Auf der Suche nach der autonomen, fühlenden Maschine
Ein Interview mit Prof. Dr.-Ing. Berend Denkena, Leiter des Instituts für Fertigungstechnik und Werkzeugmaschinen (IFW) an der Leibniz Universität Hannover
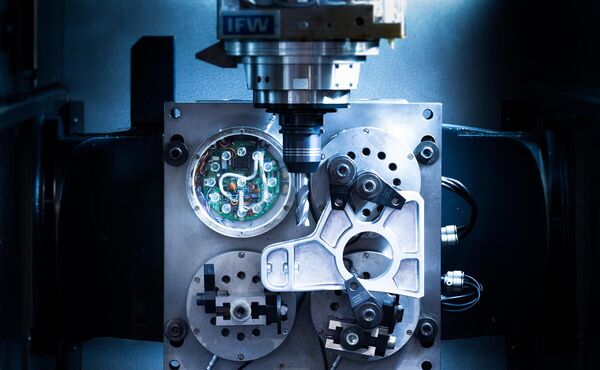
Auf der Suche nach der autonomen, fühlenden Maschine
Ein Interview mit Prof. Dr.-Ing. Berend Denkena, Leiter des Instituts für Fertigungstechnik und Werkzeugmaschinen (IFW) an der Leibniz Universität Hannover
Es ist ein grosser Traum, an dem in den Laboren des Instituts für Fertigungstechnik und Werkzeugmaschinen (IFW) an der Leibniz Universität Hannover geforscht und entwickelt wird: die fühlende und smarte Maschine. Was kann sie? Was wird sie können? Prof. Dr.-Ing. Berend Denkena, Leiter des Instituts gibt Antworten auf den grossen Traum.
Autor: Eugen Albisser
Inhalt dieses Artikels
Definition von «fühlende Maschine»?
Professor Denkena, beginnen wir dieses Interview mit einer Definitionsfrage: Wie kann man eine «fühlende Maschine», wie sie am IFW entwickelt wird, am besten definieren?
Die «fühlende Maschine» adaptiert die Fähigkeiten eines Werkers in der Produktion. Wie der Werker mit seinen Händen erfühlt die Maschine den Zustand des Prozesses, Werkstücks und Werkzeugs. Mittels strukturintegrierter Sensorik in den Komponenten misst die Maschine die Prozesskräfte. Und: Diese Maschine reagiert wie ein Werker. Durch die Erfassung des Prozesszustandes und die anschliessende Generierung von Zustandsdaten und -signalen zur weiteren Auswertung ist die fühlende Werkzeugmaschine beispielsweise in der Lage, Prozessstellgrössen autonom an die aktuelle Situation im Prozess anzupassen.
Die fühlende Maschine für die smarte Fabrik
Eine fühlende Maschine ist sicherlich auch als Grundlage gedacht für eine komplett autonom arbeitende Werkzeugmaschine in der smarten Fabrik. Wie würde eine solche smart Factory produzieren?
Die individuelle Produktion, die Fertigung in Losgrösse 1 – dieser Trend nimmt weiter zu. Die Kleinserien- und Einzelteilfertigung wird in der Fabrik der Zukunft eine bedeutende Rolle spielen. Um dabei wirtschaftlich agieren zu können, muss bereits das erste gefertigte Bauteil den gestellten Anforderungen entsprechen. Das heisst, dass die zahlreichen Einflussgrössen in der Fertigung bei der Planung und Bearbeitung der Bauteile berücksichtigt werden müssen.
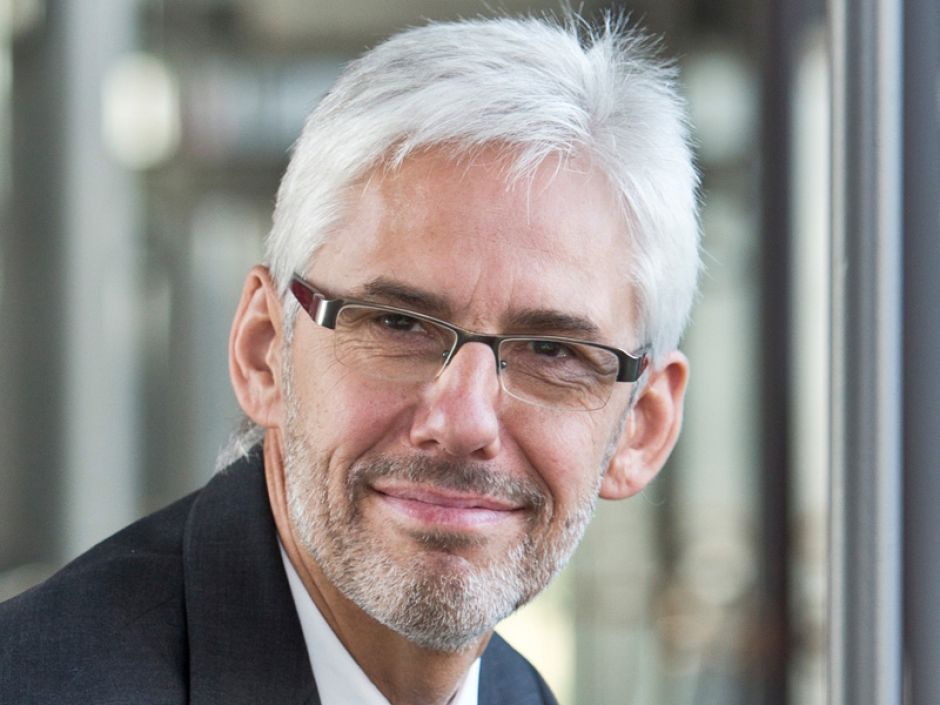
Was eine riesige Herausforderung sein kann.
Ja, und selbst für erfahrene Mitarbeiter ist es kaum möglich, auf Anhieb alle Stellgrössen richtig einzustellen. Künstliche Intelligenz ist das Schlagwort, wenn es um die Werkzeugmaschine der Zukunft geht. Die Maschine muss aus den Informationen im Prozess lernen, Prozessstellgrössen autonom anzupassen und das im Prozess gelernte Wissen auch wieder in die Planung miteinfliessen zu lassen. Die fühlenden Maschinen ermöglichen es, dieses Wissen in Form der gemessenen Kräfte im Prozess zu erfassen. Sie sind damit ein wesentlicher Grundbaustein der smarten Fabrik, in der die gesamte Fertigung von der Planung bis hin zum fertigen Bauteil vollautonom abläuft.
Stufe zwei auf dem Weg zur autonomen Maschine
Wie weit entfernt sind wir noch von dieser Vision?
Die erste Stufe auf dem Weg zur autonomen Maschine – der überwachten Fertigung – haben wir bereits erreicht. Auf dem Weg zur zweiten Stufe – der automatisierten Fertigung – haben wir mit unseren Forschungsarbeiten bereits wichtige Erfolge erzielt. Diese Erkenntnisse aus der Forschung nun in der Industrie zu etablieren, ist der nächste wesentliche Schritt für die Fabrik der Zukunft. Auch wenn wir unter anderem durch neue technologische Möglichkeiten aus dem Bereich der Digitalisierung rasant grosse Fortschritte erzielen, ist es noch ein weiter Weg hin zu einer teilautonomen und schliesslich einer vollautonomen Fertigung.
Was genau fehlt noch? Wo ist die Technologie noch nicht so weit?
Wie bereits erwähnt, unterliegt die spanende Fertigung zahlreichen Einflussfaktoren, die bis heute noch nicht alle vollständig erforscht sind. Trotz der grossen technischen Fortschritte ist es immer noch schwierig, das genaue Maschinenverhalten vorherzusagen. Viele der bereits existierenden Überwachungs- und Regelungssysteme sind Insellösungen für spezielle Prozesse, die nur mit viel Parametrieraufwand auf andere Prozesse oder Maschinen übertragen werden können. Gerade für die Einzelteilfertigung werden allerdings Systeme benötigt, die auch für noch unbekannte Prozesse funktionieren und sich ohne Aufwand auf unterschiedliche Maschinen übertragen lassen.
Aber aktuell sind Fertigungsprozesse in der Regel fest programmiert mit wenig Möglichkeiten zur Anpassung.
Das ist so. Die technologischen Möglichkeiten, um Werkzeugbahnen autonom an die aktuellen Gegebenheiten im Prozess anzupassen, sind bisher nur sehr eingeschränkt vorhanden. Hier fehlt es noch an robusten Algorithmen, die in der Lage sind, die verschiedenen Störgrössen, wie beispielsweise Werkzeugverschleiss, geeignet zu berücksichtigen. Ebenfalls ist die Rückführung von Prozesswissen in die Planungsebene bislang kaum vorhanden.
Die fühlende Maschine und ihre Sensoren
Wenn wir die fühlende Maschine Ihres Instituts genauer anschauen, welche Komponenten und Neuentwicklungen bestimmen diese Maschinen?
Im Gegensatz zu herkömmlichen Sensorsystemen sind die Sensoren bei den fühlenden Maschinen in die Struktur der Maschine integriert. Dadurch wird der Prozess durch das Sensorsystem nicht beeinträchtigt. Zudem ist die Sensorik kostengünstig und für bestehende Maschinen nachzurüsten. Um an den steifen Strukturen die Prozesskräfte zu erfassen, haben wir DMS [Dehnungsmessstreifen, Anm. der Redaktion] mit erhöhter Sensitivität entwickelt. Zusätzlich haben wir Kerben in die Struktur des Spindelschlittens eingebracht, mit denen eine lokale Dehnungserhöhung ermöglicht wird.
Was ist das Resultat?
Wir konnten mit diesen beiden Ansätzen zeigen, dass eine genaue Kraftmessung ohne Beeinträchtigung der Struktursteifigkeit nahe am Prozess möglich ist. Dieser Ansatz zur Kraftmessung ist dabei nicht nur auf eine Komponente beschränkt. So konnten wir ebenfalls erfolgreich weitere fühlende Komponenten, wie das Spannsystem, entwickeln.
Dehnungsmessstreifen statt Kraftsensoren: Warum?
Sie verwenden in der fühlenden Maschine Dehnungsmessstreifen statt Kraftsensoren. Weshalb und welche anderen Sensoren werden sonst noch eingesetzt?
DMS sind im Gegensatz zu herkömmlichen Kraftsensoren kostengünstig und dadurch für die industrielle Anwendung sehr attraktiv. Je nach Einsatzgebiet arbeiten wir auch mit anderen Sensoren, wie Beschleunigungssensoren zur Ratterdetektion oder auch mit steuerungsinternen Signalen.
Wie viele Sensoren sind momentan im Einsatz in einer einzigen Maschine?
Die Anzahl der Sensoren variiert von Werkzeugmaschine zu Werkzeugmaschine. Aktuell sind an den fühlenden Maschinen am IFW neun Dehnungsmessstreifen angebracht. Durch eine höhere Anzahl an Sensoren können natürlich mehr Informationen aus dem Prozess aufgenommen und Ausfälle einzelner Sensoren besser kompensiert werden. Dennoch hängt die Anzahl der notwendigen Sensoren stark von dem konkreten Anwendungsfall und der verwendeten Werkzeugmaschine ab.
Wie kann man die Datenfülle da noch erfassen und korrekt auswerten − und dies in Echtzeit?
Die Auswertung der Daten ist eine grosse Herausforderung. Wir arbeiten mit Filtern und der Berechnung von Merkmalen, um auch nur die wirklich notwendigen Informationen zu verarbeiten. Dabei sehen wir, dass wir hier an die Grenzen der heutigen Steuerung stossen. Die Echtzeitfähigkeit ist ein Schlagwort: Um diese zu erreichen, arbeiten wir eng mit Werkzeugmaschinen- und Steuerungshersteller zusammen.
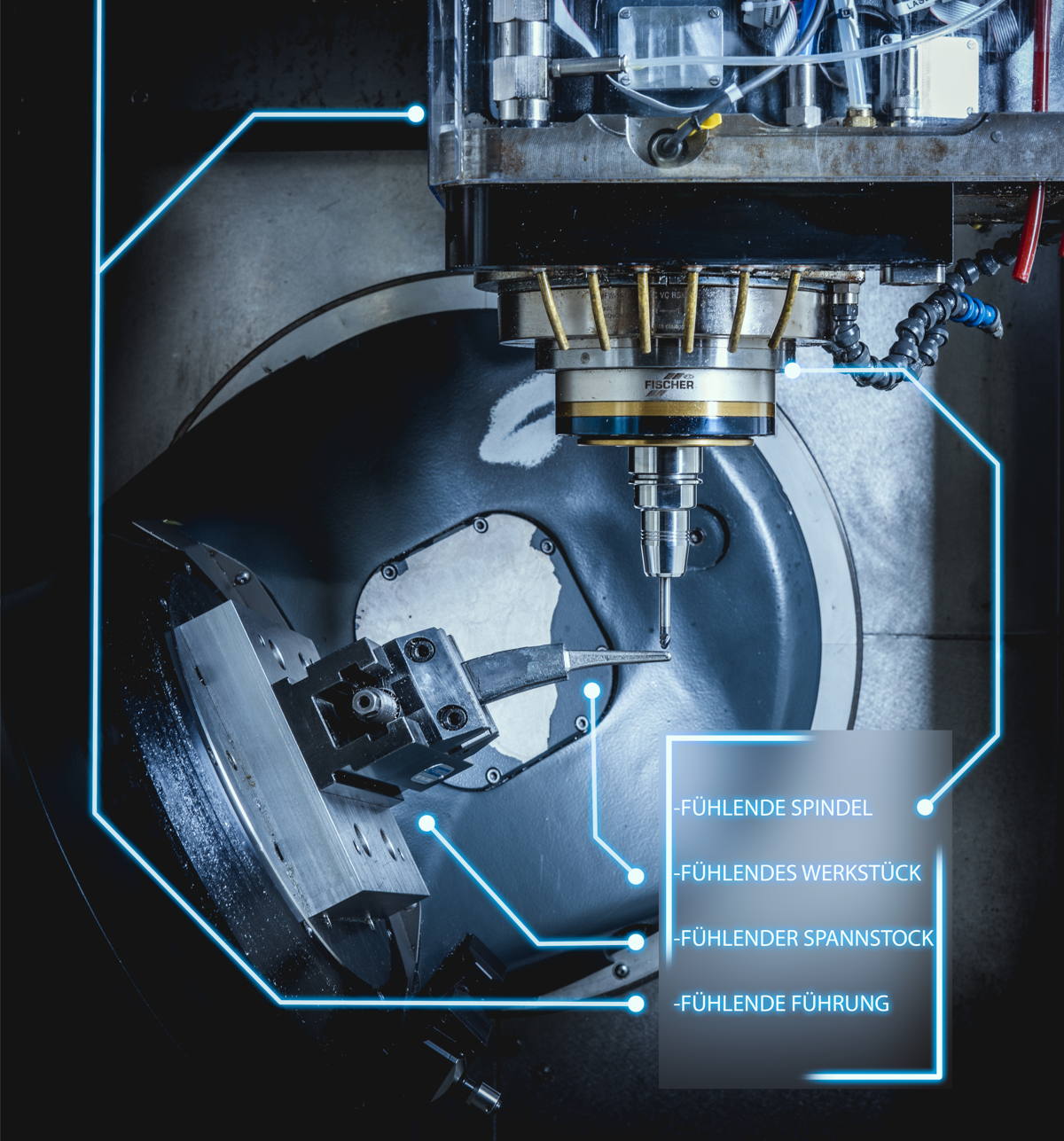
Das gentelligente Werkstück
Was man oft vergisst: Es ist ja nicht nur die Maschine, die fühlen sollte, sondern auch die Werkstücke. Wie weit ist man in dieser Beziehung und wie läuft da eine Kommunikation ab zwischen Werkstück und Werkzeugmaschine?
Wir haben im Rahmen des Sonderforschungsbereichs «Gentelligente Bauteile im Lebenszyklus» intensiv daran gearbeitet und Konzepte entwickelt. Die «fühlende» Eigenschaft ist dabei nur eine der werkstückinternen Funktionen. Ein gentelligentes Werkstück trägt die Informationen für seine Bearbeitung mit sich und sucht sich so selbstständig den Weg durch die Produktion. Durch die Informationen, die im Werkstück gespeichert sind, wird eine bauteilindividuelle Bearbeitung in der Maschine ausgelöst.
Und die Fertigungshistorie kann auch nachverfolgt werden.
Ja, auch dies. Die fühlenden Eigenschaften der Bauteile ermöglichen es, die gesamte Fertigungshistorie aufzunehmen und kontinuierlich im Bauteil zu speichern. Im fertigen Bauteil werden die zur Prozessüberwachung integrierten Sensoren für die Aufnahme von Belastungen verwendet. Die so über den Lebenszyklus des Bauteils gesammelten Informationen fliessen in die Entwicklung der nächsten Bauteilgeneration ein.
Was in den Labors entwickelt wird, ist eine Sache; am Markt eine andere. Welche Entwicklungen aus dem IFW an der fühlenden Maschine sind bereits markttauglich und vor allem wirtschaftlich sinnvoll?
Von der prototypischen Entwicklung am Institut hin zu einem industriell einsetzbaren Produkt ist es ein weiter Weg. Durch die enge Zusammenarbeit mit der Industrie sind wir hier dennoch schon sehr weit fortgeschritten. Einige unserer fühlenden Komponenten werden bereits zur Überwachung von Prozessen eingesetzt. Die intelligente Abdrängungskompensation auf Basis der fühlenden Komponenten ist bereits auf dem Weg in die industrielle Anwendung.
Welche Entwicklungsschritte stehen dann momentan an?
Wie eingangs bereits angedeutet, arbeiten wir aktuell daran, die fühlende Maschine durch den Einsatz moderner Technologien wie Künstlicher Intelligenz, auch intelligent zu machen. Bisher haben wir die Informationen aus dem Prozess vor allem genutzt, um zu reagieren. Jetzt geht es darum, beispielsweise Prozesszustände vorherzusagen, um frühzeitig kritische Prozesszustände zu vermeiden. Aktuelle Forschungsarbeiten beschäftigen sich zudem mit dem Einsatz von Halbleiter-Dehnungsmessstreifen. Sie erzielen eine deutlich höhere Sensitivität als herkömmliche Dehnungsmessstreifen.
Einsatz von Künstlicher Intelligenz
Wie wird Künstliche Intelligenz bereits eingesetzt?
KI wird bei uns bereits in vielen Bereichen eingesetzt. Beispielsweise kann die Werkzeugmaschine durch den Einsatz von KI lernen, wie die Eingriffsbedingungen mit den Kräften im Prozess zusammenhängen. Dieses Wissen wird dann in der Bahnplanung verwendet, um die Werkzeugbahnen autonom so anzupassen, dass Formfehler vermieden werden. Gerade bei komplexen 5-Achs-Bauteilen in der Einzelteilfertigung stossen klassische Verfahren hier schnell an ihre Grenzen. Die fühlenden Maschinen liefern der KI die dafür notwendigen Informationen. So ist es erstmalig möglich, dass Maschinen aus den Informationen vorangegangener Prozesse lernen und das gelernte Wissen auch für die autonome Bahnplanung für neue Prozesse anwenden.
Vielleicht brauche ich da mal eine Begriffserklärung: Das Institut verwendet selber den Begriff «fühlende Maschine». Gibt es einen Unterschied zu einer smarten, intelligenten Maschine? Und wenn ja, wo steckt der Unterschied – wo wird eine Grenze gezogen?
Die smarte oder intelligente Maschine ist die zweite Ausbaustufe der fühlenden Maschine. Die fühlende Maschine ermöglicht den überwachten Prozess. Informationen können direkt aus dem Prozess ermittelt werden. Bei der smarten Maschine werden diese Informationen genutzt, um Prozessstellgrössen autonom anzupassen. Die smarte Maschine kann den Prozess nicht nur selbstständig überwachen, sondern auch autonom auf Fehler und Veränderungen im Prozess reagieren.
Artikel zur Künstlichen Intelligenz
KI-Serie: Wie lernen Maschinen, wie lernen Menschen?
Teil 1 - Wie lernen Maschinen?
«Eine KI ist nicht intelligent» − Ein Gespräch mit Prof. Dr. Thilo Stadelmann von der ZHAW
Teil 2 - Wie lernen Menschen?
«Unser Gehirn tut, was es will» − Ein Gespräch mit Prof. Dr. Dr. Werner Wiater, Universität Augsburg
Ein wichtiger Teil einer solchen Maschine ist auch, dass sie in einem Notfall sich selbst reparieren könnte. Gibt es ein Beispiel für eine Reparatur, die heute schon möglich ist und auch aufzeigt, wie weit eigentlich diese Vision gehen könnte in der Zukunft?
Durch die datenbasierte Zustandsüberwachung können wir Schäden an einzelnen Maschinenkomponenten bereits frühzeitig erkennen. Ungeplante Maschinenstillstände werden dadurch vermieden. Wir haben hier beispielsweise schon grosse Erfolge in der Zustandsüberwachung von Kugelgewindetrieben durch den Einsatz von KI erzielt. Schäden werden so rechtzeitig erkannt. Die Maschine übermittelt erkannte Schäden dann autonom an einen Servicetechniker. Selbstreparierende Maschinenkomponenten sind aktuell Gegenstand zahlreicher Forschungsvorhaben.
Haben Sie ein Beispiel dafür?
Beispielsweise können sich intelligente Materialien bei Bedarf ausdehnen und so verschleissbedingten Vorspannungsverlusten entgegenwirken. Andere Materialien haben eine Art Formgedächtnis und können selbst nach einer Kollision wieder autonom ihre ursprüngliche Form annehmen. Die Vision der selbstheilenden Maschine setzt sich aus der Selbstdiagnose und der Selbstheilung zusammen.
Welche Entwicklung im Bereich «fühlende Maschine» finden sie eigentlich am spannendsten und auf welche sind sie besonders stolz?
Die fühlenden Maschinen werden bei uns schon seit Jahren stetig weiterentwickelt und verbessert. Es ist dann natürlich ein tolles Gefühl zu sehen, dass sich diese Arbeit gelohnt hat und wir hier auch zeigen können, dass beispielsweise Formfehler im Prozess durch den Einsatz der fühlenden Maschinen deutlich reduziert werden können. Gerade das Interesse der Industrie zeigt uns, dass wir hier auch einen wesentlichen Beitrag zum wirtschaftlichen Fortschritt leisten. Jetzt zu sehen, wie die fühlenden Maschinen durch unsere Forschungsarbeit zunehmend intelligenter und autonomer werden, macht mich natürlich besonders stolz.
Der mobile Werkzeugroboter
Es gibt neben der fühlenden Werkzeugmaschine auch noch den mobilen Werkzeugroboter, der an ihrem Institut entwickelt wird. Wie geht es dem?
Das IFW hat die mobile Werkzeugmaschine für die flexible Ausbesserung und den Einsatz bei der Bearbeitung von Grossbauteilen entwickelt. Ein grosser Erfolg ist in diesem Zusammenhang die Ausgründung der Firma Picum MT, die die mobile Werkzeugmaschine erfolgreich weiterentwickelt und aktuell in die industrielle Anwendung bringt. Natürlich unterstützen wir die Weiterentwicklung der mobilen Werkzeugmaschine bei Picum MT auch weiterhin durch unsere Forschungsarbeiten. Im Zusammenhang mit unserem neuen Forschungszentrum für Grossmaschinen Scale ist geplant, die mobile Werkzeugmaschine für die Bearbeitung von Grossbauteilen einzusetzen.
Was ist das Spezielle an diesem Roboter?
Bei herkömmlichen Werkzeugmaschinen muss das Werkstück zur Maschine transportiert werden. Die Maschinen haben nur einen fest definierten Bearbeitungsraum und sind dadurch in ihrer Skalierbarkeit eingeschränkt. Gerade bei Grossbauteilen oder fest montierten Bauteilen ist dies oft problematisch. Bei der mobilen Werkzeugmaschine kommt die Maschine zum Werkstück. Das bedeutet die Maschine kann überall auf dem Werkstück platziert werden und ist dadurch deutlich flexibler als fest stationierte Werkzeugmaschinen. Da sich die mobile Maschine quasi auf dem Werkstück entlang bewegen kann, können prinzipiell Bauteile von beliebiger Grösse bearbeitet werden.
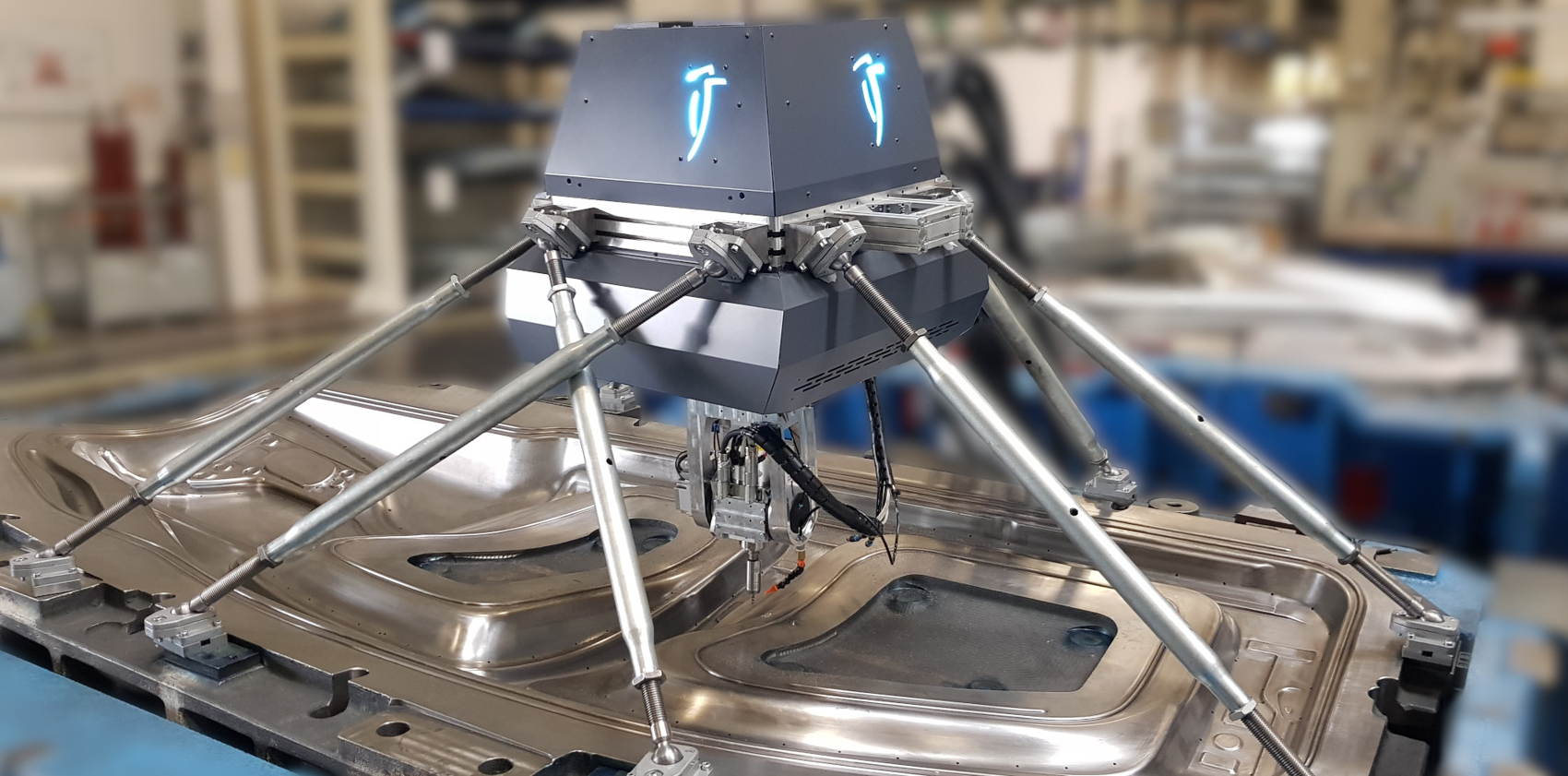
Maschinen für die skalierbare Fertigung
Wohin steuert die Entwicklung in diesem Bereich?
Die Entwicklung geht hin zur skalierbaren Fertigung. Das bedeutet, dass die Bauteilgrösse in Zukunft nur noch eine untergeordnete Rolle spielen wird. Mobile Werkzeugmaschinen ermöglichen die hochgenaue Bearbeitung von Bauteilen in jeder beliebigen Grössenskala.
Werden da Forschungsresultate vom einen auf den anderen übertragen? Von der fühlenden Werkzeugmaschine also auf den Werkzeugroboter und umgekehrt. Wenn ja, welche zum Beispiel?
Forschungsresultate werden nicht nur für eine Maschine genutzt. Die Übertragbarkeit der Forschungsergebnisse auf andere Maschinen und Prozesse hat bei uns einen sehr hohen Stellenwert. Die im Zusammenhang mit der fühlenden Maschine entwickelten Methoden zur Ermittlung von Kräften im Prozess und zur Prozessanpassung werden teilweise auch an der mobilen Maschine eingesetzt.
Fühlende Spannelemente und fühlende Schlitten
Generell: Mit welchen Firmen arbeiten Sie im Bereich der fühlenden Maschinen zusammen?
Wir arbeiten hier unter anderem mit Werkzeugmaschinenherstellern, Spannmittelherstellern, Herstellern von Sensorik sowie mit Betrieben, die weitere Komponenten für Werkzeugmaschinen fertigen, zusammen. Dürfen die Firmen die Forschungsresultate übernehmen und sie in die eigenen Maschinen integrieren? Ja, uns ist es sehr wichtig, unsere Forschungsergebnisse auch in die Industrie zu bringen und für Unternehmen anwendbar zu machen. Mit unseren Forschungsarbeiten legen wir die Grundsteine für die industrielle Anwendung.
Sehen wir denn bereits die Resultate im Markt oder werden in Kürze welche kommen?
Bereits heute sind die in Hannover entwickelten fühlenden Komponenten bei einigen Unternehmen erfolgreich im Einsatz. Beispielsweise setzt die DMG Mori AG auf die Kompensation von Formfehlern mit Hilfe eines «fühlenden Schlittens» und die Firma Römheld nutzt fühlende Spannelemente zur Zustandsüberwachung. Weitere nationale und internationale Technologiepartner sind beispielsweise die Berg & Co. GmbH und das Korea Institute of Machinery and Materials. Eingesetzte Komponenten sind sensorische Spannsysteme für die Werkstückspannung oder fühlende Führungswagen.
Dieser Artikel erschien exklusiv in unserem Printmagazin, Ausgabe #009
Printmagazin TECHNIK und WISSEN, Ausgabe #009
Impressum
Autor: Eugen Albisser, Chefredaktor Online
Bildquelle: IFW, Leibniz Universität Hannover
Eine Publikation von «Technik und Wissen»
Informationen
Instituts für Fertigungstechnik und Werkzeugmaschinen (IFW)
Leibniz Universität Hannover
ifw.uni-hannover.de
Weitere Artikel
Veröffentlicht am: