Bild: Enrico Bossart (links) Michael Rom im Tunnel Digitalization Center bei Flums.
Im Tunnel Digitalization Center bei Flums testet Siemens seine Tunnel-Anwendungen und Automatisierungslösungen unter realen Einsatz-Bedingungen. Wieso das wichtig ist und welche Rolle dabei der digitale Zwilling spielt, erklären Michael Rom, Head of Factory Automation bei Siemens Digital Industries, und Enrico Bossart, Verantwortlicher Tunnelbranche bei Siemens Digital Industries, im Gespräch.
Von Markus Back (Text) und Damian Byland (Fotos)
Ein Tunnel ist im Prinzip nichts weiter als ein Loch, das durch den Berg getrieben wurde. Wieso braucht es also ein Tunnel Digitalization Center, kurz TDC?
Rom: Diese Frage ist berechtigt! Wir haben viele Ideen, wie sich Anwendungen im Tunnelbereich automatisieren und digitalisieren lassen. Anders als bei Maschinen liessen sich dort neue Technologien und innovative Konzepte bis anhin aber nur mit sehr hohem Aufwand installieren und testen. Mit dem TDC als Testlabor können wir nun auch Tunnellösungen ohne grossen Aufwand in einem realitätsnahen Umfeld simulieren und überprüfen. Beispielsweise können wir im TDC zeigen, wie ein Sicherheitstor mit einem Visualisierungssystem kommuniziert oder dessen Daten in die Cloud gelangen. Ein schöner Nebeneffekt ist, das zeigten die ersten Besuche mit Kunden und Fachleuten, dass die Gespräche im realen Umfeld eine sehr viel bessere Qualität haben, als wenn man gemeinsam vor einem Plan sitzt und diskutiert.
Nun dürften in der Schweiz vermutlich nicht mehr so viele neue Tunnels entstehen, geht es im TDC auch darum, Erneuerungsmassnahmen besser planen zu können?
Rom: Die Technik entwickelt sich weiter und da Tunnels regelmässig saniert werden müssen, haben wir im TDC die Möglichkeit, neue Technologien direkt im realen Umfeld zu testen. Ein Beispiel für praxisnahe Tests ist die Innenbeleuchtung von Schaltschränken, um Servicepersonal schon von Weitem informieren zu können. Ist alles in Ordnung, scheint durch die Glastür des Schaltschranks beispielsweise ein petrolgrünes Licht, bei einer Störung oder einem kaputten Bauteil dagegen ein rotes Licht.
Bild: Enrico Bossart (links) Michael Rom im Tunnel Digitalization Center bei Flums.
Im Tunnel Digitalization Center bei Flums testet Siemens seine Tunnel-Anwendungen und Automatisierungslösungen unter realen Einsatz-Bedingungen. Wieso das wichtig ist und welche Rolle dabei der digitale Zwilling spielt, erklären Michael Rom, Head of Factory Automation bei Siemens Digital Industries, und Enrico Bossart, Verantwortlicher Tunnelbranche bei Siemens Digital Industries, im Gespräch.
Von Markus Back (Text) und Damian Byland (Fotos)
Ein Tunnel ist im Prinzip nichts weiter als ein Loch, das durch den Berg getrieben wurde. Wieso braucht es also ein Tunnel Digitalization Center, kurz TDC?
Rom: Diese Frage ist berechtigt! Wir haben viele Ideen, wie sich Anwendungen im Tunnelbereich automatisieren und digitalisieren lassen. Anders als bei Maschinen liessen sich dort neue Technologien und innovative Konzepte bis anhin aber nur mit sehr hohem Aufwand installieren und testen. Mit dem TDC als Testlabor können wir nun auch Tunnellösungen ohne grossen Aufwand in einem realitätsnahen Umfeld simulieren und überprüfen. Beispielsweise können wir im TDC zeigen, wie ein Sicherheitstor mit einem Visualisierungssystem kommuniziert oder dessen Daten in die Cloud gelangen. Ein schöner Nebeneffekt ist, das zeigten die ersten Besuche mit Kunden und Fachleuten, dass die Gespräche im realen Umfeld eine sehr viel bessere Qualität haben, als wenn man gemeinsam vor einem Plan sitzt und diskutiert.
Nun dürften in der Schweiz vermutlich nicht mehr so viele neue Tunnels entstehen, geht es im TDC auch darum, Erneuerungsmassnahmen besser planen zu können?
Rom: Die Technik entwickelt sich weiter und da Tunnels regelmässig saniert werden müssen, haben wir im TDC die Möglichkeit, neue Technologien direkt im realen Umfeld zu testen. Ein Beispiel für praxisnahe Tests ist die Innenbeleuchtung von Schaltschränken, um Servicepersonal schon von Weitem informieren zu können. Ist alles in Ordnung, scheint durch die Glastür des Schaltschranks beispielsweise ein petrolgrünes Licht, bei einer Störung oder einem kaputten Bauteil dagegen ein rotes Licht.
Im TDC soll der Nachweis erbracht werden, dass sich mithilfe eines digitalen Zwillings die Komplexität im Tunnelbau reduzieren lässt. Können Sie das anhand eines Beispiels erklären?
Bossart: Klassisch ist es so, dass das Personal erst geschult werden kann, wenn die Anlage in Betrieb ist. Wenn sich während der Schulung aber zeigt, dass etwas nicht passt oder stimmt, sind die notwendigen Korrekturen und Anpassungen extrem aufwendig, da ja alles bereits in Betrieb ist. Sehr viel einfacher ist es daher, vorab mit dem Personal am digitalen Zwilling zu testen und Schulungen durchzuführen. Wenn sich hier Unstimmigkeiten zeigen, lassen sich diese relativ einfach beheben, was Zeit und Geld spart. Ein weiterer Aspekt des digitalen Zwillings ist die Standardisierung, da sich mit dieser die Komplexität, insbesondere von grossen Projekten reduzieren lässt.
Mir erschliesst sich nicht die Ersparnis, die sich durch die Verwendung des digitalen Zwillings ergeben soll? Die Kosten entstehen doch in beiden Fällen?
Bossart: Nehmen wir als Beispiel die Inbetriebnahme eines Tunnels. Für diese bedarf es Fachpersonen, die teilweise von sehr weither anreisen. Müssen diese wegen nicht vorhergesehener Probleme warten oder wieder abreisen, entstehen zusätzliche Kosten.
Ein anderer Kostenfaktor, der für eine virtuelle Inbetriebnahme eines Tunnels spricht, sind die geltenden Normen und Vorschriften. Für die Ventilation müssen verschiedene Szenarien getestet werden. Dabei werden bei einer konventionellen Inbetriebnahme die Lüfter ein- und ausgeschaltet. Zum Schutz des Lüfters müssen jedoch gewisse Ein- und Ausschaltzeiten berücksichtigt werden, wodurch sich die Inbetriebnahme extrem in die Länge ziehen kann. Mit einem digitalen Zwilling hingegen lassen sich vorab alle Programme und Szenarien testen, sodass man sicher sein kann, dass alles funktioniert, wenn man mit seinen Programmen auf die Baustelle geht.
Kritische Stimmen sagen, dass die mit der Digitalisierung erzielbaren Einsparungen durch den höheren IT-Aufwand sowie die Lizenzkosten für die Software gefressen werden. Was entgegnen Sie diesen?
Rom: Für die Digitalisierung einer Anlage oder einer Maschine sind in der Tat mehr IT-Aufwände sowie Lizenzkosten einzuberechnen, als wenn man keine digitalisierten Anwendungen nutzt. Doch Untersuchungen zeigen, dass diese Kosten im Vergleich zu den Einsparungen, die sich mit dem Einsatz virtueller Simulationswerkzeugen erreichen lassen, sehr gering sind. Dies gilt insbesondere für den zeitlichen Aufwand, der sich durch eine virtuelle Inbetriebnahme reduzieren lässt, da Fehler frühzeitig und nicht erst auf der Baustelle erkannt werden. Durch die fortschreitende Vernetzung von Anlagen und Prozessen wird man ausserdem gar nicht mehr umherkommen, zu digitalisieren, wenn man am Markt bleiben möchte – unabhängig von den Kosten.
Zudem ist die Digitalisierung mittlerweile in vielen Software-Werkzeugen ein integraler Bestandteil, sodass Anwenderinnen und Anwender keinen zusätzlichen Aufwand investieren müssen, um zu digitalisieren oder einen digitalen Zwilling zu erstellen. Das decken heute viele Software-Pakete automatisch ab, weshalb das nichts Spezielles mehr ist.
Schutz vor Cyber-Angriffen
Beim TDC ist das eine Mal vom BIM, das andere Mal vom digitalen Zwilling die Rede. Was genau ist es denn nun?
Bossart: Das Building Information Modeling ist das komplette Framework der Baubranche und beinhaltet neben dem digitalen Zwilling der Bauten weitere Elemente, wie zum Beispiel Angaben zu Mengen und Kosten. Diese Daten werden im gesamten Modell für die weitere Verarbeitung sowie für die Kosten- und Bauplanung benutzt.
Sprechen wir als Siemens DI vom digitalen Zwilling, meinen wir die Virtualisierung und Simulation der Automatisierung, die am Ende nichts anderes macht, als ein virtuelles Abbild der Anlage möglichst realitätsnah darzustellen. Entscheidend bei dessen Einsatz ist, dass es für den kompletten Lebenszyklus einer Anlage, eines Projekts oder einer Maschine nur einen Datensatz für das Engineering, die virtuelle und reale Inbetriebnahme sowie das Retrofit gibt. Denn nur so ist gewährleistet, dass alle Beteiligten immer mit aktuellen Daten planen und arbeiten können. Zusammenfassend lässt sich also sagen, dass das BIM sowie auch unsere Simulation oder Virtualisierung einen spezifischen Teil des gesamten digitalen Zwillings einer Tunnelanlage darstellen.
Rom: Selbst wir haben lange den Begriff des digitalen Zwillings mit einem einzelnen Objekt oder einer einzelnen Maschine verbunden. Mittlerweile verbinden wir damit ganze Gewerke und das ist auch gedanklich eine neue Vorstellung des digitalen Zwillings. Das nächste Ziel wird es sein, verschiedene digitale Modelle zu vernetzen, um einen noch grösseren Nutzen aus der Digitalisierung ziehen zu können.
Die Digitalisierung von Maschinen und Anlagen, aber auch Infrastrukturen, birgt die Gefahr von Cyber-Angriffen. Wie lässt sich diesen am besten begegnen?
Rom: Zunächst eines vorweg; die Annahme, die Digitalisierung sei der Grund für Cyber-Angriffe, ist zu kurz gedacht. Jede offene Ethernet- oder USB-Schnittstelle bietet Kriminellen einen Angriffspunkt. Durch die Digitalisierung hat sich aber das Thema multipliziert, da mit ihr auch die Anzahl Knoten und Verbindungen oder grundsätzlich der Vernetzungsgrad zugenommen hat. Durch jede Meldung eines Angriffs oder Vorfalls können Schwachstellen beseitigt und gleichzeitig Unternehmen und Mitarbeitende weiter für dieses Thema sensibilisiert werden – und dieses wachsende Bewusstsein um mögliche Gefahren ist aus meiner Sicht ein guter Schutz vor Cyber-Angriffen.
Schutz vor Cyber-Angriffen
Beim TDC ist das eine Mal vom BIM, das andere Mal vom digitalen Zwilling die Rede. Was genau ist es denn nun?
Bossart: Das Building Information Modeling ist das komplette Framework der Baubranche und beinhaltet neben dem digitalen Zwilling der Bauten weitere Elemente, wie zum Beispiel Angaben zu Mengen und Kosten. Diese Daten werden im gesamten Modell für die weitere Verarbeitung sowie für die Kosten- und Bauplanung benutzt.
Sprechen wir als Siemens DI vom digitalen Zwilling, meinen wir die Virtualisierung und Simulation der Automatisierung, die am Ende nichts anderes macht, als ein virtuelles Abbild der Anlage möglichst realitätsnah darzustellen. Entscheidend bei dessen Einsatz ist, dass es für den kompletten Lebenszyklus einer Anlage, eines Projekts oder einer Maschine nur einen Datensatz für das Engineering, die virtuelle und reale Inbetriebnahme sowie das Retrofit gibt. Denn nur so ist gewährleistet, dass alle Beteiligten immer mit aktuellen Daten planen und arbeiten können. Zusammenfassend lässt sich also sagen, dass das BIM sowie auch unsere Simulation oder Virtualisierung einen spezifischen Teil des gesamten digitalen Zwillings einer Tunnelanlage darstellen.
Rom: Selbst wir haben lange den Begriff des digitalen Zwillings mit einem einzelnen Objekt oder einer einzelnen Maschine verbunden. Mittlerweile verbinden wir damit ganze Gewerke und das ist auch gedanklich eine neue Vorstellung des digitalen Zwillings. Das nächste Ziel wird es sein, verschiedene digitale Modelle zu vernetzen, um einen noch grösseren Nutzen aus der Digitalisierung ziehen zu können.
Die Digitalisierung von Maschinen und Anlagen, aber auch Infrastrukturen, birgt die Gefahr von Cyber-Angriffen. Wie lässt sich diesen am besten begegnen?
Rom: Zunächst eines vorweg; die Annahme, die Digitalisierung sei der Grund für Cyber-Angriffe, ist zu kurz gedacht. Jede offene Ethernet- oder USB-Schnittstelle bietet Kriminellen einen Angriffspunkt. Durch die Digitalisierung hat sich aber das Thema multipliziert, da mit ihr auch die Anzahl Knoten und Verbindungen oder grundsätzlich der Vernetzungsgrad zugenommen hat. Durch jede Meldung eines Angriffs oder Vorfalls können Schwachstellen beseitigt und gleichzeitig Unternehmen und Mitarbeitende weiter für dieses Thema sensibilisiert werden – und dieses wachsende Bewusstsein um mögliche Gefahren ist aus meiner Sicht ein guter Schutz vor Cyber-Angriffen.
Im Zusammenhang mit Cyber Security spricht man auch bei Siemens von Defense-in-Depth-Konzepten. Was hat man sich unter diesen vorzustellen?
Bossart: Lassen Sie mich das Defense-in-Depth-Konzept anhand des Zwiebel-Prinzips erklären. Das, was geschützt werden soll, befindet sich im Innern der Zwiebel, und die einzelnen Zwiebelschichten stellen die verschiedenen Stufen der Sicherheitsmassnahmen dar. So beginnt beispielsweise der Schutz vor Cyber-Angriffen nicht erst bei der Anlage, sondern schon beim Zutritt in ein Gebäude oder an einen Schaltschrank. Dieser geschützte Zugang ist die erste Schicht und sozusagen die Schale der Zwiebel. Sie soll einen Angreifenden davon abhalten, beispielsweise über eine ungesicherte Schnittstelle eine Schadsoftware aufzuspielen.
Eine tiefere Schicht in der Zwiebel beinhaltet die Struktur des Netzwerkes. Wichtige Sicherheitsaspekte, die in dieser Schicht relevant werden, sind beispielsweise, wie mit offenen Ports umgegangen wird, wie Netzwerksegmentierungen und Sicherheitszonen aufgebaut sind und wie diese geschützt werden.
Im Inneren der Zwiebel befindet sich das System oder das Produkt, bei dem wir durch den Verzicht von proprietären Protokollen und dem Einsatz verschlüsselter Kommunikation die Sicherheit erhöhen. Alle Schichten zusammen bilden das Defense-in-Depth-Konzept.
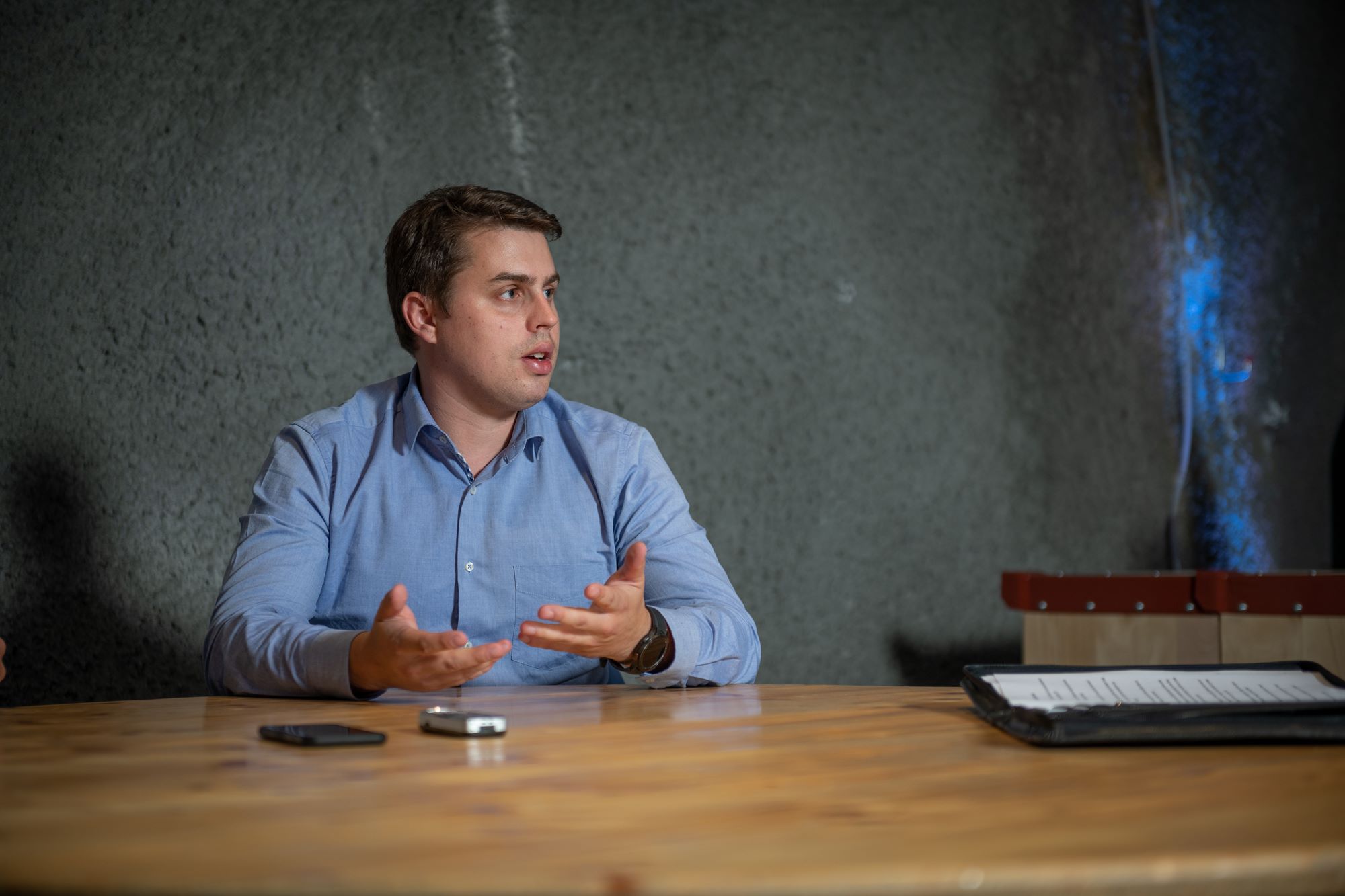
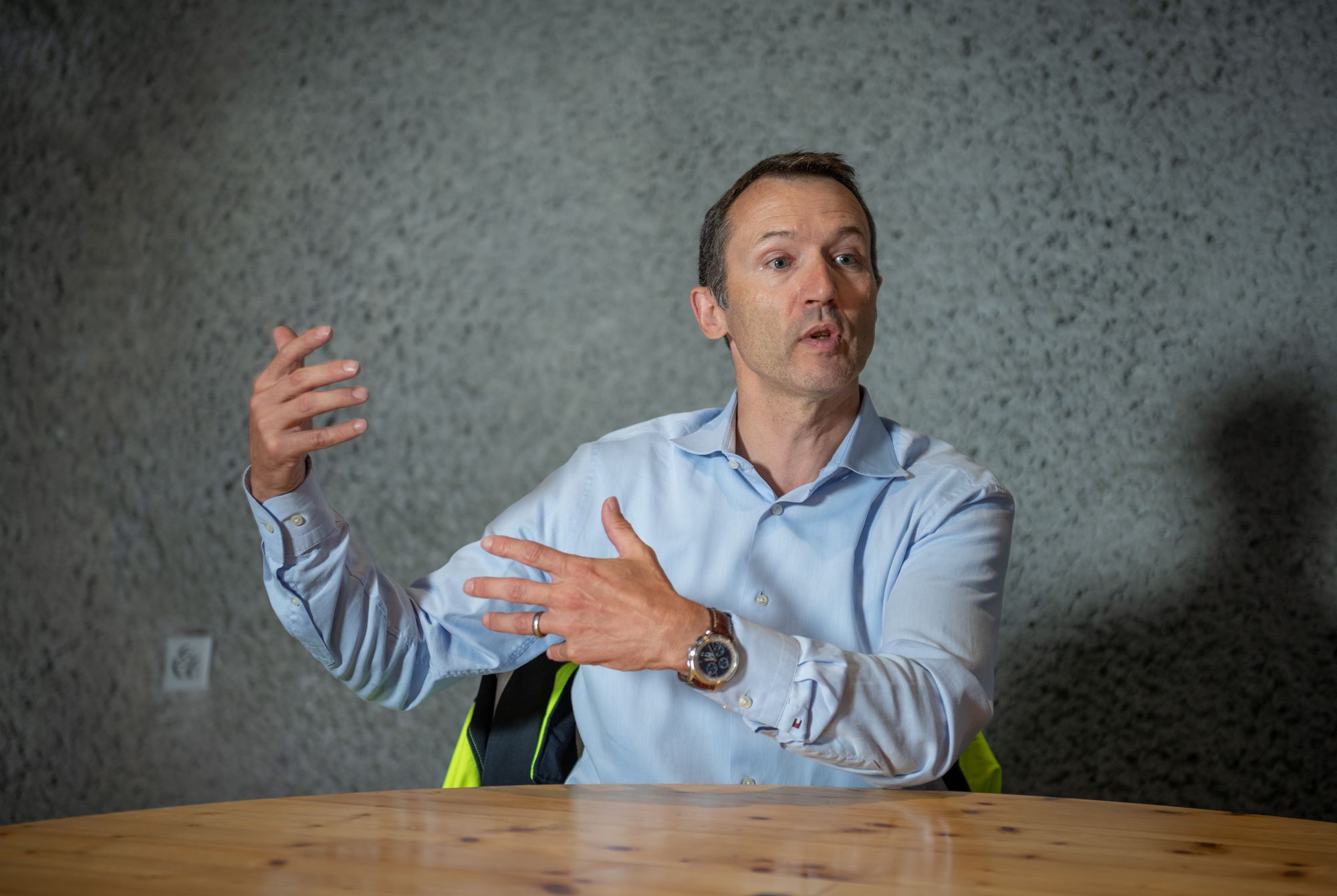
Lassen Sie uns abschliessend noch kurz über die dritte Röhre des Gubrists sprechen, die im kommenden Jahr eröffnet werden soll. Was von Siemens wird in dieser zum Einsatz kommen?
Rom: Das beginnt mit den Stromversorgungen als einfachstes Element und geht über die Peripherie-Systeme und der Niederspannungsschalttechnik bis hin zu den Komponenten für die Steuerung, Visualisierung und Kommunikation. Uns freut das natürlich sehr, da es unsere Kompetenz in der Automatisierung und Digitalisierung im Tunnelbau unterstreicht.
Tunnel Digitalization Center TDC
Das TDC ist eine Initiative zwischen SCAUT (Swiss Center for applied Underground Technologies), der Siemens AG und weiteren Industriepartnern. Diese dient dazu, die Integration von Automatisierungslösungen in neue oder bestehende Tunnelprojekte zu vereinfachen und Anwendern diese direkt am Objekt zu zeigen. Der Fokus liegt hierbei auf phasen- und bereichsübergreifenden Systemlösungen, welche die gesamte Wertschöpfungskette sowie den gesamten Lebenszyklus von Tunnelanlagen umfassen – angefangen bei der Planung mit BIM und der nachfolgenden Rohbau- und elektromechanischen Ausrüstung bis hin zur Betriebsphase und digitalen Services im Unterhalt.
Interessierte können einen individuellen Besuchstermin mit den Experten von Siemens im TDC vereinbaren. Anfragen an: industry.ch@siemens.com.
Weitere Artikel, die Sie interessieren könnten
Mehr Wissen. Immer auf dem Laufenden sein. Folge uns auf Linkedin.
Multimediastorys von «Technik und Wissen»
Impressum
Autor: Markus Back
Bildquelle: Damian Byland
Redaktionelle Bearbeitung: Technik und Wissen
Eine Publikation von Technik und Wissen
Informationen
Siemens
siemens.ch
Weitere Artikel
Veröffentlicht am: