Gedruckte Werkzeuge und Formen für Faserverbunde
3D-Druck als disruptive Technologie
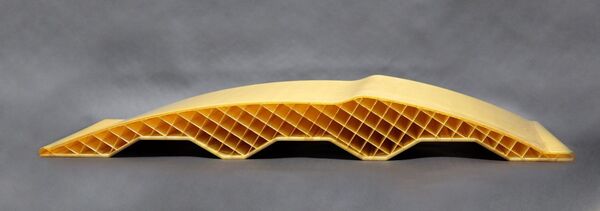
Gedruckte Werkzeuge und Formen für Faserverbunde
3D-Druck als disruptive Technologie
Grosses Composite-Layup-Werkzeug für einen Dassault Falcon Jet. Gedruckt auf einem Stratasys 900mc Acceleration Kit mit dem Material ULTEM 1010.
Das traditionelle Fertigungsverfahren im Composite-Werkzeugbau ist als extrem langwieriger und kostspieliger Prozess bekannt. Inwiefern könnte die additive Fertigung eine günstigere Alternative darstellen? Mit dieser Thematik hat sich Tim Schniepp, Senior Director Composite Solutions bei Stratasys, befasst.
Vor nicht allzu langer Zeit war die Herstellung von Composite-Bauteilen ein sehr kostspieliger, mühsamer und ineffizienter Prozess. Ich spreche von der Zeit, in der Hersteller von Verbundkonstruktionen, OEMs und Werkzeuglieferanten kaum eine Alternative hatten, als sich mit traditionellen Verfahren und den damit verbundenen Einschränkungen auseinanderzusetzen. Eine Zeit, in der Hersteller für die Werkzeugfertigung traditionelle Materialien wie Aluminium, Stahl, Invar oder teures FRP (faserverstärktes Polymer) verwenden mussten, was lange Vorlaufzeiten von mehreren Wochen oder – bei grösseren, komplexeren Werkzeugen – vielen Monaten bedeutete.
Das hatte damals zur Folge, dass selbst bei relativ einfachen Werkzeugformen die Kosten oft in fünfstellige Höhen schnellten. Letztlich beeinträchtigte dies den Zeitplan der gesamten Entwicklungsprogramme und verhinderte sowohl Designoptimierungen als auch Produktinnovationen, ausserdem waren die daraus resultierenden Werkzeuge schwer, schwierig in der Handhabung und Lagerung.
Sie können sich vorstellen, was das für ein Albtraum war. Natürlich ist dieses Szenario für viele Unternehmen noch immer Realität und erklärt zum Teil, warum die Flugzeugkosten nach wie vor so hoch sind und Composite-Bauteile so teuer sein können.
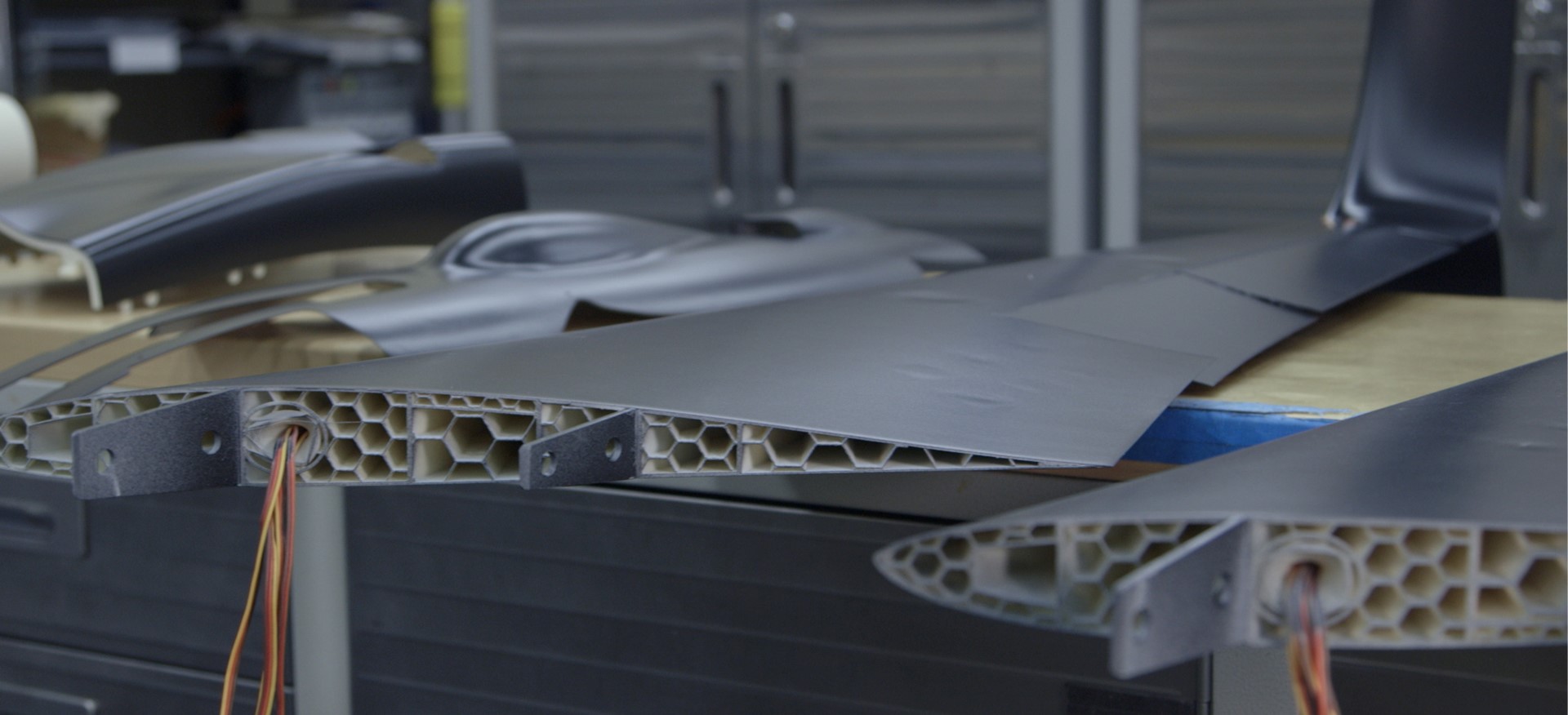
Teure Lagerung von Werkzeugen
Bei einem Flugzeughersteller kann je nach Programm eine Handvoll Composite-Bauteile ausreichen, da nicht unbedingt Bedarf an einer hohen Stückzahl besteht. Es gibt beispielsweise nur ein paar hundert F-22-Kampfflugzeuge auf der Welt, aber die Investition in Werkzeuge - sowohl zeitlich als auch finanziell - für den Hersteller oder OEM ist unglaublich wichtig, um eine relativ geringe Anzahl von Teilen zu produzieren.
Hinzu kommt, dass diese Werkzeuge über Jahre hinweg gelagert werden müssen, um Ersatzteile herstellen zu können. Wir sind auf ein Unternehmen gestossen, das seine Werkzeuge auf einem ungenutzten Parkplatz hinter seiner Produktionsstätte lagert, weil es keine andere Möglichkeit hat, derart grosse, sperrige Objekte aufzubewahren. Im schlimmsten Fall investieren Unternehmen mehr als ein Jahr an Zeit und sechsstellige Summen in eine sehr grosse, komplexe Laminierform, die sie vielleicht nur wenige Male verwenden.
Dabei darf nicht vergessen werden, was passiert, wenn sich die Konstruktionsvorgaben für solche Werkzeuge als ungenau herausstellen oder Änderungen erfordern. Nachdem ich für einen weltweit führenden Hersteller an der Konstruktion und Produktion von Verkleidungen (Gondeln) für Flugzeugtriebwerke gearbeitet hatte, habe ich Programme erlebt, bei denen das Werkzeugdesign bereits 12 bis 14 Monate im Voraus feststehen musste. Eine signifikante Konstruktionsänderung kann dann ziemlich dramatische Auswirkungen haben, weil sie kostspielige, zeitaufwändige Modifikationen am Werkzeug erfordert und so zu erheblichen Verzögerungen bei der Lieferung von Strukturen und damit der Herstellung von Flugzeugen führt.
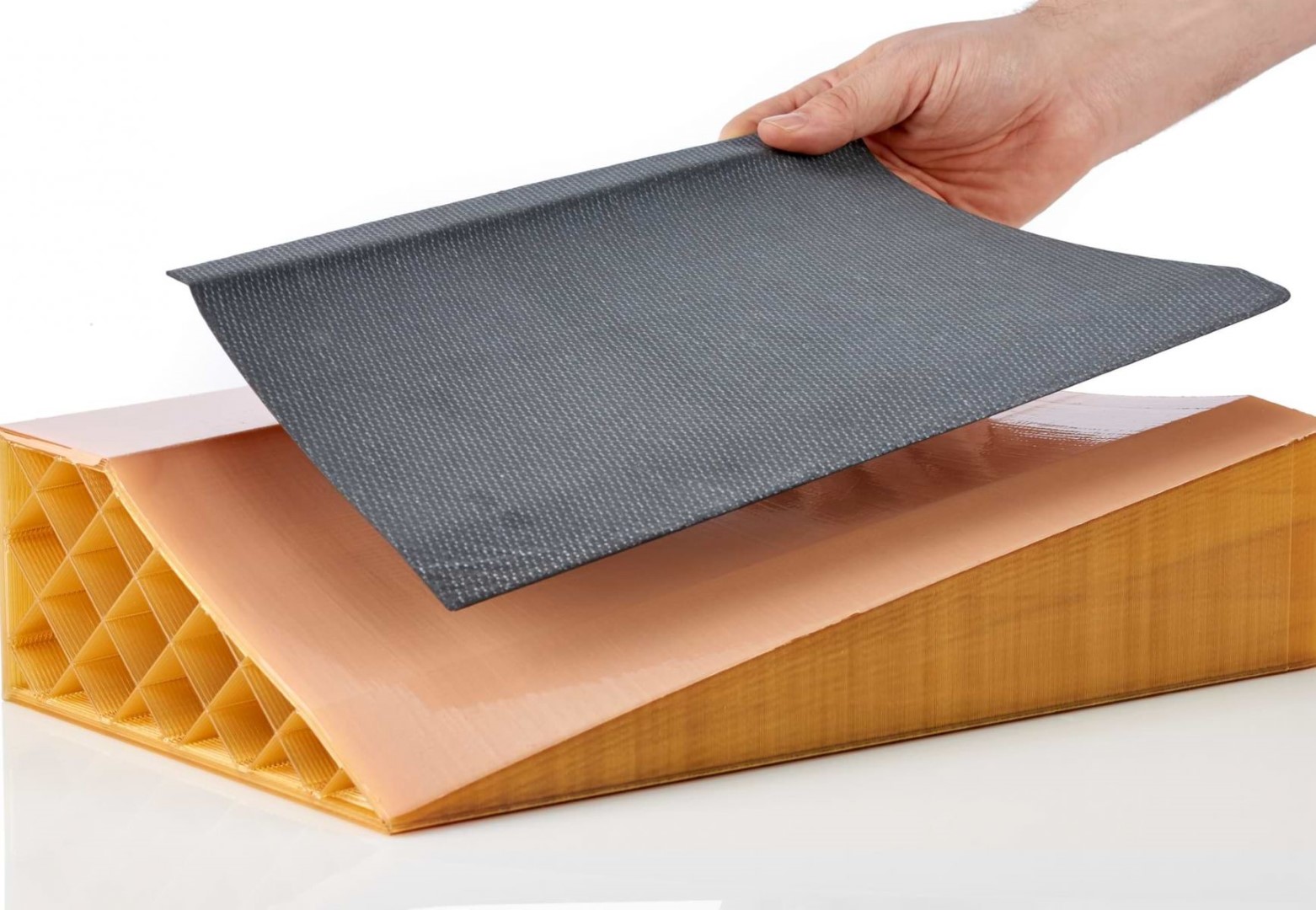
3D-Druck für Composite-Werkzeuge
Es muss jedoch nicht zwingend so sein. Für eine wachsende Zahl von zukunftsorientierten, versierten Herstellern ist das auch nicht mehr der Fall. Die fortschrittliche Composite-Branche hat seit jeher Bedarf an innovativen Werkzeuglösungen. Eine sich schnell verbreitende Technologie ist in diesem Zusammenhang zweifelsohne der 3D-Druck. Einige OEMs und führende Zulieferer in der Luft- und Raumfahrtindustrie setzen die additive Fertigung bereits seit vielen Jahren für die schnelle Herstellung von kostengünstigen Composite-Werkzeugen ein. Obwohl es eine Vielzahl von additiven Fertigungstechnologien gibt, liegt der wichtigste und relevanteste Schwerpunkt auf extrusionsbasierten Technologien.
Eine solche Lösung ist die 3D-Drucktechnologie FDM (Fused Deposition Modeling), bei der Bauteile Schicht für Schicht durch hochgradig kontrollierte und automatisierte Erwärmung und Extrusion von thermoplastischen Materialien hergestellt werden. FDM ermöglicht die schnelle Herstellung von hocheffektiven Composite-Werkzeugformen für eine breite Palette von Werkzeuggrössen und -typen, die bei Aushärtungstemperaturen von über 180°C in typischen Autoklavenzyklen (Konsolidierungsdrücke über 0,7 MPa) eingesetzt werden können.
Grosse und komplexe Strukturen
Boeing hat 2012 den Einsatz von FDM-Technologie für das Composite-Tooling im Rahmen einer technischen Publikation der SAMPE (Society for the Advancement of Materials and Process Engineering) bekannt gegeben und beschreibt darin seine Entwicklungsbemühungen in Bezug auf grosse, komplexe, ausserhalb des Autoklaven ausgehärtete Strukturen.
Um den Anforderungen von Laminierformen gerecht zu werden, haben wir uns bemüht, die 3D-Druckfunktionen und Materialeigenschaften von Stratasys-Produkten - insbesondere die Temperaturbeständigkeit - zu verbessern, und so das 3D-Druck-Angebot für Composite Werkzeuge und Vorrichtungen zu erweitern.
Doch auch Flugzeugkomponenten werden auch direkt gedruckt, wie das Beispiel von Aurora Flight Sciences zeigt. Das Unternehmen hat vor zwei Jahren seine erste 3D-gedruckte Drohne gebaut und dabei das Potenzial der Technologie vorteilhaft genutzt: Die Konstruktions- und Bauzeit konnte im Vergleich zu einer herkömmlichen Drohne um die Hälfte verkürzt werden. Die Drohne mit einer Spannweite von drei Metern wurde zu 80 Prozent im 3D-Druck mit Leichtbaumaterialien von Stratasys gefertigt - dadurch erreicht das Flugobjekt Geschwindigkeiten von rund 240 Stundenkilometern.
Beträchtliche Materialfortschritte
Stratasys hat massiv in die Bereitstellung von 3D-Drucklösungen investiert, die auf die spezifischen Anforderungen der Composite-Werkzeuge zugeschnitten sind. Durch die Einführung des Hochtemperatur-Thermoplastes ULTEM 1010 von Stratasys und einer zweifach höheren Durchsatzleistung mittels des F900 Acceleration Kits ermöglicht es den Kunden der FDM 3D-Drucktechnologie, die Lieferkette der Composite-Werkzeuge signifikant zu beeinflussen. Dieser Bereich erfährt zudem fortwährend neue Investitionen, da derzeit neue Funktionen und leistungsstarke, auf die Werkzeugproduktion ausgerichtete Materialien entwickelt werden, die für kurzfristige Markteinführungen bestimmt sind.
Die Entwicklung von Stratasys' Hochtemperatur-Materialien sowie der erhöhte Durchsatz seiner 3D-Drucker ermöglichen die Herstellung von Hochtemperatur-Schichtwerkzeugen innerhalb von Stunden oder Tagen. Bisher waren es Wochen oder Monaten, die für die Herstellung und Beschaffung erforderlich waren. Darüber hinaus können 3D-gedruckte Werkzeuge im Vergleich zu traditionellen Werkzeugmaterialien erheblichen Kosteneinsparungen erzielen, neben zahlreichen anderen, seltener quantifizierten Vorteilen, wie z.B. drastischen Gewichtseinsparungen. Fallstudien mit Erstausrüstern wie Dassault Falcon Jet, Aurora Flight Sciences und SSL (ehemals Space Systems Loral) veranschaulichen das Potenzial für eine Reduzierung der Kosten und Durchlaufzeiten um mehr als 80 %.
Neuer Rennwagenflügel in knapp zwei Wochen
Ein weiteres aktuelles Beispiel, das die signifikante Zeitersparnis durch dieses Verfahren demonstriert, ist das F1-Rennsportteam und Stratasys-Kunde McLaren-Honda, das in der Grand Prix-Saison 2017 in weniger als zwei Wochen mit FDM-3D-Druck einen neuen Rennwagenflügel produzierte. In diesem Fall fertigte das Team ein ULTEM1010-Formwerkzeug per 3D-Druck, um die Form des Flügels zu erstellen. Da dieses Material den hohen Temperaturen beim Aushärten von Verbundstrukturen standhalten kann, wurde es während des gesamten Aushärtungszyklus zur Herstellung der endgültigen Struktur verwendet. Der Flügel aus Carbonfaser wurde dann aus dem Werkzeug entformt, wodurch das Team ein wiederverwendbares Composite-Schichtwerkzeug zurückbehält.
Der additive Charakter des 3D-Drucks, der dazu führt, dass das Material nur dort platziert wird, wo es benötigt wird, erschafft zudem ganz natürlich einen Prozess mit hoher Effizienz und minimalen Abfallprodukten. Dadurch wird nicht nur der Materialverbrauch, sondern auch das Gewicht der Werkzeuge drastisch reduziert. Diese Optimierung ermöglicht es, dass Werkzeuge vom Anwender direkt gehandhabt werden anstatt mit Kränen oder Hebevorrichtungen, und reduziert auch die thermische Masse des Werkzeugs während des Aushärtungsprozesses. Dadurch werden wiederkehrende Kosten und betriebliche Ineffizienzen weiter reduziert.
Da die Nachfrage nach neuen Anwendungen, Produktverbesserungen und einer schnelleren, kostengünstigeren Werkzeugherstellung weiter zunimmt, sind die Hersteller von Verbundteilen gezwungen, Innovationen zu entwickeln. Damit können sie wettbewerbsfähig bleiben, zumal die Erstanwender dieser Technologie bereits von den Vorteilen des 3D-Drucks in der Werkzeugfertigung profitieren.
Autor
Timothy Schniepp
Senior Director Composite Solutions bei Stratasys
Impressum
Text: Tim Schniepp, Senior Director Composite Solutions bei Stratasys
Bildquelle: Stratasys
Publiziert von Technik und Wissen (lm)
Informationen
Weitere Artikel
Veröffentlicht am: