Vom Trend zum innovativen Zerspanungswerkzeug
Drei Hersteller erklären den Einfluss von Trends auf ihre Werkzeugentwicklung
Vom Trend zum innovativen Zerspanungswerkzeug
Drei Hersteller erklären den Einfluss von Trends auf ihre Werkzeugentwicklung
Welche aktuellen Trends haben einen Einfluss auf die Entwicklungen der Werkzeughersteller und welche innovativen Zerspanungswerkzeuge entstehen daraus? Fraisa, Horn und Mapal geben Auskunft.
Inhaltsverzeichnis
Wer die ungeheure Auswahl an innovativen Zerspanungswerkzeugen auf dem Markt kennt, der weiss: Die Werkzeughersteller verfolgen nicht einen einzigen Trend, sondern dutzende, wenn nicht sogar hunderte. Zwar gibt es seit jeher ein paar unschlagbare Argumente in der Entwicklung neuer Tools und die heissen: höhere Produktivität, reduzierte Kosten und hohe Verfügbarkeit. An diesen immerwährenden Trends kommt zwar kein Hersteller vorbei – aber danach ist die Ausrichtung weit offen. Wie weit und was sie alles abdecken, lesen Sie hier in den drei Interviews.
Firma: Fraisa
Antwortgeber: Dirk Kammermeier, CTO
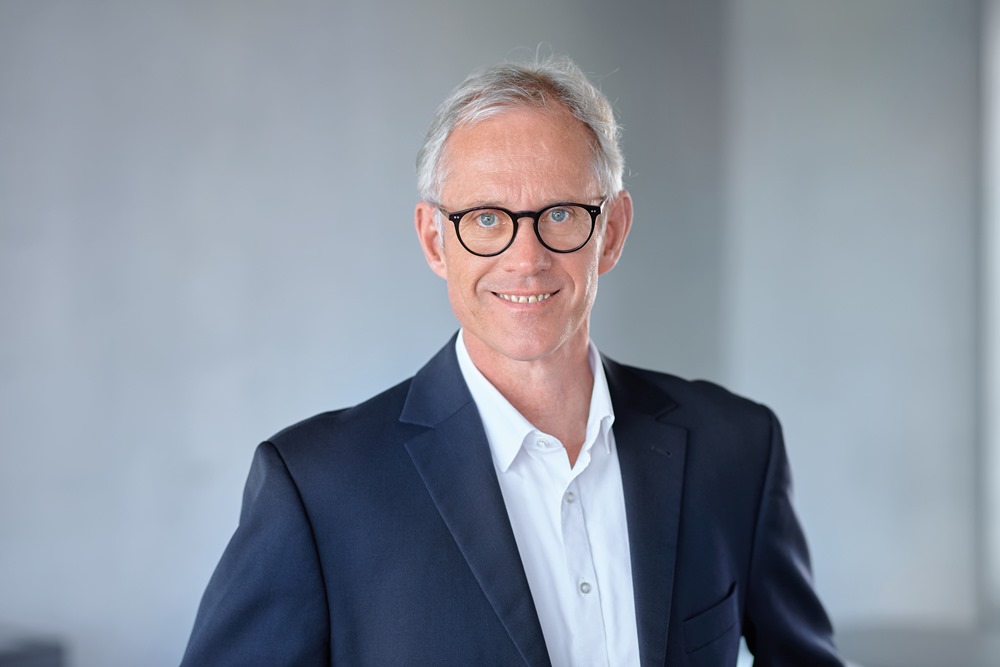
Herr Kammermeier, was sind momentan die grossen Trends, die in Ihre Entwicklung von Werkzeugen einfliessen?
Die grossen Trends der Vergangenheit wie höhere Produktivität, reduzierte Kosten und hohe Verfügbarkeit sind auch in der Zukunft gültig. Allerdings kristallisieren sich ein paar spezifische Details heraus, die die grossen Trends supporten.
So entwickelt die Fraisa seit ein paar Jahren konsequent ihrer MFC-Technologie (Multi Functional Cutting) weiter, die den Anwendern erlaubt, ein Hochleistungswerkzeug für viele Operationen einzusetzen. Das erhöht die Produktivität signifikant, da weniger Werkzeuge gewechselt werden müssen und reduziert Werkzeug- als auch Logistikkosten. Überdies liefert Fraisa für diese Werkzeuge weit über 100’000 erprobte Schnittdaten, sodass bereits das erste Teil schnell und hochproduktiv hergestellt werden kann.
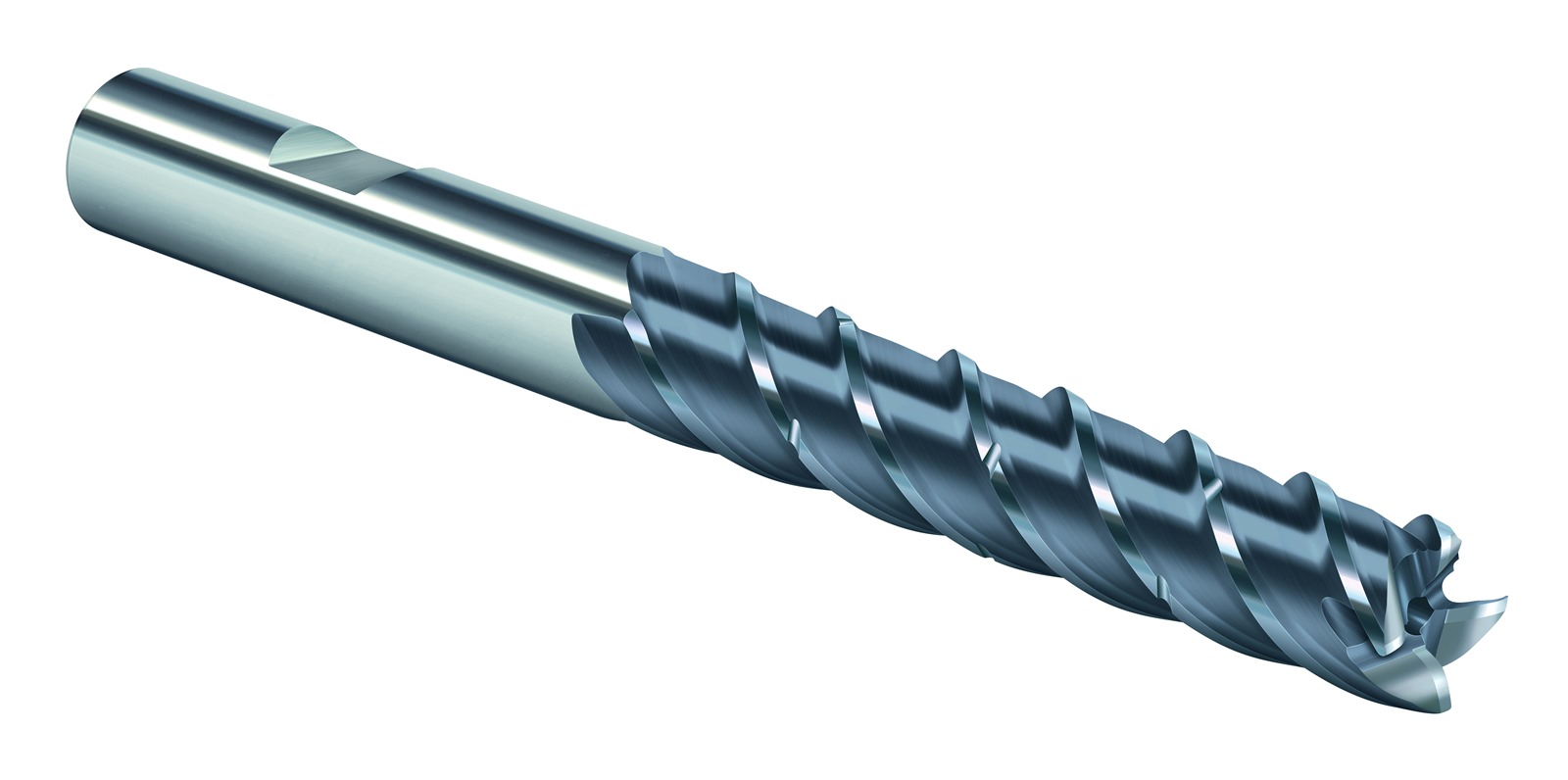
Neben der MFC-Technologie designet Fraisa ihre Werkzeuge auch so, dass diese für HDC-Prozesse (High Dynamic Cutting) eingesetzt werden können. Bei den HDC-Prozessen ist die gesamte Werkzeugschneide im Eingriff, wodurch sich das Belastungskollektiv aus Abrasion, Adhäsion und Temperatur auf einen grossen Schneidenbereich verteilt. Das wiederum führt zu einem deutlich geringeren Werkzeugverschleiss.
Interessant ist dies hauptsächlich für lange Werkzeuge mit grosser Eingriffstiefe. Beim HDC-Prozess führt das Werkzeug neben der Vorschubbewegung und der Drehbewegung des Werkzeugs noch eine Orbitalbewegung um die eigene Drehachse aus.
Hierfür sind hochdynamische CNC-Maschinen notwendig, die sich aber in vielen Bereichen schon im Markt durchgesetzt haben. Durch diese Bewegungsüberlagerung kann sichergestellt werden, dass das Werkzeug immer mit der gleichen Spanungsdicke belastet wird.
Eine gleichmässig konstante Werkzeugbelastung sorgt für eine hohe Prozesssicherheit und lange Standwege. Da beim HDC-Prozess die Werkzeugbelastung präzise eingestellt werden kann, können enorme Zerspanungsleistungen erzielt werden und es eröffnet die Möglichkeit, Werkzeuge mit noch grösseren Schneidenlängen einzusetzen, was ebenfalls einer höheren Produktivität gleichkommt.
Längere Werkzeuge für tiefere Kavitäten dank HDC-Prozess
Sie haben eingangs «die höhere Produktivität, reduzierte Kosten und hohe Verfügbarkeit» als vergangene und gegenwärtige Trends erwähnt. Wie sieht es mit den Losgrössen aus?
Die Losgrössen bei unseren Kunden sinken seit Jahren. Das bedeutet natürlich, dass Agilität und Flexibilität gefragter sind als jemals zuvor – und dies muss geschehen bei gleichzeitiger Verkürzung der Durchlaufzeiten. Genau hier unterstützt Fraisa ihre Kunden mit ihren Technologien.
Durch die MFC-Werkzeuge, die eine Vielzahl an Zerspanungsoperationen bei unterschiedlichen Werkstoffen abdecken, können unsere Kunden viele Werkzeugwechsel vermeiden und Werkzeugmagazinplätze einsparen. Durch die HDC-Prozesse können auch deutlich längere Werkzeuge für tiefere Kavitäten zum Beispiel eingesetzt werden. Auch hier unterstützt Fraisa mit ihrem ToolExpert den Kunden beim Werkzeugeinsatz.
Somit kann der Kunde Bauteilwandungen mit einem Prozess herstellen und muss nicht mit zwei oder drei Überläufen die Wandung bearbeiten, was Zeit kostet und die Qualität schmälert. Beide Prozesse zusammen ermöglichen den Kunden die Maschinen länger autonom laufen zu lassen, was insbesondere in Hochlohnländern wie der Schweiz einen enormen Wettbewerbsvorteil darstellt.
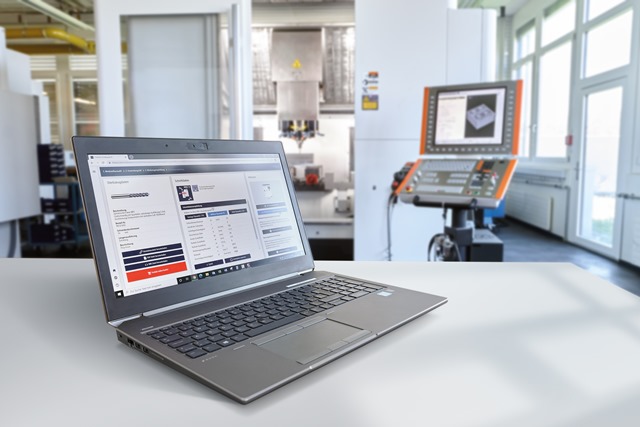
Sie haben diese MFC-Werkzeuge erwähnt, welche die gegenwärtigen Trends unterstützen. Können Sie eines dieser Werkzeuge noch kurz vorstellen?
Die Fraisa bietet schon einige MFC-Werkzeuge an, die mit den erwähnten Features ausgerüstet sind. Besonders hervorheben möchte ich aber den AX-FPS-Schruppfräser, der ein anschauliches Beispiel für die doch recht komplexe Geometrieauslegung für solche Werkzeuge herangezogen werden kann.
Dieses Werkzeug wurde die Aluminiumbearbeitung entwickelt und weist in seiner längsten Standardvariante eine Schneidenlänge von 5,2 × Werkzeugdurchmesser auf. Kunden, die für die Luftfahrtindustrie Aluminium Strukturbauteile herstellen, sind begeistert von der Performance.
Mit diesem Werkzeug kann mit einer Zustellung über die gesamte Eintauchlänge des Werkzeugs extrem hohe Zerspanungsraten unter Einhaltung von engen Bauteiltoleranzwerten erzielt werden.
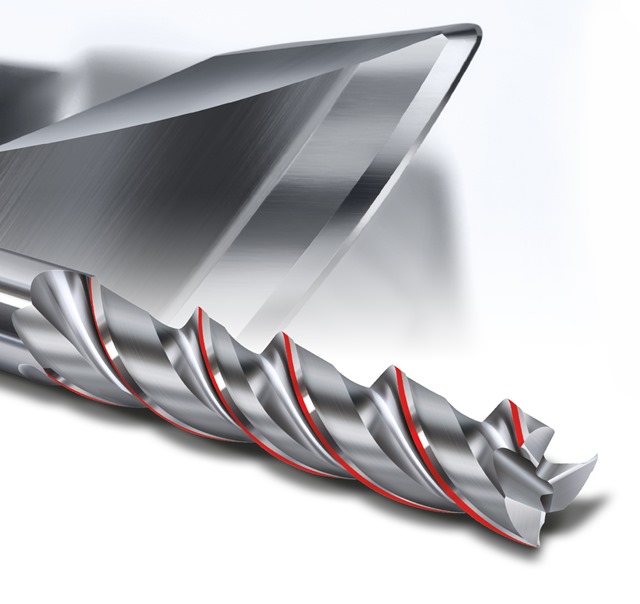
Innovative Stützfasen-Technologie
Was kann dieses Tool und welche technischen Raffinessen stecken dahinter?
Der AX-FPS-Schruppfräser wurde in enger Kooperation mit Fraisa-Kunden entwickelt. Kritische Designmerkmale wurden von der Fraisa patentiert. Eines dieser Merkmale ist die innovative Stützfasen-Technologie, die das Schruppen dünnwandiger, hoher und langer Bauteilwände sowie stabiler Bauteile mit hohen Schnitttiefen und grossen Werkzeugumschlingungen ermöglicht.
Bei diesem Werkzeug sind winzige Stützfasenelemente am Werkzeugumfang angeschliffen, die von der Spitze bis zum Schaft in ihrer Breite abnehmen. Dadurch wird das Werkzeug in Abhängigkeit von der Auskraglänge unterschiedlich gedämpft. In dem Bereich, wo es die grössten radialen Schwingungsamplituden aufweist – das ist der Spitzenbereich des Werkzeugs –, werden die Schwingungen stärker gedämpft als in Bereichen, die näher am Schaft liegen.
Dies ist auch wichtig, da das Werkzeug extrem scharf und leichtschneidend ausgelegt ist, um sehr enge Lagetoleranzen von dünnen Bauteilstegen herzustellen. Hochglanzgeschliffene Spanflächen am Werkzeug unterstützen die Performance der Werkzeuge noch weiter und sorgen für einen schnellen Spanabtransport, um eine beispielhaft hohe Prozesssicherheit zu gewährleisten.
«Geplante Schnittparameter bei dieser Werkzeugauskragung galten als unerreichbar»
Was waren die Herausforderungen, um das Tool zu entwickeln und wie hat man sie gemeistert?
Schaftfräser mit einer Schneidenlänge von 5,2 × Werkzeugdurchmesser, die auf der ganzen Länge eingesetzt werden, neigen bei hohen Zerspanungsleistungen massiv zum Rattern, was die Prozessstabilität stark reduziert. Vor der Entwicklung des AX-FPS-Schruppfräsers galten die vom Kunden geplanten Schnittparameter bei dieser Werkzeugauskragung als unerreichbar. Das Ziel konnte nur durch enge Kooperation mit dem Kunden erreicht werden, an der sich auch viele Marktbegleiter beteiligt hatten. Den technologischen Durchbruch brachte die von der Fraisa patentierte Stützfasentechnologie, die den Schneidenbereich in Abhängigkeit von der Auskraglänge unterschiedlich dämpft. Schneidenbereiche, die weiter von dem Schaft entfernt sind, werden mehr gedämpft als Bereiche, die näher am Schaft liegen. Somit kann das gefährliche Rattern der Werkzeuge bei hohen Zerspanungsraten wirksam unterdrückt werden.
Welche Vorteile bietet das Werkzeug mit dieser Innovation für die Kunden?
Unsere Kunden können mit dem AX-FPS-Schruppfräser sehr prozesssicher auch fragile Kavitäten – unter anderem Strukturbauteile aus Aluminium – mit hohen Zerspanungsraten bearbeiten, was die Beliebtheit der Werkzeuge in der Luftfahrindustrie zeigt. Aber auch im Formenbau finden HDC-Anwendungen mit MFC-Werkzeugen grossen Anklang, da mit wenigen Werkzeugen hochproduktiv und extrem prozesssicher bei niedrigen Kosten produziert werden kann.
Wenn wir den oben genannten Trend anschauen oder dieses Produkt: Welche Weiterentwicklung wird es da noch geben oder könnte es geben?
Die HDC-Technologie in Kombination mit gezielten Dämpfungsflächen an den Schneiden ermöglicht es, das Werkzeug deutlich länger prozesssicher einzusetzen. Schon heute laufen in den Zerspanungslaboren der Fraisa Werkzeuge mit Schneidenlängen, die deutlich über den Faktor 5,2 hinausgehen. Die beste Werkzeug-Technologie nützt jedoch nichts, wenn diese nicht zum Kunden transferiert werden kann. Deshalb entwickelt Fraisa auch Prozesswissen zu den Technologien und transferiert dieses im Rahmen einer Prozessoptimierung mit der Werkzeug-Technologie zum Kunden. Denn ohne umfangreiches Anwendungswissen kann das Potenzial der Hochleistungswerkzeuge nicht voll ausgeschöpft werden.
Firma: Paul Horn
Antwortgeber: Matthias Luik, Leiter Forschung und Entwicklung
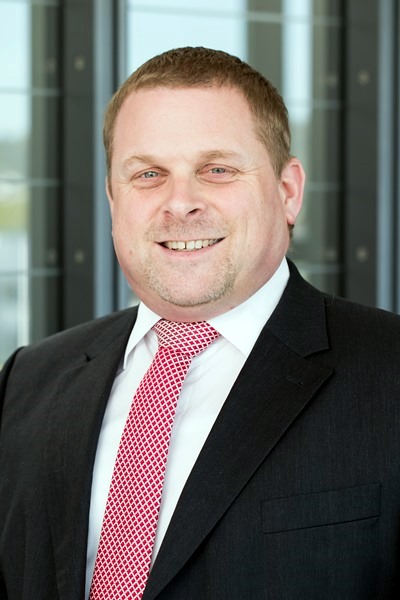
Was sind momentan die grossen Trends, die in Ihre Entwicklung von Werkzeugen einfliessen?
Zum einen zeichnen sich weiterhin digitale Trends ab. Diese haben Schwerpunkte im Bereich künstliche Intelligenz und Sensorik. Blickt man auf die Werkzeugschneide, so liegen etwa schwer zerspanbare Materialien weiterhin im Trend und verlangen nach entsprechenden Werkzeuglösungen.
Welcher scheint ihnen der Wichtigste oder würden Sie besonders hervorheben, weil er bei Ihnen eine grosse Rolle spielt?
Generell gehen die drei genannten Trends einher und haben gemeinsame Ziele: die Optimierung von Zerspanprozessen, die Ausschöpfung von Lebensdauer sowie die Erhöhung von Prozesssicherheit.
Einzigartige Lösung zur Echtzeit-Werkzeugüberwachung von Mikro-Drehbearbeitungen
Gibt es ein Produkt im Portfolio von Paul Horn, das bereits mehrere dieser erwähnten Trends aufgenommen und umgesetzt hat?
Ja. Die Kistler Gruppe – ein Weltmarktführer für dynamische Messtechnik zur Erfassung von Druck, Kraft, Drehmoment und Beschleunigung – hat in enger Zusammenarbeit mit der Paul Horn GmbH eine weltweit einzigartige Lösung zur Echtzeit-Werkzeugüberwachung von Mikro-Drehbearbeitungen entwickelt.
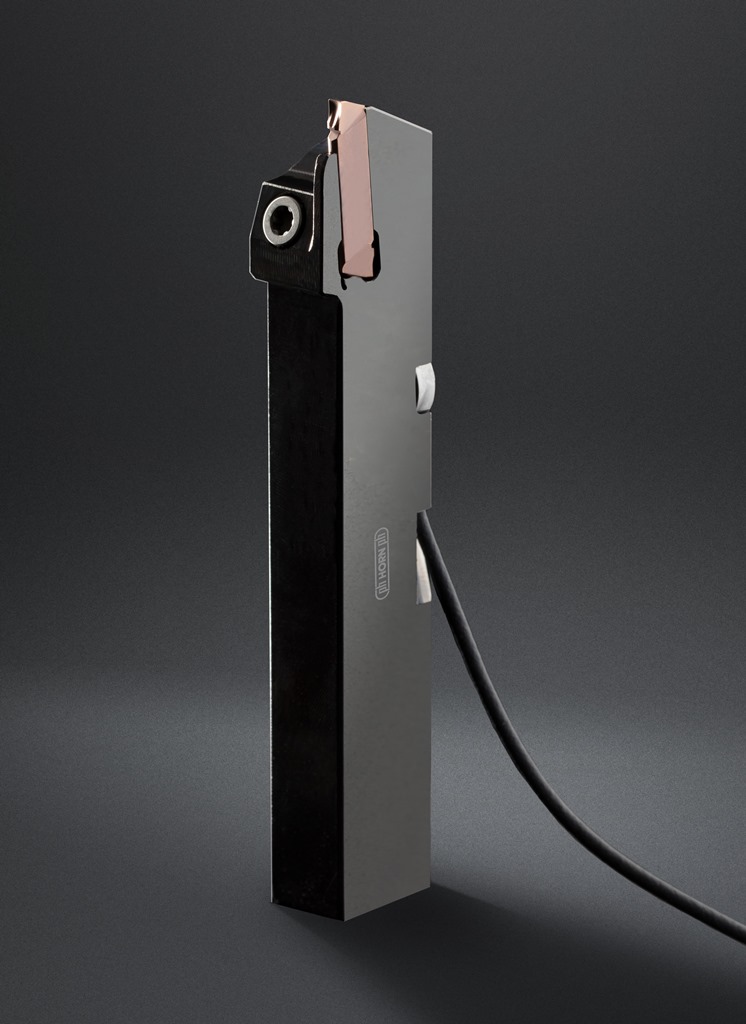
Das Piezo Tool System (PTS) besteht aus einem Kraftsensor, welcher in das Drehwerkzeug eingelegt wird und Aufschluss über den Zustand des Werkzeuges während der Bearbeitung gibt. Der winzige Piezo-Sensor misst selbst niedrigste Zerspankräfte mit hoher Auflösung. Der Maschinenbediener kann so fehlerhafte Materialien und Schneidstoffe oder auch einen Werkzeugbruch sofort erkennen. Die Folge ist ein minimaler Ausschuss bei maximaler Qualität.
Das System eignet sich für den Einsatz bei Drehbearbeitungen speziell im Mikrometerbereich. Hier sind alternative Messmethoden wie die Überwachung der Antriebsleistung des Hauptspindelmotors aufgrund der geringen Abweichungen unergiebig.
Auch eine Messung des Körperschalls liefert bei kleinen Werkstücken keine konstant zufriedenstellenden Ergebnisse. Ein visuelles Überwachen scheidet aufgrund des Einsatzes von Kühlschmierstoffen sowie den hohen Rotationsdrehzahlen beim Bearbeitungsprozess ebenfalls aus.
Die neue Lösung ist kompatibel mit ausgewählten Standard-Drehhaltern von Horn. Sie erfordert keinen Eingriff in die CNC-Steuerung. Der Einsatz erfolgt maschinenunabhängig. Der Austausch der Sensoren geschieht schnell und problemlos. Die Folge eines Einsatzes des Piezo Tool Systems sind eine Reduzierung der Produktionskosten sowie eine Erhöhung der Fertigungskapazitäten.
Ferner arbeitet Horn ständig an Neuentwicklungen in den Bereich Geometrie, Substrat und Beschichtung wie den Sorten IG oder SG.
Was waren die Herausforderungen, um das Piezo Tool System zu entwickeln und wie hat man sie gemeistert?
Bei unserem PTS-System waren hauptsächlich die Unterbringung des Sensors im Werkzeug, die Positionierung des Sensors sowie die Datenübertragung wichtige Kernthemen, die es zu bewältigen galt. Neben konstruktivem Geschick waren primär der Dialog mit Kunden und unserem Partner Kistler ausschlaggebend für das Ergebnis.
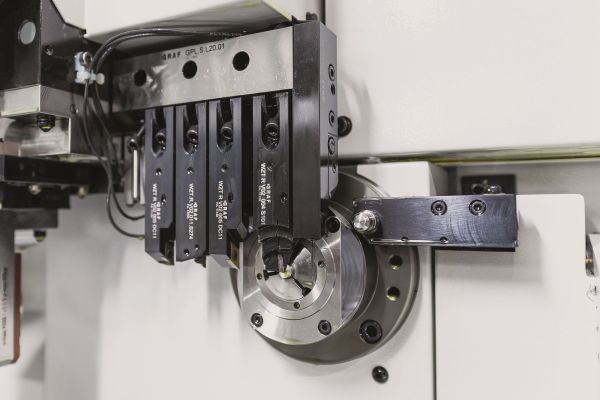
Welche Weiterentwicklung wird es da noch geben oder könnte es geben?
Im Bereich Sensorik ist künftig eine Datenvereinfachung geplant sowie die Erweiterung der Auswertungsmöglichkeiten. Ein weiterer Schritt ist die Einbindung von KI für intelligente Produktion.
Arbeiten Sie generell bei der Entwicklung von Zerspanungswerkzeugen mit Hochschulen zusammen?
Wir arbeiten mit mehreren Hochschulen zusammen. Unter anderem jenen in Stuttgart, Karlsruhe, Aachen und Schmalkalden. Der wissenschaftliche Austausch, Forschungsprojekte und Prüfungen gehören bei unserem ganzheitlichen Ansatz ebenso dazu, wie der direkte Draht zu unseren Kunden. Wir sind davon überzeugt, dass im Dialog die besten Lösungen entstehen.
Firma: Mapal
Antwortgeber: Jacek Kruszynski, CTO
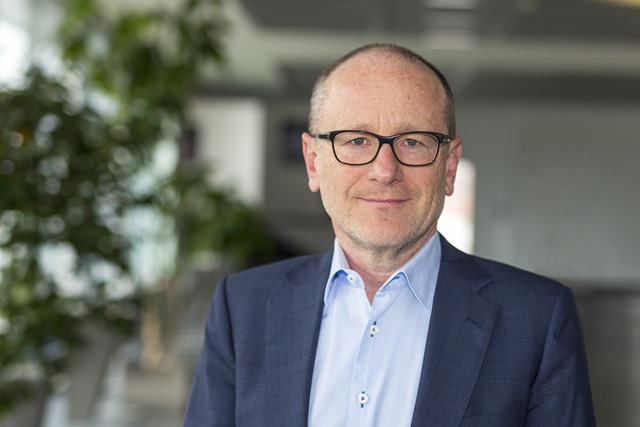
Was sind momentan die grossen Trends, die in Ihre Entwicklung von Werkzeugen einfliessen?
Selbstverständlich gibt es mehrere grosse Trends in der zerspanenden Industrie und den Märkten für Präzisionswerkzeuge. In der Automobilindustrie bestimmen die Bauteile für die Elektromobilität die Trends in der Zerspanung, wobei die Bearbeitung des Statorgehäuses hier strategisch an erster Stelle zu nennen ist. Die prozesssichere und wirtschaftliche Bearbeitung dünnwandiger Gehäuse ist aber nicht nur auf die Automotive-Industrie beschränkt.
Als zweiten Trend, der ebenfalls branchenübergreifend zu sehen ist, möchte ich die Titanbearbeitung nennen. Titan kommt als Werkstoff mit seinen speziellen Eigenschaften in immer mehr Bauteilen unterschiedlichster Branchen auch ausserhalb der Luftfahrt zum Einsatz. Gleiches gilt für Verbundwerkstoffe mit CFK.
Die Digitalisierung ist ein weiterer Trend, den Hersteller von Präzisionswerkzeugen sowohl innerbetrieblich als auch im Hinblick auf neue Produkte umsetzen. Künstliche Intelligenz, Cloud Computing oder Connectivity sind hier wesentliche Schlagworte.
Welcher scheint ihnen der Wichtigste oder würden Sie besonders hervorheben, weil er bei Ihnen eine grosse Rolle spielt?
Ich möchte an der Stelle die Titanbearbeitung hervorheben, da wir wie erwähnt diese Tendenz in vielen Branchen sehen. Und zwar Titan sowohl als Verbundwerkstoff zusammen mit CFK – in diesem Bereich sehen wir, dass der Anteil von Verbundwerkstoffen mit Titan und CFK im Vergleich zu Aluminium und CFK zunimmt. Aber genauso, dass Titan allein als Werkstoff zunehmend für unterschiedlichste Bauteile in der Medizintechnik, im Automotivebereich und natürlich in der Luftfahrt zur Anwendung kommt.
Für Mapal spielt der Trend eine wichtige Rolle, da Titan und Titanverbundwerkstoffe schwer zu bearbeiten sind und ein grosses Know-how sowohl von den zerspanenden Betrieben als auch von den Präzisionswerkzeugherstellern im Hinblick auf die Werkzeugauslegung und -entwicklung erfordert.
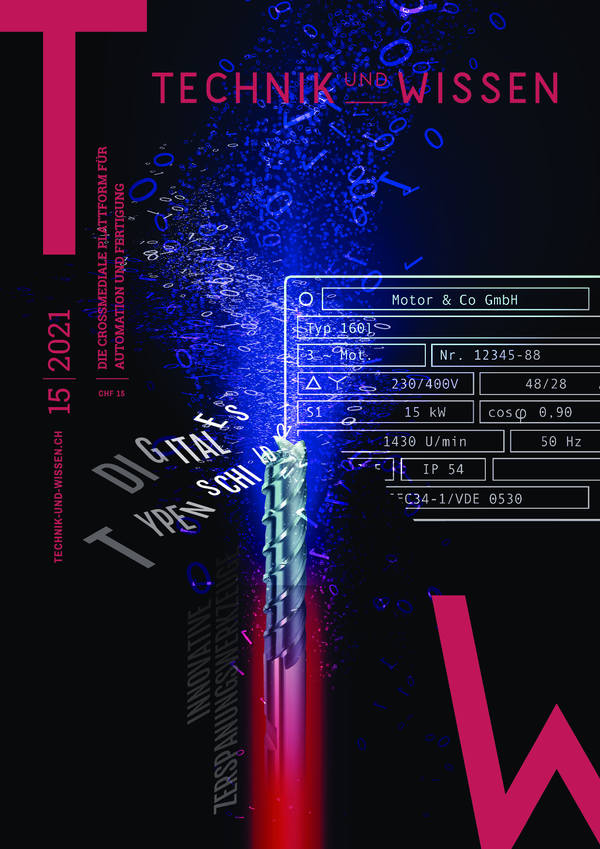
Schwerpunkt«Innovative Zerspanungswerkzeuge»
Printmagazin Ausgabe #015 - Weitere Werkzeughersteller wie Bimu, Mapal, Paul Horn und Fraisa standen uns Red und Antwort zum Schwerpunktthema «Innovative Zerspanungswerkzeuge».
Neue Bohrer und Fräser für die Titanbearbeitung
Welches Produkt in Ihrem Portfolio gibt es, das diesen Trend bereits aufnimmt und umgesetzt hat?
Mapal hat zur EMO 2021 neue Bohrer und Fräser aus Vollhartmetall und Fräser mit Wendeschneidplatten für die Titanbearbeitung auf den Markt gebracht. Hohe Schnittwerte und durchdachte Wärmeabfuhr kennzeichnen alle drei Neuentwicklungen. Bei der Auslegung der Werkzeuge haben wir uns an den Anforderungen der Zielmärkte an die Titanzerspanung orientiert.
Entsprechend breit ist das Spektrum an verfügbaren Durchmessern: Angefangen bei kleinen Grössen ab 3 mm, wie sie oft in der Medizintechnik verlangt werden, über die mittleren Grössen für Sportwagenkomponenten bis hin zu den grossen Werkzeugen für den Flugzeugbau und die Energietechnik.
Was können diese erwähnten Werkzeuge und welche technischen Raffinessen stecken dahinter?
Nehmen wir die Wendeschneidplattenfräser NeoMill-Titan als Beispiel. Wir haben speziell auf die Titanbearbeitung abgestimmte Walzenstirnfräser als Aufsteck- und Schaftvariante sowie Eckfräser neu im Standardportfolio. Die Topografie der Wendeschneidplatte des NeoMill-Titan wurde von Grund auf neu entwickelt, um die Späne optimal zu formen und abzuführen. Die Wendeschneidplatten verfügen über je zwei Schneidkanten und weisen Eckenradien von 0,8 mm bis 4 mm auf.
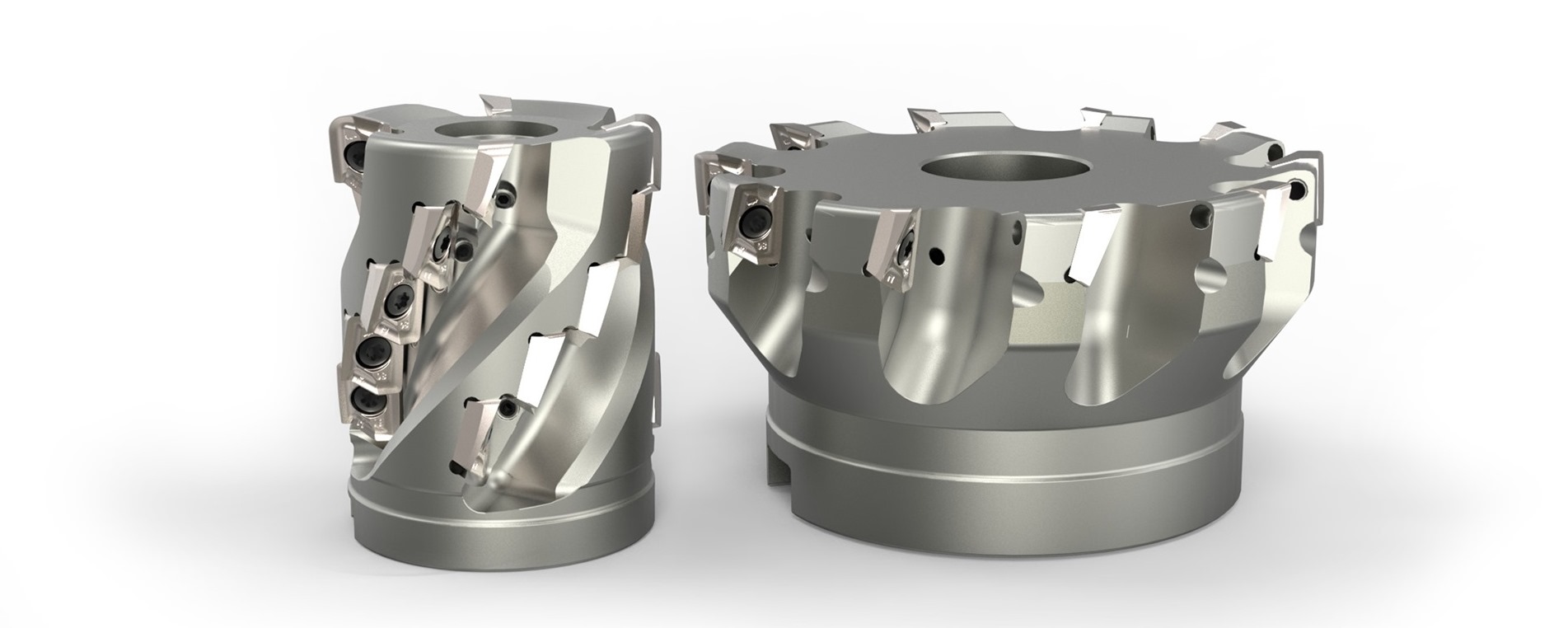
Beim Schneidstoffkonzept standen minimaler Verschleiss und die Vermeidung von Aufbauschneiden im Fokus. Neben einer verschleissfesten Universalsorte wurde speziell für die Bearbeitung mit höheren Schnittgeschwindigkeiten eine temperaturfeste Hochleistungssorte entwickelt, die Schnittgeschwindigkeiten bis 70 m/min möglich macht.
Für die Hochtechnologieschneiden wurde auch der Werkzeugkörper neu entwickelt, um die Späne optimal aus der Scherzone zu befördern. Die Ungleichteilung der Schneiden sorgt für Stabilität und Laufruhe. Variabel gestaltete Kühlmittelaustritte ermöglichen die Regulierung der Durchflussmenge für jede einzelne Schneide.
Was waren die Herausforderungen, um das Tool zu entwickeln und wie hat man sie gemeistert?
Die geforderte Bearbeitungsqualität und die Werkzeugstandzeiten stehen bei der Titanbearbeitung im Fokus. Wir setzen beide Anforderungen durch unsere Schneidengeometrie und eine optimale Beschichtung optimal um.
Welche Weiterentwicklung wird es bei diesen Werkzeugen noch geben?
Die Produktpalette für die Titanbearbeitung werden wir über die Neuheiten 2021 hinaus erweitern.
Impressum
Autor: Eugen Albisser
Bildquellen: Fraisa, Horn, Mapal
Redaktionelle Bearbeitung: Technik und Wissen
Eine Publikation von Technik und Wissen
Weitere Artikel
Veröffentlicht am: