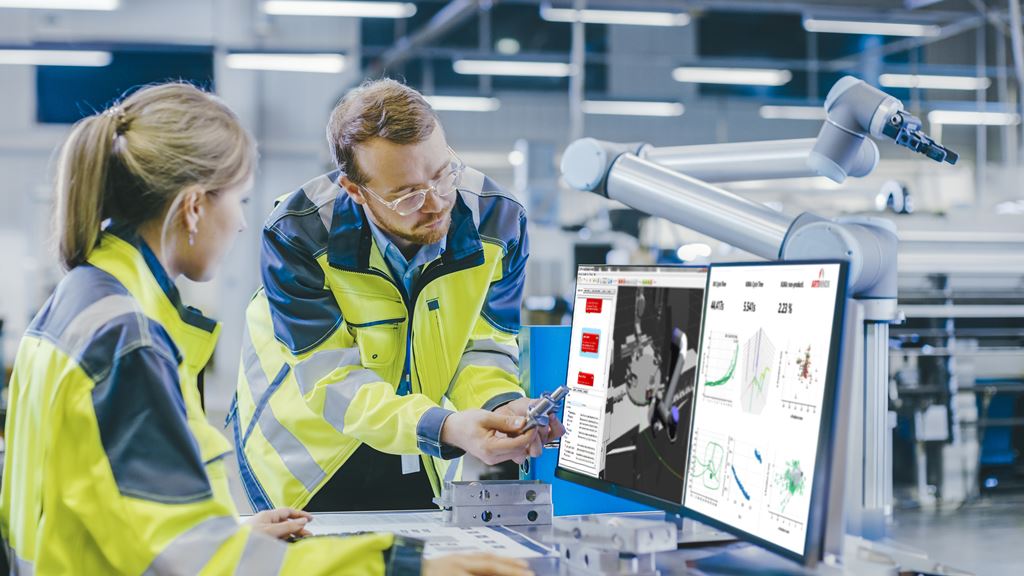
Viele Automatisierungsprozesse sind hochkomplex. Oft ist es unmöglich von aussen zu sehen, was in einer Maschine oder Anlage zu welchem Zeitpunkt vorgeht. Das wäre jedoch hilfreich, um Prozesse weiter zu optimieren, Predictive Maintenance zu ermöglichen oder Prozesse an sich ändernde Gegebenheiten anzupassen. Eine herstellerunabhängige Datenanalysesoftware speziell für Produktionsprozesse ermöglicht tiefe Einblicke.
Redaktionelle Bearbeitung: Technik und Wissen
Prozessdaten gibt es in einer Produktionsanlage zu Genüge. Sensoren, Aktoren, Kameras, Roboter erfassen und verarbeiten Unmengen an Daten. Meistens ist also nicht das Sammeln der Daten die Herausforderung, sondern diese zu analysieren, einzelnen Prozessschritten zuzuordnen und sinnvoll zu visualisieren. Nur anhand solcher verdichteten Informationen lassen sich aus riesigen Datenmengen hilfreiche Rückschlüsse ziehen und kontextbezogene Erkenntnisse ableiten.
Herstellerunabhängige Analysesoftware erhöht Produktivität
Die Analysesoftware Learning & Analytics for Robots (LAR) der Robotikexperten ArtiMinds aus Karlsruhe ermöglicht detaillierte Einblicke in Produktionsprozesse. Sie hat sich in Roboteranwendungen bewährt, die mit dem Programmiertool ArtiMinds RPS aus dem eigenen Hause entwickelt wurden und steht jetzt als herstellerunabhängiges Analysetool für alle Automatisierungsprozesse zur Verfügung. Die Software erfasst spezifische Bewegungs- und Sensordaten des Produktionsprozesses, speichert sie in einer lokalen Datenbank und ordnet die Daten einzelnen Prozessschritten zu.
Für die Zuordnung lassen sich verfügbare Signale wie z.B. die eines Schrittzählers nutzen. Über frei konfigurierbare Dashboards kann der Anlagenbetreiber dann verschiedene Einblicke in den realen Produktionsprozess sowie einzelne Schritte gewinnen. Diese Dashboards lassen sich entsprechend der Bedürfnisse verschiedener Zielgruppen (Instandhaltung, Produktionsplanung, Qualitätssicherung, Management usw.) erstellen und die visualisierten Daten anhand definierter KPIs bewerten.
Datenanalyse, Überwachung, Optimierung und Dokumentation sind so mit einem einzigen Tool möglich, und zwar bei der Planung und Inbetriebnahme von Neuanlagen ebenso wie in Brownfield-Anlagen. Standardisierte Schnittstellen zu industriellen Komponenten sorgen für eine einfache Integration ohne zusätzliche Programmierung. Dadurch ist auch der Einsatz rein zur kurzfristigen Fehlersuche z.B. über OPC UA attraktiv.
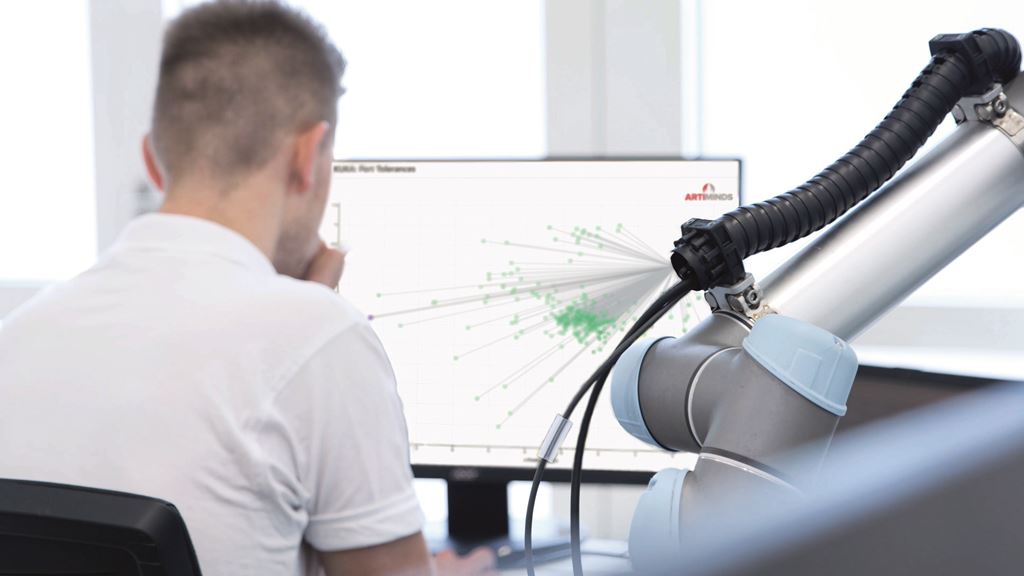
Insgesamt steht die Prozessanalyse von Produktionsanlagen im Mittelpunkt. Über langfristige Datenerfassung und -abgleiche lassen sich Verschleiss ermitteln, Instandhaltung planen, Abweichungen zwischen verschiedenen Produktchargen auffinden, Ursachen von Problemen aufdecken, Taktzeiten optimieren, Wartezeiten verkürzen, Qualität verbessern und vieles mehr.
Anwender profitieren dabei vom synchronisierten Datenabgleich zwischen Robotersteuerung oder SPS und den Sensorkomponenten, der manuell nur schwer umzusetzen wäre. Dabei nutzt die Software vorhandene Prozessdaten und braucht nur selten ergänzende Hardware. Einige bereits realisierte Praxisbeispiele zeigen, welche Anwendungsfälle davon profitieren können:
Predictive Maintenance mit Bordmitteln
In einer Anlage, in der unter anderem über zehn Roboter an der Produktherstellung beteiligt sind, sorgen zahlreiche Kameras für die Qualitätssicherung. Der Anlagenbetreiber trat mit der Anfrage, wie sich die vorbeugende Instandhaltung optimieren lässt, an ArtiMinds heran. Die Lösung war mit minimalem Eingriff und ohne zusätzliche Hardwareintegration in den Produktionsprozess umsetzbar: Nach Installation der LAR-Software war es dem Anwender möglich, die jeweiligen Erkennungsergebnisse der zur QS eingesetzten Kameras mit dem jeweiligen Prozessschritt abzugleichen und entsprechend abzuspeichern.
Aus einem breiten Sortiment vordefinierter Analysekacheln konnte er die für seinen Zweck hilfreichen auswählen und im zugehörigen Nutzer-Front-End im Browser visualisieren. So hat der Anlagenbetreiber nun einen Einblick in die Live-Daten des Prozesses. Er kann Tendenzen beobachten und beispielsweise Grenzwerte setzen und die Zeitpunkte definieren, zu denen Instandhaltungsmassnahmen geplant werden sollten. Installation zusätzlicher Hardware war hier nicht notwendig und damit auch kein Eingriff in die bestehende Anlage.
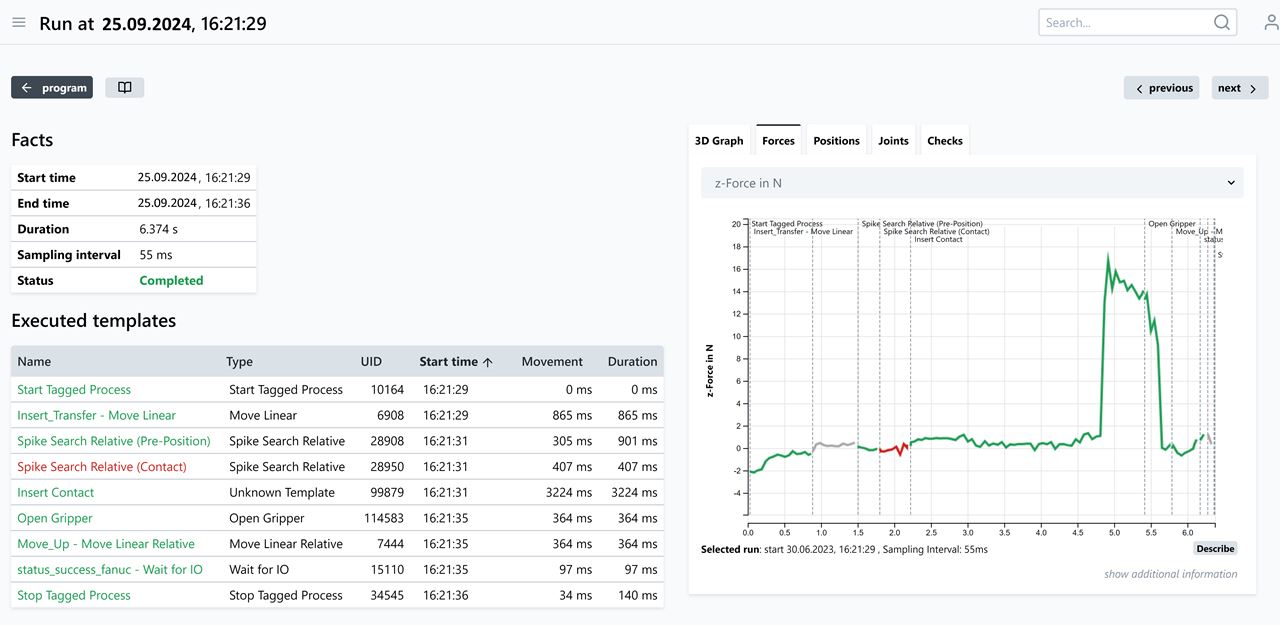
Taktzeiten optimieren
In einer anderen Anwendung im Automobilbau ging es um Prozessoptimierung. Zwei Roboterarme arbeiteten gleichzeitig in einem Punktschweissprozess. Um herauszufinden, welcher Roboter idealerweise welche Teilaufgaben übernimmt, galt es im ersten Schritt reale Warte- und reale Taktzeiten der beiden Roboter zu ermitteln. Auch hier wurde mit der LAR- Analysesoftware möglich, was zuvor nicht einfach umsetzbar war: Den realen Ist-Zustand einer Anlage digital und automatisiert abzubilden, ohne weitere Hardware zu integrieren. Mit den gesammelten und visualisierten Daten liessen sich dann im nächsten Schritt Aufgaben optimal auf die zwei Roboter verteilen und Taktzeiten des Produktionsprozesses optimieren.
Daten dokumentieren
Im Zusammenhang mit Qualität spielt auch eine nachverfolgbare Dokumentation und lückenlose Datenerfassung eine wichtige Rolle. Prozessdaten müssen erfasst und verfügbar gehalten werden. In vielen Fällen geschieht dies mit Hilfe von Hand ausgefüllten Excel-Listen, die dann meist aufwendig von einer Stelle an die andere kopiert werden müssen. Ein Anwender, der sich gegen diese manuellen und fehleranfälligen Arbeiten entschied, setzte ebenfalls auf die automatische Datenerfassung und Anbindung mit Hilfe der LAR-Software. Hier ist die Zeitersparnis immens und auch die Qualität der Daten verbessert sich, weil keine Fehler mehr durch manuelle Weitergabe oder Kopieren entstehen und Daten in Echtzeit gesammelt werden können.
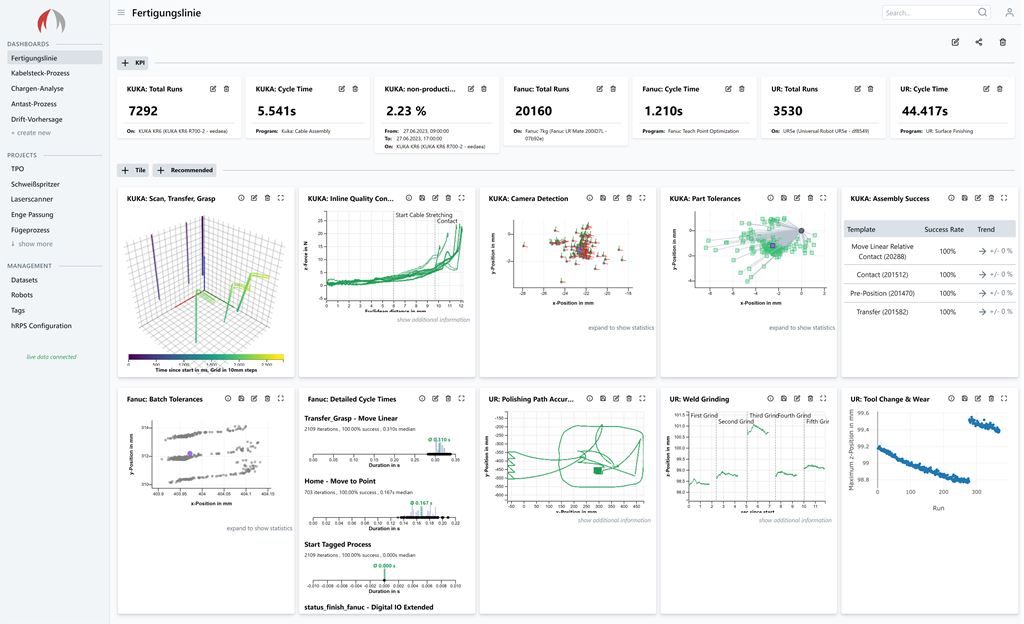
Fehlersuche und Prozessoptimierung
Ein Prozess zum Fügen von Bauteilen zu einem Elektromotor war aufgrund hoher Bauteiltoleranzen nicht prozesssicher. Hier ging es im ersten Schritt darum, die Prozessdaten mit der LAR-Software zu dokumentieren. Mit den gesammelten Daten wurde es dann im nächsten Schritt möglich, den Prozess zu überwachen und automatisch zu entscheiden, ob die Bauteile nutzbar sind, oder als Ausschuss entsorgt werden müssen. Damit ist aber noch nicht das volle Potential ausgereizt. Denkbar wäre in einem weiteren Schritt die Realisierung einer (automatisierten) Teachpunkt-Optimierung mit Hilfe der realen Prozessdaten, um Toleranzen der Bauteile automatisch auszugleichen und den Ausschuss zu verringern.
Reale Prozesse transparent machen
Viele Anwendungen kämpfen damit, die verschiedenen Prozessdaten in Deckung zu bringen. Dieses Problem galt es bei einem Fügeprozess zu lösen, bei dem Komponenten im Antriebsstrang eines Pkws zusammengesetzt werden sollten. Der Prozess lief bei der Anlageninbetriebnahme noch nicht optimal und auch die Taktzeit liess Luft nach oben. Nun galt es herauszufinden, wann genau innerhalb der vielen Prozessschritte Fehler auftraten. Dann mussten die zu diesem Zeitpunkt zugehörigen Sensordaten ermittelt und zum Problem in Bezug gebracht werden. Hier war es hilfreich, dass für den Fügeprozess bereits ein Kraft-Momenten-Sensor im Einsatz war. Dieser war ursprünglich nur zur Kollisionsvermeidung eingesetzt. Mit dem vorhandenen Sensor und der Analysesoftware wurde es nun aber möglich, der Ursache auf den Grund zu gehen, indem auch die beim Fügeprozess auftretenden Kräfte gemessen und mit einzelnen Roboterbewegungen in Beziehung gesetzt wurden. In einem zweiten Schritt kann der Anwender damit den Prozess optimieren, zum Beispiel indem er Parameter anpasst oder einzelne Anlagenteile gezielt neu teacht.
Teachvorgänge automatisieren
Rainer Jäkel, CTO bei der ArtiMinds Robotics GmbH, erklärt: «Das schrittweise Vorgehen ist für den Anwender äusserst attraktiv, weil er flexibel entscheiden kann, wie weit er bei der Optimierung gehen will. Will er nur den Ist-Zustand erfassen, dann die notwendigen Anpassungen berechnen lassen und manuell in den Prozess zurückspielen? Oder will er auch das Zurückspielen automatisieren? Beides ist möglich.»
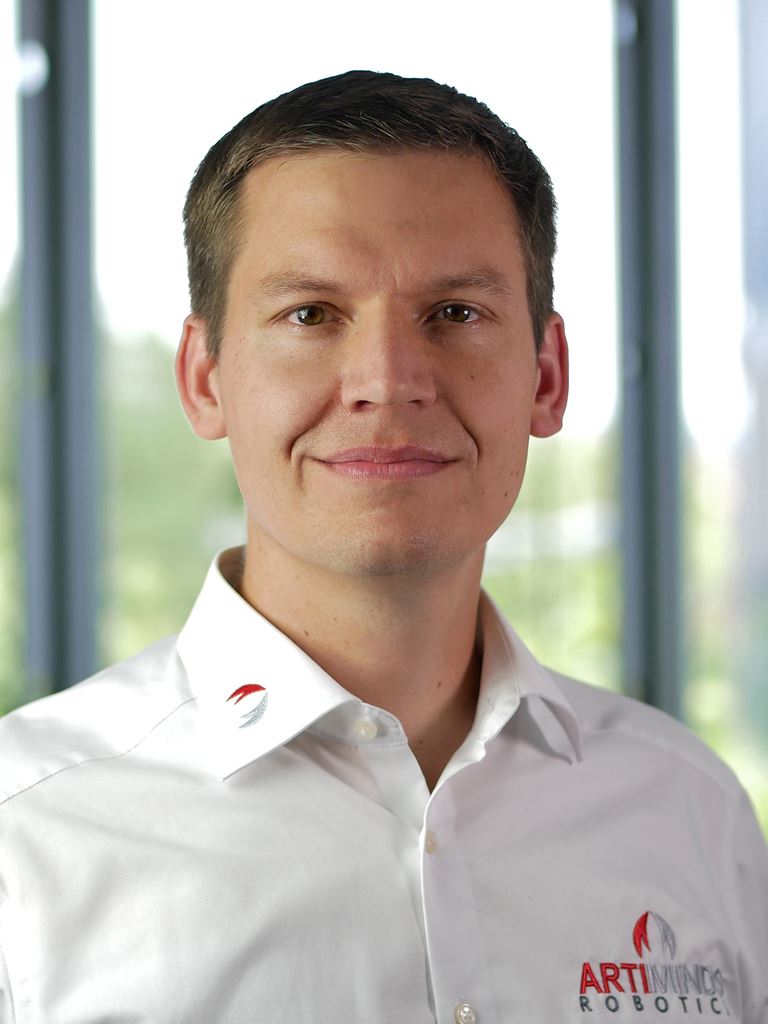
Eine Anwendung, bei der die automatisierte Nachjustierung sinnvoll war, realisierten die Robotikexperten in einer Brownfield-Anlage. Bedingt durch Erschütterungen im Produktionsumfeld wanderte eine Prozessmaschine nach und nach relativ zum eingesetzten Roboter. Schliesslich war der Versatz so gross, dass der Roboter seine Teilaufgabe nicht mehr zuverlässig ausführen konnte. Es kam zu Produktionsausfällen und der Roboter musste regelmäßig neu geteacht werden.
Um das Problem in den Griff zu bekommen, wurde eine Kamera ergänzt, die die Abweichungen der Prozessmaschine überwacht. Gemeinsam mit der LAR-Software wertet sie die Position aus. Wird die Abweichung zwischen Maschine und Roboterarm zu gross, gibt die Software automatisiert einen neuen Startpunkt für den Arbeitsschritt des Roboterarms an diesen weiter. Dieser passt sich in wohl definierten Schranken den veränderten Bedingungen im laufenden Prozess automatisch an.
Qualität verbessern
Nicht nur Prozess- sondern auch Qualitätsoptimierung ist eine Aufgabe, die mit der Analyse-Software gelöst werden kann. Bei einem Automobilhersteller sollte beim Einrichten einer Anlage automatisiert ein Schweisskopf ausgerichtet und dadurch die optimale Qualität einer Schweissnaht erzielt werden. Dies wurde mit einem zusätzlichen taktilen Sensor realisiert, der die reale Abweichung des Bleches von der Vorgabe ermittelt. Zusammen mit der Analysesoftware konnte auch hier der Prozess so optimiert werden, dass Schweissnähte höchster Qualität entstanden.
Jäkel ergänzt: «Diese Maschinen sind in Werken international im Einsatz. Mit unserer Software hat der Kunde beim Einrichten und der Inbetriebnahme in Deutschland jede Menge Daten gesammelt, die nun für die Fernwartung beim internationalen Einsatz der Maschine zur Verfügung stehen. Kommt es bei der Montage zu Problemen, ist über den Datenabgleich eine bessere Beratung aus der Ferne möglich.»
Die Anwendungsvielfalt macht deutliche, dass zahlreiche Bestands- und Neuanlagen von der Analysesoftware profitieren. Durch die einfache Integration lassen sich Vorteile ohne zusätzlichen Programmieraufwand und meist sogar ohne zusätzliche Sensor-Hardware in kürzester Zeit nutzen.
Passend zu diesem Artikel
Impressum
Textquelle: Artiminds
Bildquelle: Artiminds
Redaktionelle Bearbeitung: Technik und Wissen
Weitere Artikel
- Automatisierung
- Predictive Maintenance
- Produktion
- Produktionsoptimierung
- Prozessindustrie
- Software
- SPS
Veröffentlicht am: