Die Servotechnik ermöglicht es mit den Technologieobjekten in der Simatic Steuerung, den Torquemotor Simotics T-1FW3 Motor präzise zu regeln und so die Pressbewegung dynamisch an das Werkstück anzupassen. Nicht wie früher die Königswelle, an die alle Bewegungen in der Maschine gekoppelt waren, sondern eine virtuelle Leitachse gibt den Takt vor, auf den sich alle Servomotoren in der Maschine synchronisieren.
Umformtechnik: Schwungrad raus, Servomotor rein
Hatebur Kaltumformmaschine – mit Direktantrieb zu flexibleren Umformprozessen
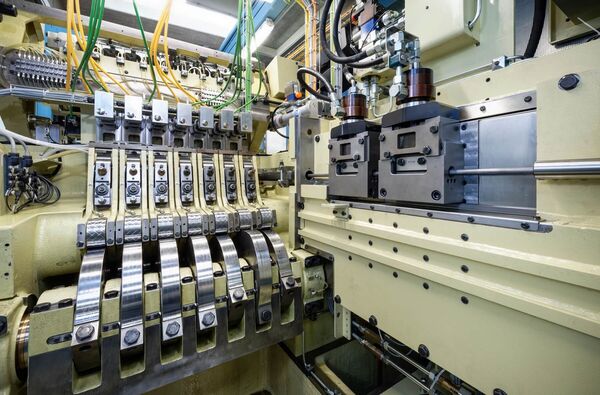
Umformtechnik: Schwungrad raus, Servomotor rein
Hatebur Kaltumformmaschine – mit Direktantrieb zu flexibleren Umformprozessen
Die Firma Hatebur bietet ihre Kaltumformmaschine neu auch mit einem Direktantrieb an – anstelle eines herkömmlichen Antriebs mit Schwungrad. Dazu setzt das Unternehmen auf einen Servomotor von Siemens und erreicht eine völlig neue Flexibilität beim Umformprozess.
Beitrag hören statt lesen (mit Download-Funktion)
Wie entstehen eigentlich komplexe Metallformteile, Schraubenmuttern oder Schlauchstutzen? Bei grossen Mengen werden sie in der Regel nicht zerspanend hergestellt oder gegossen, sondern in die gewünschte Form gepresst. Dabei wird Stahl – kalt oder erwärmt – in mehreren Stufen mit progressiven Werkzeugen und durch den Einsatz hoher Presskräfte geformt. So entstehen beispielsweise auch Zündkerzenkörper und Verbindungsteile für den Automobilbau, oder Kettenrollen für Förderbänder – nahezu ohne Materialverlust.
Beim Umformen von Stahl sind gewaltige Kräfte im Spiel. So verwundert es nicht, dass die horizontale Kaltumformmaschine, die der Maschinenbauer Hatebur entwickelt hat, eindrückliche 60 Tonnen auf die Waage bringt. Allein der Maschinenkörper wiegt 30 Tonnen.
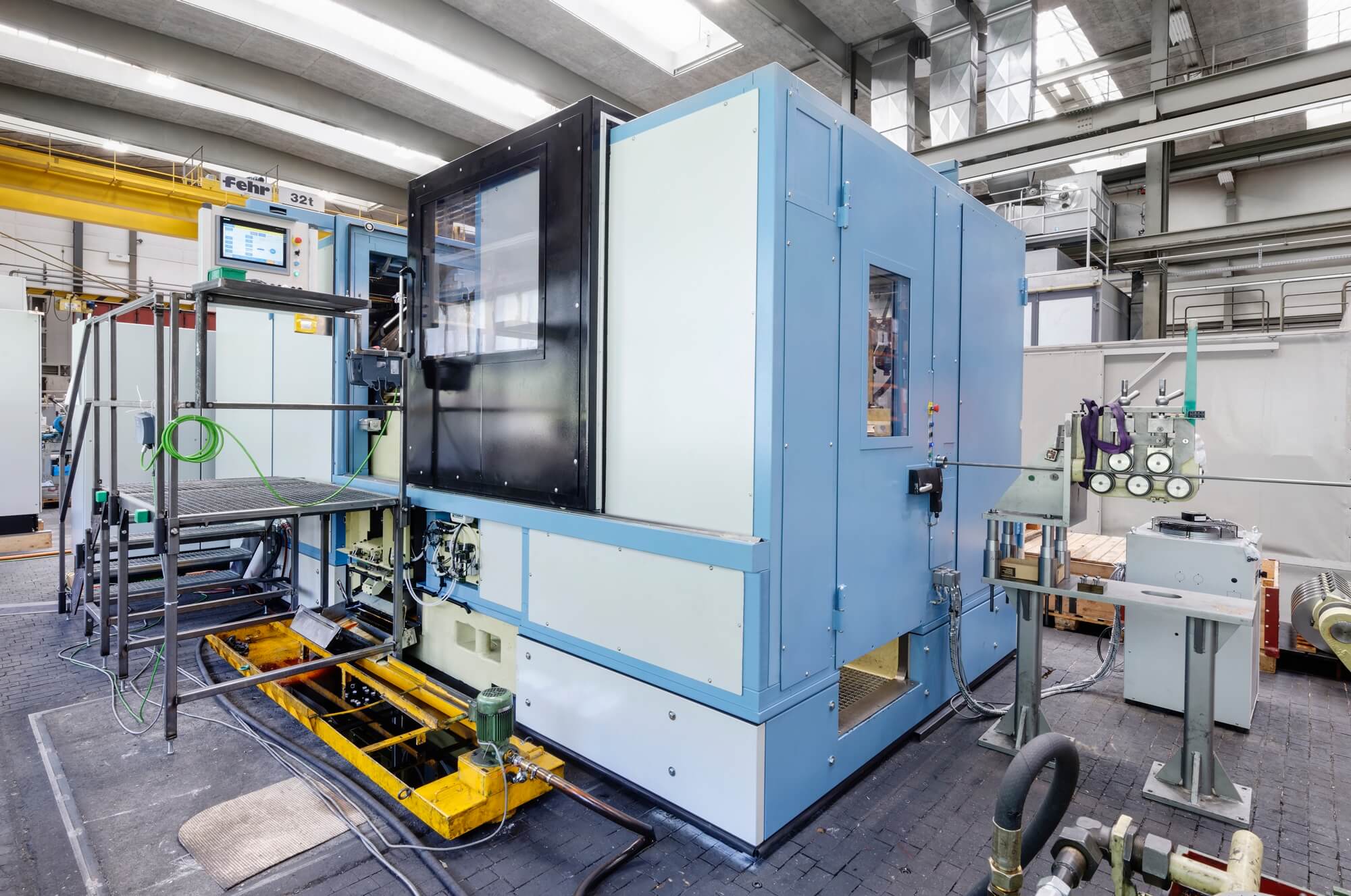
Damit verleiht er der Maschine die nötige Stabilität und Steifigkeit, wenn der Pressschlitten während des Umformprozesses mit einer Presskraft von maximal 250 Tonnen nach vorne fährt und bis zu 180 Werkstücke pro Minute aus der Maschine rattern. Beim Ausgangsmaterial für die Presse mit dem Namen COLDmatic CM725 sprechen die Fachleute zwar von einem «Draht»; dieser kann jedoch einen stattlichen Durchmesser von zwei Zentimetern erreichen. Der Draht wird ab einem Haspel durch einen Richtapparat in die Umformmaschine gezogen. Die in der Maschine kalt gescherten Abschnitte werden von Zangen gegriffen und im mehrstufigen Werkzeug der Maschine nacheinander umgeformt.
Deutlich flexibler umformen
Bisher bestückte Hatebur seine Umformmaschine mit einem herkömmlichen Antrieb. Ein eher kleiner Asynchronmotor setzte ein grosses Schwungrad mit fast einem Meter Durchmesser und einem Gewicht von über 1000 kg in Bewegung. Dieses übertrug die Kraft über ein Getriebe auf Zahnräder und Kurvenscheiben, die für die Vorschubbewegung des Pressschlittens und der Nebenantriebe wie Auswerfer und Schere sorgten. Die Drehzahl des Motors war dabei konstant.
Mit der neusten Ausführung der Horizontalpresse gelingt dem Unternehmen, das seit der Gründung 1930 im Familienbesitz ist, eine innovative Weiterentwicklung: Der traditionelle mechanische Antrieb des Pressschlittens wurde durch einen Servomotor ersetzt.
Bei einem Servomotor lassen sich Beschleunigung, Drehzahl und die Winkelposition der Motorwelle flexibel steuern. Andreas Maritz, Innovationsmanager bei Hatebur, sieht klare Vorteile bei der neuen Technologie: «Wir können nun den Hauptantrieb sowie die bestehenden Servoantriebe des Drahteinzugs, des Quertransports und der Zangen programmieren und alle Bewegungen der Maschine flexibel aufeinander abstimmen. Das erlaubt uns für jedes Werkstück die optimalen Einstellungen zu wählen. Lange Teile können beispielsweise langsam transportiert werden, damit die Maschine sie sicher greift und kein Stück verloren geht oder verrutscht. Oder wir formen bei Bedarf zugunsten der Werkzeugstandzeit etwas langsamer um, transportieren dafür schneller. Das heisst, dass durch die bedarfsgerechte Anpassung der Kinematik der Prozess bei mindestens gleicher Produktivität verbessert wird.»
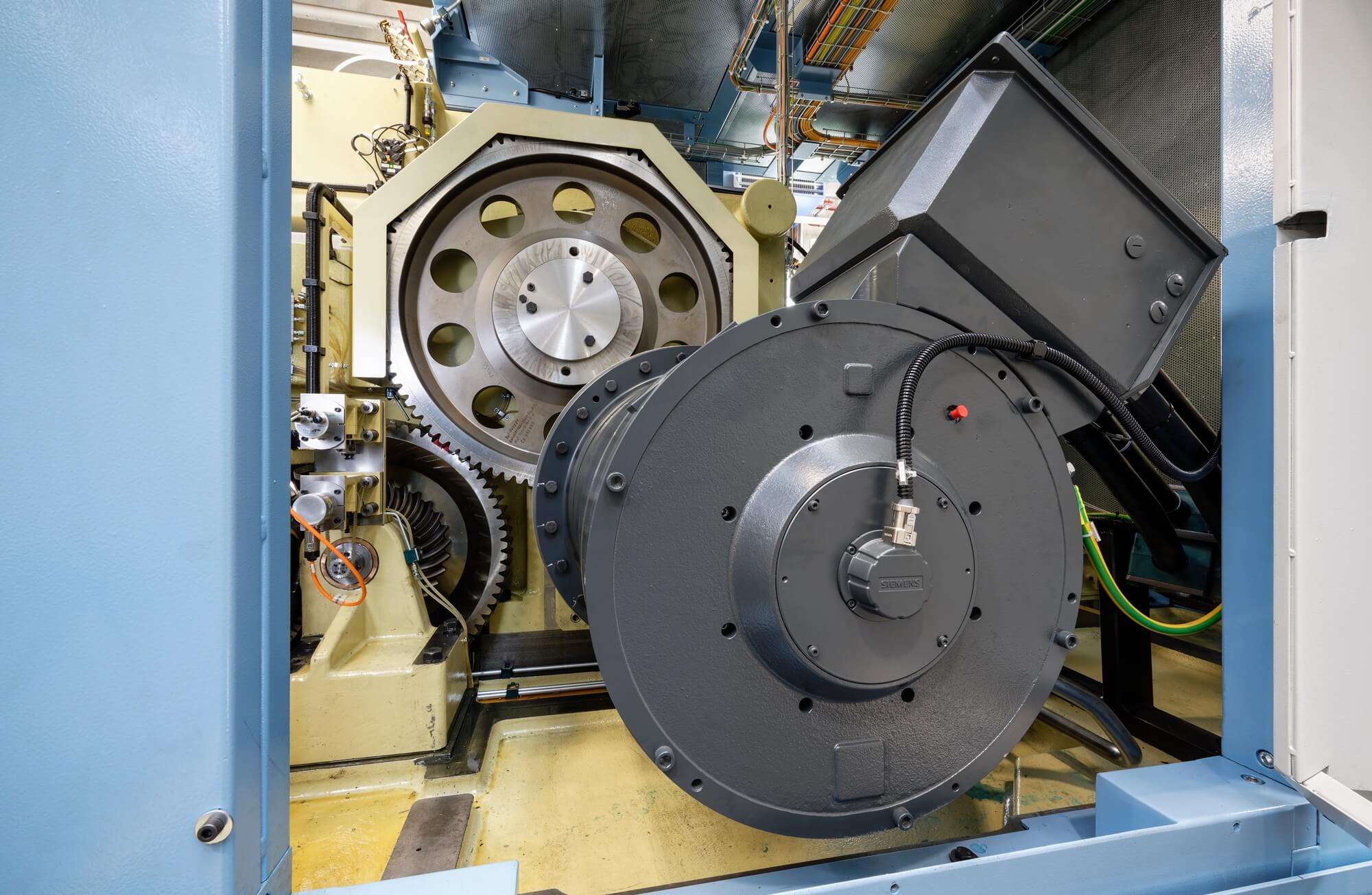
Wo bisher das grosse Schwungrad die Kraft für die Umformung bereitstellte, thront nun ein eindrücklicher Simotics T-1FW3-Torquemotor mit einer Leistung von 500 kW und einem Drehmoment von 8150 Nm. «Glücklicherweise passte der Motor nahezu perfekt in die Maschine», so Maritz, «das erlaubt uns, unsere Maschinen sowohl mit dem bisherigen Antrieb, als auch mit einem sogenannten Direktantrieb ohne Schwungrad anzubieten.» Die Leistungsfähigkeit des Direktantriebs ist vergleichbar mit derjenigen eines Antriebs mit Schwungrad, dazu muss aber ein Teil der kinetischen Energie im kompletten Antriebsstrang genutzt werden. Der dadurch relativ klein ausfallende Motor erlaubt es, die Geschwindigkeit über eine Kurbelwellenumdrehung gezielt zu variieren.
Wartungsfreundlich dank weniger Verschleiss
«Wir liebäugelten schon länger damit, unsere Maschinen mit einem Direktantrieb zu versehen und waren dafür auch in Kontakt mit Siemens», erinnert sich Maritz. Als ein langjähriger Kunde aus der Umgebung vor rund zwei Jahren erneut eine Maschine orderte, liess er sich von der neuen Technologie überzeugen.
Der Kunde, ein Zulieferer für die Automobilbranche, wird sich auch beim Unterhalt der Anlage freuen: Zahlreiche Verschleissteile wie Kupplung, Bremsen oder Keilriemen fallen weg, was die Maschine deutlich wartungsärmer macht. Maritz präzisiert: «Wenn wir langsamer umformen, müssen die Werkzeuge weniger oft ersetzt werden. Ein stabiler, ruhiger Transport verhindert, dass ein Werkstück schräg in die Matrize gelangt.» Dass das Schwungrad nicht mehr in Gang gesetzt und abgebremst werden muss, spart Zeit im täglichen Betrieb, zum Beispiel beim Werkzeugwechsel.
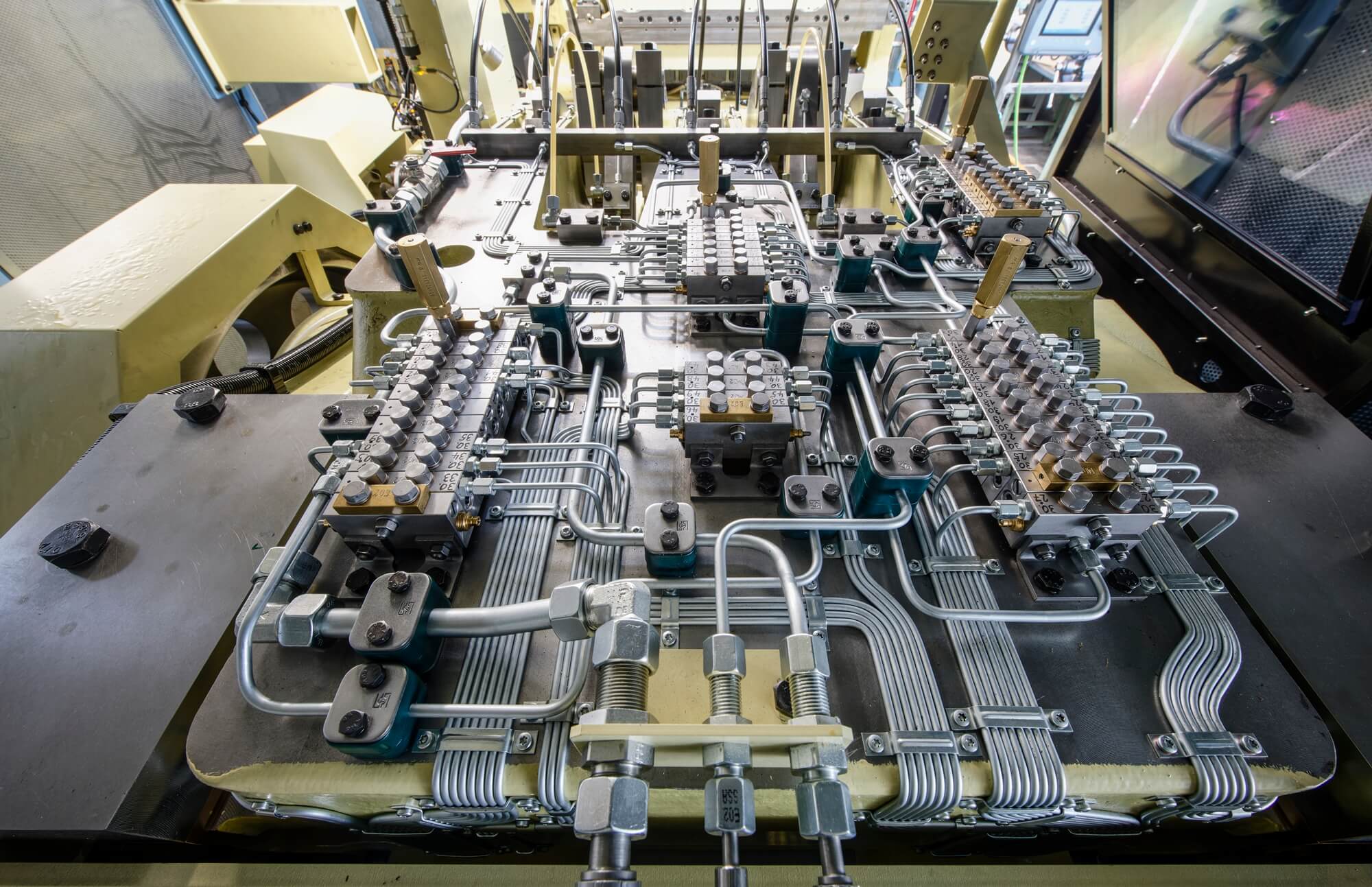
Energiespeicher für den Umformprozess: Kondensator statt Schwungrad
Die dicken Kabel machen deutlich: Hier fliessen grosse Ströme – bis zu 1430 A –, um die gewaltige Maschine mit einer Umformarbeit bis 18 kJ zu betreiben. Die Energie für den Umformprozess, die früher im Schwungrad gespeichert war, muss nun anders bereitgestellt werden. Luftgekühlte Kondensatoren sorgen dafür, dass keine zu grossen Leistungsschwankungen das Netz belasten. Sie werden mit Netzstrom aufgeladen, speichern die Energie, bis wieder umgeformt wird und glätten so den Leistungsverlauf. Dank dieser nahezu konstanten Anschlussleistung fallen dem Betreiber keine hohen Kosten für grosse Leistungsspitzen an.
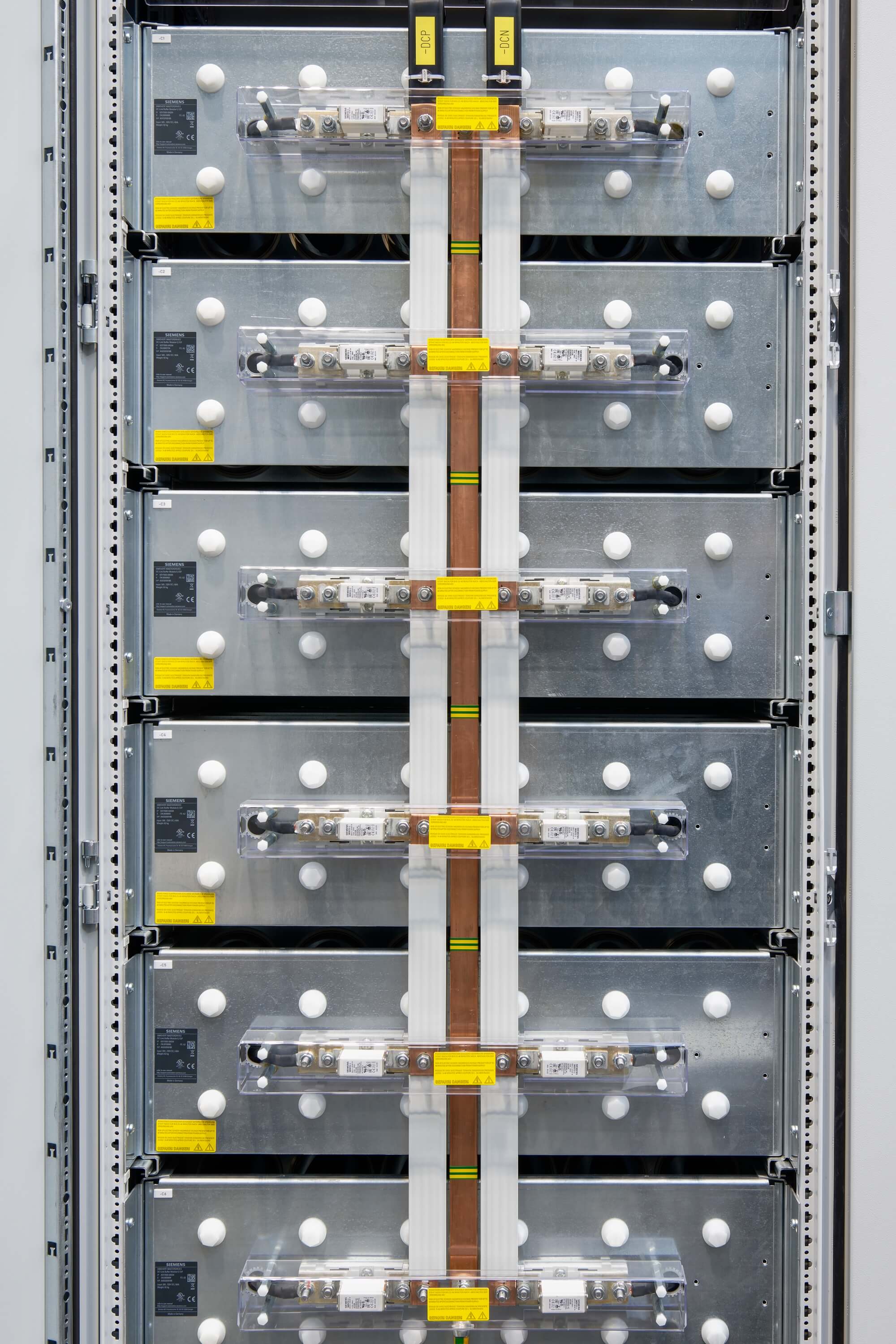
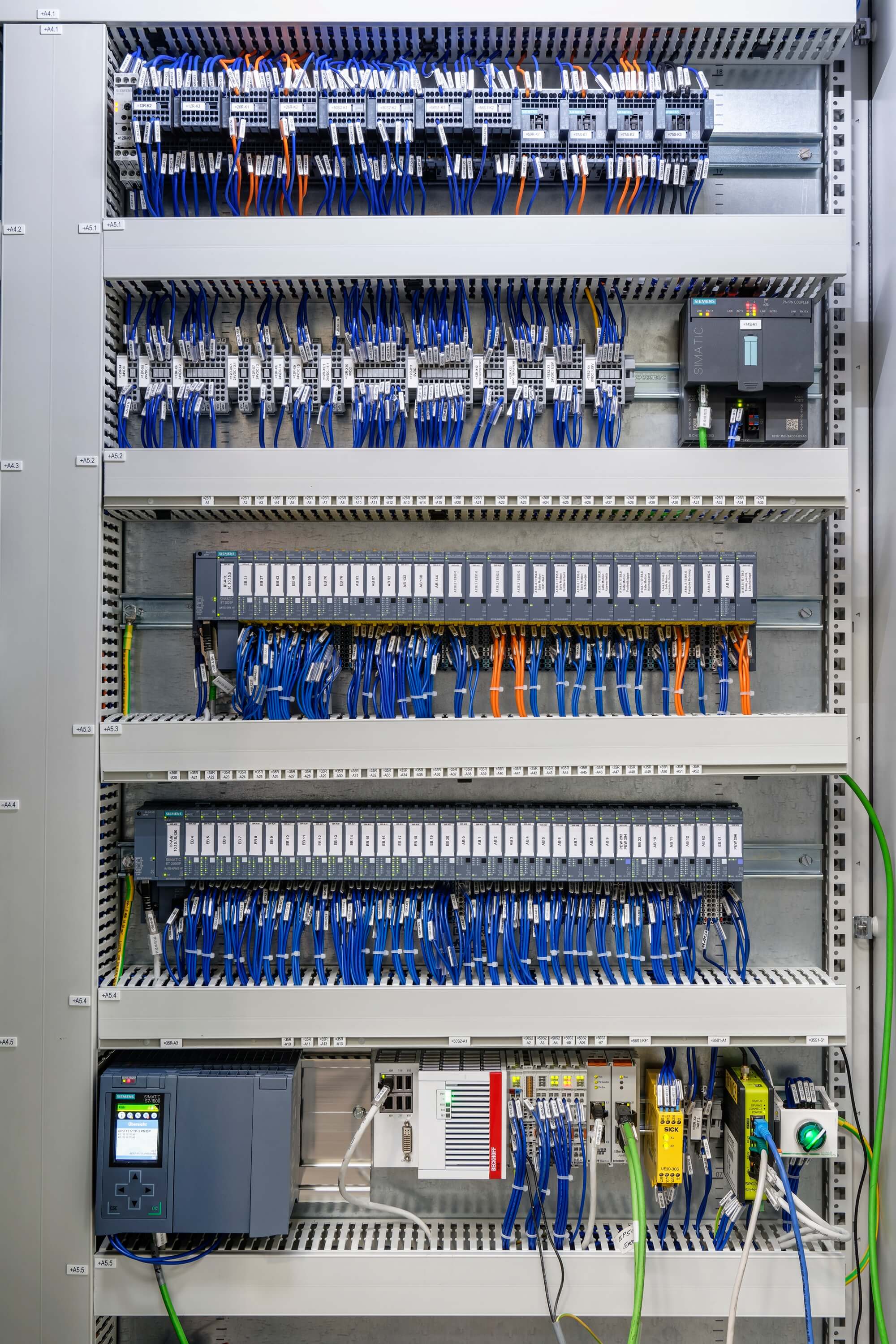
Dass sich die Firma Hatebur, die weltweit rund 300 Mitarbeitende beschäftigt, bei diesem Projekt für Siemens entschieden hat, ist kein Zufall. «Wir verwenden standardmässig Steuerungen von Siemens», erklärt Elektroingenieur Pascal Schwarz, der die Steuerung des Direktantriebs, basierend auf einer Simatic S7-1500TF, mitentwickelt hat. «Da wir unsere Maschinen rund um den Globus vertreiben, schätzen wir zudem den weltweiten Service von Siemens». Dass Siemens alle Antriebskomponenten – Schaltschrank, Motor und Pressensteuerung – ab Werk lieferte, war ein weiteres Plus und nicht zuletzt stimmte auch der Preis.
Effiziente Automation mit dem Simatic SimaPress Servo Standard
Für die effiziente Automatisierung hat Siemens den Simatic SimaPress Servo Standard mit vorgefertigten Software-Bausteinen speziell für Servopressen mit einer Simatic-Steuerung entwickelt. «Wir nutzen für unsere Pressen eine eigene, über Jahre entwickelte Software und verwenden Teile des SimaPress Servo Standards, um den Direktantrieb zu steuern», erklärt Schwarz. Mit seinen Fragen habe sich Schwarz jederzeit an das Siemens Application Center APC wenden können.
Bald wird die Maschine an den Kunden geliefert, ans Stromnetz angeschlossen und nimmt die Produktion auf – Plug-and-play eben. Maritz und sein Team freuen sich, dass die Neuentwicklung unter realen Produktionsbedingungen zum Einsatz kommt und sehen für den Direktantrieb in der Umformtechnik ein grosses Potenzial. ◊
Technik in Kürze Die Servotechnik ermöglicht es ...
Hatebur Umformmaschinen AG Das Reinacher Unternehmen ist ...
Das Reinacher Unternehmen ist ein weltweiter Entwickler und Lösungsanbieter von Maschinen, Werkzeugen und Verfahren für die Warm- und Kaltumformung. Hatebur wurde 1930 gegründet und ist zu 100 Prozent in Familienbesitz. Rund 300 Mitarbeitende an Standorten in der Schweiz, Italien, China, Japan und Deutschland sichern die führende Marktposition und die Technologieführerschaft der Unternehmensgruppe.
Diese Artikel könnten Sie auch interessieren
Impressum
Textquelle: Siemens
Bildquelle: Siemens
Redaktionelle Bearbeitung: Technik und Wissen
Eine Publikation von Technik und Wissen
Weitere Artikel
Veröffentlicht am: