird, benötigt man auch eine Feinzentrierung, um den Vorkammerbereich zu schützen. Da ist die Mini-Feinzentrierung sehr wichtig, weil im Kavitäten- oder im Inselbereich nicht viel Platz zur Verfügung steht.
Das war die vorerst letzte Episode dieser Podcast-Staffel 1 für den Formenbau. Folgen Sie uns auf Linkedin - und erfahren Sie, sobald eine neue Staffel folgen wird.
>>> Weitere Folgen werden kontinuierlich aufgeschaltet. Erscheinungsdaten siehe Landingpage Agatalk - Gespräche über Normalien
Impressum
Textquelle: Agathon und Technik und Wissen
Bildquelle: Agathon
Redaktionelle Bearbeitung: Technik und Wissen
Eine Publikation von Technik und Wissen
Informationen
Agathon
www.agathon.ch
Weitere Artikel
Veröffentlicht am: