Wie Gühring sich in der E-Mobilität positioniert
Neue Werkzeug und Bearbeitungsstrategien
Firmenbeitrag
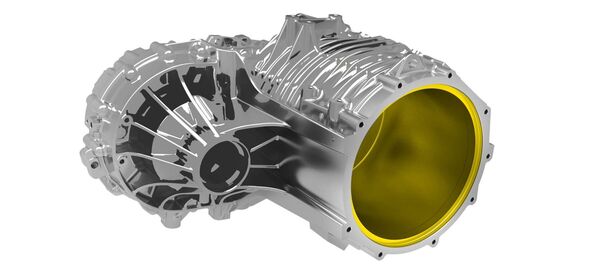
Wie Gühring sich in der E-Mobilität positioniert
Neue Werkzeug und Bearbeitungsstrategien
Firmenbeitrag
Blick auf das Bauteil (Statorseite). Die Statorbohrung wird mit Gühring PKD-Werkzeugen hergestellt.
Die Automobilindustrie im Wandel: Alternative Antriebskonzepte wie der Elektromotor setzen völlig neue Bearbeitungsaufgaben auf die Agenda der Zulieferer. Werkzeughersteller wie Gühring sind hier in der Pflicht, die E-Komponenten prozesssicher herzustellen.
Gühring ist bereits heute in der Lage, alle zu zerspanenden Komponenten aus Aluminiumlegierungen eines E-Fahrzeuges zu bearbeiten. Neben E-Motor-Gehäusen und den dazugehörigen Getriebedeckeln werden auch Nebenaggregate wie Batteriewannen oder elektrische Kältemittelverdichter zerspant.
Herausforderungen an Gührings PKD-Werkzeuge
Das E-Motor-Gehäuse inklusive Getriebedeckel wird aus Aluminiumlegierungen gefertigt und mit Gühring PKD-Werkzeugen hergestellt. Die Herausforderungen hierbei sind enorm: Verlangt wird die prozesssichere Herstellung von engen Durchmesser-Toleranzen bis IT6 sowie enge Form- und Lagetoleranzen, wie beispielweise eine Koaxialität von bis zu 40 µm bei einer Bezugslänge von über 400 mm, die auf Umschlag bearbeitet wurde.
Leichtbauwerkzeug aus Aluminium
Die Statorbohrung fordert hohe Massgenauigkeit. Das dafür passende 6-schneidige PKD-Werkzeug von Gühring hat bei einem Durchmesser von 235 mm ein Kippmoment von 22 Nm und wiegt weniger als 20 Kilogramm. Hierbei handelt es sich um ein sogenanntes Leichtbauwerkzeug aus Aluminium, das neben der Reduzierung der Spindellast maximale Produktivität gewährleistet.
Neben der Leichtbauweise, welche maximale Präzision ermöglicht, ist eine weitere Herausforderung die Bauteilsauberkeit. Mit Hilfe von innovativen Werkzeuggeometrien werden Späne beim Fräsen, Aufrauen und Reiben von der zu bearbeitenden Fläche bzw. Bohrung definiert abgeführt. Somit wird das Risiko, dass sich Al-Späne in den Kühlrippen verklemmen, stark reduziert.
Bild: 6-schneidiges Gühring PKD-Werkzeug im Einsatz.
Alle Komponenten im Blick
Neben E-Motor-Gehäusen und dazugehörigen Getriebedeckeln werden auch Nebenaggregate, wie Batterie- wannen für die Lagerung der Energiespeicher und Kältemittelverdichter, die für das Thermomanagement in Fahrzeugen eingesetzt werden, bearbeitet. Batteriewannen sind aufgrund der Grösse von bis zu 2x1 m sowie der Dünnwandigkeit besonders schwingungsanfällig.
Primär beim Fräsen wird dieses Problem mithilfe geometrischer Merkmale, wie einer starken Ungleichteilung der Schneiden sowie einer steifen Werkzeugschnittstelle durch störkonturoptimierte Aufnahmen, gemeistert. Mit bereits über 20 erfolgreichen Batteriegehäuseprojekten gilt Gühring als führend in dieser Anwendung. Die Bearbeitung mit Minimalmengenschmierung garantiert zusätzlich langfristige Nachhaltigkeit in der Produktion.
Enge Durchmessertoleranzen und Form- und Lagetoleranzen
• wirtschaftliche und gleichzeitig präzise Bearbeitung der engen Durchmessertoleranzen bis IT6
• prozesssichere Werkzeuglösungen bei besonders engen Form- und Lagetoleranzen, beispielweise eine Koaxialität von bis zu 40 µm bei einer Bezugslänge von über 400 mm
• FEM-Berechnung während der Werkzeugkonstruktion zur Gewichtsreduzierung
Sauberes Thermomanagement durch optimierte Fräswerkzeuge
Eine weitere Herausforderung bei den Elektrofahrzeugen stellt das Thermomanagement dar. Bisher trieb der Verbrennungsmotor die konventionelle Klimaanlage an. Für Elektrofahrzeuge soll künftig der sogenannte elektrische Kältemittelverdichter als Wärme- und Kältepumpe eingesetzt werden. Dieser besteht aus zwei Spiralen, deren gegenläufige Bewegung Gas verdichtet.
Eine möglichst effiziente Verdichtung wird durch enge Toleranzen der Spiralen realisiert. Die Anforderungen an Form- und Lagetoleranz sind beispielweise eine Winkligkeit von 20 µm und eine Linienform von 8 µm. Engste Oberflächengüten unter Rz 4 µm im Zusammenspiel mit dünnwandigen Flächen mit Wandstärken von kleiner 3 mm und Eingriffshöhen bis zu 25 mm sind für diese Bearbeitungsaufgabe repräsentativ. Die Lösungen sind Fräswerkzeuge mit minimalen Schnittdrücken. Durch hochpositive Spanwinkel und erhöhte Steifigkeit werden die Toleranzen prozesssicher eingehalten.
Bild: 6-schneidiges Gühring PKD-Werkzeug im Einsatz.
Alle Komponenten im Blick
Neben E-Motor-Gehäusen und dazugehörigen Getriebedeckeln werden auch Nebenaggregate, wie Batterie- wannen für die Lagerung der Energiespeicher und Kältemittelverdichter, die für das Thermomanagement in Fahrzeugen eingesetzt werden, bearbeitet. Batteriewannen sind aufgrund der Grösse von bis zu 2x1 m sowie der Dünnwandigkeit besonders schwingungsanfällig.
Primär beim Fräsen wird dieses Problem mithilfe geometrischer Merkmale, wie einer starken Ungleichteilung der Schneiden sowie einer steifen Werkzeugschnittstelle durch störkonturoptimierte Aufnahmen, gemeistert. Mit bereits über 20 erfolgreichen Batteriegehäuseprojekten gilt Gühring als führend in dieser Anwendung. Die Bearbeitung mit Minimalmengenschmierung garantiert zusätzlich langfristige Nachhaltigkeit in der Produktion.
Enge Durchmessertoleranzen und Form- und Lagetoleranzen
• wirtschaftliche und gleichzeitig präzise Bearbeitung der engen Durchmessertoleranzen bis IT6
• prozesssichere Werkzeuglösungen bei besonders engen Form- und Lagetoleranzen, beispielweise eine Koaxialität von bis zu 40 µm bei einer Bezugslänge von über 400 mm
• FEM-Berechnung während der Werkzeugkonstruktion zur Gewichtsreduzierung
Sauberes Thermomanagement durch optimierte Fräswerkzeuge
Eine weitere Herausforderung bei den Elektrofahrzeugen stellt das Thermomanagement dar. Bisher trieb der Verbrennungsmotor die konventionelle Klimaanlage an. Für Elektrofahrzeuge soll künftig der sogenannte elektrische Kältemittelverdichter als Wärme- und Kältepumpe eingesetzt werden. Dieser besteht aus zwei Spiralen, deren gegenläufige Bewegung Gas verdichtet.
Eine möglichst effiziente Verdichtung wird durch enge Toleranzen der Spiralen realisiert. Die Anforderungen an Form- und Lagetoleranz sind beispielweise eine Winkligkeit von 20 µm und eine Linienform von 8 µm. Engste Oberflächengüten unter Rz 4 µm im Zusammenspiel mit dünnwandigen Flächen mit Wandstärken von kleiner 3 mm und Eingriffshöhen bis zu 25 mm sind für diese Bearbeitungsaufgabe repräsentativ. Die Lösungen sind Fräswerkzeuge mit minimalen Schnittdrücken. Durch hochpositive Spanwinkel und erhöhte Steifigkeit werden die Toleranzen prozesssicher eingehalten.
Gühring: 40 Jahre Erfahrung im Bereich PKD
Gühring bringt über 40 Jahre Erfahrung im Bereich PKD (polykristalliner Diamant) in die Bearbeitung von E-Motor-Gehäusen ein. Zugleich werden neuste Produktinnovationen in die E-Bearbeitung integriert. Präventive Massnahmen mit dem Ziel einer maximalen Prozesssicherheit, wie die FEM-Berechnung während der Werkzeugkonstruktion zur Gewichtsreduzierung oder Steifigkeits- und Schwingungsuntersuchungen unter Berücksichtigung realer Betriebsdrehzahlen, sind im Tagesgeschäft etabliert.
So sorgt Gühring mit Hochdruck dafür, dass das Thema E-Mobilität für seine Kunden ganzheitlich, aus einer Hand und global behandelt wird und steht der Automobilindustrie als kompetenter Partner in der serienreifen Produktion von Elektroantrieben weltweit zur Seite. Durch die Strategie eines breiten Produktportfolios ist Gühring auf den dynamisch verlaufenden, technologischen Wandel im automobilen Antriebsstrang bestens vorbereitet.
Weitere Artikel, die Sie interessieren könnten
Mehr Wissen. Immer auf dem Laufenden sein. Folge uns auf Linkedin.
Multimediastorys von «Technik und Wissen»
Impressum
Das ist ein Firmenbeitrag von Gühring
Textquelle: Gühring
Bildquelle: Gühring
Publiziert von Technik und Wissen
Informationen
Weitere Artikel
Veröffentlicht am: