Das eine Unternehmen baut Maschinen in den Allgäuer Bergen, das andere entwickelt und fertigt unweit vom Kölner Dom anspruchsvolle Fahrzeugkomponenten. Beide eint eine Leidenschaft: Faserverbundwerkstoffe. Der Firma Germa Composite aus Pulheim gelang es in Teamwork mit der bayrischen HG Grimme SysTech, das Besäumen von Karosserie-Bauteilen aus Naturfaserverbundmaterialien zu beschleunigen und zu automatisieren.
Ein Artikel der Firma HG Grimme SysTech
Autor: Nikolaus Fecht
Es ist eine der typischen Erfolgsstorys, die man gerne in der Zeitung liest: 2010 in einer Garage gegründet, heute ein mittelständisches Familienunternehmen mit guter Auftragslage. Vor allem der Autoindustrie und dem Motorsport verdankt die Germa Composite GmbH aus Pulheim (bei Köln) den Aufstieg zum mittelständischen Composite-Spezialisten. Die Kernkompetenz liegt in der Herstellung von High-Performance-Bauteilen, die aus mit Harz getränkten Fasermatten im beheizbaren Druckbehälter (Prepreg-Autoklaven) unter Vakuum, Überdruck und Wärme gehärtet werden.
Naturfaser-Boom erfordert Prozessbeschleunigung
Zwei Autoklaven stehen in der Produktionshalle, an denen Geschäftsführer Jörg Gehrmann den jüngsten Trend erklärt: «Neuerdings härten wir hier drin immer öfter Composites mit Naturflachfasern aus, auf die wir uns vor rund zwei Jahren neben anderen Fasern zusätzlich spezialisiert haben. Wegen des Booms geht der Trend aktuell hin zu immer grösseren Serien bis zur Losgrösse 1000, derentwegen wir den Prozess nun weiter automatisieren.»
Das betrifft auch die Nachbearbeitung der in den Autoklaven gehärteten Fasermaterialien, die bisher entweder manuell oder auf einer grossen CNC-Fräsmaschine ablief. «Unsere grosse, schwer gängige Portalfräsmaschine eignet sich mit ihrem sehr grossen Bearbeitungskopf eigentlich nur für einfache XXL-Bauteile», erklärt Jörg Gehrmann. «Wir fertigen jedoch immer mehr Bauteile mit sehr komplexen Geometrien. Dafür benötigen wir eine Maschine mit kleinem, wendigem Bearbeitungskopf und sehr schnellem Vorschub.»
Das eine Unternehmen baut Maschinen in den Allgäuer Bergen, das andere entwickelt und fertigt unweit vom Kölner Dom anspruchsvolle Fahrzeugkomponenten. Beide eint eine Leidenschaft: Faserverbundwerkstoffe. Der Firma Germa Composite aus Pulheim gelang es in Teamwork mit der bayrischen HG Grimme SysTech, das Besäumen von Karosserie-Bauteilen aus Naturfaserverbundmaterialien zu beschleunigen und zu automatisieren.
Ein Artikel der Firma HG Grimme SysTech
Autor: Nikolaus Fecht
Es ist eine der typischen Erfolgsstorys, die man gerne in der Zeitung liest: 2010 in einer Garage gegründet, heute ein mittelständisches Familienunternehmen mit guter Auftragslage. Vor allem der Autoindustrie und dem Motorsport verdankt die Germa Composite GmbH aus Pulheim (bei Köln) den Aufstieg zum mittelständischen Composite-Spezialisten. Die Kernkompetenz liegt in der Herstellung von High-Performance-Bauteilen, die aus mit Harz getränkten Fasermatten im beheizbaren Druckbehälter (Prepreg-Autoklaven) unter Vakuum, Überdruck und Wärme gehärtet werden.
Naturfaser-Boom erfordert Prozessbeschleunigung
Zwei Autoklaven stehen in der Produktionshalle, an denen Geschäftsführer Jörg Gehrmann den jüngsten Trend erklärt: «Neuerdings härten wir hier drin immer öfter Composites mit Naturflachfasern aus, auf die wir uns vor rund zwei Jahren neben anderen Fasern zusätzlich spezialisiert haben. Wegen des Booms geht der Trend aktuell hin zu immer grösseren Serien bis zur Losgrösse 1000, derentwegen wir den Prozess nun weiter automatisieren.»
Das betrifft auch die Nachbearbeitung der in den Autoklaven gehärteten Fasermaterialien, die bisher entweder manuell oder auf einer grossen CNC-Fräsmaschine ablief. «Unsere grosse, schwer gängige Portalfräsmaschine eignet sich mit ihrem sehr grossen Bearbeitungskopf eigentlich nur für einfache XXL-Bauteile», erklärt Jörg Gehrmann. «Wir fertigen jedoch immer mehr Bauteile mit sehr komplexen Geometrien. Dafür benötigen wir eine Maschine mit kleinem, wendigem Bearbeitungskopf und sehr schnellem Vorschub.»
Empfehlung aus Süddeutschland
Über eine Empfehlung aus der süddeutschen Automobilindustrie lernt Jörg Gehrmann die HG Grimme SysTech GmbH aus Wiedergeltingen (Unterallgäu) kennen, die seit rund 35 Jahren CNC-Maschinen unter anderem zum Fräsen von Kunststoffen und zum Fräsen von Verbundwerkstoffen herstellt. So fräst ein bekannter Fahrzeughersteller mit mehreren Anlagen aus Wiedergeltingen bereits serienmässig CFK-Rahmenteile. Nach einem Benchmark mit Wettbewerbsprodukten entscheidet sich das CNC-Team der Germa Composite schliesslich für ein 5-Achsen-CNC-Gantry-Fräsanlage von HG Grimme SysTech mit einem in zwei Arbeitsbereiche teilbaren Tisch. Für sie spricht: Es ist eine freistehende Maschine, die sich ohne Bodenvorarbeiten installieren liess.
Zum Einsatz kommt eine Eigenentwicklung von HG Grimme: ein einseitig gelagerter Fräskopf mit hochdynamischen Drehachs-Getriebe. Beim Blick in den Maschinenraum fällt auf: Im Gegensatz zu anderen Maschinen bewegt sich der Balken mit dem Fräskopf nicht von vorne nach hinten und retour, sondern von links nach rechts. Für die Maschine sprach laut Jörg Gehrmann der kleine, flexible Fräskopf, der im Pendelbetrieb die Nachbearbeitung von zwei nebeneinander im Arbeitsraum auf zwei Vakuumspanntischen aufgespannten Werkstücken erlaubt. Als positiv bezeichnet er ausserdem, dass sich der Bearbeitungskopf um 550 Grad drehen lässt, sodass sich damit eigentlich fast alles in einer «Durchfahrt bearbeiten lässt».
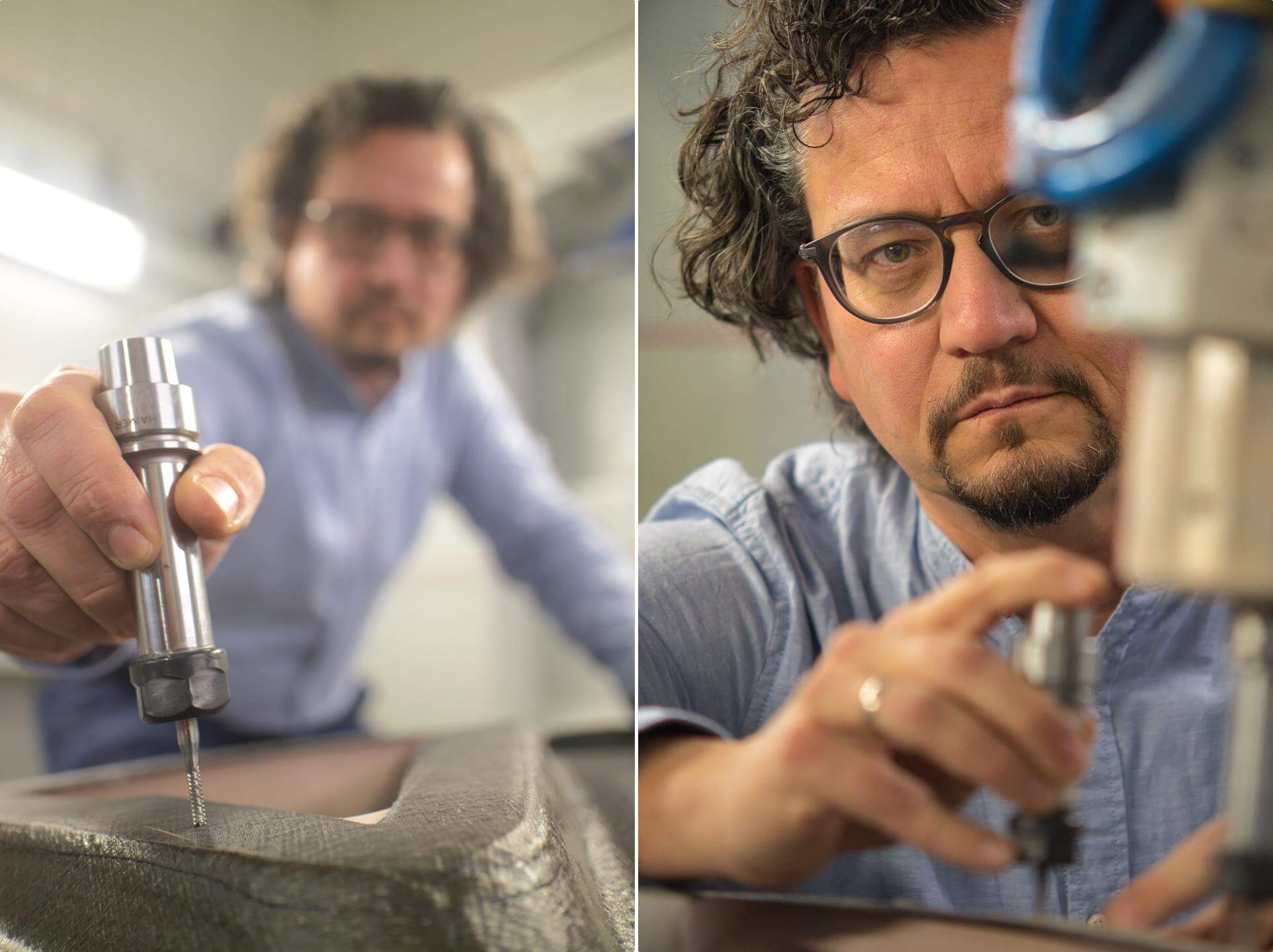
Saubere Schnittkanten und exzellente Oberflächen im Visier
Germa stellt aus Naturfasern vor allem Karosseriebauteile her. Bei diesen sogenannten Aussenhautteilen (Exterieur) ist ausser der präzisen Bearbeitung vor allem das Aussehen gefragt. «Wichtig sind für uns saubere Schnittkanten und qualitativ hochwertige Oberflächen», erläutert der Geschäftsführer. «Wir setzen dazu Spezialfräswerkzeuge ein, die aber nur mit hohen Drehzahlen optimale Ergebnisse liefern. Aktuell erzielen wir auf der HG Grimme-Maschine bei Drehzahlen von 15‘000 bis 25‘000 Umdrehungen pro Minute sehr gute Schnittkanten und Oberflächen.» Die Gantry-Maschine bietet bei einer Maximalspindeldrehzahl von 40‘000 min-1 und einem Vorschubtempo von 80 m/min. genügend dynamische Reserven.
Wie produktiv und ergonomisch die neue Investition arbeitet, zeigt ein Besuch in Pulheim: Ein Bediener legt zur Nachbearbeitung eine grosse Innenverstärkungsschale für eine Fahrzeug-Fronthaube auf eine Vorrichtung, die bereits in der Gantry-Anlage auf dem Vakuumspanntisch liegt. Während der Facharbeiter die Schale mit beiden Händen im Werkzeug positioniert, startet er die Vakuumpumpen mit einem Knieschalter: Der Spanntisch hält nun das Werkzeug mit der Schale vibrationsfrei fest, die Germa Composite in Losgrösse 500 bis maximal 1000 herstellt.
Sechs Minuten statt zwei Stunden Nachbearbeitung
«Das Nacharbeiten dauerte früher eineinhalb bis zwei Stunden», berichtet Gehrmann. «Nach Optimierung des CNC-Programms liegen wir aktuell bei unter sechs Minuten. Das sind eindeutige Vorteile bei der Geschwindigkeit und auch bei der Qualität.» In dieser knappen Zeit gilt es, eine komplexe Form mit einer rund sieben Meter langen Kontur zu besäumen, Löcher auszuschneiden und Bohrungen zum Anbringen von Bauteilen zu fräsen.
Eine Lösung mit Robotern nahmen die Pulheimer vorher ebenfalls unter die Lupe, entschieden sich aber aus Kosten- und Qualitätsgründen schliesslich für eine klassische Werkzeugmaschine. «Wir kamen mit dem Roboter nicht auf die Toleranzen und Wiederholgenauigkeit, die uns eine Gantry-Maschine bietet», sagt der Geschäftsführer. «Ausserdem ist eine Gantry-Maschine flexibler einsetzbar. So können wir auf ihr auch unsere Werkzeuge- und Vorrichtungen bearbeiten.»
Sechs Minuten statt zwei Stunden Nachbearbeitung
«Das Nacharbeiten dauerte früher eineinhalb bis zwei Stunden», berichtet Gehrmann. «Nach Optimierung des CNC-Programms liegen wir aktuell bei unter sechs Minuten. Das sind eindeutige Vorteile bei der Geschwindigkeit und auch bei der Qualität.» In dieser knappen Zeit gilt es, eine komplexe Form mit einer rund sieben Meter langen Kontur zu besäumen, Löcher auszuschneiden und Bohrungen zum Anbringen von Bauteilen zu fräsen.
Eine Lösung mit Robotern nahmen die Pulheimer vorher ebenfalls unter die Lupe, entschieden sich aber aus Kosten- und Qualitätsgründen schliesslich für eine klassische Werkzeugmaschine. «Wir kamen mit dem Roboter nicht auf die Toleranzen und Wiederholgenauigkeit, die uns eine Gantry-Maschine bietet», sagt der Geschäftsführer. «Ausserdem ist eine Gantry-Maschine flexibler einsetzbar. So können wir auf ihr auch unsere Werkzeuge- und Vorrichtungen bearbeiten.»
Ein Tag Einarbeitung für neue Gantry-Anlage
Auch die Mehrkosten für Gantry-Anlage, Programmiersystem sowie der anstehende Schulungs- und Ausbildungsaufwand waren keine Hürden. So ist die neue HG Grimme-Anlage mit demselben Programmiersystem wie die anderen Maschinen ausgestattet, sodass das Bedienungsteam sie sofort nutzen konnte. «Alles in allem fiel der Schulungsaufwand gering aus», stellt der Germa-Chef zufrieden fest. «HG Grimme hat unser Team so geschult, dass es die Maschine bereits am nächsten Tag produktiv bedienen konnte.»
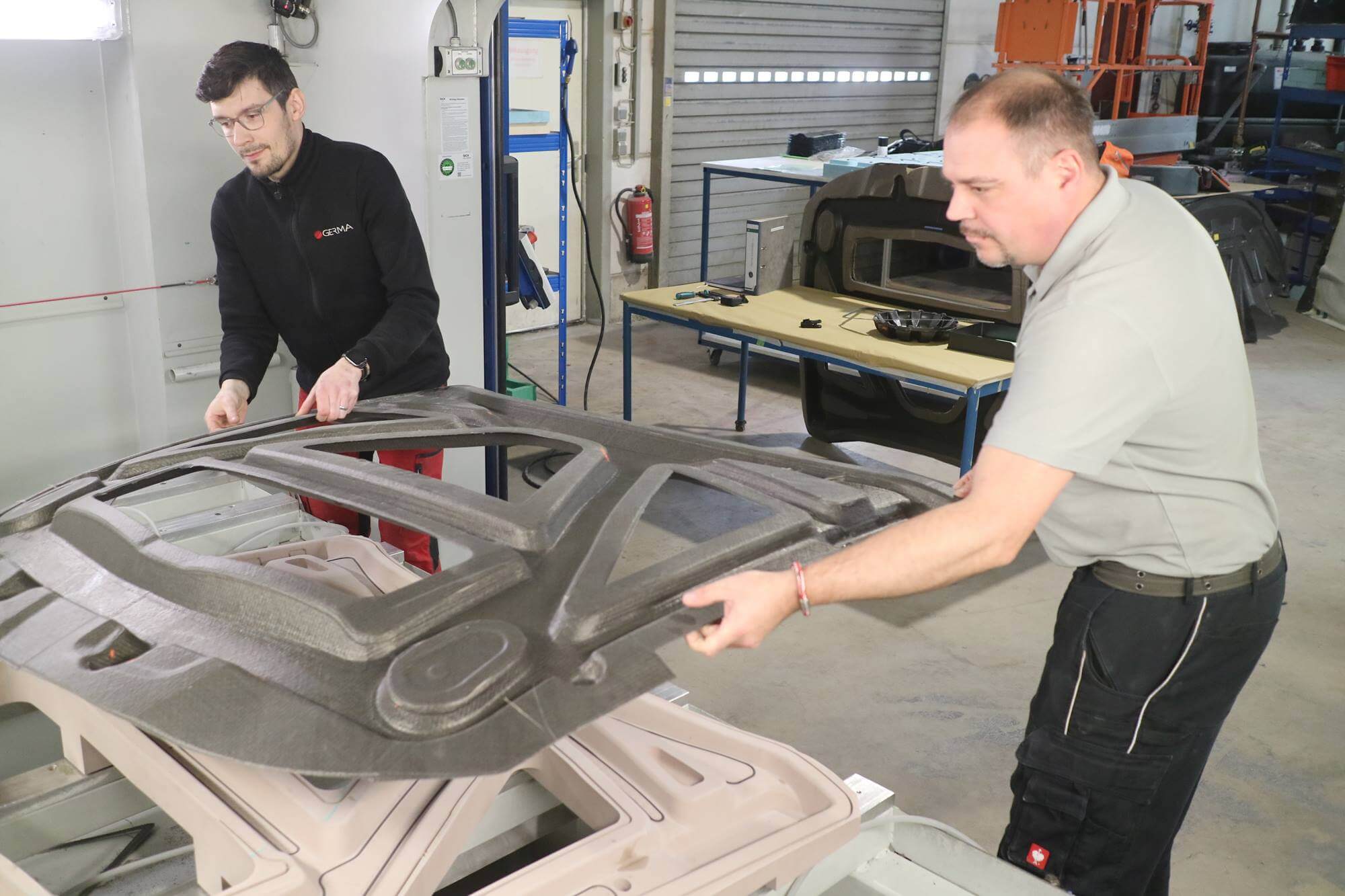
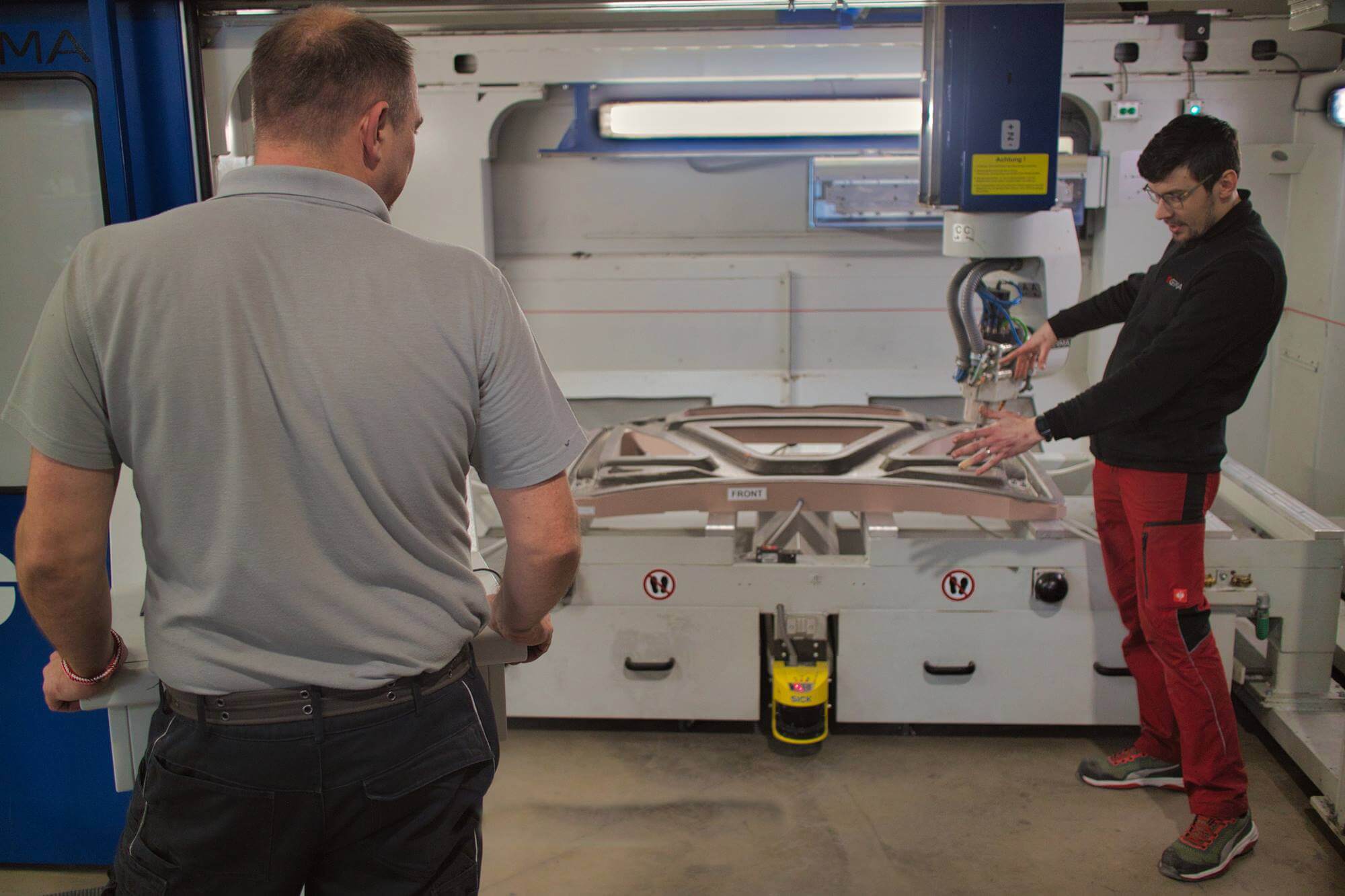
Den Einsatz erleichtert ein unauffälliger gelber Kasten, unten an der HG Grimme-Anlage. Es handelt sich um einen sogenannten PLS-Laserscanner, der den Gefahrenbereich der Maschine überwacht. Dr.-Ing. Ingo Gehlhaar, Kundenbetreuer bei HG Grimme SysTech: «Der optische Scanner stellt sicher, dass niemand im Arbeitsraum ist. Nach dem Einlegen des Teils drückt der Bediener «Zyklus Start»: Die Türen schliessen sich und die Bearbeitung startet automatisch. Das spart viel Zeit.» Ausserdem lässt sich die Maschine so auch von ungeschultem Personal bedienen.
Eine besondere Herausforderung sind bei der Composite-Bearbeitung Späne und Stäube: Damit sie nicht die Antriebstechnik blockieren, sitzt diese in der Gantry-Maschine oben. Das Bedienpersonal wird durch eine besondere Einhausung vor gesundheitsschädlichen Stäuben geschützt. Zusätzlich wurde eine leistungsfähige, horizontale Absaugung installiert.
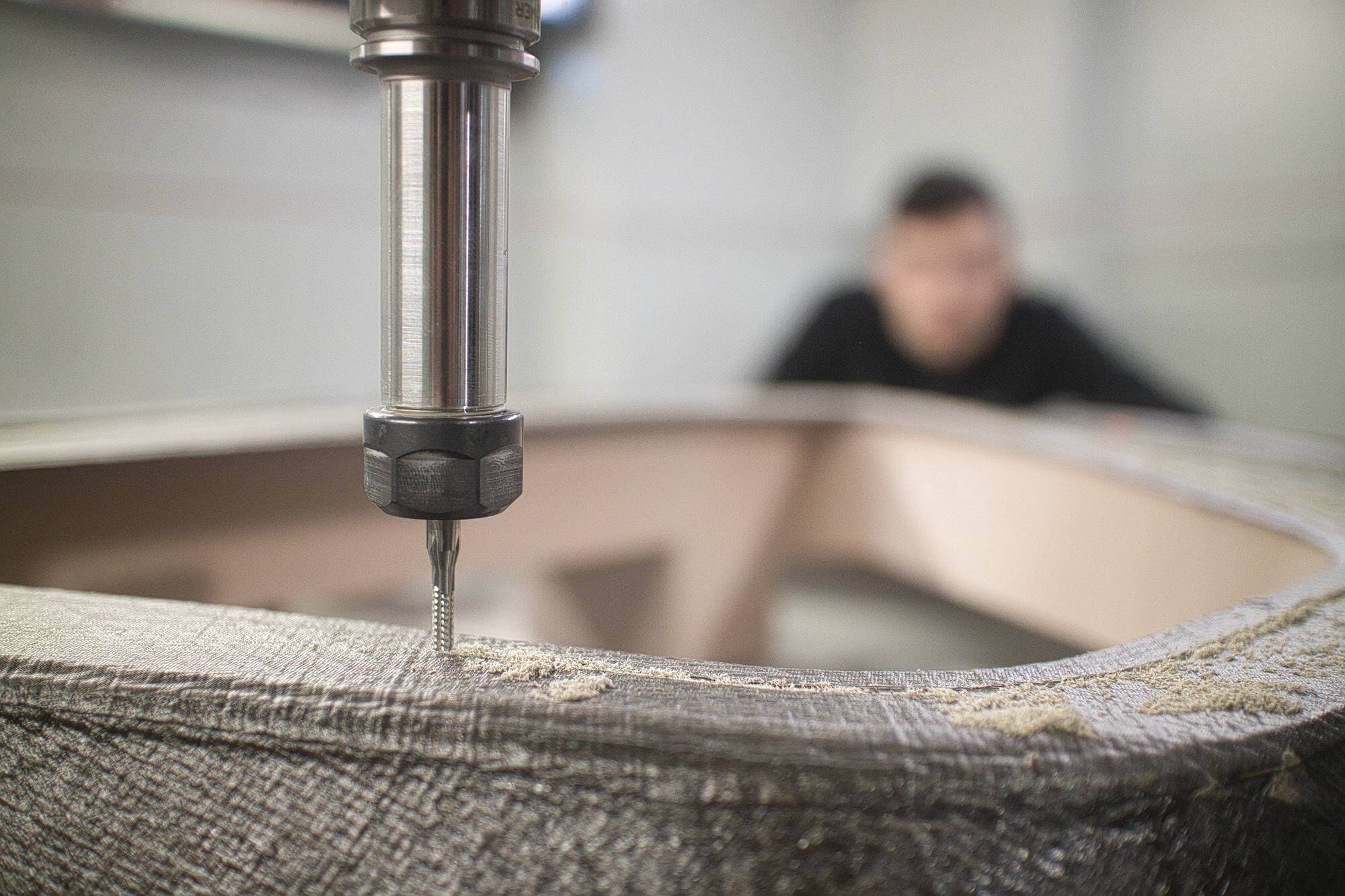
Prognose: Naturfaser für viele Anwendungen geeignet
Die Investition in die neue Gantry-Fräsmaschine war für Germa Composite nur ein weiterer Schritt in eine nachhaltigere Zukunft. Gehrmann: «Wir brauchen jetzt auch biokompatible Harzstoffe, um damit echt nachhaltige Bauteile herzustellen. Mit verbesserten Eigenschaften eignen sich dann Naturfasern für viele Anwendungen – nicht nur im Motorsport oder im Serienfahrzeug.»
Technikwissen zu: HG 5-Achsen CNC Gantry-Fräsanlage
Technik im Detail: HG 5-Achsen CNC Gantry-Fräsanlage / G-S-F 24-13
Maschinentyp: Fräsanlage auf Gantry-Basis mit zwei Shuttle-Tischen zur Bearbeitung von Kunststoffen und Verbundwerkstoffen
Tischfläche: 2'450 mm x 1'250 mm (Ebenheit: ± 0,05 mm/m)
Tischrahmen: von 3 Seiten begehbar
Verfahrwege: 3'050 mm x 1'800 mm x 900 mm
Antriebe: Zahnstangenantrieb und Linearachsen mit gehärteten Präzisions-Linearführungen mit Abstreifern sowie Edelstahlband
Wiederholgenauigkeit: ± 0,03 – 0,055 mm
Max. Beschleunigung: 4'000 mm/s2
Max. Geschwindigkeit: 80'000 mm/min (X/Y) bzw. 40'000 mm/min (Z)
Sonderausstattung: Mittentrennwand, Automatiktüren, Blechverkleidung rechts links am Tisch, Schallschutzkabine/-Dach, Maschineninnenraumbeleuchtung, Knieschalter, PLS-Scanner zur Überprüfung des Arbeitsraumes, externes Bedienpult
Weitere Artikel, die Sie interessieren könnten
Impressum
Autor: Nikolaus Fecht im Auftrag von HG Grimme SysTech
Bildquelle: HG Grimme
Redaktionelle Bearbeitung: Technik und Wissen
Informationen
Weitere Artikel
Veröffentlicht am: