- Retrofit einer Leimholzzuschnittmaschine mit fliegender Säge
- Einbindung eines Leitsystems
- Verknüpfung SEW-Generation B und C
- Datenaustausch über UDP, ProfiNet und ProfiBus mit Fremdsteuerung
- Synchronisation von acht Antrieben
- mm-genauer Zuschnitt von Leimholz bis 1'100 mm Breite und 25 m Länge
- Komplettumbau der Schaltschranktechnik auf SEW-MOVI-C modular
- komplette Applikations-Programmierung mit SEW-Controller UHX45A
- Erstellung der Visualisierung auf SEW-DOP
Mitunter führt Empirik zum Ziel
Retrofit einer Zuschnittanlage mit fliegender Säge
Wenn neue Technologien alte ersetzen, führt das mitunter zu Problemen. Mit welchen die Alfred Imhof AG beim Retrofit einer Leimholz-Zuschnittanlage konfrontiert wurde und wie sie diese gelöst hat, beschreibt dieser Beitrag.
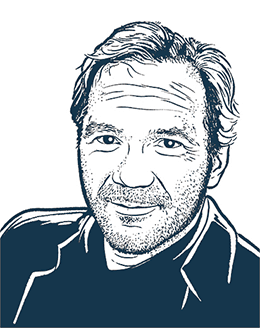
Autor: Eugen Albisser, Chefredaktor Online und Digitales Storytelling.
E-Mail / LinkedIn-Profil
Das Retrofit von Maschinen wird immer beliebter. Kein Wunder, denn es gibt genügend Argumente, die gegen eine Neuanschaffung sprechen (siehe auch Kasten: Zwölf Gründe, die für ein Retrofit sprechen). Diese kennt auch die Roth Burgdorf AG, weshalb die Berner ihre Springer Kappsäge auf den neuesten Stand der Technik brachte. Aber nicht nur deswegen! Bei der Leimholz-Zuschnittanlage handelt es sich um ein echtes Unikat. Die Maschine ist ein Prototyp und wurde vom Hersteller Springer nie in Serie produziert.
Trotz ihres Alters funktioniert sie mechanisch immer noch einwandfrei und ist mit den anderen Maschinen vollständig in den Produktionsprozess integriert. «Nach 15 Jahren war es nun aber an der Zeit, sie auf den neuesten Stand der Technik zu bringen», sagt Markus Mandel, Deputy Head of Automation Engineering Department bei Alfred Imhof, der Schweizer Vertretung von SEW Eurodrive.
Kurzinfo zum Retrofit
Neue Generation von Komponenten
Die Wünsche der Firma Roth waren klar: Mit der Erneuerung der Anlage wollte man eine geringere Ausschussrate, weniger Stillstände, eine höhere Genauigkeit und mehr Transparenz, um bei Fehlern oder Änderungen schneller reagieren zu können. Und natürlich sollte nur das ausgetauscht werden, was zum Erreichen dieser Ziele notwendig ist. «Also haben wir die Antriebe belassen und uns auf die Elektronik konzentriert», so Markus Mandel. Hierbei wurden die Schütze und Relais getestet und teilweise ausgetauscht, komplett erneuert wurden das Bedienpanel, die I/O-Module und die Frequenzumrichter.
Die ausgetauschten Komponenten stammten allesamt noch aus der Generation B von SEW Eurodrive, die beim Bau der Leimholz-Zuschnittanlage gerade auf den Markt kamen. Nun erfolgte der Wechsel auf die neue Generation C.
Einachs- und Mehrachsmodule im Einsatz
Zum Einsatz kommt nun das Bedienpanel DOP11C-72, das über ein hochauflösendes Farbdisplay, schnelle Prozessoren und einen grossen Arbeitsspeicher verfügt. Bei den I/O-Modulen wurden zwei Buskoppler eingebaut, zehn Eingangsmodule mit je acht digitalen Eingängen und sechs Ausgangsmodule mit acht digitalen Ausgängen. Bei den Umrichtern wählte man die zum Automatisierungsbaukasten Movi-C gehörenden Mehrachssystem MOVIDRIVE modular. Die Applikations-Umrichter sind im Portfolio von SEW Eurodrive als Einachs-Applikations-Umrichter (MOVIDRIVE Technology / System) bis 315 kW Nennleistung und als modulare Mehrachssysteme mit Einzel- und Doppelachsmodulen bis zu 180 A Nennstrom erhältlich. Bei Roth wurde eine Versorgungsmodul MDP90A mit 50 kW eingebaut, dazu vier Einzelachsmodule (48 A, 8 A, 8 A, 4 A) und zusätzlich zwei Doppelachsmodule mit je 2x8 A.
«Das Mehrachssystem eignet sich besonders, wenn die Anzahl der Motoren gleich oder grösser als drei ist – allein aus finanziellen Gründen», sagt Markus Mandel. So wird nur eine einzige Einspeisung benötigt und die Netzkomponenten sind lediglich ein statt acht Mal vorhanden, was einen grossen Vorteil darstellt.
Neue Generation von Komponenten
Die Wünsche der Firma Roth waren klar: Mit der Erneuerung der Anlage wollte man eine geringere Ausschussrate, weniger Stillstände, eine höhere Genauigkeit und mehr Transparenz, um bei Fehlern oder Änderungen schneller reagieren zu können. Und natürlich sollte nur das ausgetauscht werden, was zum Erreichen dieser Ziele notwendig ist. «Also haben wir die Antriebe belassen und uns auf die Elektronik konzentriert», so Markus Mandel. Hierbei wurden die Schütze und Relais getestet und teilweise ausgetauscht, komplett erneuert wurden das Bedienpanel, die I/O-Module und die Frequenzumrichter.
Die ausgetauschten Komponenten stammten allesamt noch aus der Generation B von SEW Eurodrive, die beim Bau der Leimholz-Zuschnittanlage gerade auf den Markt kamen. Nun erfolgte der Wechsel auf die neue Generation C.
Einachs- und Mehrachsmodule im Einsatz
Zum Einsatz kommt nun das Bedienpanel DOP11C-72, das über ein hochauflösendes Farbdisplay, schnelle Prozessoren und einen grossen Arbeitsspeicher verfügt. Bei den I/O-Modulen wurden zwei Buskoppler eingebaut, zehn Eingangsmodule mit je acht digitalen Eingängen und sechs Ausgangsmodule mit acht digitalen Ausgängen. Bei den Umrichtern wählte man die zum Automatisierungsbaukasten Movi-C gehörenden Mehrachssystem MOVIDRIVE modular. Die Applikations-Umrichter sind im Portfolio von SEW Eurodrive als Einachs-Applikations-Umrichter (MOVIDRIVE Technology / System) bis 315 kW Nennleistung und als modulare Mehrachssysteme mit Einzel- und Doppelachsmodulen bis zu 180 A Nennstrom erhältlich. Bei Roth wurde eine Versorgungsmodul MDP90A mit 50 kW eingebaut, dazu vier Einzelachsmodule (48 A, 8 A, 8 A, 4 A) und zusätzlich zwei Doppelachsmodule mit je 2x8 A.
«Das Mehrachssystem eignet sich besonders, wenn die Anzahl der Motoren gleich oder grösser als drei ist – allein aus finanziellen Gründen», sagt Markus Mandel. So wird nur eine einzige Einspeisung benötigt und die Netzkomponenten sind lediglich ein statt acht Mal vorhanden, was einen grossen Vorteil darstellt.
Pragmatische Lösungen
Bei vielen Retrofit-Projekten kommen immer wieder Fragen auf, die durch das Aufeinandertreffen von neuen und alten Lösungen entstehen. In diesem speziellen Fall stellte sich eine solche Frage in Bezug auf den Datenaustausch. Die Steuerungstechnik der Generation C unterstützt nicht Profibus, die Hauptsteuerung der Anlage basiert aber noch auf diesem. Aus Kostengründen wollte der Kunde das bestehende System aber nicht verändern.
«Um diesem Wunsch gerecht zu werden und keine aufwendigen Korrekturen vornehmen zu müssen, verwenden wir die alte, Profibus-fähige Steuerung als Gateway», erklärt Markus Mandel: «Die Daten des Leitsystems werden über Profibus auf der alten Steuerung gesammelt, wobei der gesamte Logikteil auskommentiert wird. Wir greifen die Daten dann über das User Datagram Protocol ab und leiten sie entsprechend an den neuen MOVI-C Controller weiter.»
Dass man UDP und nicht etwa TCP verwendet, ist schnell erklärt: Es ist einfach und schlank. Man muss nicht Hunderte von Befehlen senden und beim Empfang quittieren. Intern müssen aber gewisse Sicherheitsmechanismen eingebaut werden, um dennoch zu überprüfen, ob die Daten angekommen oder verwendet wurden. «Wir haben hier bewusst auf eine einfache Lösung gesetzt», erklärt Mandel.
Die Funktionsweise der Anlage
In der Leimholz-Zuschnittanlage wird das Holz, das in der Maschine zuvor verleimt und gehobelt wird, millimetergenau abgelängt – dafür braucht es insgesamt acht Antriebe. Nachgeschaltet ist der mitlaufende Kappautomat, der über je zwei Klemmrollen auf der Ein- und Auslaufseite verfügt. Kommt das gehobelte Brettschichtholz am Ende der Hobelmaschine an, erkennt ein Sensor den Materialaustritt und die Auftragsdaten werden übernommen.
Die eingangsseitigen Klemmrollen des Kappautomaten werden dann pneumatisch circa 10 mm über die Höhe des Leimholzbalkens vorpositioniert. Beim Austritt des Holzes aus der Hobelmaschine fährt ein Messrad gegen dessen Unterseite und erfasst die Vorschubgeschwindigkeit des zu schneidenden Materials. Ein Sensor vor dem Sägeantrieb erfasst die Länge des Materials und sorgt zugleich dafür, dass die Klemmrollen absinken.
Je nach Vorgabe des Leitsystems erfolgen millimetergenau ein Frontschnitt, ein Mittelschnitt und ein Endschnitt des Materials. Die Herausforderung dabei ist, dass das Material aus dem vorgelagerten Hobelprozess ständig nachfliesst und sich der Kappautomat für den Front- und Mittelschnitt fliegend aufsynchronisieren muss.
Video: Aufsynchronisierung mit mitfahrendem Schnitt
Das Aufsynchronisieren als Herausforderung
«Das Aufsynchronsieren lässt sich mit einem Standardmodul von SEW einfach realisieren», sagt Markus Mandel und relativiert gleich im nächsten Satz: «Das Schwierige in dieser Anwendung ist jedoch der mitfahrende Schlitten mit seinem mechanischen Spiel, was beim Aufsynchronisieren zu einem Schleppabstand führt, der hinausgerechnet werden muss.» Weil das nicht einfach irgendwie am Computer geht, bedurfte es empirische Versuche vor Ort. Diese Testschnitte haben zwar Zeit in Anspruch genommen, von der man bei einem Retrofit eigentlich nicht viel hat, aber nur so konnte man den Schleppabstand kompensieren.
12 Gründe, die für ein Retrofit sprechen
1. Kosteneffizienz: Ein Retrofit ist in der Regel deutlich kostengünstiger als der Kauf einer neuen Maschine. Sie sparen dabei sowohl Anschaffungskosten als auch Ausgaben für den Transport und die Installation einer neuen Maschine.
2. Modernisierung: Durch das Retrofit wird Ihre Maschine auf den neuesten Stand der Technik gebracht, sodass Sie von verbesserten Funktionen und einer erhöhten Leistung profitieren können, ohne die gesamte Maschine austauschen zu müssen.
3. Umweltfreundlichkeit: Ein Retrofit trägt zur Schonung der Umwelt bei, da weniger Ressourcen für die Produktion einer neuen Maschine verbraucht werden. Zudem wird der Energieverbrauch optimiert, was zu einer Reduzierung der CO2-Emissionen führt.
4. Kürzere Stillstandszeiten: Bei einem Retrofit sind die Stillstandzeiten der Maschine in der Regel kürzer als bei der Installation einer neuen Maschine, da keine umfangreichen Demontage- und Montagearbeiten erforderlich sind.
5. Wertsteigerung: Durch das Retrofit steigt der Wert Ihrer bestehenden Maschine, da sie nun über moderne Funktionen verfügt und in ihrer Leistungsfähigkeit optimiert wurde.
6. Anpassungsfähigkeit: Ein Retrofit ermöglicht es, Ihre Maschine individuell auf Ihre Bedürfnisse zuzuschneiden und gezielt die Komponenten zu verbessern, die für Ihren Betrieb am wichtigsten sind.
7. Geringere Schulungskosten: Da Ihre Mitarbeiter bereits mit der Maschine vertraut sind, entfallen aufwendige Schulungen für den Umgang mit einer neuen Maschine.
8. Verlängerung der Lebensdauer: Durch das Retrofit wird die Lebensdauer Ihrer Maschine verlängert, sodass Sie die Investition in eine komplett neue Maschine aufschieben können.
9. Verbesserte Sicherheit: Das Retrofit kann dazu beitragen, die Sicherheit Ihrer Maschine zu erhöhen, indem veraltete Komponenten ersetzt und neue Sicherheitsfunktionen hinzugefügt werden.
10. Bessere Integration in bestehende Systeme: Bei einem Retrofit wird Ihre Maschine an die bestehenden Produktions- und Steuerungssysteme angepasst. Dies erleichtert die Integration und minimiert mögliche Inkompatibilitäten, die beim Einsatz einer neuen Maschine auftreten könnten.
11. Reduzierung von Verschleiss und Wartungskosten: Durch den Austausch alter, verschlissener Komponenten gegen modernere und langlebigere Teile kann das Retrofit die Wartungskosten und den Verschleiss Ihrer Maschine reduzieren.
12. Verbesserung der Produktqualität: Durch präzisere Steuerungen und optimierte Prozesse, die durch das Retrofit ermöglicht werden, kann die Qualität Ihrer produzierten Produkte gesteigert werden, was wiederum zu zufriedeneren Kunden und höheren Umsätzen führen kann.
Das Programmieren
Dass bei einem Retrofit die Maschinenbediener eine wesentliche Rolle spielen, ist für Markus Mandel und sein Team klar. «Das beginnt schon beim Vorprojekt», erklärt er. Bei diesem wird normalerweise ein Tag investiert, die Anlage zu inspizieren, die Mitarbeiter zu befragen, Videos der Anlage zu erstellen und den Programmcode zu sichten. Weil dieser aber meist nicht lesefreundlich geschrieben ist, erfährt man aus den Gesprächen mit den Mitarbeitern, die alle Störungen und Abhängigkeiten der Maschine auswendig kennen, mehr.
Apropos Programmcode und Mitarbeiter: Das Programm musste vollkommen neu aufgesetzt werden und man wollte die Gelegenheit nutzen, um die Abläufe intuitiver und das Programm übersichtlicher zu gestalten. So wurde der Tagesablauf mit den Mitarbeitern Schritt für Schritt durchgegangen. Was schalten die Mitarbeiter ein, welche Seiten am Bedienpanel brauchen sie danach, was müssen sie öfter einstellen als anderes? Wo wollen Sie lieber direkt zur Zieleingabe kommen, statt drei Einstellungen zuerst anzuwählen? «Wenn man sich dann die Notizen anschaut, erkennt man schnell, dass viele Seiten nicht notwendig sind, einige sogar ins Leere führen oder nur am Anfang gebraucht werden.» Mit dieser Massnahmen konnte das Programm von 40 auf 20 Seiten gekürzt werden.
Bild: Übergang Hobelmaschine in mitfahrende Kappsäge.
Fazit und Zukunft
Das Retrofit erfolgte, während die vor- und nachgelagerten Maschinen weiter produzierten. Das verlängerte die Massnahme von zwei bis drei Wochen auf insgesamt vier Wochen, da bearbeitetes Material auf dem Weg zur nächsten Station immer wieder die Maschine passieren musste.
Trotz dieser Verzögerung erweist sich das Retrofit als voller Erfolg. Nach der Erneuerung hat sich wie gewünscht die Fehlerquote deutlich reduziert und die Genauigkeit erheblich verbessert. Anstatt der vier bis fünf Millimeter zuvor, liegt sie nun unter einem Millimeter. Und sollte es Störungen geben, kann das Team von Alfred Imhof jetzt mittels Fernwartung helfen.
Mit der neu eingesetzten Technik ist der Zugriff auf alle relevante Maschinendaten möglich, für den Bereich «Condition Monitoring/Predictive Maintenance» stehen detaillierte Diagnosedaten zur Verfügung. Diese Daten können unter anderem über den plattformunabhängigen Service OPC-UA bereitgestellt und abgegriffen werden. Oder sie werden noch im Edge-Prozess gefiltert und bearbeitet, um dann zum Beispiel von einem übergeordneten System weiterverarbeitet und angezeigt zu werden. «Mit der neuen Technik sind die Weichen für IoT und Industrie 4.0 jedenfalls gestellt», sagt Markus Mandel. Zudem ist die Anlage jetzt technisch auf jenem Stand, dass sie bei Bedarf auch in puncto Nachhaltigkeit ausgebaut werden kann – zum Beispiel mit dem Einbau eines Energiespeichers.
Vom Retrofit profitiert hat nicht nur die Firma Roth. «Auch wir lernen bei jedem Projekt wieder etwas dazu», meint Markus Mandel. «In diesem Fall hat sich wieder einmal gezeigt, dass gute Vorbereitung die halbe Miete ist, hauptsächlich hinsichtlich der Stillstandszeit. Wir haben neue Wege gesucht und gefunden, um diese Zeiten noch weiter zu verkürzen», freut sich Markus Mandel.
Bild: Übergang Hobelmaschine in mitfahrende Kappsäge.
Fazit und Zukunft
Das Retrofit erfolgte, während die vor- und nachgelagerten Maschinen weiter produzierten. Das verlängerte die Massnahme von zwei bis drei Wochen auf insgesamt vier Wochen, da bearbeitetes Material auf dem Weg zur nächsten Station immer wieder die Maschine passieren musste.
Trotz dieser Verzögerung erweist sich das Retrofit als voller Erfolg. Nach der Erneuerung hat sich wie gewünscht die Fehlerquote deutlich reduziert und die Genauigkeit erheblich verbessert. Anstatt der vier bis fünf Millimeter zuvor, liegt sie nun unter einem Millimeter. Und sollte es Störungen geben, kann das Team von Alfred Imhof jetzt mittels Fernwartung helfen.
Mit der neu eingesetzten Technik ist der Zugriff auf alle relevante Maschinendaten möglich, für den Bereich «Condition Monitoring/Predictive Maintenance» stehen detaillierte Diagnosedaten zur Verfügung. Diese Daten können unter anderem über den plattformunabhängigen Service OPC-UA bereitgestellt und abgegriffen werden. Oder sie werden noch im Edge-Prozess gefiltert und bearbeitet, um dann zum Beispiel von einem übergeordneten System weiterverarbeitet und angezeigt zu werden. «Mit der neuen Technik sind die Weichen für IoT und Industrie 4.0 jedenfalls gestellt», sagt Markus Mandel. Zudem ist die Anlage jetzt technisch auf jenem Stand, dass sie bei Bedarf auch in puncto Nachhaltigkeit ausgebaut werden kann – zum Beispiel mit dem Einbau eines Energiespeichers.
Vom Retrofit profitiert hat nicht nur die Firma Roth. «Auch wir lernen bei jedem Projekt wieder etwas dazu», meint Markus Mandel. «In diesem Fall hat sich wieder einmal gezeigt, dass gute Vorbereitung die halbe Miete ist, hauptsächlich hinsichtlich der Stillstandszeit. Wir haben neue Wege gesucht und gefunden, um diese Zeiten noch weiter zu verkürzen», freut sich Markus Mandel.
Alfred Imhof und der Retrofit-Bereich
Die Firma Alfred Imhof bietet schon seit vielen Jahren Retrofits und baut diesen Geschäftsbereich kontinuierlich aus. Sie übernimmt dort auch die Gesamtleitungen solcher Projekte und koordiniert daher die Arbeiten mit Partnerfirmen, die zum Beispiel den Schaltschrank umbauen – wie beim Retrofit bei der Firma Roth – oder mechanische Umbauten vornehmen. «Alles aus einer Hand» ist die Maxime, damit Retrofit-Kunden selbst entlastet werden.
Weitere Artikel, die Sie interessieren könnten
Impressum
Autor: Eugen Albisser
Bildquelle: Alfred Imhof
Redaktionelle Bearbeitung: Technik und Wissen
Informationen
Alfred Imhof AG
imhof-sew.ch
Weitere Artikel
Veröffentlicht am: