Prozessintegration, Automation sowie Digitale Transformation (DX) und Grüne Transformation (GX): Auf der Hausausstellung 2024 in Pfronten feiert DMG Mori den traditionellen Auftakt ins Veranstaltungsjahr mit neuen Lösungen für die Machining Transformation (MX).
Prozessintegration, Automation sowie Digitale Transformation (DX) und Grüne Transformation (GX): Auf der Hausausstellung 2024 in Pfronten feiert DMG Mori den traditionellen Auftakt ins Veranstaltungsjahr mit neuen Lösungen für die Machining Transformation (MX).
Redaktionelle Bearbeitung: Technik und Wissen
Zu den Highlights der Ausstellung gehören die Weltpremiere DMF 400|11 als perfektes Beispiel für die Prozessintegration und das PH Cell 500 als Innovation im Bereich der modularen Palettenhandlings. Ein weiteres Highlight ist Celos X. Das ganzheitliche digitale und datenbasierte Ecosystem schafft zusätzliche Potenziale in der Optimierung von Fertigungsprozessen. Der Lasertec Showroom komplettiert das technologische Leistungsspektrum mit effizienten Produkten für das Additive Manufacturing, während die Academy Area Einblicke in das umfangreiche Aus- und Weiterbildungsangebot von DMG Mori bietet.
MX – Machining Transformation
Nachhaltige Prozessoptimierung für eine zukunftssichere Fertigung
«The Home of Innovation steht auf den vier Säulen Prozessintegration, Automation, Digitale Transformation (DX) und Grüne Transformation (GX)», blickt Irene Bader, Member of the Board der DMG Mori Company Limited auf die kommende Hausausstellung in Pfronten. «Diese Säulen bilden das Fundament für die Machining Transformation (MX), mit der wir unsere Kunden auf dem Weg hin zu einer zukunftsorientierten Produktion unterstützen.» Das übergeordnete Ziel bestehe darin, Fertigungsprozesse effizienter und nachhaltiger zu gestalten, um im globalen Wettbewerb langfristig erfolgreich zu bleiben.
Die Prozessintegration reduziert Durchlaufzeiten und Umspannvorgänge, indem immer mehr Technologien in einem Arbeitsraum vereint werden. In Pfronten wird DMG Mori zeigen, wie sich Drehen, Fräsen, Schleifen und Verzahnen ebenso in einer Aufspannung durchführen lassen wie das In-Prozess-Messen für eine durchgängige Qualitätskontrolle. Produktivitätssteigernde und flexible Automationslösungen, sowohl für die Serienfertigung als auch die Herstellung von kleinen Losgrössen, werden ebenfalls zu sehen sein. Darüber hinaus demonstriert DMG Mori Lösungen in der Digitalen Transformation (DX). Sie unterstützen die Prozessoptimierung zusätzlich – von der Auftragsplanung über die Programmierung bis hin zur Qualitätskontrolle und Dokumentation. Vor dem Hintergrund von Ressourcenknappheit und Klimaschutzzielen zahlen diese drei Säulen auf die vierte Säule, die Grüne Transformation (GX) ein. Massnahmen zur Energieeinsparung von mehr als 30 Prozent, die Nachrüstung von Automationslösungen und die Maschinenüberholung schaffen neue Potenziale, die Produktivität ressourcenschonend zu steigern.
Weltpremiere: DMF 400|11
Erweiterung der DMF-Baureihe in eine neue Dimension
Die DMF 400|11 von DMG Mori vereint das erfolgreiche Konzept der neuen Fahrständerbaureihe mit einem Arbeitsraumvolumen von 4,7 m³.
Mit den von Grund auf neu entwickelten DMF 200|8, DMF 300|8 und DMF 300|11 hat DMG Mori in den vergangenen Jahren seine Innovationskompetenz mehrfach unter Beweis gestellt. Basierend auf diesem wegweisenden Fahrständerkonzept präsentiert der Werkzeugmaschinenhersteller nun auch das grösste Modell der Baureihe, die DMF 400|11.
Im Vergleich zum Vorgängermodell DMF 360|11 überzeugt die Weltpremiere mit einem um 400 mm vergrösserten X-Weg und 150 mm mehr in der Z-Achse. Die massive Konstruktion resultiert aus dem gusseisernen Maschinenbett, drei Linearführungen in der X-Achse sowie geschliffenen und gekühlten Kugelgewindetrieben. Damit ist die Fahrständermaschine der perfekte Begleiter in der Bearbeitung anspruchsvoller Grossbauteile – von Strukturbauteilen über lange Träger bis hin zu Komponenten für den Werkzeug- und Formenbau.
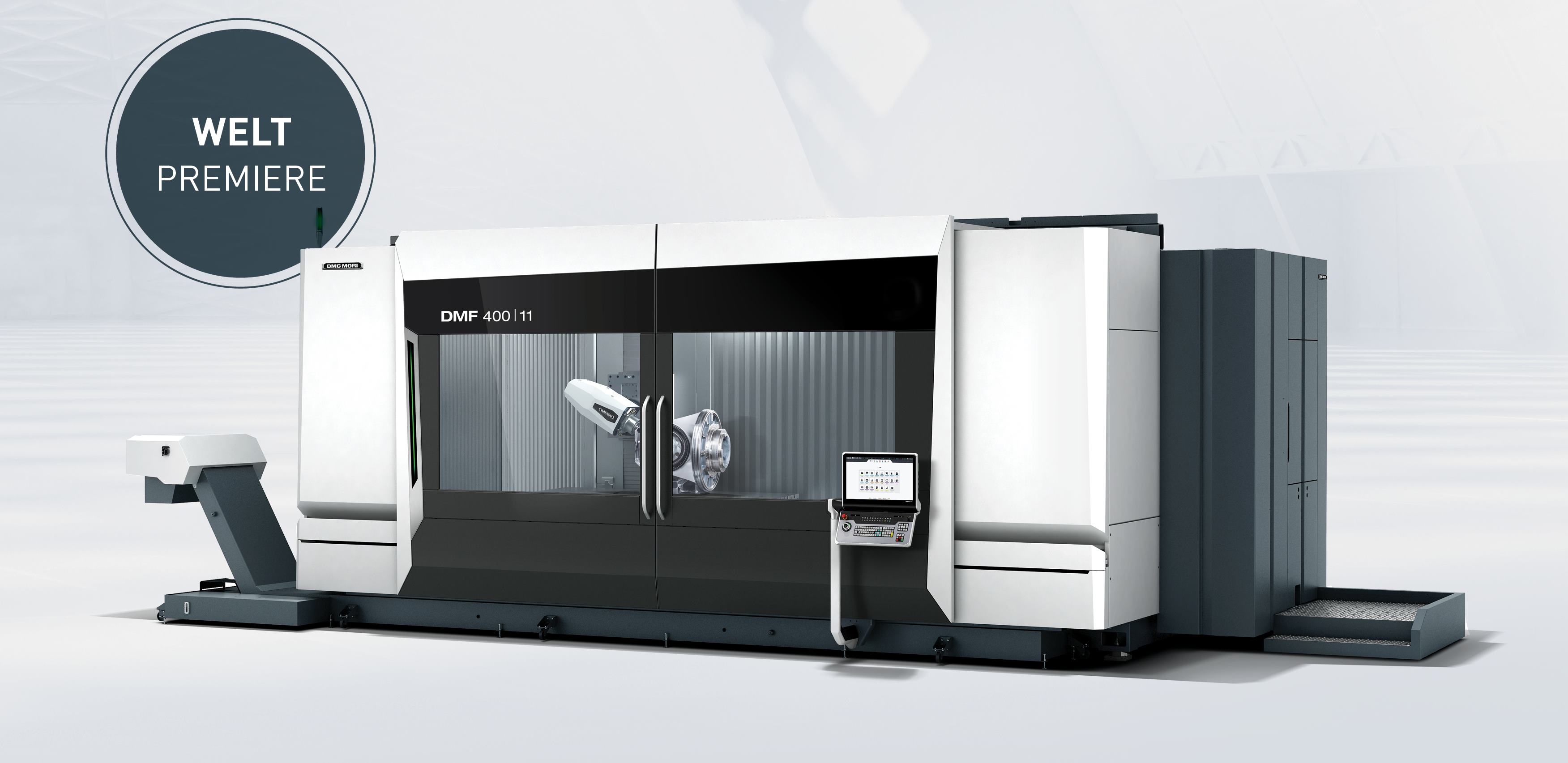
Für die Bearbeitung langer Bauteile sind die Fahrständermaschinen von DMG Mori seit jeher die richtige Wahl. Mit Verfahrwegen von 4000 × 1100 × 1050 mm bietet die DMF 400|11 viele Möglichkeiten in der universellen Zerspanung. Die optionale, schnell zu integrierende Trennwand teilt den Bearbeitungsraum in zwei separate Arbeitsräume, die das hauptzeitparallele Rüsten von Bauteilen ermöglichen. Dies schafft eine Alternative zu einer Maschine mit Palettenwechsler, verbunden mit der hohen Flexibilität zur Bearbeitung von langen Bauteilen. Der Starrtisch ist im Standard für Werkstücke mit bis zu 8.000 kg ausgelegt. Optional kann DMG Mori einen oder zwei Rundtische für jeweils 1.200 kg schwere Bauteile integrieren. Die Maschine lässt sich mit verschiedensten Typen und Grössen von Teilapparaten und Aufsatztischen als A-Achse kombinieren. Der modulare Baukasten wird durch einen FD-Rundtisch für anspruchsvolle Fräs-Dreh-Operationen ergänzt, womit sich die DMF 400|11 perfekt für die Prozessintegration eignet und die Machining Transformation (MX) vorantreibt.
Aus diesen Optionen ergibt sich eine enorme Bearbeitungsvielfalt. Die DMF 400|11 ermöglicht eine 5-achsige Bearbeitung von Werkstücken mit bis zu ø 1400 × 1000 mm und 1200 kg sowie die mehrseitige Bearbeitung von bis zu 4600 mm langen Bauteilen. Zudem bietet DMG Mori grössere Werkzeugmagazine mit bis zu 120 Plätzen an. Im Standard fasst das Magazin 40 Werkzeuge mit einer Länge von bis zu 400 mm. Der Werkzeugwechsel wird hinter dem Arbeitstisch durchgeführt – ein besonderes Merkmal der jüngsten DMF-Generation von DMG Mori. Dies verleiht der DMF 400|11 eine hohe Prozesssicherheit. Zudem liegen die Linearführungen ausserhalb des Arbeitsraums, was sie vor abrasiven Werkstoffen schützt und zur Langlebigkeit der Komponenten beiträgt.
Präzision und Dynamik bei allen Anwendungen
Ein Highlight des innovativen Fahrständerkonzepts von DMG Mori – und somit auch der DMF 400|11 – ist die konstant auskragende Y-Achse. Sie verleiht der Maschine eine gleichbleibende Steifigkeit über den gesamten Verfahrweg. Dadurch können Anwender – unabhängig von der Spindelposition – jederzeit die maximale Spindelleistung abrufen. Umfangreiche Kühlmassnahmen im Standard gewährleisten eine hohe thermische Langzeitgenauigkeit. Die DMF 400|11 verfügt über einen Lineartrieb in der X-Achse sowie über innengekühlte und geschliffene Kugelgewindetriebe in der Y- und Z- Achse. Dies sorgt für beste Oberflächengüten am zu bearbeitenden Bauteil. Das optional erhältliche Dynamikpaket steigert nochmals die Performance der Maschine durch erhöhte Beschleunigungen mit bis zu 6 m/s² und Eilgängen mit bis zu 80 m/min in der X-Achse.
Die optimierte B-Achse der DMF 400|11 hat ein schrägverzahntes Getriebe und eine verbesserte Klemmung mit 6000 Nm. Dies entspricht einer Steigerung von 60 Prozent zur Vorgängermaschine. Zur Grundausstattung gehört die integrierte Speedmaster Spindel mit 15'000 min-1. Alternativ ist eine Speedmaster Spindel mit 20‘000 min-1 verfügbar. Ausserdem kann die DMF mit der neu entwickelten SK 50 / HSK-A100 Powermaser Spindel von DMG Mori mit 12'000 min-1 und einem Drehmoment von bis zu 430 Nm ausgestattet werden. Wie für alle MASTER Spindeln gilt auch hier eine laufzeitunabhängige Gewährleistung über 36 Monate. Mit der HSK-A100 Schnittstelle und einer damit verbundenen Werkzeuglänge von 540 mm und maximal 20 kg, lässt sich die Zerspanleistung der Maschine nochmals steigern.
Optimale Ausstattung für eine zukunftssichere und flexible Fertigung
Die DMF 400|11 lässt sich problemlos in digitale Infrastrukturen einbinden, was die Investition absolut zukunftssicher macht. Exklusive DMG Mori Technologiezyklen steigern darüber hinaus die Produktivität in der Bearbeitung, beispielsweise durch die problemlose Programmierung von frei schwenkbaren Winkelköpfen mittels AngularTool. Noch produktiver wird die Fertigung auf der DMF 400|11 mit Hilfe von Automationslösungen. Hierfür hat DMG Mori bereits entsprechende Schnittstellen, beispielsweise für den Einsatz von Roboterhandlings, integriert.
INH 63 und INH 80
Horizontale Bearbeitungszentren für mehr Produktivität, Präzision und ökologische Nachhaltigkeit
Als horizontale Bearbeitungszentrum der Extraklasse verbinden die INH 63 und INH 80 von DMG Mori Mechatronik, Machining Transformation (MX) und eine ressourcenschonende CNC-Fertigung.
Die neuen horizontalen Bearbeitungszentren INH 63 und INH 80 von DMG Mori setzen Massstäbe in der Horizontalbearbeitung. Im Zusammenspiel mit Machining Transformation (MX) von DMG Mori unterstützen die beiden Modelle Anwender auf dem Weg in eine nachhaltige, effiziente und wettbewerbsfähige Zukunft der CNC-Fertigung. Konzipiert sind die Horizontalbearbeitungszentren für anspruchsvolle Bauteile im Werkzeug- und Formenbau sowie im Energie- und Greentech-Sektor – darunter beispielsweise Antriebstechnik für die Elektromobilität. Auch komplexe Teile für den Aerospace-Sektor stehen im Fokus.
Die INH 63 kann 630 mm grosse Paletten handhaben, während die INH 80 für 800 mm grosse Paletten ausgelegt ist. Mit ihrer Stabilität, Präzision und Bearbeitungsvielfalt – sie sind als 5-achsige Ausführung erhältlich – fungieren die beiden Maschinen auf allen Ebenen der Machining Transformation als perfekte Grundlage. Sie erlauben einen hohen Grad an Prozessintegration, lassen sich flexibel automatisieren und sind optimal für die digitale Transformation vorbereitet.
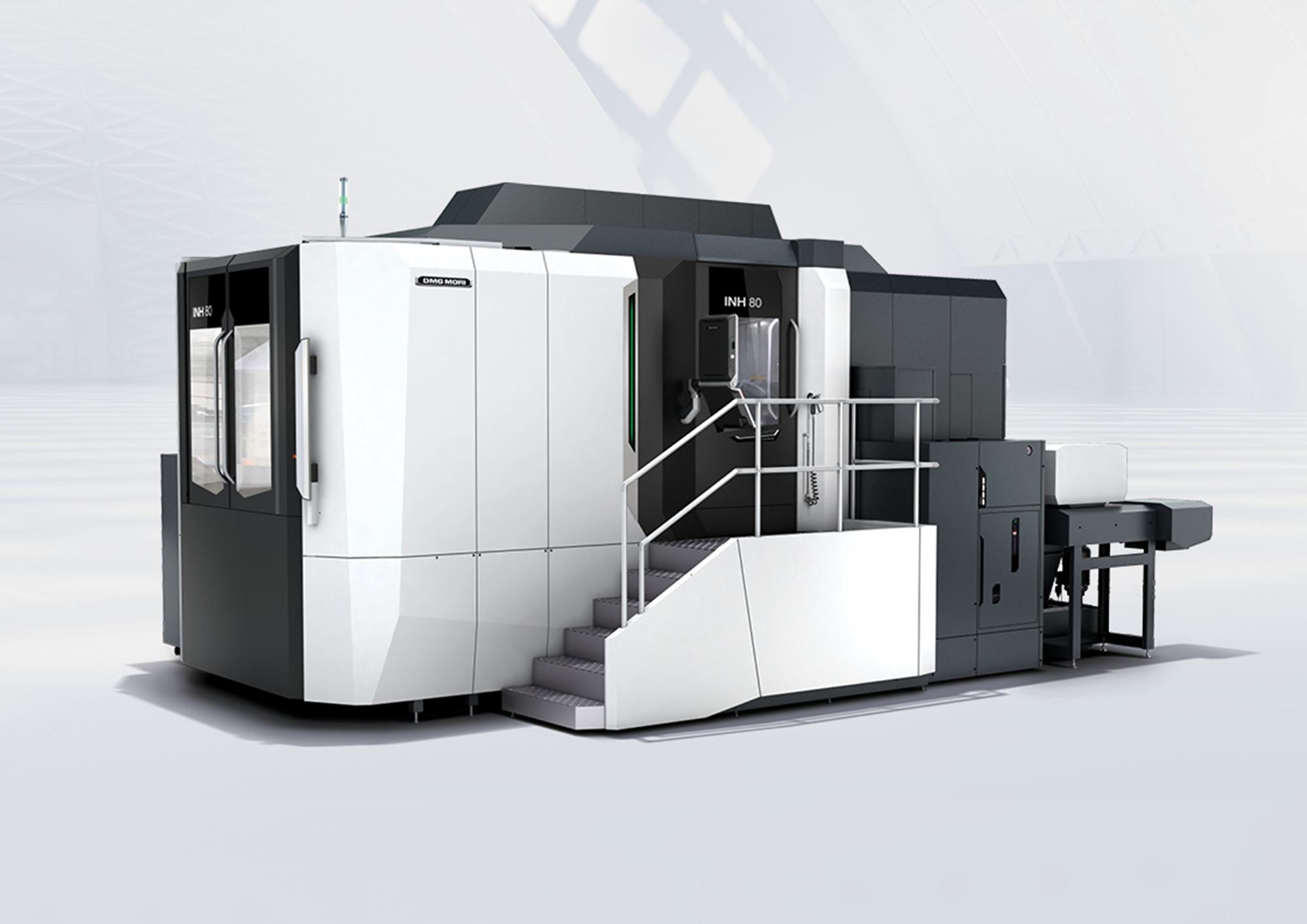
Eine symmetrische, FEM-optimierte Struktur, Twin-Kugelumlaufspindeln in den X-, Y- und Z-Achsen sowie der abgesetzte X-Schlitten im Rahmenständer verleihen der INH 63 und INH 80 ihre hohe Stabilität und erlauben eine dynamische Bearbeitung. Die nötige Präzision gewährleisten Twin-Messsysteme von Magnescale sowie die zuverlässige Kühlung der Kugelgewindetriebe und anderer Wärmequellen. Diese minimieren thermische Verschiebungen und Veränderungen in der Maschinenstruktur. Beide Horizontalbearbeitungszentren zeichnen sich zudem durch ihre breiten Achsbereiche aus, was eine effiziente Spanabfuhr sicherstellt. Die INH 63 und INH 80 überzeugen von der Leichtzerspanung bis in den Hochlastbereich. Im Standard verfügen sie über ein Powermaster Spindeln mit 12'000 min-1 Drehzahl und 808 Nm Drehmoment. Optional sind Spindeln mit bis zu 16‘000 min-1 bzw. mit 1'414 Nm Drehmoment (8'000 min-1). In allen drei Fällen gilt eine lange Gewährleistung von 36 Monaten ohne Laufzeitbegrenzung.
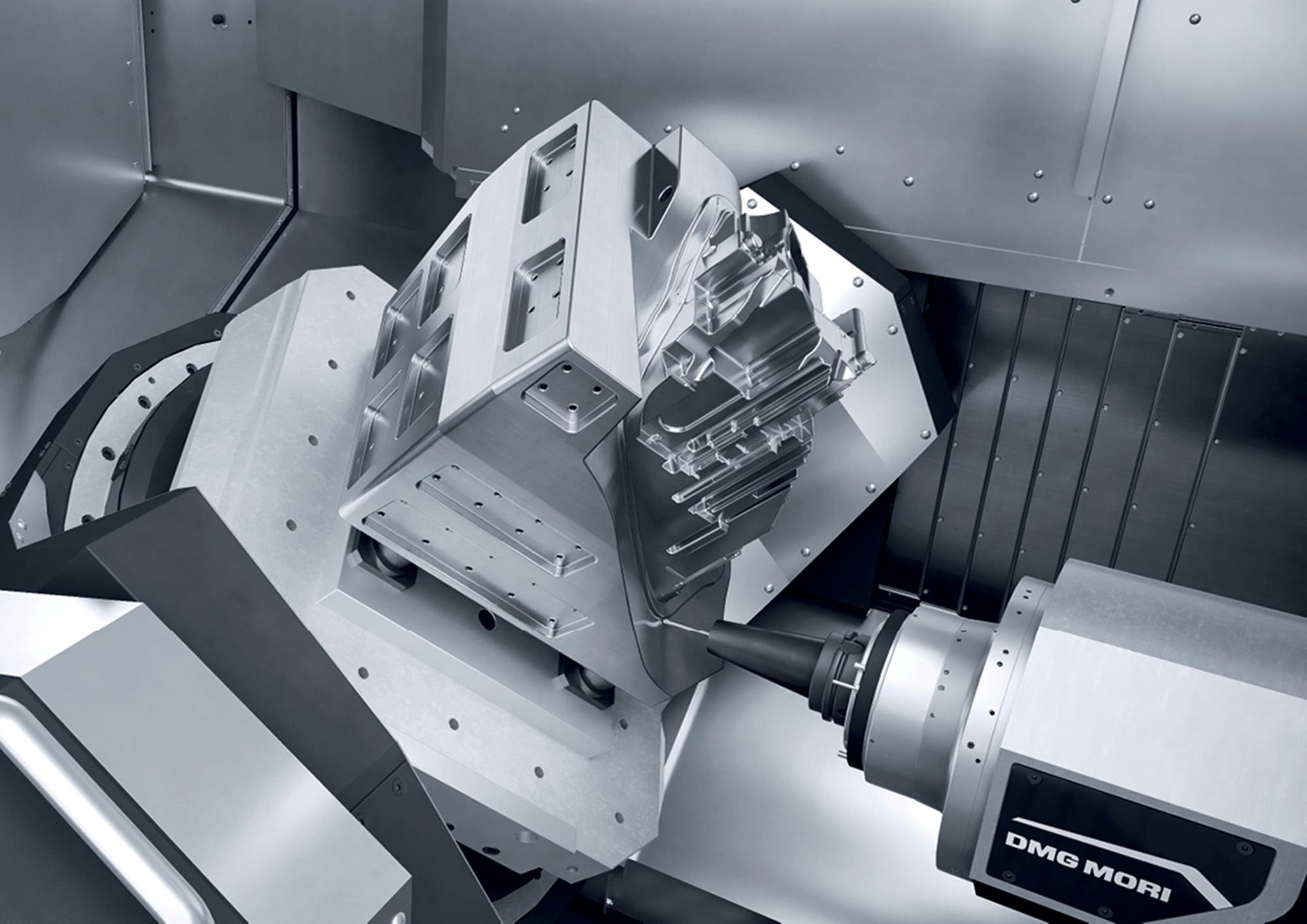
Ergonomie und Bearbeitungsvielfalt
In der 5-Achs-Ausführung der neuen INH Bearbeitungszentren verfügt der Schwenk-Rundtisch mit gross dimensionierten Lagern und zwei Hochleistungs-Torquemotoren als A-Achse. Das eliminiert das Umkehrspiel und gewährleistet maximale Präzision. Der ergonomisch zugängliche Arbeitsraum ist so gross dimensioniert, dass er selbst ausladenden Werkzeugen ausreichend Platz bietet. Mit der Möglichkeit, negative Winkeln zu bearbeiten, erfüllen die INH 63 und INH 80 eine essenzielle Anforderung im Werkzeug- und Formenbau. Der Tisch lässt sich ausserdem komplett auf 180° durchschwenken. Dies ermöglicht Bearbeitungen «über Kopf» und schafft insbesondere für den Einsatz der Fräs-Dreh-Technik immense Vorteile.
Ganzheitliche Innovationen für die Machining Transformation (MX)
Die INH 63 und INH 80 sind gute Beispiele für den starken Fokus, den DMG Mori in Form der Machining Transformation (MX) auf nachhaltigen Fortschritt legt. Prozessintegration, Automation, Digitale Transformation (DX) und Grüne Transformation (GX) sind hierbei tragende Säulen. Ihre sich verstärkende Wechselwirkung zeigt deutlich, dass Nachhaltigkeit und betriebliche Exzellenz keineswegs gegensätzliche Ziele sind, sondern erfolgreich Hand in Hand gehen können. So verkürzt die Integration unterschiedlicher Fertigungsprozesse in einer Maschine – Drehen, Fräsen und weiteren Verfahren wie Messen oder Verzahnen – die Prozesskette. Rüstzeiten werden reduziert, während die Qualität steigt.
In Summe steigt die Ressourceneffizienz, was zur Nachhaltigkeit beiträgt. Eingebunden in flexible Fertigungszellen und -systeme arbeiten die INH 63 und INH 80 auch unbeaufsichtigt über bis zu drei Schichten. Automatisiertem Werkzeug- bzw. Palettenhandlings und der intelligente Leitrechner Cell Controler LPS 4 erhöhen die produktiven Spindelstunden gegenüber der Stand Alone-Installation von 2'000 auf über 6'000 pro Jahr. Die Ausstattung mit digitalen Technologien erlaubt zudem eine Einbindung in ganzheitliche Produktionssysteme. Unmittelbare Auswirkung auf die Grüne Transformation (GX) hat darüber hinaus der Greenmode. Er reduziert den Energieverbrauch der Maschinen um über 30 Prozent und optimiert gleichzeitig die Ressourcennutzung.
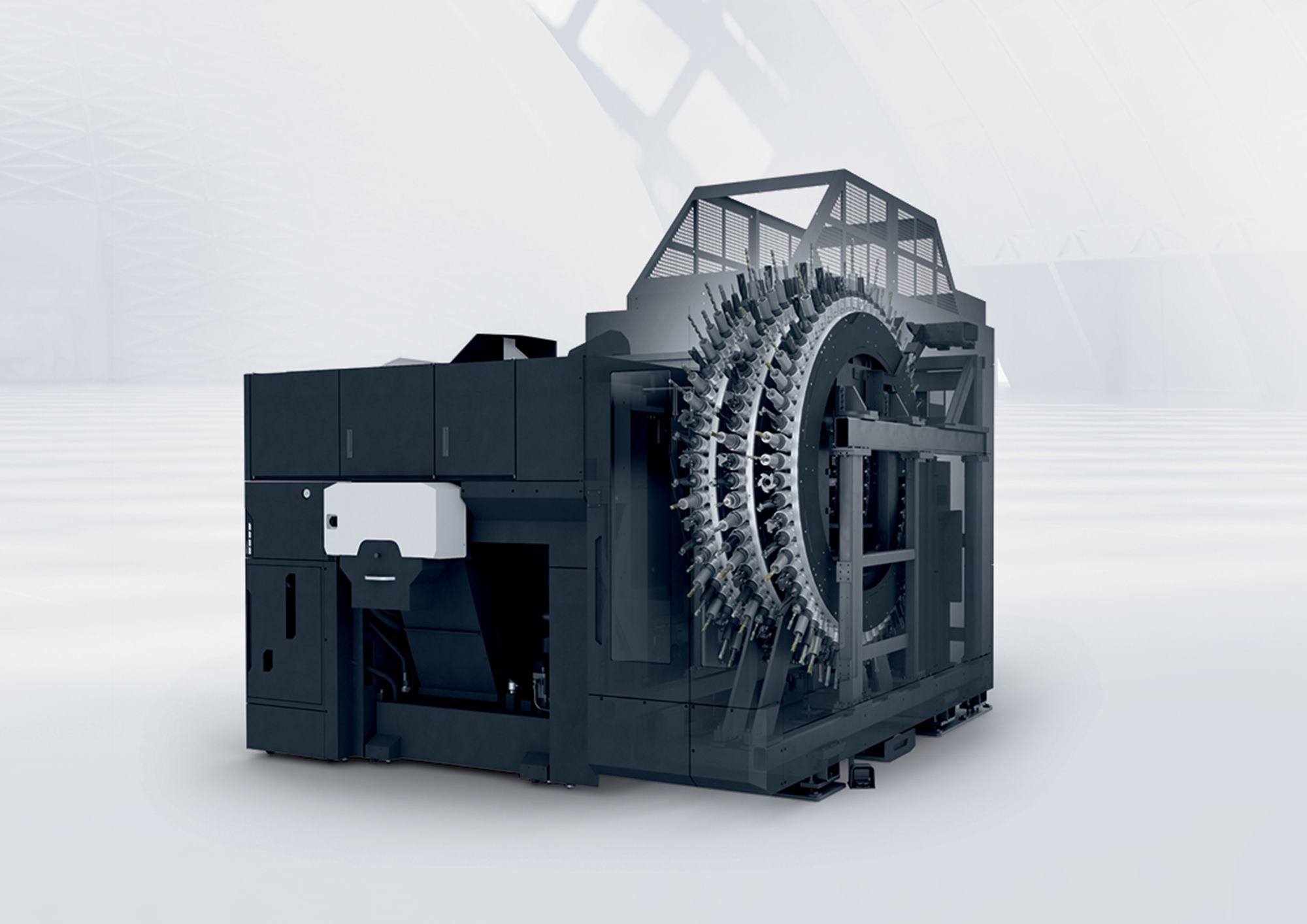
Am Beispiel eines hochpräzisen spiralförmigen Kegelrads für industrielle Windkraftanlagen demonstriert die INH-Baureihe ihr Leistungsvermögen mit Blick auf Effizienz und Nachhaltigkeit. Das Getriebeelement ist aus robustem Stahl und misst ø 482 × 66 mm. Durch die Integration von Fertigungsprozessen wie dem 5-Achs-Fräsen, dem Verzahnen und dem In-Prozess-Messen in einem Arbeitsraum sind beiden Horizontalbearbeitungszentren in der Lage, das Kegelradgetriebe in einer einzigen Aufspannung komplett zu fertigen. Der Transport zwischen den zuvor separaten Bearbeitungsstationen entfällt. Das spart Liegezeiten und steigert gleichzeitig die Präzision. Denn jede Neupositionierung schafft Raum für potenzielle Fehler.
Einen grossen Anteil an der Komplettbearbeitung hat das Verzahnen mit Standardwerkzeugen. Die 5-Achs-Performance kombiniert mit den jeweiligen DMG Mori Technologiezyklen ermöglichen Verzahnungsprozesse wie Schruppen und Schlichten auf Standardmaschinen. Spezialisierte und damit teure Einzweck-Verzahnungssysteme sind nicht erforderlich. Hinsichtlich der Digitalen Transformation (DX) sorgen 1:1-Simulation und die begleitende Analyse von Prozessdaten für eine optimale Maschinenauslastung. Dies reduziert das Risiko von Maschinenstillständen und sorgt für eine höhere Energieeffizienz. Pro Bauteil lassen sich bis zu 80 Prozent des Stromverbrauchs einsparen.
In Summe zeigt dieser Anwendungsfall, dass die INH-Baureihe alle Elemente der Machining Transformation in sich vereint und auf Zukunftsmärkte wie die Windkraft anwendet. Die INH 63 und INH 80 verbinden ökonomische Effizienz mit ökologischer Weitsicht und schaff so ein Vorbild für den Werkzeugmaschinenbau der Zukunft.
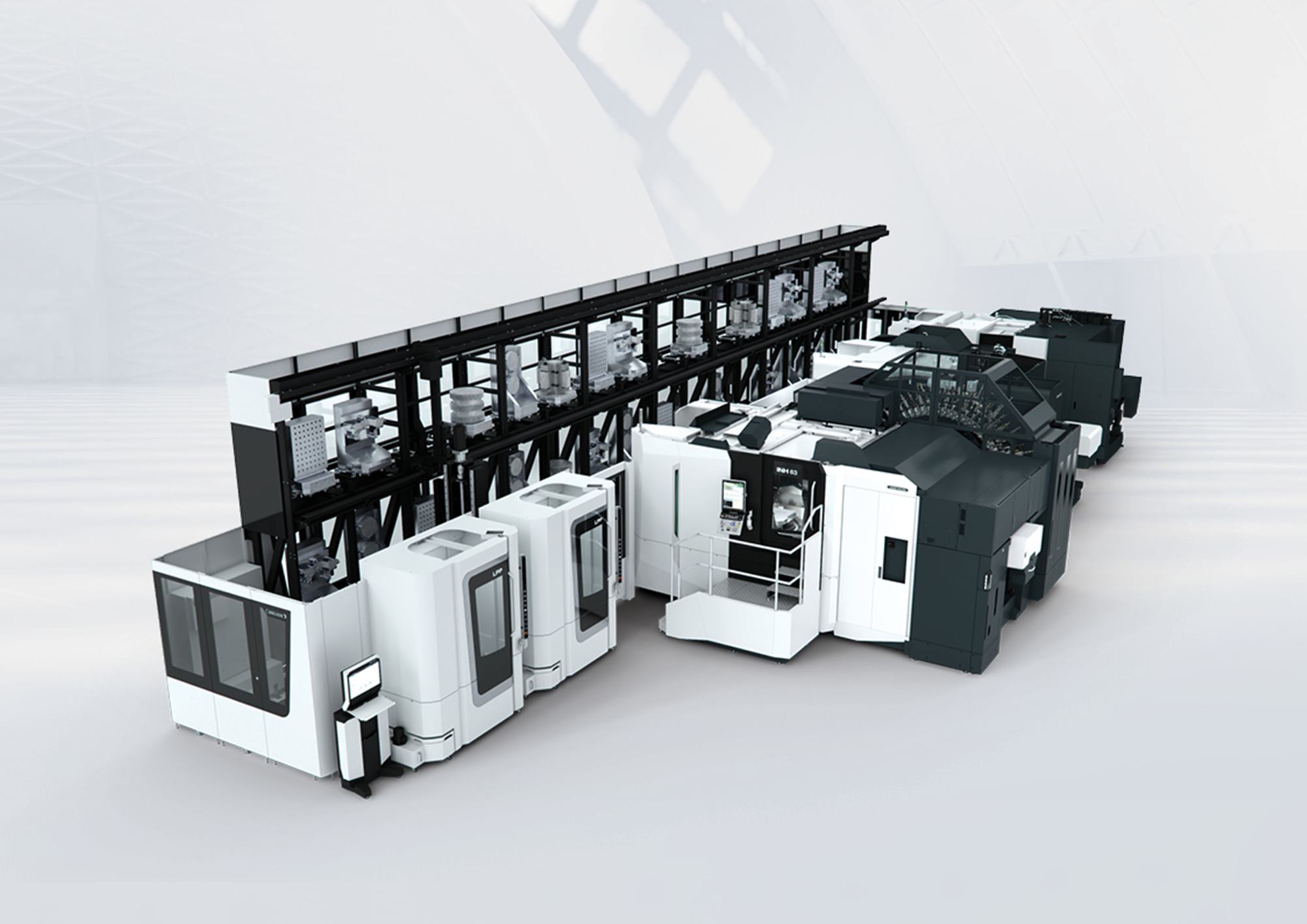
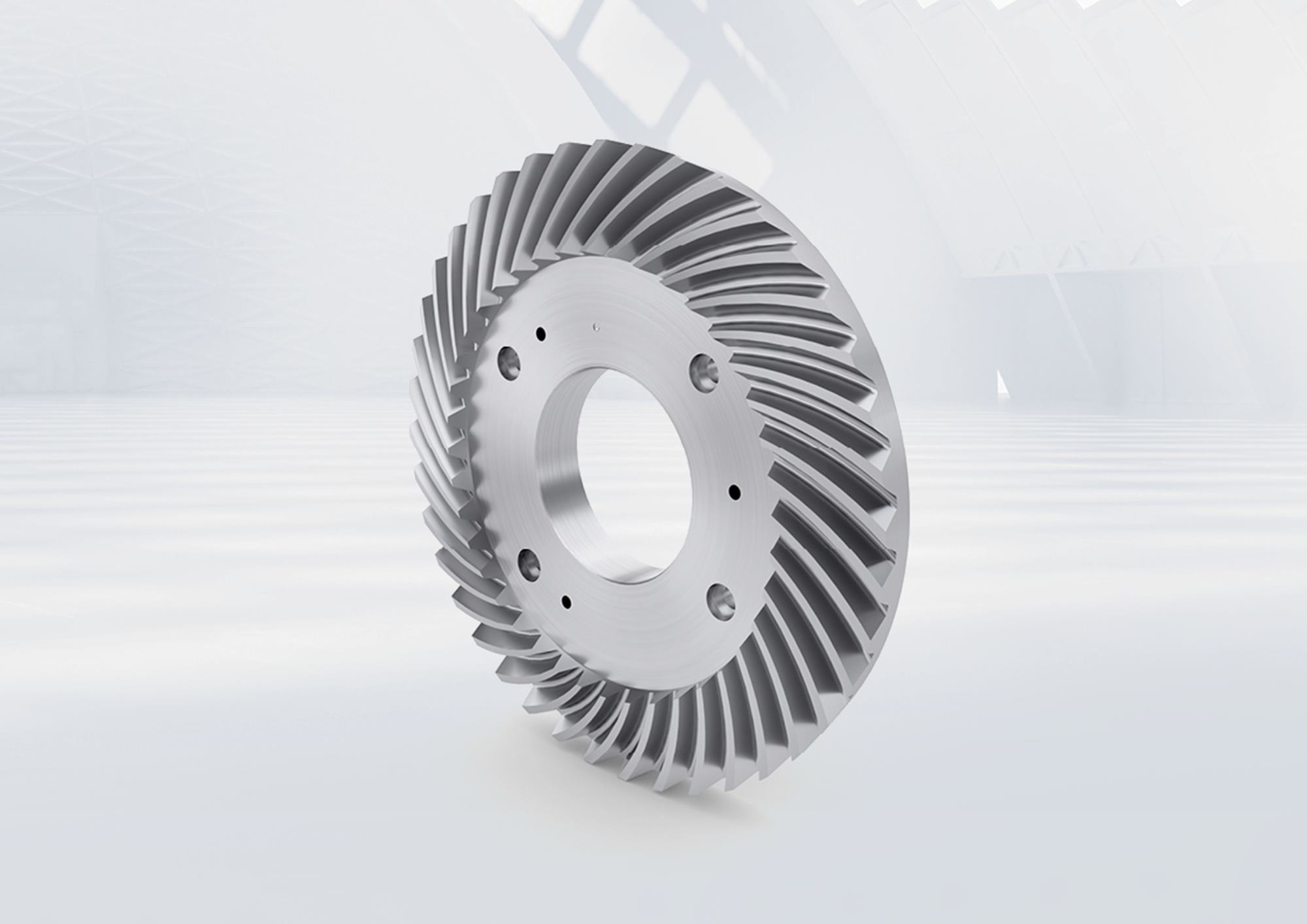
PH Cell 500
Modulares Palettenhandling mit bis zu 500 kg Transfergewicht
Hohe Steifigkeit, Maschinenpaletten aus Stahl inklusive der bewährten Spannkonentechnologie – optimiert für das Handling von Paletten bis 500 × 500 mm bietet das PH Cell 500 dieselben Vorteile wie das grössere PH Cell 800 bei einer gleichzeitig kompakteren Bauweise.
Mit dem PH Cell 500 erweitert DMG Mori die Baureihe der modularen Palettenhandlingsysteme um ein kompaktes Modell für bis zu 500 kg Transfergewicht. Es ist kompatibel sowohl zur DMU 65 und DMU 75 Monoblock 2nd Generation als auch zur DMU 65 H Monoblock. Je nach Konfiguration der Regalmodule bietet das PH Cell 500 Platz für bis zu 32 Paletten. Die maximalen Werkstückabmessungen liegen bei 500 × 500 × 750 mm. Das Transfergewicht beträgt 500 kg. Wie die anderen Modelle der Baureihe ist auch das PH Cell 500 ergonomisch und dank der Pallet Master Software leicht bedienbar.
«Durch die konsequente Weiterentwicklung seiner Palettenhandlingsysteme unterstreicht DMG Mori den hohen Stellenwert der Automation als feste Säule in der Machining Transformation», erklärt Cornelius Nöss, Geschäftsführer Deckel Maho Pfronten, den Fokus auf Produkte wie das PH Cell 500. Die neue Palettenautomation ermöglicht eine hochflexible automatisierte Fertigung von kleinen Losgrössen und Einzelteilen. Grund dafür ist die Modularität des Systems, die eine kundenindividuelle Konfiguration ermöglicht. In der Praxis lassen sich mit dem PH Cell 500 die Spindelstunden um bis zu 300 Prozent erhöhen und die Stückkosten um 50 Prozent senken.
Im Standard wird das PH Cell 500 mit einem Regalmodul ausgeliefert. Ausgestattet mit drei Regalböden bietet es Platz für zwölf 400 × 400 mm oder neun 500 × 500 mm grosse Paletten. In der Version mit vier Regalböden finden 16 der kleineren oder zwölf der grösseren Paletten Platz. Eine Kombination unterschiedlicher Palettengrössen ist ebenfalls möglich. Das PH Cell ist nachrüstbar, wenn die Maschine über eine Automationsvorbereitung verfügt. Gleiches gilt für die Erweiterung des Palettenhandlingsystems um ein zweites Regalmodul. So gewährleistet DMG Mori jederzeit – auch im Nachhinein – eine bedarfsgerechte Konfiguration, die den Produktionsanforderungen gerecht wird.
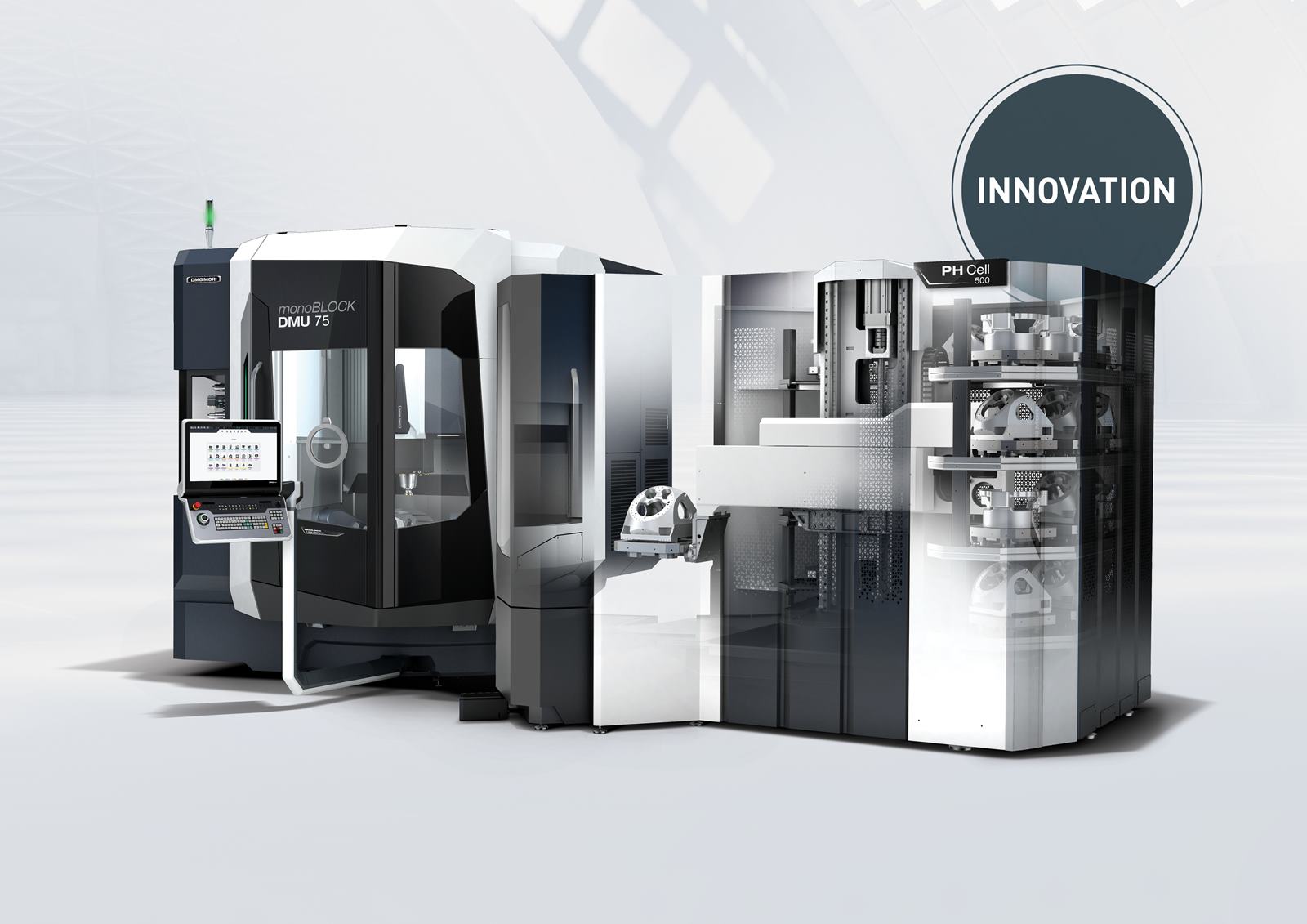
Zuverlässigkeit und ergonomische Bedienung
Wie das PH Cell 800 hat DMG Mori auch das PH Cell 500 stabil konstruiert. Da hier ebenfalls Maschinenpaletten aus Stahl zum Einsatz kommen, wird das integrierte Spannkonensystem im Maschinentisch genutzt. Das heisst, es wird keine Nullpunktspannstation auf dem Maschinentisch benötigt und gleichzeitig ist der Spänefall besser. Eine ergonomische Bedienung gewährleisten der drehbare Rüstplatz im Standard sowie die separate Bedienung der Pallet Master Software per Touchscreen.
Celos X
Zukunftssichere Lösung für Unternehmen in der Fertigung
Auf der diesjährigen DMG Mori Hausausstellung in Pfronten wird Celos X als fortschrittlichste Technologie der Digitalen Transformation (DX) vorgestellt. Damit unterstützt Celos X Anwender dabei, die Machining Transformation (MX) zu realisieren. Rund zehn Jahre nach der Einführung von Celos als weltweit erste App-basierte Maschinensteuerung revolutioniert DMG Mori die Fertigungstechnik erneut – dieses Mal noch tiefgreifender und umfassender. So ebnet Celos X den Weg in die fertigungstechnische Zukunft.
DMG Mori verfolgt mit Celos X einen ganzheitlich-kundenorientierten Innovationsansatz. Im Ergebnis umfasst das Celos X Ökosystem ein stetig wachsendes Bündel an digitalen Produkten und Applikationen sowie datenbasierten Services. Damit bietet es eine einzigartige Durchgängigkeit über alle Steuerungsvarianten von DMG Mori. Celos X besteht aus den beiden Komponenten Celos Xperience und Celos Xchange. Celos Xperience dient als unmittelbare Interaktionsebene der Anwender mit Applikationen und Softwaresystemen. Mit der cloudbasierten Celos Xchange Plattform schafft DMG Mori einen zentralen und sicheren Datenraum für die durchgängige Integration des Shopfloors. In den
Wechselwirkungen seiner Funktionen und Fähigkeiten bietet Celos X eine einzigartige Nutzererfahrung und nahtlose digitale Interoperabilität. Celos X überzeugt dabei mit einer grossen Funktionsvielfalt, Performance und Durchgängigkeit. Konkret sind damit die Inhalte von Celos X auf allen angebotenen Steuerungstypen in nahezu gleichem Umfang vorhanden.
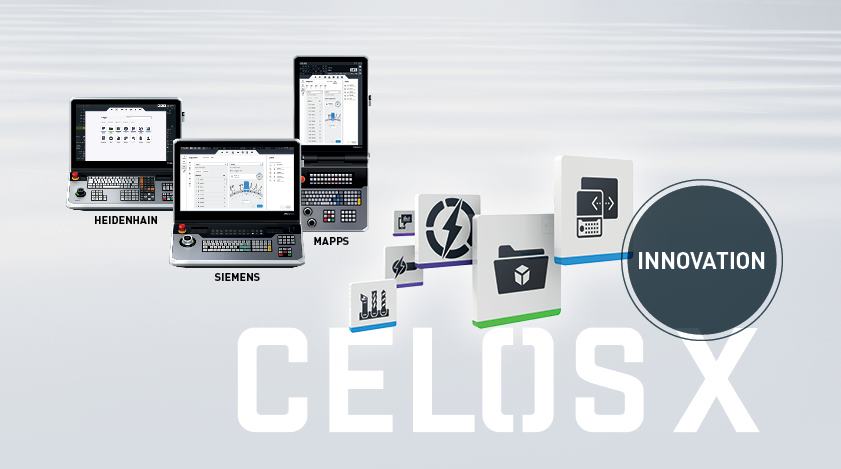
Celos Xchange: Die zentrale Datenplattform – sicher, skalierbar, offen
Celos Xchange fungiert als multifunktionale Schaltzentrale des Celos X Ökosystems und orchestriert im Besonderen das gesamte Applikations- und Datenmanagement auf der Ebene der Celos Xperience. «Als cloudbasierter Datenraum ermöglicht
Celos Xchange überdies die bidirektionale Integration der fertigenden Werkstatt in die Unternehmens-IT sowie perspektivisch den offenen und sicheren Datenaustausch mit Partnern entlang von Lieferketten und innerhalb globaler Wertschöpfungsnetzwerke», erklärt Dr. Tommy Kuhn, Geschäftsführer DMG Mori Digital GmbH. Insbesondere beeindruckt Celos Xchange in Kombination mit der standardisierten Maschinenkonnektivität von DMG Mori mit einer hohen Skalierbarkeit und der Interoperabilität zu Fremdmaschinen sowie Partnerapplikationen. Sicherheit und Datensouveränität stehen dabei an erster Stelle. Der Kunde bestimmt zu jeder Zeit, welche Daten mit Celos Xchange synchronisiert werden. Zudem wird hier die Basis für den Zugriff auf aktuelle Neu- und Weiterentwicklungen gelegt.
Effizienter Zugriff auf Fertigungsinformationen: Celos Xchange bietet eine zentrale Datenplattform für die Erfassung, Aggregation und Nutzung von Fertigungsdaten. Unternehmen können ihre Produktionsdaten an einem Ort speichern und verwalten, was die Effizienz und den Zugriff auf relevante Informationen verbessert.
Kommunikation über Systemgrenzen hinweg: Celos Xchange schafft die Möglichkeit der bidirektionalen Integration der Fertigungswerkstatt in die Unternehmens-IT. Dadurch können Unternehmen ihre Fertigungsprozesse nahtlos mit anderen Systemen und Softwarelösungen, wie ERP oder CAD/CAM, verbinden und die reibungslose Kommunikation und Datenübertragung gewährleisten.
Horizontale Integration: Celos Xchange öffnet die Perspektive auf einen offenen und sicheren Datenaustausch mit Partnern entlang der Lieferkette und innerhalb globaler Wertschöpfungsnetzwerke. Unternehmen können Daten über den zugehörigen Datenraum sicher teilen und die Zusammenarbeit mit externen Partnern optimieren.
Von Daten zum Mehrwert: Celos Xchange legt den Grundstein für die Analyse und Auswertung von Fertigungsdaten. Auf Basis der gewonnenen Erkenntnisse können Unternehmen die Leistung von Maschinen und ihren Fertigungsprozessen transparent überwachen, drohende Engpässe identifizieren und Massnahmen zur kontinuierlichen Verbesserung initiieren.
Celos Xperience: Digitaler Werkzeugkasten
Celos Xperience ist mit über 30 Apps und durchgängigen Workflows der digitale Werkzeugkasten für alle Anwendungen und Software-Systeme innerhalb des Celos X Ökosystems. Über die verfügbaren Lösungen erschliesst sich folgerichtig der ganzheitliche Kundenmehrwert von Celos X. Alle Applikationen und Workflows verfolgen das Ziel, die Maschinenbedienung zu vereinfachen, die Anzahl der Spindelstunden zu erhöhen und gleichzeitig die Energieeffizienz zu optimieren.
Intuitive Benutzeroberfläche: Celos Xperience bietet eine benutzerfreundliche und intuitive Bedienoberfläche, die es Anwendern ermöglicht, schnell und ohne CNC-spezifisches Fachwissen auf alle relevanten Informationen und Anwendungen zuzugreifen. Die nahtlose Integration von Apps und Technologiezyklen in Celos X auf der Steuerung verbessert die Effizienz und Benutzererfahrung und vereinfacht die Bedienung der Werkzeugmaschinen.
Umfassende Funktionalitäten: Celos Xperience ermöglicht eine breite Palette an Funktionalitäten, die über die Steuerung von CNC-Maschinen hinausgehen. Das Angebot reicht von der Verbesserung von Prozessen der Arbeitsvorbereitung und Wartung bis hin zum Monitoring und ist durch die No-Code-Plattform TULIP auch für kundenseitige Anwendungen offen.
Machining Transformation mit Celos X
Mit dem Start des Celos X Ökosystems gewinnt die Machining Transformation (MX) von DMG Mori nochmals an Kraft und Dynamik. Als integratives Bindeglied von der NC-Steuerung in den Datenraum von Celos Xchange und mit offener Interoperabilität vom Shopfloor in übergeordnete Systemwelten ist Celos X die Basis für die Digitale Transformation (DX). Überdies bereichert die Funktionalität und Performance von Celos X auch die drei weiteren MX-Säulen von Prozessintegration, Automation und Grüner Transformation (GX). Zusammen betrachtet erschliesst Celos X der Machining Transformation (MX) umfassende Vorteile, die sich positiv auf Produktivität, Qualität, Kosten, Arbeitsbedingungen und Flexibilität auswirken und die ökologische Nachhaltigkeit der Fertigung fördern. Celos X wird so zu einem entscheidenden Werkzeug für die Kunden von DMG Mori, um in einem wettbewerbsintensiven und sich schnell entwickelnden Marktumfeld auch in Zukunft wettbewerbsfähig zu bleiben.
Impressum
Textquelle: DMG Mori
Bildquelle: DMG Mori
Redaktionelle Bearbeitung: Technik und Wissen
Informationen
DMG Mori
www.dmgmori.com
Weitere Artikel
Veröffentlicht am: