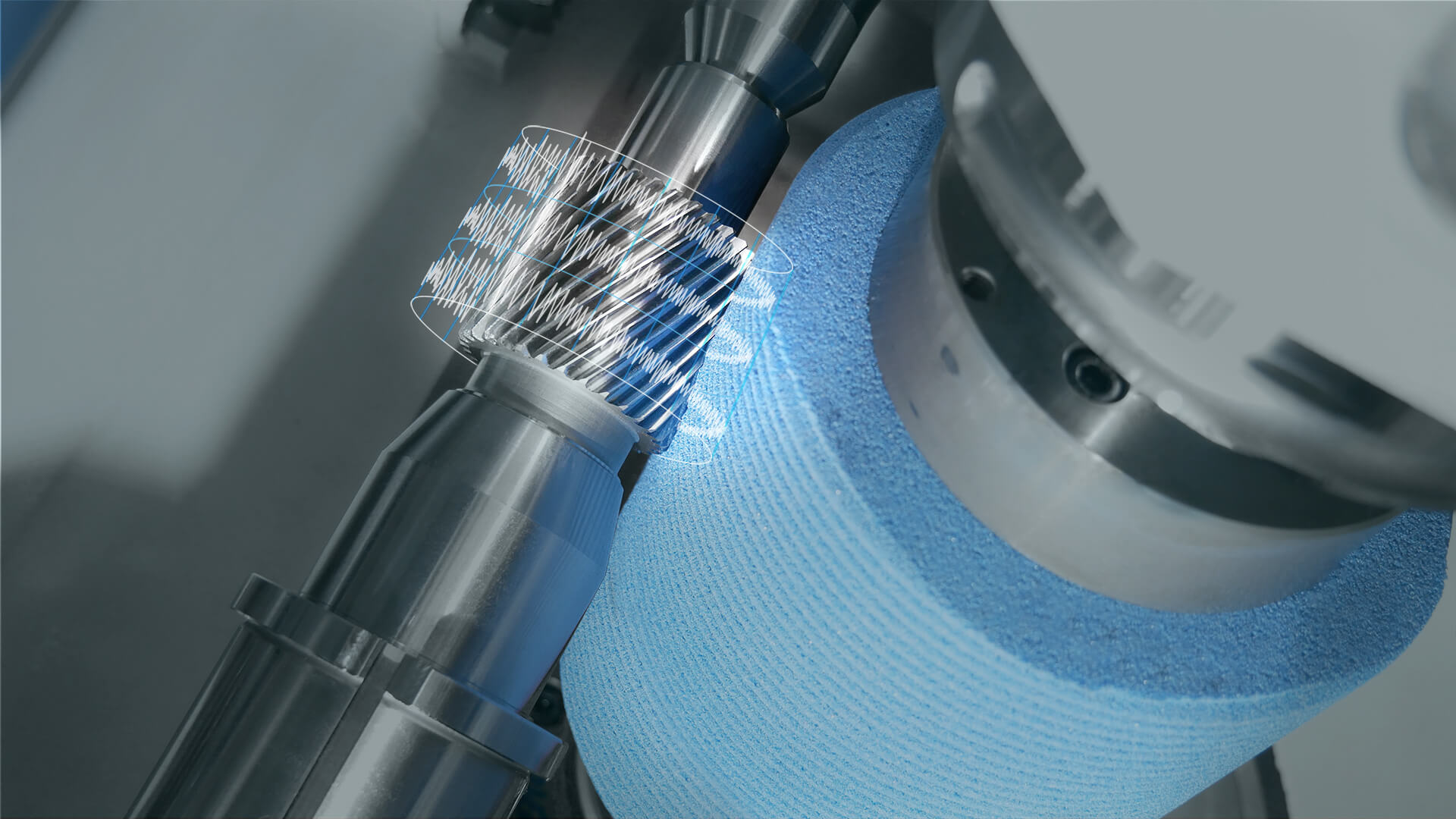
Getriebe für E-Autos sind viel einfacher aufgebaut als für konventionelle Verbrenner, stellen aber weit höhere Anforderungen an die Fertigungsgenauigkeit der eingesetzten Zahnräder. Durch völlig neue Verfahren zur Qualitätssicherung direkt im finalen Bearbeitungsprozess Verzahnungsschleifen lassen sich diese Vorgaben auch in der Serienfertigung erfüllen.
Vollelektrische Fahrzeugantriebe kommen meist mit zweistufigen, nicht schaltbaren Getrieben aus. Man sollte meinen, dass dies die Herstellung stark vereinfacht. Schliesslich verfügt der beschriebene Getriebeaufbau über gerade einmal vier Verzahnungen, verteilt auf Antriebswelle, die zweite Stufe mit Festrad und Zwischenwelle sowie das Achsantriebsrad. Aber so einfach sind die Verhältnisse nicht: Zunächst sind die Motordrehzahlen beim E-Antrieb mit bis zu 16'000 U/min viel höher als beim Verbrenner.
Bei Geschwindigkeiten ab etwa 80 km/h sind die Abroll- und Windgeräusche der dominierende Faktor, unabhängig vom Antriebsstrang. Aber in dem Bereich darunter können sich bei E-Fahrzeugen die Getriebegeräusche störend bemerkbar machen. Das müssen wir auch bei der Fertigung der Zahnräder berücksichtigen.»
Dazu liefern E-Motoren über einen breiten Drehzahlbereich ein nahezu konstantes Drehmoment. Anders als beim Verbrenner liegt es bereits ab Drehzahl Null am Getriebe an. Überdies gibt es noch eine zusätzliche Randbedingung, die die Fertigung wesentlich anspruchsvoller macht als beim konventionellen Antriebsstrang, wie Friedrich Wölfel, der Leiter des Maschinenvertriebs bei Kapp Niles, beschreibt: «Ein Verbrennungsmotor maskiert die Getriebegeräusche, sodass diese erst gar nicht wahrgenommen werden. Ein Elektromotor ist dagegen nahezu lautlos. Bei Geschwindigkeiten ab etwa 80 km/h sind die Abroll- und Windgeräusche der dominierende Faktor, unabhängig vom Antriebsstrang. Aber in dem Bereich darunter können sich bei E-Fahrzeugen die Getriebegeräusche störend bemerkbar machen. Das müssen wir auch bei der Fertigung der Zahnräder berücksichtigen.»
Auf das Geräuschverhalten optimierter Wälzschleifprozess für Zahnräder
Natürlich stehen auch bei E-Antrieben die Flankentragfähigkeit der Zahnräder und gute Laufeigenschaften im Vordergrund. Das nahezu konstante Drehmomentniveau und die hohen Drehzahlen erfordern allerdings eine andere Auslegung der Verzahnung, die sich aber wiederum auf das Geräuschverhalten auswirken kann. Dabei sind gerade hier die Ansprüche höher als beim Verbrenner.
Keinen Unterschied zwischen Zahnrädern für E-Fahrzeuge und konventionelle Antriebe gibt es dagegen bei dem Druck, diese mit höchster Wirtschaftlichkeit herzustellen. Dementsprechend kommt auch in der Serienfertigung von E-Getriebe-Verzahnungen im Regelfall das hochproduktive Wälzschleifverfahren als Feinbearbeitungsprozess zum Einsatz.
Für Kapp Niles als Spezialist für die Hartfeinbearbeitung von Zahnrädern stellt sich damit die Aufgabe, einen gleichermassen produktiven und vor allem auch mit Blick auf das Geräuschverhalten optimierten Wälzschleifprozess zu realisieren.
Spannender Artikel zum Thema Elektroauto-Produktion:
LASERVERFAHREN FÜR DIE ELEKTROAUTO-PRODUKTION – DIE MEGATRENDS
Getriebegeräuschen auf der Spur
Achim Stegner, Leiter der Vorentwicklung bei Kapp Niles, beschreibt die Grundlagen: «Abhängig sowohl von den konstruktiv definierten Modifikationen der Verzahnungen, wie beispielsweise Linienkorrekturen, Breitenballigkeiten, Kopfrücknahmen, als auch den sogenannten verfahrenstypischen Profil- und Linienverschränkungen entstehen im Getriebe beim Eingriff charakteristische Geräusche, die bestimmten Zahneingriffsfrequenzen zugeordnet werden können. Das gesamte Getriebe wiederum weist ebenfalls je nach konstruktiver Auslegung bezüglich Körperschall und Abstrahlungen charakteristische Eigenschaften auf. Die Anregung erfolgt hierbei in der Zahneingriffsfrequenz und deren Vielfachen. Die Hersteller versuchen diesen Effekt durch eine angepasste Auslegung von Getriebe und Verzahnungen möglichst gering zu halten.»
Diese Überlegungen gelten zunächst einmal nur für «perfekte» Verzahnungen. Aber natürlich weisen auch Zahnräder, wie jedes andere mechanische Bauteil, in der Serienfertigung Abweichungen von der idealen Sollgeometrie auf. Diese haben unterschiedliche Ursachen und Auswirkungen, wie Achim Stegner erläutert: «Neben der Anregung durch den Zahneingriff gibt es weitere Störgrössen, die zu Geräuschen im Zahneingriff führen können.
Diese machen sich als sogenannte Geisterfrequenzen bemerkbar. Es handelt sich dabei um Frequenzen, die nicht mit den Zahneingriffsfrequenzen und deren Vielfachen zusammenfallen, und die eben auch beim Schleifen in das Bauteil eingebracht werden können.»
Ursachen für Geisterfrequenzen sind minimale Unregelmässigkeiten, die in der Serienfertigung kaum völlig zu vermeiden sind. Besonders kritisch wird es dann, wenn sich diese Abweichungen nahezu ganzzahlig auf dem Umfang eines Zahnrads abbilden, da es damit zu einer harmonischen Anregung kommt. Es erfordert viel Know-how und Prozesserfahrung, um die Gründe für solche Unregelmässigkeiten zu erkennen und diese möglichst schon im Vorfeld zu vermeiden.
Ungünstige Drehzahlkonstellation im Wälzschleifprozess kann Folgen haben
Die Ursache für solche Störungen kann beispielsweise in den Achsantrieben der eingesetzten Werkzeugmaschine zu finden sein. Elektrische Motoren weisen gewisse Pendelmomente auf. Messsysteme arbeiten mit diskreten Strichzahlen und endlichen Exzentrizitätsfehlern aus der Montage. Nicht zuletzt können Wuchtzustand und Spindellager einen Beitrag zu möglichen Unregelmässigkeiten leisten. Bereits Welligkeiten in der Grösse ab 0,1 µm können bei Verzahnungen zu Geräuschen führen.
Achim Stegner kennt auch noch mehr Ursachen: «Jede Maschine weist Eigenschwingungen auf. So beträgt beispielsweise die typische Eigenfrequenz einer Werkstückspindel etwa 250 Hz. Auch diese kann sich bei einer ungünstigen Drehzahlkonstellation im Wälzschleifprozess ganzzahlig auf dem Werkstück abbilden. Solche Effekte können wir mit unserem Wissen über die geschickte Wahl eines geeigneten Drehzahlfensters bei der Bearbeitung eliminieren.»
Ist das Optimierungspotenzial auf der Maschinenseite ausgeschöpft, gibt es zudem eine Reihe von technologischen Möglichkeiten, um die Bauteilqualität hinsichtlich des Geräuschverhaltens zu verbessern. Hierzu zählen z. B. die Wahl der Gangzahl der Schleifschnecke, das Drehzahlverhältnis beim Abrichten und Schleifen, die Schlichtdrehzahl und die Vorschubgeschwindigkeit.
Die zwei Arten von Fehlern beim Verzahnungsschleifen
Grob gesagt, gibt es beim Verzahnungsschleifen in der Serie zwei typische Arten von Fehlerbildern: Zum einen zeichnen sich Trends ab, die eine kontinuierliche Veränderung von Merkmalen aufzeigen. Zum anderen gibt es individuell auffällige Bauteile. Trends sind meist einfacher zu beherrschen. Sie entstehen beispielsweise durch die allmähliche Abnutzung einer Schleifschnecke. Werden hier zulässige Fertigungstoleranzen überschritten, genügt es meist, den Zyklus zwischen zwei Abrichtvorgängen zu verkürzen. Sie lassen sich bei der Bauteilprüfung auch gut durch eine allmähliche Annäherung der Messwerte an die Toleranzgrenze erkennen.
Bauteilindividuelle Fehler hingegen sind nicht vorhersehbar. Sie machen sich durch plötzliche Abweichungen bei einem oder auch mehreren Qualitätskriterien bemerkbar. Ursache können Schleifschneckenausbrüche, Rohteilfehler oder aber auch Rüstfehler sein.
Bei den Analyse- und Steuerungsmethoden ansetzen
Da bei hocheffizienten Fertigungsverfahren wie dem Wälzschleifen die eigentliche Bearbeitung eines Zahnrads wesentlich weniger Zeit beansprucht als die Kontrollmessung, können auch nicht 100 % aller Bauteile geprüft werden. Zudem sind, wie eingangs beschrieben, die Qualitätsansprüche an Verzahnungen für E-Getriebe extrem hoch. «Die geforderten Toleranzen von Profilwinkel, Flankenlinienwinkel, Rundlauf, Zweikugelmass sind teils um den Faktor 3 kleiner als im konventionellen Antriebsstrang.
Beim Flankenlinienwinkelfehler fHss liegt eine typische Forderung bei ± 4 µm, bei Verbrenner-Getrieben waren das auch mal ± 13 µm», schildert Friedrich Wölfel die Anforderungen seiner Kunden. Zusammen mit den geforderten Maschinen- und Prozessfähigkeiten bewegen sich diese Qualitätsanforderungen am Rande des technisch und wirtschaftlich Machbaren. Und auch statische und dynamische Stabilität von Bearbeitungsmaschine und Prozess lassen sich nicht beliebig steigern.
Als Ausweg bleibt nur, bei den Analyse- und Steuerungsmethoden anzusetzen. Denn ansonsten gilt: Je enger die Toleranzgrenzen bei gleichbleibender Maschinen-/Prozessfähigkeit werden, desto grösser muss die Anzahl der gemessenen Bauteile sein. Das allerdings ist mit hohem Aufwand verbunden. Und letztlich ist eine nachgelagerte Bauteilprüfung auch nicht wertschöpfend.
Closed Loop als wichtiges Hilfsmittel
Mit Blick auf die Herangehensweise bei trendbedingten Abweichungen von der Sollgeometrie hat sich heute bereits der sogenannte Closed Loop als wichtiges Hilfsmittel etabliert. Beschleunigt und verbessert wird damit die Rückkopplung zwischen nachgelagerter Verzahnungsmessung und der Bearbeitungsmaschine selbst.
Hierbei werden die Ergebnisse der Prüfung auf der Messmaschine nicht mehr ausgedruckt und dem Maschinenbediener zur Bewertung auf Papier zur Verfügung gestellt, sondern direkt als standardisierte Datei an die Bearbeitungsmaschine übermittelt.
Die Schleifmaschine entscheidet dann anhand vorwählbarer Toleranzkorridore selbstständig, ob überhaupt in den Prozess eingegriffen werden muss, etwa mit skalierbaren Korrekturwerten. Treten unerwartet hohe Abweichungen von der Sollgeometrie auf, liegt die Entscheidung zum weiteren Vorgehen dann wieder beim Bediener selbst.
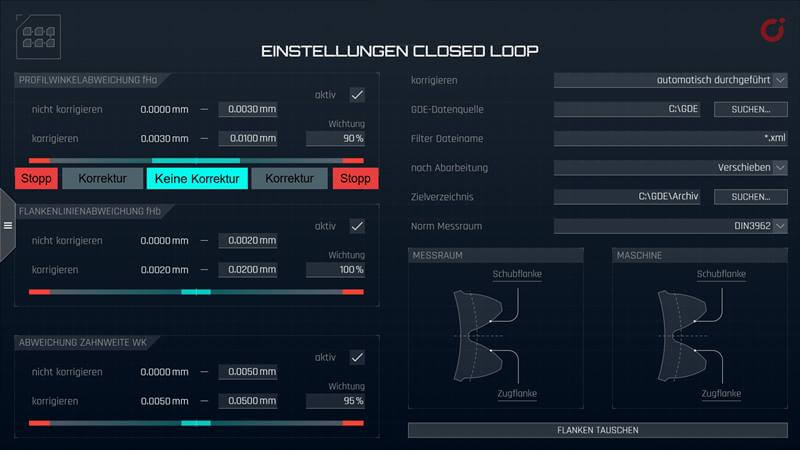
Der Schiedsrichter am Ende des Herstellprozesses
Am Ende des Herstellprozesses eines kompletten Getriebes steht ein sogenannter End-of-line-Prüfstand. Dort werden nicht mehr nur einzelne Zahnräder hinsichtlich ihrer Qualität geprüft, sondern fertig montierte Getriebe bewertet. Sie durchlaufen verschiedene Prüfzyklen, mit denen der spätere Betrieb im Fahrzeug simuliert wird. Dabei wird auch das Betriebsgeräusch aufgenommen.
Durch eine entsprechende Auswertung dieser Daten können Akustiker Eingriffsverhältnisse, typische Frequenzen und mögliche Störgeräusche herauslesen. «Leider fallen damit auch Verzahnungsfehler erst am Ende des Herstellungsprozesses auf», moniert Friedrich Wölfel. «Dann muss das komplette Getriebe demontiert, die einzelnen Bauteile geprüft und darauf aufbauend analysiert werden, welches Bauteil für die Auffälligkeit am Prüfstand verantwortlich ist. Möglicherweise kann auch eine komplette Charge an Bauteilen Probleme bereiten. Das fällt aber erst auf, wenn die komplette Wertschöpfungskette bereits abgeschlossen ist.»
Weiterentwicklung der In-Prozess-Analyse
Zwar gibt es heute Möglichkeiten, Bauteile zu identifizieren, die Geräusche verursachen könnten, bevor sie ins Getriebe eingebaut werden. Ein bei E-Antrieben sehr gängiges Verfahren ist die sogenannte Welligkeitsanalyse auf Verzahnungsoberflächen. Hierbei werden auf der Verzahnungsmessmaschine Profil-, Linien- und Teilungsmessungen an allen Zähnen durchgeführt und so aneinandergereiht, dass das Zahnrad über seinen kompletten Umfang abgebildet wird. Mittels mathematischer Verfahren lässt sich die Welligkeit auf dem Zahnrad erfassen.
Allerdings ist dieses Verfahren beginnend mit der vollständigen Vermessung der Zahnräder sehr zeitaufwändig und damit für eine 100 %-Prüfung in der Serienfertigung ungeeignet. Dazu Friedrich Wölfel: «Die Schleifzeit typischer E-Getriebe-Bauteile beträgt weniger als eine Minute, die Messzeit dagegen vier bis sechs Minuten; bei einer Allzahnmessung als Basis einer Welligkeitsanalyse sogar nochmal deutlich mehr. Und letztlich ist eine nachgelagerte Bauteilprüfung auch nicht wertschöpfend. Was hier benötigt wird, ist eine Weiterentwicklung der In-Prozess-Analyse, die bereits bei der Bearbeitung selbst Rückschlüsse auf die erzeugte Bauteilqualität zulässt.»
Geräuschprobleme schon bei der Bearbeitung erkennen
Ein vielversprechender Ansatz ist tatsächlich, mögliche Fehler schon während des Schleifens auszumachen. Prozessmonitoring heisst das Schlagwort. Achim Stegner erklärt die Herangehensweise: «Wir haben in der Maschine bereits zahlreiche Sensoren und Messsysteme, die uns sehr viele Signale, Messwerte und Informationen liefern können. Momentan nutzen wir sie vorrangig nur, um die Funktionen der Maschine zu bedienen. Zukünftig wollen wir sie darüber hinaus aber auch einsetzen, um den Bearbeitungsprozess direkt in der Maschine zu beurteilen.»
Damit ist aber nicht gemeint, eine zusätzliche taktile Messfunktion in die Schleifmaschine zu integrieren, um damit einen schnelleren Closed Loop zu realisieren. Es geht hier auch nicht darum, ein geschliffenes Bauteil direkt in der Maschine zu prüfen, zu bewerten und eventuelle Abweichungen bei der Herstellung weiterer Bauteile zu korrigieren. Der Fokus liegt vielmehr auf der Analyse des Bearbeitungsprozesses in Echtzeit (!), um Abweichungen von einem vorher definierten Referenzprozess zu erkennen. Dafür reicht es aber nicht, nur Hüllkurven für Signale aus der Maschine zu definieren.
Beispielhaft lässt sich das anhand des Signals «Stromaufnahme der Schleifspindel» erläutern – siehe folgendes Bild:
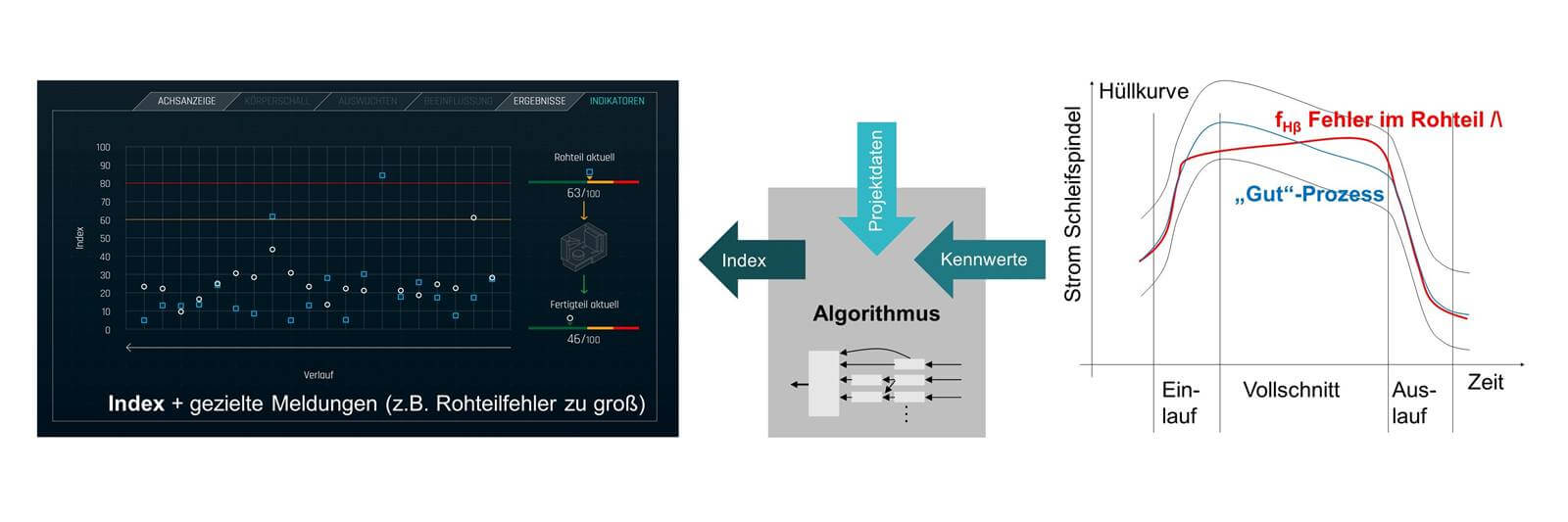
Nutzen kann man dieses Signal, um einen möglichen Flankenlinienwinkelfehler (fHss) frühzeitig zu erkennen. Stegner: «Das Verfahren über die Hüllkurvenerkennung kommt allerdings hier an seine Grenzen, da der Fehler nur schwer zu identifizieren ist. Solange das Signal innerhalb der Hüllkurve bleibt, wird kein Alarm ausgelöst. Man benötigt also eine intelligentere Form der Auswertung. Eine künstliche Intelligenz, die versucht, Entscheidungsstrukturen des Menschen nachzubilden. Dieser trifft aus einer Vielzahl unterschiedlicher Informationen – überlagert mit seinen Erfahrungen – Entscheidungen, nach denen er handelt.
Prozessmonitoring: Eingreifen, bevor es zu spät ist
Prozessmonitoring lässt sich als bauteilspezifische Überwachung und Bewertung des Schleifprozesses definieren. Wie beschrieben, ist es nicht trivial, aus den Sensorsignalen eine Handlungsanweisung zu generieren. Aber es ist möglich. Aus Zeitsignalen lassen sich verschiedene Kennwerte bilden. Im einfachsten Fall können diese Maximal- oder RMS-Werte (Root Mean Square) der Signale sein.
Die Kennwerte werden dann mit den bekannten Projektdaten über Algorithmen zusammengefasst und zu Indices verarbeitet, zum Beispiel zu einem Geräusch- oder Schneckenausbruch-Index. Speziell zu den Getriebegeräuschen führt Achim Stegner aus: «Für geräuschkritische Bauteile lässt sich über eine FFT (Fast Fourier Transformation) eine Ordnungsanalyse ähnlich dem Ordnungsspektrum an einem End-of-line-Prüfstand erstellen.
Damit können die aufgezeichneten Signale besser eingeordnet und in Bezug zu Ergebnissen am Getriebeprüfstand gebracht werden – siehe folgendes Bild:

Nicht aufbereitete Messdaten haben keinen Nutzen.» Am Ende helfen vor allem im Fertigungsumfeld nur entsprechende Indices, um sehr spezifisch Fehler zu identifizieren.
Der Nutzen des Prozessmonitorings lässt sich also an folgenden Punkten festmachen:
- 100 %-Prüfung aller Bauteile
- Identifikation von Auffälligkeiten noch im Schleifprozess
- Erkennung von bauteilspezifischen Fehlern
- Gezielte Meldung über Unregelmässigkeiten
- Adaptiver Eingriff in den Prozess
- Teilerückverfolgung
Nächster Schritt: Standardisierung
Prozessmonitoring ist heute noch keine App, die man einfach herunterladen und nutzen kann. Es ist vielmehr eine kunden- und anwendungsspezifische Entwicklung, die bezogen auf das jeweilige Bauteil Indices definiert und überwacht. Doch schon dieser erste Schritt ist weit mehr, als bis vor kurzem für machbar gehalten wurde.
Dazu Achim Stegner: «Schon heute setzen mehrere Pilotkunden diese Funktionalität ein. Wir können aktuell bereits unterschiedliche Fehler erkennen und auch prozessseitig eingreifen. Zudem arbeiten wir bereits daran, dass die Schleifmaschine sich Kennwerte für neue Bauteile selbst anlernt. Dazu ist aber natürlich breites Erfahrungswissen aus Fehlerbildern, der geometrischen Qualität der Bauteile und entsprechender Rückmeldungen vom Getriebeprüfstand notwendig.» Friedrich Wölfel ergänzt:
«Nächstes Ziel ist, dass der Anwender diese Funktionalität auch ohne unsere bauteilspezifische Unterstützung nutzen kann. Wichtig ist auch zu verstehen, dass sich Prozessmonitoring und Closed Loop nicht widersprechen, sondern ergänzen.»
Beide Ansätze zur prozessintegrierten Qualitätssicherung stehen schon heute für Kapp Niles-Maschinen zur Verfügung und erhalten durch die Erfahrungen aus dem Serieneinsatz kontinuierlich weitere Funktionsumfänge und Nutzungsmöglichkeiten.
Impressum
Textquelle: Kapp Niles
Autor: Dipl.-Phys. Martin Witzsch, freier Journalist im Auftrag von Kapp Niles
Bildquelle: Kapp Niles
Redaktionelle Bearbeitung: Technik und Wissen
Eine Publikation von Technik und Wissen
Informationen
Kapp Niles
www.kapp-niles.com
Weitere Artikel
Veröffentlicht am: